In April, the epidemic in Shanghai and Guangzhou relapsed, and as two cities with more developed automobile industries, this round of epidemics made the automotive industry press the pause button.
On April 14, Xiaopeng Automobile He Xiaopeng said on Weibo: "In May, all Chinese automakers may stop work and production", and then Huawei Yu Chengdong also said that if Shanghai cannot resume work and production, all technology and industrial industries involving Shanghai's supply chain will face suspension after May.
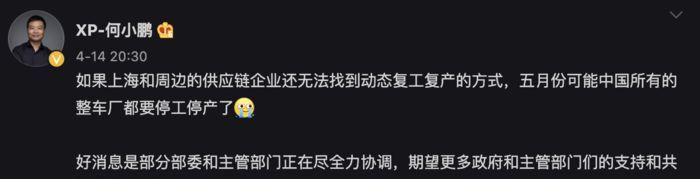
In addition to the car companies in Shanghai, many supply chain companies have also been affected by the epidemic, and the unstable supply of parts has made the suspension of production spread among domestic car companies, which is even worse in the case of the original lack of cores.
Small parts are difficult to turn down
Why can a single city in Shanghai influence the entire domestic auto industry? Perhaps many people do not know that Shanghai has always been the base camp of automobile supporting enterprises.
Since the 1980s and 1990s, Shanghai has promoted the supporting improvement of the autonomous industrial chain through the localization of Santana, and the German and American supply chain systems developed by SAIC Volkswagen and SAIC-GM have become more open, and Geely, Great Wall, Chery and other enterprises also have huge production capacity in Jiangsu and Zhejiang regions, further strengthening the industrial chain status of Shanghai and its surroundings.
From a logistics point of view, Shanghai Port is located at the mouth of the Yangtze River, carrying a large number of auto parts and vehicle import and export trade tasks, and Shanghai is also a central city integrating import, export, sales and research and development. Bosch, one of the world's largest automotive suppliers, has set up its Chinese headquarters in Shanghai and has auto parts production plants in Suzhou and Wuxi. At the same time, NXP, Qualcomm and other major automotive suppliers of electronic components will also set up R&D, sales and other departments in Shanghai.
Therefore, when any part cannot be sent to the car company in time, the car cannot be built. This is also the direct reason why He Xiaopeng and Yu Chengdong respectively sounded the supply chain danger warning.
Not only Xiaopeng and Huawei, on April 9, WEILAI Automobile issued an announcement saying, "Since March, due to the epidemic, the company's supply chain partners in Jilin, Shanghai, Jiangsu and other places have stopped production one after another, and have not yet recovered." Affected by this, WEILAI's vehicle production has been suspended. ”
Li Bin, CEO of Weilai Automobile, said, "A car is not as good as a part. Affected by the epidemic in Changchun and Hebei, we cut off some parts in mid-March, relying on some parts inventory to barely support until last week. Recently, there have been epidemics in Shanghai and Jiangsu, and many partners cannot supply goods and can only suspend production. ”
On the evening of April 13, Great Wall's tank brand announced that due to the impact of the epidemic, the tank 300 model involved a total of 8 suppliers to stop work and stop operation, which affected the tank 300 to suspend production from April 14.
According to the report of Guosen Securities, there are about 23 independent parts and components companies in the epidemic-affected areas, including 17 in the Shanghai area, mainly supplying SAIC Motor, Yutong Bus, Dongfeng Motor, Ford, Mercedes-Benz, Honda, Toyota, etc., while there are 4 in Changchun and 2 in Guangzhou.
A total of 21 foreign-funded parts companies were affected, including Bosch, Yazaki, Denso, GATSCO, ZF, Magna, Faurecia, Valeo, almost all of which have production bases in Shanghai, and supporting customers include Volkswagen, General Motors, Ford, SAIC, FAW, Toyota, Mercedes-Benz, BMW, etc.
After the closure of Shanghai, the logistics of factories and inter-provinces and regions have stagnated, and the raw materials of some auto suppliers cannot be transported from Kunshan and Zhejiang to Shanghai, or the shipment is delayed, and the production rhythm is slowing down, which has brought a heavy blow to the entire auto industry.
The most obvious phenomenon is that the car companies that used to be "Party A" are now more like "Party B" in the industrial chain, and they have gradually lost the ability to negotiate in the process of car manufacturing.
The supply chain determines the life and death of car companies
The problem of lack of cores, parts and components and lack of battery raw materials for several consecutive years has made the entire automotive industry understand that the competition of new energy in the future is not a battle between car companies and car companies, but an all-round competition between the industrial chain and the ecological chain.
As of April 20, in addition to BYD, the supply chain of other car companies has basically been affected, and the reason why BYD can stand alone is that its supply chain is highly vertical, and core components can be produced and supplied by themselves. On the other hand, those car companies that do not have their own production and self-supply are gradually losing their right to speak, whether they can produce cars no longer depends on the strength and output of car companies themselves, and the supply chain determines the life and death of car companies.
At present, the biggest impact on car companies is the battery and chip, which as the core components of intelligent electric vehicles, whether car companies can deliver on time is up to them.
Suppliers are too concentrated and fail to coordinate capacity according to delivery schedules is a direct cause of the chip shortage. According to the statistics of the Association of Passenger Vehicles, each vehicle is equipped with an average of more than 20 MCU chips. According to the data of China's automotive chip industry innovation strategic alliance, the import rate of automotive chips in mainland China exceeded 90% in 2019, mainly from five major automotive MCU suppliers such as Renesas Electronics, NXP, Infineon, STMicroelectronics, and Texas Instruments, while the foundries are mainly TSMC, UMC, and GF.
But the lack of core is not a problem that only appears now, from the first half of 2020, the progress of new energy vehicle electronics has accelerated, and the original mobile phone chips have grabbed production capacity with each other, but under the epidemic, not many companies dare to expand production capacity and stop at any time, which has led to the shortage of automotive chips so far. The suspension of other supplier categories has a great impact on the industrial chain, which has aggravated the delay in car delivery, and the phenomenon that sales do not know when the new car will be delivered.
It can be seen that the layout of car companies to invest in the upstream and downstream of the industrial chain, it is crucial to have a controllable supply and price, otherwise sooner or later they will face the dilemma of being stuck in the neck or without rice.
In fact, in the rapid transformation of the new four modernizations, more and more automakers are also realizing that the traditional model of outsourcing parts and electronic products to suppliers and then integrating them is no longer suitable for the development needs of smart electric vehicles.
If the long-term zero relationship in the past is that the automaker is in a dominant position and the parts supplier is in a subordinate position, then the relationship now becomes more complicated, and the head parts manufacturer has become the dominant player in the substantive sense in some fields, and the car company has become a subordinate.
In the era of new energy, suppliers also hope to seek more investment growth opportunities from the upstream and downstream of the electric vehicle industry chain, but behind the new zero game, which side can represent the future needs to be observed, it can be determined that the final supply and demand side is not a competitive relationship, but to seek common ground while reserving differences.
Supply chains are blocked, who is most nervous?
In this context, which car company is most likely to survive this "cold winter"?
Zhang Yongwei, secretary general of the China Electric Vehicle 100 Association, said at the third international symposium across the oil age, "The supply chain is a key threshold for the future development of electric vehicles and intelligent vehicles. This supply chain is globalized, and companies will be greatly affected by external factors such as international markets. In particular, the epidemic, trade disputes between major countries, technological competition, and shipping will affect the pattern of the automotive industry supply chain. ”
Zhang Yongwei said that the current domestic automotive supply chain is facing multiple challenges. On the one hand, the independent production capacity of key components is weak. For example, among the world's top 20 automotive semiconductor manufacturers, there is only one local Chinese company, and some key components are imported more than 80%.
Let's take a look at what car companies are doing for the supply chain at present.
From the perspective of battery companies, the head enterprises with sufficient funds settle upstream materials through equity acquisition, self-research, and large-scale order binding, and this year, GAC Aean will build an independent battery cell production line, magazine batteries, super-speed batteries, sponge silicon anode chip batteries and other independently developed battery cell technology to achieve independent mass production;
Great Wall Motors split the power battery business to establish Honeycomb Energy, which is scheduled to be listed on the Science and Technology Innovation Board at the end of the year; BYD, which has been deeply involved in the battery field for many years, naturally controls a large number of power lithium-ion battery industry resources, and in response to its own rapidly growing orders due to blade batteries and DM-i technologies, the first pure electric vehicle will be launched with Toyota at the end of the year.
"It should be an inevitable trend for vehicle companies to build their own battery factories." Cui Dongshu, secretary general of the National Passenger Car Federation, said that the battery is similar to the engine of a fuel vehicle, and car companies can build their own engine plants and transmission factories to achieve integrated control. "Self-built battery factories will also be in this style in the future, and each vehicle company will have its own core technology foundation."
Under pressure, more and more Chinese car companies are accelerating their layout in the semiconductor field. In December last year alone, Great Wall Motor signed a strategic investment agreement with Tongguang Co., Ltd. to officially enter the third-generation semiconductor industry and promote the industrialization of silicon carbide semiconductor materials and chips; Geely and Baidu-invested Yijiatong Technology launched the first domestic vehicle-grade 7nm intelligent cockpit chip "Dragon Eagle One". In addition, SAIC Motor said on the interactive platform that with the rapid development of intelligent electric vehicles, the company is stepping up the layout of the field of automotive semiconductors, and the possibility of self-developing some automotive semiconductor and chip technologies in the future is not ruled out.
The new forces of car-making are not far behind. "Wei Xiaoli" has built an autonomous driving team and started the self-research process of automatic driving chips; Zero Run Auto has released an AI intelligent driving chip Lingxin 01 with independent intellectual property rights, and the first model equipped with this chip, Zero Run C11, has been delivered in October 2021.
Even if car companies do not produce chips, they must master relevant technologies and patents, so that they are not completely subject to semiconductor manufacturers. The lack of core production is undoubtedly a great test for car companies, especially for car companies that rely too much on imported chips, and the safety and security of the supply chain has become an important proposition that they have to face.
Going back to the original question, supply chains are blocked, who is most nervous? From the layout of these two years, the first-line traditional car companies, the head of the new forces are not nervous, the most nervous should be those ranked in the perennial rank of 5 outside the second- and third-tier car companies, they do not have enough strength to self-research, but also do not have enough funds to open up the supply chain, can only conform to the times with the tide, this epidemic may also be seen as a car company reshuffle, can survive May has become the criterion for judging the strength of car companies.
Supply chain logistics into a hot potato
In addition to the supply chain dispute, the challenges of car companies are far more than this, after suppliers resume work, whether they can solve the current supply crisis of China's automotive industry depends largely on whether they can solve the logistics situation under the post-epidemic situation.
Car companies have their own methods, SAIC-GM Pudong many factories to achieve closed-loop production, obtained truck delivery passes, to a certain extent to ensure the supply of materials; SAIC passenger cars prepared emergency materials in advance, about 5,000 employees sleep in the factory to maintain closed production; Zhiji Automobile rushed to Pudong 4 hours before the sealing and control of a large number of materials, and in the community closed-loop isolation control, organized a group of teams with luggage to stay in the Port Factory, into the closed-loop management.
Even so, as the sealing time continues to be extended, personnel and parts cannot be replenished in time, and closed-loop production cannot escape the doom of production stoppage.
For car companies, it is not a simple matter to fully resume work and production, far from allowing workers to return to the workshop and then restart the production line. To start a production line, it is impossible to have a production line and workers, but also raw materials and parts. At present, the core problem is that the logistics dilemma caused by closed management, the supply of upstream parts and components to Shanghai, the finished products of the downline to be sent out of Shanghai, and even the supply chain logistics within Shanghai, in this special period, are necessary to carry out proper coordination.
At present, there is a large area of congestion of freight ships in major ports in Shanghai, Yangshan and Ningbo, highway transportation is also not optimistic, and logistics transportation has an embarrassing situation of high freight of 50,000 yuan and still no truck drivers are willing to take orders.
These problems are no longer problems that car companies can solve, which requires the joint efforts of supply enterprises, production enterprises and logistics enterprises, but it is more necessary to manage and coordinate the overall logistics situation of local and national areas.
The good news is that the relevant national units are studying countermeasures for the resumption of logistics. According to Xinhua News Agency, on April 18, the national video conference on ensuring the smooth flow of goods to promote the stability of the industrial chain supply chain was held in Beijing, which mentioned that "it is necessary to issue and use the national unified pass in sufficient quantity, the nucleic acid test results are mutually recognized nationwide within 48 hours, and the closed-loop management of 'picking and leaving is pursued' is implemented, and the passage must not be restricted on the grounds of waiting for nucleic acid results." ”
At the same time, in view of the current difficulties in the automotive industry chain supply chain, the Ministry of Industry and Information Technology has also quickly set up a smooth coordination platform for the automotive industry chain supply chain, overall coordination, accurate docking, since the platform was launched on April 11, 585 registered enterprises, 366 problem messages, involving nearly 20 provinces and cities more than 1,700 vehicle and key parts enterprises.
Judging from the current situation, the key difficulties of the supply chain problem are mainly concentrated in two aspects, one is that logistics and transportation are blocked, raw materials cannot be transported in, and finished products cannot be transported; second, supply chain enterprises stop work and production, affecting the production of complete vehicles.
Logistics dredging can only solve the urgent need, and what needs to be changed is still the relationship between car companies and supply chains. For car companies, the most important thing is to establish their own warehousing system, car companies in the past requirements for the supply chain is "according to its production rhythm and production demand for supply", from the current trend point of view, if still according to this set of old standards, obviously can not keep up with the market rhythm. Under the turmoil, who can dance with change, who can change at the right time, who can stand and make money.
Wisdom and action
"Change" has become the key word for car companies in 2022, the automobile is the mainland's second only to the real estate industry, on the one hand, the automobile industry is pivotal, the pull effect on the upstream and downstream industries is extremely prominent, on the other hand, the automobile is still the main bulk consumer goods, stable automobile consumption, for the stability of consumption of the basic disk is also critical.
However, if there is a danger, it is organic, and the powerful faction will show more and more frustration and courage in the face of difficulties, turning "change" into "breaking the situation", and China's auto market will regain its vitality. Black swan events are frequent, and embracing change is the new way out.