The Highlander dismantling live broadcast time will be from February 22 to 24, mainly from the passive safety of the vehicle and the two aspects of body materials to reveal, to see what is commendable about the passive safety of the vehicle and the body materials of the new Highlander, and will there be any embarrassment?
Demystify the whole process of Highlander's dismantling
Some time ago, we watched the frontal 40% overlapping deformable barrier crash test of the new generation of GAC Toyota Highlander as an exclusive media at the C-NCAP test site of the China Automobile Center, and many netizens followed our lens to watch the whole process of the crash test.
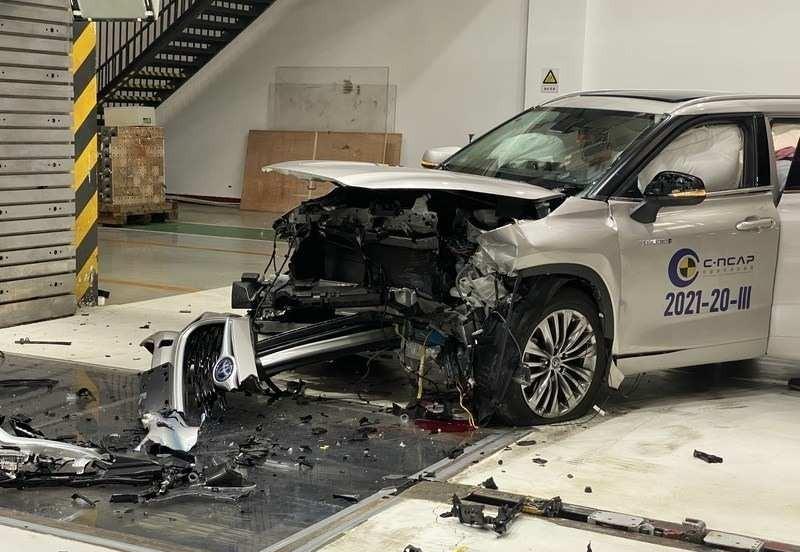
Although the entire crash test process has been displayed without reservation, many netizens still raised various questions during the live broadcast, such as whether it is safe for the test vehicle to crash into this way, why the front of the car is almost gone, why is it said that its protection is in place, and so on.
So in order to make up for the regrets at that time, we decided to spend money to buy the Highlander Iii car that had undergone a 40% crash test of positive bias and carry out an in-depth demystification and dismantling.
Final preparation before disassembly
8:30 a.m. on the 22nd
The Highlander who was to be dismantled this time has come to the dismantling site, and the dismantling engineer is making final dismantling preparations, and in the next dismantling process, he took the lead in dismantling the four doors and two covers of the vehicle.
We see that Highlander, who has undergone a 40% crash test of frontal bias, has been completely unrecognizable, the front anti-collision beam has been seriously deformed due to local force, and the energy-absorbing box has also produced a large collapse.
The dismantling work is about to begin
9:30 a.m. on the 22nd
Our filming team is in full swing, the team of engineers is waiting patiently, and without further ado, the dismantling work is about to begin!
The demolition of Highlander officially began
10:05 a.m. on the 22nd
With the sound of the wind cannon, the demolition of Highlander officially began, and the first to dismantle was the four doors and two covers of the vehicle. First of all, you need to remove the fixing bolts and connecting bolts on the door hinges and ensure that all the wires have been removed before removing the door to avoid unnecessary damage.
Door removal is a breeze
10:30 a.m. on the 22nd
Highlander's doors (including the main driver's door) were still very easy to remove, and there were no difficulties. Careful netizens found that there were also different degrees of dents in the door of the passenger side of the vehicle, which was only damaged by the collision vehicle during the transfer process, and was not caused by the 40% crash test of the frontal bias.
After the main driver's seat door is removed, we can see that there is an obvious color retention phenomenon on the knee airbag of the main driver's seat, indicating that the dummy's knee has contacted the airbag during the collision, which has played a better cushioning role to avoid the knee directly hitting the interior panel, followed by the removal of the tire.
The internal structure on both sides of the front is the same
11:00 a.m. on the 22nd
Highlander's wheels and body coverings have been basically disassembled, and the internal structure of the front part of the car has been completely exposed. It can be seen that the collision side has undergone obvious collapse, and the aluminum alloy anti-collision beam including the energy absorber box at the rear absorbs a part of the impact force through deformation and collapse, which has better mechanical advantages such as plasticity than the stamped steel plate material, and the weight is controlled.
The vehicle's tank components have also been concave, which shows the power of the collision. In addition, we saw that the structure on both sides of the engine was consistent, and the fender mounting beam on the collision side had better energy absorption during the impact.
The next step is to disassemble the anti-collision beam, but because the anti-collision beam has been deformed, it cannot be disassembled by simple bolts, so it can only be cut.......
The effect of the aluminum alloy energy absorption box is remarkable
11:40 a.m. on the 22nd
Highlander's front bumper has been completely disassembled under the efforts of engineers, and as for whether the anti-collision beam is aluminum or steel, it is only a trade-off between different characteristics, if only from the cost point of view, the price of aluminum alloy is definitely more expensive.
We come to the side where there is no collision, and although the honeycomb energy-absorbing box does not have the design of the collapse induction tank, it can make the impact force better dispersed in the tank. However, its aluminum alloy design, the impact of energy absorption will also be better, enhance the collapse ability of the front collision, and further protect pedestrians.
The full-frame subframe is still used
13:00 on the 22nd
After the removal of the front bumper and water tank of the vehicle, the true appearance of the engine has been fully displayed, and it can be seen that the engine has not suffered major damage, but due to the impact force on one side, a certain offset has been generated.
The full-frame subframe structure is basically the same as that of the previous generation Highlander, and the structure of the collision side produces a large bend, which well resolves the impact of the collision. We can also see from the structure on the other side that the vehicle disperses part of the impact energy and resists the deformation of the body through the solder joint or the difference in material in the bias collision.
Difficult to disassemble inside the engine compartment
14:30 on the 22nd
We shifted our attention from the front of the Highlander to the rear of the car, the anti-collision beam at the rear of the body used a double-bow high-strength steel design, and did not use aluminum alloy materials, which can improve the rigidity and hardness of the structure, and the role of unloading energy absorption can only be handed over to the rear car.
Highlander's exhaust system has also been dismantled, followed by the separation of the engine from the engine compartment, but due to more severe collision collapse, the dismantling process is not as easy as expected.
The Highlander chassis is disassembled
15:30 on the 22nd
Since the front and rear suspensions of the engine were connected to the subframe of the vehicle, engineers separated highlander's front and rear axles directly from the body for easier disassembly.
The front suspension of the new Highlander is McPherson style, and the rear suspension is in the form of multiple linkages. The lower control arm of the suspension is still a closed section control arm welded from two layers of steel plate, which is visually thinner than the lower control arm made of cast iron. We also saw that Highlander's rear axle motor was not damaged, and the damage point of the bias collision was mainly concentrated in the front of the car.
In addition, a resin skid plate is also installed on the rear suspension under the control arm, which can act as a fairing and reduce some wind resistance and noise.
The first day of the Highlander dismantling was completed
17:00 on the 22nd
Today's dismantling work is basically completed, mainly the new generation of Highlander body coverings and front and rear axles are disassembled, and the overall structure of the entire body is fully displayed. Tomorrow (February 23) will mainly disassemble the internal position of the vehicle's central control screen, dashboard, air conditioning panel, etc., and carry out a comprehensive interpretation from the aspects of passive safety and materials.
Interior demolition work is about to begin
08:55 on the 23rd
Today, the main interior of Highlander is demolished, including vehicle seats, center consoles, ceilings and other interior coverings, only the body structure and the welding assembly of the coverings (body in white), the engineer team is discussing the specific implementation plan, we wait a moment ~ .
Rear seat removal is complete
9:30 a.m. on the 23rd
Highlander's rear seats have been disassembled, asphalt damping pads are attached to the inside of the baseplate, and PVC coatings are sprayed on the outside of the baseplate, which are more common vibration isolation measures.
As a hybrid model, the new Highlander is installed under the second row of seats, and a separate reinforced structure is made behind the battery pack, which plays a certain protective role when the vehicle ride safety zone is squeezed.
Thus it can be seen that the front and rear parts of the vehicle are mainly used as buffer energy absorption areas, which allow large deformations to occur in the event of front and rear collisions, so that the force and acceleration on the occupant body do not exceed the specified endurance limit.
There is no visible damage to the battery pack
10:40 a.m. on the 23rd
When we remove the thick felt above the battery pack, we can see the true appearance of the battery pack below. Because the battery pack is mounted on the floor beam of the vehicle, it plays a sufficient support role for the side circumference, and the lateral width of the battery pack is smaller than the width of the seat, so there is not much protective structure.
After all, the position of the battery pack is below the rear occupant, if the battery pack is invaded, how much protective measures to do, does not have substantial significance.
The new Highlander also achieved a perfect score in the side impact test, so the vehicle did not suffer a large bending instability when subjected to lateral loads.
The roof removal is complete
11:15 a.m. on the 23rd
The Highlander's roof has also been removed, allowing for a view of the beams in the middle of the roof, connected to the B-pillar in a closed whole, providing most of the rigid support for the crew compartment when the vehicle is side-touched or rolled over.
The vehicle roof also uses sound-absorbing cotton for noise absorption, which can eliminate a certain rain hitting sound, and the roof also plays some role in heat insulation.
Use a small amount of foam bottom plate
13:10 on the 23rd
Highlander's seats have all been disassembled, and you can see that the underside is covered with felt for sound insulation, as well as a relatively simple foam partition, which looks slightly cheaper than THE PU foam material.
The next step was to disassemble the Highlander's center console and cockpit wiring harness to see the reinforced structure underneath the vehicle.
Trip the friends ~ shoot something else for everyone to see
14:40 on the 23rd
Due to the power of the on-site lights, it actually tripped ~ taking advantage of this gap, I give you a picture of the structure of the door interior panel, and the quality of the door workmanship will also have an impact on the characteristics of the NVH when the vehicle is driving.
In the interior panels of highlander's front and rear doors, the presence of sound-absorbing materials such as sound-absorbing cotton is not seen, and the control of noise is debatable. However, the sealing of the black skid plate is better, and further disassembly is required to see the structure of the reinforcing ribs.
In terms of details, the snaps of the door interior panels are equipped with soft sponge washers, and there is also a circle of sponge material around the speakers, which can effectively avoid collisions with the interior panels and generate noise.
The steering column after the collision has also been disassembled, and it is seen that it adopts a collapsed structure, similar to the radio retracting antenna, which can release the collision energy to a certain extent, but there is still obvious deformation after the impact.
The Highlander is almost in-white condition
15:30 on the 23rd
The new generation highlander's center console and wiring harness have been basically disassembled, and the vehicle has reached an almost body-in-white state. Next, we will interpret the various sections of the body-in-white body, as well as the key components.
The demolition of Highlander is basically complete
17:30 on the 23rd
Today's dismantling work is basically completed, mainly for the disassembly of the interior parts of the vehicle, so that the Highlander after the collision has reached the state of the body-in-white, you can clearly see the welding assembly of the vehicle structural parts and the covering parts. Tomorrow (February 24), we will analyze the structural changes after the collision of the vehicle, and the strength test of Highlander's A and B pillars and other components will be continuously monitored.
Is the interior structure of Highlander after the collision okay?
9:00 a.m. on the 24th
After the dismantling of the previous two days, the highlander who participated in the front 40% bias crash test was basically disassembled, and today it is mainly for the analysis of the loss point of the vehicle and the material of the body, and to see how the force of the vehicle is transmitted at the time of impact, whether the firewall of the vehicle and the structure of the crew compartment have been impacted, etc. We will present it to you in the form of a live graphic.
There are three main force paths for bias collisions
10:30 a.m. on the 24th
Let's first look at the side where the collision has never occurred, and analyze how the collision force of Highlander is transmitted and dispersed in a bias collision. Highlander absorbs and transmits the impact force through three paths, the upper path is mainly the water tank frame to the Shotgun front end structure (the upper beam on the inside of the front fender for energy absorption), and then to the A-pillar and the lower column.
The middle path is the most critical force path transmission route, which is first effectively absorbed by the aluminum alloy front anti-collision beam and energy absorbing box, and then the force is transmitted through the front longitudinal beam with increasing strength, and then transmitted to the rear floor longitudinal beam.
The third force transmission path is to effectively carry and absorb the impact force through the front beam and longitudinal beam of the full-frame subframe, and then transmit it backwards to the Highlander's body. Next, we will conduct a more intuitive analysis of deformation on the impact side.
The front stringer does not achieve the best results for the absorption and transfer of energy
12:40 on the 24th
After lunch, let's talk about what deformations occurred in the structural parts of the vehicle in Highlander's frontal 40% crash test, and how the lost points of the front and rear ductors were caused. And this is also where netizens pay more attention.
First of all, Highlander scored 16.883 points in this bias collision, and the loss points were mainly the chest and calf of the front driver, the chest and left calf of the co-pilot occupant, and the head of the female passenger in the back row, and the other parts were full marks.
We see that the main body of the Highlander's front longitudinal beam bends reasonably, but we do not think that the best effect of impact force conduction is achieved. Because we found that the collapse of the energy-absorbing box at the front end is not very large, and there is a solder joint failure at the root of the front longitudinal beam, including the bottom of the front cabin of the vehicle and the bottom longitudinal beam of the vehicle have seen a lot of structural glue cracking, as well as the cracking of the vibration relief plate in the front floor, indicating that a considerable part of the collision force is transmitted to these parts of the body during the collision process, resulting in deformation.
In addition, in the force transmission path of the lower part of the vehicle, we see that the full-frame subframe is well transmitted to the impact force in the bias collision through the process of external extension, and there is no phenomenon of bolt breaks at the junction between the subframe and the body. We also showed the aluminum energy absorption box in front of the subframe before, which played a better energy absorption effect in pedestrian protection.
The front legroom is significantly squeezed
14:30 on the 24th
In the vehicle's frontal 40% crash test, the full score is 20 points, and the new generation Highlander scored 16.883 points, so there is still a lot of room for improvement in the bias 40% project. Then the topic just now continues to extend, because the load in the collision is not well transferred and absorbed, and then the amount of engine displacement is too large to squeeze into the firewall.
We can see that there is a significant depression in the firewall on the impact side, and we can see a large crack, which is because the steering column is also squeezed by the engine, and the bend is then squeezed by the firewall, and the engine does not play an active role in the collision process.
As a result, the leg space of the front dummy has been significantly squeezed, causing the legs of the front dummy to cause obvious loss of points, but due to the presence of the knee air bag, it has been effectively alleviated to a certain extent. The problem of losing points on the chest of the front dummy and the neck of the back dummy is mainly caused by the matching problem of the restraint system such as seat belts and air bags.
The new generation highlander uses steel rear impact-proof beams
15:30 on the 24th
Let's talk about the material of the front and rear anti-collision beams that netizens are most concerned about, the front anti-collision beam is still made of aluminum alloy, and the rear anti-collision beam is changed from aluminum alloy to steel material, which is also the most common material in automobiles.
The anti-collision beam as a structural part, the vehicle in the design of the time is a clear strength requirements, in the case of meeting the strength requirements, compared to steel materials, aluminum alloy will be lighter, the weight of the vehicle will be better, of course, the cost will be higher, so the use of aluminum alloy collision beam will be more thick.
The interior of the doors has sufficient safety protection
16:30 on the 24th
When we cut the exterior panel of the Highlander, we can clearly see the internal structure of the door, and the more common cylindrical impactproof beam is used below the front door, and a bow-shaped stiffener is used above, arranged at a relatively straight angle.
The rear door also uses a cylindrical lower impact beam, while the upper two stiffeners have also been significantly strengthened, and the structural strength will be more excellent than the front door.
In addition, the reinforced structure inside the door, together with the A, B and C columns, as well as the sill beams, builds a lateral bearing structure to ensure that the resistance of the side to the impact and the impact force are transmitted quickly. Highlander also scored a perfect score in the side impact test, allowing us to see the body structure, including multiple longitudinal beams, which played a sufficient safety protection.
However, we also saw that there was no obvious sound insulation measures in the car door, and presumably the overall sound insulation effect was not very ideal.
The bottom panels of the carriages are made of a large amount of recycled cotton
16:45 on the 24th
In terms of body materials, the inside of the vehicle firewall and the entire lower bottom plate are made of waste spinning felt, which is commonly known as recycled cotton material, not the so-called "black heart cotton". This material is mainly made of recycled clothing crushing and pressing, as long as the recycled material meets the requirements, then the manufactured products do not have to worry too much.
It's just that highlander, as a medium-sized SUV of 300,000 yuan, should use better sound insulation materials. However, the vibration damper covering area on the floor of the carriage is still relatively large, and theoretically has a significant suppression effect on floor vibration.
The dismantling of the new generation Highlander is complete!
17:00 on the 24th
The dismantling of the new generation of Highlander has been completed, and it took three days to make a more comprehensive interpretation of Highlander, who participated in the 40% bias collision project, from which we also found many highlights and many regrets. It also received a perfect score in the side impact project, which is a visual manifestation of the safety advantages of the TNGA architecture.
The results of Highlander in the front 40% deformable overlapping barrier collision project are not particularly ideal, and it is hoped that Highlander will continue to make up for this shortcoming in the subsequent opening or improvement process.