A number of China's major auto towns have been hit by the epidemic one after another, and the supply chain is almost in shock, but practitioners have also found opportunities for nirvana regeneration while working hard to resume work
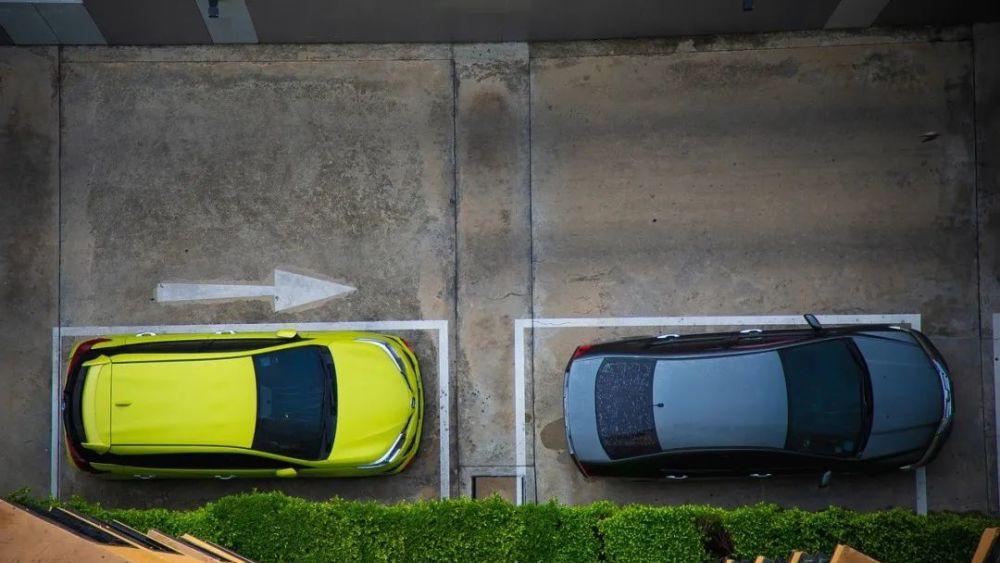
Text | Yin Lu Gu Lingyu
Edit | Mark
"Shenzhen, Guangzhou, Changchun, Shanghai, China's auto industry in addition to Chengdu and Wuhan, after the Spring Festival have been affected by the epidemic, although it seems that Shanghai's problems have led to the current dilemma of the automotive supply chain, but the problem is actually gradually accumulated, Shanghai is only the last straw that overwhelms the camel, of course, this straw is a bit heavy."
This passage comes from a manager of a domestic tier 1 automotive supplier. Indeed, although Shanghai is an important automobile town in China, accounting for more than 10% of the country's automobile production, and is the city with the most complete automobile supply chain in the country, it is undoubtedly incorrect to attribute all the current plight of China's automobile supply chain to the Shanghai epidemic.
To get rid of the predicament, the immediate approach must be to open up logistics, because the most troublesome problem for enterprises related to the automotive supply chain at present is that even if closed-loop production can be achieved, raw materials cannot be transported in and products cannot be shipped out. In this regard, the relevant state departments have successively introduced some policies, such as Shanghai's white list system, 666 of the first batch of listed companies, and more than 250 related to automobiles, accounting for about 40%, but from the perspective of actual implementation effects, the policy strength is not enough, and the implementation needs to be improved.
Aside from the whitelist, what is needed to return to work
On April 16, the Shanghai Municipal Commission of Economy and Information Technology issued the "Guidelines for the Prevention and Control of the Epidemic in Shanghai Industrial Enterprises Resuming Work and Production (First Edition)", which announced the first batch of 666 white-listed enterprises, such as SAIC Passenger Cars, SAIC Volkswagen, SAIC-GM, Tesla and other vehicle companies, and important supply chain enterprises such as ZF, Aptiv and Valeo are all on the white list, and the proportion of automobile-related enterprises is the highest. However, from the perspective of implementation, the current whitelist system still has two shortcomings.
The first shortcoming is the issue of execution. After the release of the white list, a number of Shanghai Auto related enterprises said that the white list could not be recognized in the streets, communities, and neighborhood committees, and employees still could not leave the community and could not return to work. At present, the conditions that returnees need to meet are:
1. There is no positive infection in the building within 7 days;
2. The company issues a certificate of employment demand and a certificate of whitelist enterprises;
3. 48-hour nucleic acid negative proof, with the above information to apply to the neighborhood committee, but some neighborhood committees do not recognize the validity of the white list, out of various concerns do not dare to release people. At present, the return of employees of whitelist related enterprises is not optimistic, and the proportion of returnees is generally less than 50%, and less than 30% is not uncommon.
For industrial manufacturing enterprises, it is not how many percentage of employees who return to work can restore how much production capacity, if the proportion of returning to work is less than half, the recovery of production capacity usually does not exceed 10%, because multiple key positions are missing, and the production rhythm must be greatly reduced, otherwise it is easy to cause safety hazards.
Two days after the release of the whitelist, Tesla "fished" out 8,000 employees, officially resumed work on April 19, and is expected to achieve a single shift next week. But this is mainly because Tesla's employees live more concentrated, and the efficiency of "fishing people" is relatively high. Other companies generally have difficulty achieving Tesla's similar efficiency, and most companies are still in the stress test stage of resuming work and production, such as SAIC Lingang Plant, the first car that just completed the stress test of resuming work and production on April 19.
The second shortcoming is that the coverage of whitelisted companies is still insufficient. The current whitelist covers mainly vehicle manufacturers and important Tier 1 suppliers, which allows Tier 1 suppliers to deliver finished products to OEMs to solve urgent needs. Tier 1 suppliers can also use their own whitelist to facilitate access for their next tier suppliers and solve the delivery problems of tier 2 suppliers. But further down, the whitelist is powerless. Because secondary suppliers are often not on the white list, they are unable to solve the convenience of the next tier supplier, can not obtain raw materials and spare parts, the secondary supplier delivers the finished product, consumes the raw material, will face another shutdown.
The automobile supply chain is currently the longest chain of industrial manufactured products, the most graded categories, automotive suppliers can be divided into at least four to five levels, one to three levels of suppliers are mostly large-scale enterprises, suppliers below the third level, many are still in the workshop stage, relying on the whitelist system, it is difficult to cover so many levels of suppliers. It takes more than a month to solve the immediate needs, and the whitelist system is still valid, and this list must cover at least thousands of companies.
Therefore, if you want to quickly resume work and production, the first thing is to make the white list in the community and the neighborhood committee recognized, and reduce the difficulty of "fishing for people".
In addition, the whitelist system needs to expand its breadth and depth as soon as possible and establish a multi-local whitelist mutual recognition system. Shanghai automotive supply chain radiation throughout the Yangtze River Delta region, a large number of third- and fourth-level suppliers are in jiangsu and Zhejiang, the current white list is limited to Shanghai, which has a very limited role in repairing the entire automotive supply chain, the Yangtze River Delta region three provinces and one city (Jiangsu, Anhui, Zhejiang, Shanghai) to share a unified white list of mutual recognition is imminent.
If it is difficult to achieve whitelist sharing and mutual recognition in the short term, then enhancing the depth of the downward extension of the whitelist can also be used as a contingency plan, in addition to solving the convenience of passing for their own subordinate suppliers, suppliers can also rely on the supply contract and the whitelist of customer enterprises to solve problems for the next level of suppliers, so that the whitelist can really play an effective role in opening up the entire supply chain.
New opportunities under a new consensus in the supply chain
As said at the beginning of the article, the problems of China's auto supply chain are gradually accumulating, and the supply chain dilemma this time seems to be mainly due to the impact of the epidemic in a number of major auto towns, resulting in the entire supply chain of almost shock, but the problems of China's auto supply chain have actually existed for a long time, but the rapid growth of the industry in the past two decades, these problems have been covered up.
Negative sales growth began in 2018, and the outbreak of the epidemic in 2020 exposed some of the problems, but the rapid recovery of the market in the second half of 2020 and the explosive growth of the new energy vehicle market in 2021 once again delayed the pace of correcting the problem, which is the root cause of the current automotive supply chain dilemma.
Under the impact of this round of almost shock, Chinese auto industry practitioners are also seriously reflecting on the problems existing in China's auto supply chain while struggling to resume work, and according to the communication between Caijing Eleven and automakers and suppliers, it is found that the problems are concentrated in two aspects:
1. The resilience of China's automotive supply chain is insufficient, and the ability to cope with extreme impact is poor.
2, supply chain enterprises have low technical content, cost advantage is the main advantage, or even the only advantage.
Supply chain resilience was previously considered an advantage for China's auto industry, as it has strong manufacturing capabilities and OEMs often find multiple backup suppliers when procuring, giving them more room to maneuver when dealing with shocks. This is better reflected in the global supply chain crisis that began in 2020. However, in the face of this extreme impact, the performance is just the opposite, which has caused widespread reflection among practitioners.
In the reflection, many practitioners mentioned the repair process of the Japanese automotive supply chain after the 2011 March 11 earthquake in Japan, believing that this sample has many similarities with the current Chinese automotive supply chain: suppliers have stopped production on a large scale, logistics have been interrupted, and many companies have exhausted cash flow and have great operational difficulties.
As the pillar of the Japanese automotive industry, Toyota, Honda, Nissan and other automakers at that time were unanimously appreciated by the industry. Taking Toyota as an example, high-level business leaders are sent to visit suppliers one by one to collect specific problems, and for suppliers with financial difficulties, they will invest in shares to help them tide over the difficulties. After the difficulties, if the supplier intends to buy back the shares, Toyota will also sell the shares back at the market price, and many suppliers choose not to buy back, but to accept Toyota as their long-term shareholder.
The role of supply chain repair on Toyota is immediate, with global sales of 7.95 million units in 2011, down 6% year-on-year, but in 2012 it quickly rebounded to 9.748 million units, ranking first in the world. For the next ten years, Toyota was the world's top seller for six years.
After the global automotive supply chain fell into crisis in 2020, Toyota surpassed Volkswagen, ending its record of the first consecutive global sales in 2016-2019, highlighting Toyota's supply chain resilience. In 2021, Toyota will continue to maintain its sales champion, up 10% year-on-year, returning to more than 10 million sales to 10.5 million vehicles. Volkswagen, on the other hand, delivered 8.88 million vehicles in 2021, falling to a 10-year low.
In this round of domestic supply chain crisis, practitioners have also studied Toyota as an important analysis sample. For example, automakers and suppliers have mentioned that in addition to sparing no effort to support suppliers, Toyota is also greatly adjusting the previous lean management model, and now Toyota requires its suppliers to prepare 2-6 months of parts inventory to improve the level of supply chain security. The reason why suppliers can meet this demanding requirement of Toyota is also a return for the strong support of Toyota.
In the relationship between domestic OEMs and suppliers, toyota-like cases cannot be found. Previously, the preference of automakers for suppliers in crisis was to find replacements as soon as possible. This approach works well in the absence of an industry-wide crisis, and competition among suppliers is fierce, with OEMs having an advantageous position in terms of delivery cycle, price, billing period, payment method and so on. But when a limit situation is encountered, this practice fails and can even be counterproductive.
A small and medium-sized first-tier supplier staff said bluntly: "Now we can resume production, to whom to supply first, to whom to supply later, this knowledge is big, even if the price is the same, the account period is short, with cash without bills of exchange, customers who used to settle quickly, the priority must be higher." ”
In this round of crisis, OEMs also realized that the previous supply chain management method needs to be adjusted, and the future supply chain health will be low for a long time, giving greater support to high-quality suppliers, and playing a more positive role in the safety and cost control of the entire supply chain.
OEMs are increasing their support for suppliers, and suppliers can also pass this effort on a step-by-step basis throughout the supply chain. Let the upper and lower levels of the supply chain shift from the past to compete for profits and shift to the joint collaboration, which is the consensus of most practitioners to enhance the resilience of the supply chain in this round of shock crisis.
Another consensus to improve the resilience of supply chains is to continue to strengthen the localization of supply chains. For two years the voice has not stopped, but it has been saying more and doing less, but this time it is different.
A Chongqing electric vehicle brand source told "Finance Eleven" that even if they are Chongqing brands, but the supporting suppliers are still mainly in the Yangtze River Delta region, although the current production capacity has not been affected, but if the resumption of work and logistics shutdown continues, it is only a matter of time before they fall into trouble. He revealed that in the automotive industry in Chongqing today, there is more and more such a consensus from the senior management of enterprises to ordinary practitioners: the supply chain needs to be localized, and "the epidemic can be solved without Chongqing."
Localization does not necessarily mean abandoning the original suppliers, and bringing high-quality suppliers into the local area is also an important option, which is an opportunity for domestic suppliers to go global. A jiangsu-zhejiang-based body parts supplier manager said: "We are considering building a second manufacturing base in Southeast Asia. In the past, there was only one domestic factory, and now the demand for overseas customers is increasing, and the pressure on domestic customers to ensure supply is also increasing, and there is a second base overseas, and the increased cost and the increased supply freedom are completely acceptable. ”
Moreover, the acceleration of the localization process also has a positive effect, that is, to solve another important problem in China's automotive supply chain, the technical content of supplier enterprises is generally low, and the cost advantage and price advantage are almost the only competitive advantages.
This problem is not a unilateral problem of suppliers, because in the past, when automakers selected suppliers, parts with slightly higher technical content would not be considered unless the price advantage of domestic suppliers exceeded 20%. The direct result of this is that most domestic suppliers have given up the competition for high-tech subsystems and focused all their energy on cost optimization and establishing price advantages.
The current supply chain crisis has given new opportunities for domestic suppliers, a Person related to Huawei's automotive business told "Finance Eleven" that Huawei has a stronger supply chain control capability, if the epidemic continues to the second half of this year, in the context of the shortage of core components and raw materials, this may become an opportunity for Huawei, "If those international manufacturers do not have useful (parts), is it necessary to consider us." ”
A domestic medium-sized supplier manager also said that now the automakers are willing to give more opportunities and are willing to give more relaxed conditions on the price, so domestic suppliers have the ability and confidence to continue to rush upwards. "In the past few years, there have been more and more countries running, and my confidence in China's auto industry chain is getting more and more sufficient, as long as we are given the opportunity, we will definitely be able to rush up."
In the past two years, the upward momentum of Chinese suppliers has emerged, according to the list of the top 100 global auto suppliers released by the Us "Automobile News", the number of Chinese suppliers on the list in 2021 has reached 9, which has surpassed South Korea, second only to Japan, the United States and Germany. Among them, 1 was newly listed, 8 were ranked higher, and the highest ranking Yanfeng ranked 17th.
The author is a reporter for Caijing, and Han Shulin also contributed to this article