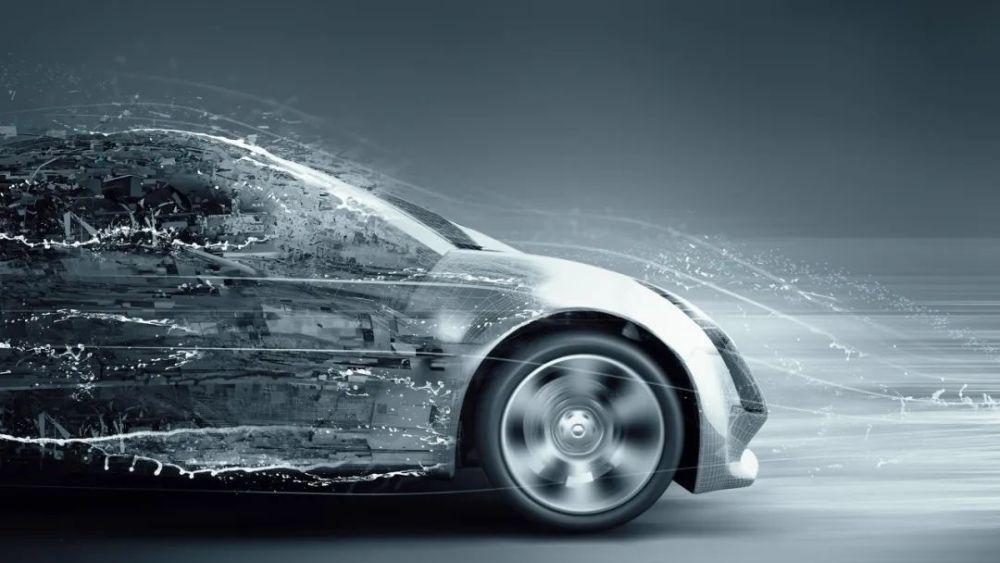
Author: Zhou Zhenxing, Geng Huili
Editor: Director Dong
Research support: China Electric Vehicle 100 Association
In April this year, two car manufacturers announced the suspension of production: BYD announced the suspension of production of fuel vehicles, determined to fully invest in new energy; while the representative of the new energy force Weilai, regrettably said that the production of vehicles was temporarily stopped.
The suspension of weilai is mainly due to the impact of the epidemic. Since March, the company's supply chain partners in Jilin, Shanghai, Jiangsu and other places have stopped production. The epidemic has not only affected Weilai, the location of the Ningde era has also issued an announcement to temporarily control logistics. Tesla's Shanghai factory and Shanghai Volkswagen were also affected accordingly. Looking further ahead, in 2021, the ideal has also been expressed, because millimeter-wave radar is out of stock, production has been reduced.
In contrast, BYD, which has a multi-link layout of the industrial chain and self-production and self-sales, seems to have been less affected by the epidemic; and the question that makes us want to explore more is: Will the external shocks on the supply chain pass? Will internal constraints be broken? Will the automotive supply chain usher in a new stage and a new format?
01
Four types of shocks in the automotive supply chain
Roughly speaking, the mainland automotive supply chain has suffered four types of external shocks, the first of which is undoubtedly the epidemic.
Beginning in 2020, the pandemic first hit China's domestic supply chain. At that time, there was news that Beijing Benz requested approval for suppliers to resume work, otherwise it would lose 400 million yuan per day, which would also affect the development of Beijing-Tianjin-Hebei. However, after the epidemic prevention and control, the Chinese factory has fully started operation.
Subsequently, the epidemic expanded globally, which in turn affected overseas supply chains, and many orders returned to China from Vietnam, Europe and other places, but the reduction and suspension of overseas factories affected the mainland through imports. For example, the wiring harness factory in Vietnam, the chip in Malaysia, etc.
In the past March, the epidemic happened to be in Jilin and Shanghai, as well as the surrounding Ningbo, Anhui, etc., and the above-mentioned cities are also important automobile industry bases, so they have once again impacted mainland automobile production, including Tesla's Shanghai factory, and also pressed the pause button.
The impact of the epidemic is always short-lived. But before there is a specific drug, the "epidemic impact" itself seems to become a norm.
The second type of shock is the mismatch caused by supply and demand. Typical is the chip. Usually, mobile phones are the main demand side of chips, while cars are the stable demand side of chips such as power.
However, the outbreak of new energy vehicles has changed this situation. On the one hand, the degree of electronicization of new energy vehicles has increased the demand for chips; on the other hand, the rapid outbreak of new energy vehicle sales has also led to insufficient chip production capacity. Coupled with the slow expansion of production capacity, there is a mismatch.
The mismatch of production capacity can be improved by successively putting new production lines into production. Of course, the problem is that under this epidemic, not many companies dare to expand production significantly.
The third type of shock is geopolitical influence. Sino-US friction in the chip field, as well as the impact of the Russian-Ukrainian conflict. These effects cannot be predicted. But when it happens, it can't be ignored. Of course, the direction of geopolitics, a thousand faces, will not be discussed.
The fourth type of impact is the development of new energy vehicles. This is a shock, but more of an opportunity. Electrification and intelligence bring new demand, and more than 70% of the traditional parts system will face reconstruction.
Overall, external shocks are somewhat powerless, but the whole should pass. But as Uncle Benshan admonished, you can't just complain about the climate. Another thing that deserves the industry's attention is the internal factors of the mainland automobile supply chain.
02
Internal factors in the automotive supply chain
One of the internal factors of the mainland automobile supply chain is that there are many, large but not strong. This is also a problem left over from history. In the era of fuel vehicles, vehicle brands are also foreign-funded and joint ventures. The core component of the engine cannot be broken, and can only do some supporting around the periphery, which belongs to the middle and low range. Therefore, when we achieved a technological breakthrough in the hydraulic field, the revenue and market value of related companies ushered in a sharp rise.
This problem has improved in the era of new energy vehicles. There are breakthroughs in the three-electric system, and the battery can already be "me-based". But while the mechanical disadvantage weakens, the electronic disadvantage is also prominent. The most prominent problem in the automotive supply chain in the past two years is the "lack of core".
In chip design, we have made rapid progress; but in manufacturing, testing and other aspects, it is still subject to people. Infineon and ST Are IDM integration, which not only requires funds, but also time to accumulate. Of course, this is not only a problem of the automobile industry, but also a problem of the chip industry.
And unlike consumer semiconductors, automotive grade chips have higher requirements for the stability and reliability of chips due to harsher use environments, longer service life, especially zero tolerance in safety. But the embarrassing thing is that the two major industries of chips and automobiles have just found that the original other is so important, the previous communication is insufficient, and the standards of the two major industries have been "independent" for many years, resulting in the lack of clear and unified standards for vehicle-grade chips.
In addition to the evaluation standards and systems of vehicle-grade chips that need to be improved, there are few third-party testing agencies. In the past, the iteration speed of mechanical-based automobiles was not so fast, and now the parts have to be rapidly iterated without losing the safety and reliability requirements, and the contradiction has arisen. Therefore, at this time, third-party certification, third-party testing, and third-party testing services are more important.
At present, there are many institutions in China that can carry out AEC-Q (Reliable Test Standard for Automotive Integrated Circuits) testing and certification, but there are very few institutions that can really meet the automotive standard level certification, and most of them only have partial testing capabilities. In order to get professional certification and let products get on the bus as soon as possible, domestic chip companies have to go abroad to do third-party certification testing, which is expensive and time-consuming.
In the era of fuel vehicles, we pay more attention to the whole vehicle, pay attention to the scale of production, pay less attention to research and development and parts, and the investment is not enough, resulting in the scale of the automobile industry going up, but leaving the heart disease of technology hollowing out. In the era of intelligent electric vehicles, the global automotive industry ushered in great changes, the industrial chain accelerated restructuring, we still have the opportunity to make up. At the two global new energy vehicle supply chain innovation conferences in 2020 and 2021, Chen Qingtai, chairman of the China Electric Vehicle 100 Association, called for attention to the safety of auto parts and supply chains: "The bottom of the automotive power is the parts power."
03
From flexibility to redundancy
Cost reduction and efficiency increase is the core proposition of every industry, and the automotive industry is the same, paying attention to flexibility and paying attention to low inventory. As a result, two distinctive features of the automotive supply chain have also been formed: a pyramidal multi-level supply system and a low-inventory supply chain management of "lean production".
However, both models are being challenged.
The multi-level supply system entrusts the research and development of most parts and components to the first-level supplier, and the car company only needs to verify these packaged "black box" modules and a small amount of redevelopment to load the car, which greatly improves the efficiency. But the emergence of new energy vehicles is changing this situation.
In the model development and design stage, car companies hope that parts can be involved and built together; at the same time, under the expectation of efficiency and immediate feedback, new energy vehicle companies have begun to directly contact second-tier and third-tier suppliers, weakening the first-tier status.
"Lean production" saves the occupation of space, time and funds by inventory for car companies, so as to achieve better financial performance. This model is also common in the apparel industry, with ZERO JIT inventory. However, lean production and zero inventory are prerequisites, that is, the stability and certainty of the external environment. But when the uncertainty of the internal and external environment is increasing significantly, perhaps, it is time to abandon the attachment to "zero inventory" and start to consider "redundancy".
When supply security becomes the core, "redundancy" becomes the key, and it also becomes "profit" from "cost".
For example, looking back at 2021, in the face of the supply chain crisis, there are two types of car companies that have performed better: the traditional jumbo that has changed from lean production to a high degree of vertical integration, and the new energy vehicle companies with a high degree of vertical integration. The former can let the younger brothers bear the supply chain pressure for themselves through absolute discourse, and the latter is self-sufficient with the manufacturing ability of the whole industry chain.
As the founder of the lean production concept, Toyota won the global sales championship in 2021, selling 10.5 million cars in the whole year, with a sales volume of about 21 Teslas. It relies on having a global supply chain inventory. Just like when the Fukushima nuclear accident occurred in 2011, only local production was affected, while the Factories in China and North America were producing as before.
However, Toyota is not without shocks, not without changes. In 2021, Toyota also had to suspend "lean production" and switch to BCP (Business Continuity Planning) to ensure a business continuity plan. Of course, Toyota still relies on a strong voice to transfer the inventory pressure and require suppliers to prepare 2-6 months of inventory for it.
In addition, Toyota will deepen its binding relationship with suppliers through equity investment and strengthen its supply chain position. Toyota Motor, for example, is Denso's largest shareholder, and the latter is the second largest Tier 1 supplier in the world by revenue in 2020.
It is BYD and Tesla that implement the integration model, trying to rely on themselves. In particular, BYD relies on its self-production system, which includes almost all the entire industrial chain of new energy, to ensure its own supply.
Vertical integration is not BYD's original intention, but because it has suffered losses, it has to choose this route that has been abandoned by the industry. Twenty years ago, almost all the key auto parts were monopolized by overseas giants, and newcomers to the industry like BYD could only go back and nibble hard if they did not have to purchase at high prices. Fortunately, BYD's hard work in batteries, electronics, semiconductors and other fields finally blossomed in 2021.
With its own power battery, three-electric system, and automotive chip self-supply capacity, BYD has risen against the trend of 21H2 in the lack of cores and production capacity shortage in its peers, and has almost maintained a growth rate of more than 200% year-on-year, becoming the runner-up in global new energy sales.
Entering 2022, the new energy industry has encountered a supply crisis in the upstream of lithium batteries, and the soaring price of lithium battery materials has made many car companies miserable, and BYD once again relied on the installed capacity second only to Ning Wang to ensure the battery supply of its own models, and climbed the throne of its own brand sales champion in February.
Of course, the integration model also has drawbacks, and the more links involved, the more competitors. Especially when the previous partner found that he had raised an opponent, his heart must be turbulent. In the face of technological change, integration will be more difficult to turn around. However, if you look at the companies that have stopped production, you will find that integration is just a "happy annoyance".
04
The troubles of happiness
Why is it said that the disadvantage of integration is the trouble of happiness, because the trouble of many car companies is whether there can be integration.
As Zhang Yongwei, vice chairman and secretary general of the Electric Vehicle 100 Association, summed up: One of the most confusing things for most automakers is how to achieve controllability in the supply chain. In particular, should we enter the field of batteries and chips? Should I do the operating system? This is currently the most anxious problem in the industry.
It can be said that vehicle companies have sufficient reasons to lead these key links on their own, but at the same time they face a huge risk of falling into the trap of the supply chain, because this is an area that car companies are not familiar with in the past. From the previous mechanical vehicle to the current entry into the semiconductor chip industry and the formation of related capabilities, the past accumulation of car companies is far from enough.
For example, in the field of IGBT, 95% of the mainland high-end market needs to rely on imports. Professional semiconductor companies also need to take the time to make technological breakthroughs. For example, in the field of batteries, technological breakthroughs may be easy, but scale can have cost advantages and form synergies, rather than desperately dragging down enterprises for "integration". For example, the operating system, for car companies, not to mention the extremely high requirements of endowments such as talent, capital, and strength, but the change of concept and organizational form may be obstacles.
Therefore, for most car companies, integration is too difficult, and how to jointly participate in cultivating China's rich automotive supply chain may be a more feasible solution. And this requires not only the efforts of car companies, but also the overall coordination and scheduling of industry regulatory departments. But it is inevitable that the automotive industry and the semiconductor, computer, and Internet industries will converge more and more. This makes the supply chain problem more complex and prominent.
05
End
During this time, I saw an interesting "reflection" on the Internet, saying that the fathers were wrong: I used to see my father and mother save cloth needles and threads, rice flour, think they are miserly, or thrifty habits, and often blame them. But now I feel that maybe it is the memory of the times. Just like this month, many people are eager to have two refrigerators at home.
This is true of people, and so will the automotive industry. When the supply chain has suffered several shocks, it is believed that the suspension of production and shortage of goods will also leave a "memory of the times" for car companies. And the change in the supply chain is beginning. As is often said to be a "crisis", perhaps "opportunities are being bred in danger", but opportunities must be left to those who are prepared.
remark:
China Electric Vehicle 100: Founded in May 2014, it is an unofficial and non-profit third-party think tank platform in the field of new energy and intelligent networked vehicles. With the goal of promoting the development of the electric vehicle and intelligent networked vehicle industry, the platform breaks the limitations of the industry, discipline, ownership and department, brings together people from all walks of life such as government, academia and industry, and promotes multi-field integration and collaborative innovation through research and exchanges.
If you are engaged in the field of automotive supply chain, welcome to have more exchanges with Yuanchuan, we will organize high-quality sharing groups, and carry out online and offline exchange activities to communicate with each other and enhance industry awareness. You can add: dongstockdong, and indicate the name, work unit, etc.
Scan the code to add a small assistant, reply to [2201] to get the Yuanchuan selected industry data integration package