For decades, carbon fiber has not been able to enter the mainstream automotive applications as the composites industry hoped, but the alternative composite applications show that the opportunities for carbon fiber applications in the automotive industry in the future are still bright.
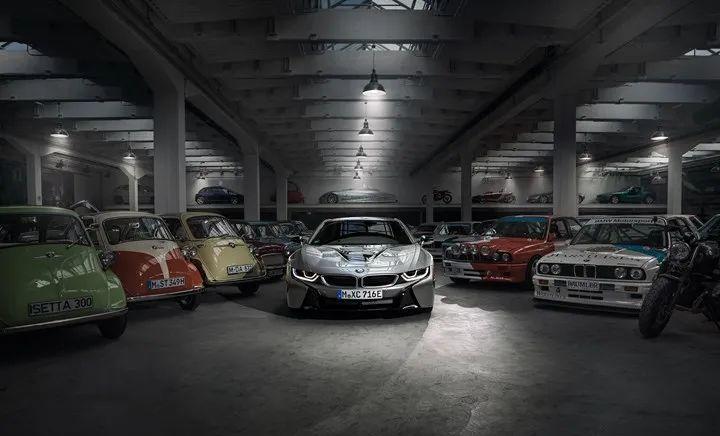
Image from BMW
For at least 40 years, the allure of the automotive market has attracted the attention of carbon fiber producers, but the prediction of large-scale adoption of carbon fiber has never been met. The first high-volume application was for the fiber-wound drive shafts on the 1984 Ford Econoline full-size van, with an annual production of about 40,000, but it was discontinued in less than 3 years, mainly due to cost issues. In the following decades, although carbon fiber shafts have appeared on OEM automotive platforms, they have always been relatively low-volume products. In the early 2000s, interest in carbon fiber continued to grow as a range of supercars and sports cars made heavy use of low-cost carbon fiber, but these applications did not move to mainstream vehicles.
In 2013, with the launch of the BMW i3 and i8, which use a lot of carbon fiber, and the establishment of a dedicated supply chain for BMW to meet its demand for carbon fiber and carbon fiber components, other automakers were expected to follow suit, but none of them did. In 2015, bmw praised the Carbon Core multi-material concept used on its mainstream 7 Series platform as a breakthrough in triggering the widespread use of carbon fiber components. While the concept has made progress on BMW's upcoming iX SUV, BMW is an isolated case, not a rule. At JEC World 2017, at least a dozen B-pillar prototypes of all-carbon fiber or carbon fiber/steel hybrid materials appeared, which became the "killer application" of carbon fiber in automobiles. While several producers have deployed the technology, it has not really become popular globally and more efforts are needed to reduce costs before this application becomes a better solution than all-steel components.
In November 2021, at the Carbon Fiber Conference held by Composites World in Salt Lake City, USA, industry consultants Dan Pichler and Tony Roberts pointed out that production of bmw's i3 platform is coming to an end, so the amount of carbon fiber used in the automotive industry will drop significantly. They also stressed that no large-scale carbon fiber vehicle projects that have been announced are currently underway, and that carbon fiber applications in automobiles are expected to grow at a compound annual growth rate of only 2.4% by 2026, and are mainly used for racing, personalized and small-volume production niche car platforms.
It's still to be done. With the massive shift from internal combustion engines (ICEs) to electric powertrains, isn't it all the more important to lose weight given the extra weight that batteries bring? Doesn't this portend a huge demand for carbon fiber? For the first question, the answer is yes, that the weight reduction of the car is still very important. For the second question, while carbon fiber is still a consideration, it is premised on the premise that it is cost-effective. There are currently several ways OEMs can reduce the weight of automotive components, including replacing steel with aluminum.
Composites are now very attractive for lightweight battery housing applications on battery electric vehicles, as demonstrated at the Society of Plastics Engineers (SPE) in the United States at the Automotive Composites Conference and Exhibition (ACCE) in November 2021. In this conference, most of the presentations around the topic were introductions to glass fiber reinforced composite battery shells, which attracted a large audience. These battery cases are lighter than metal and can incorporate features such as thermal insulation, flame retardancy and electromagnetic shielding at a competitive cost.
Solutions to replace carbon fiber structures with high volume percentages also continue to show good economic benefits. More and more van platforms incorporate composite cabin bed panels made of UV-resistant glass fiber sheet molding compounds (SMCs). A project by the Advanced Composites Manufacturing Innovation Institute (IACMI) in Knoxville, Tennessee, in collaboration with Volkswagen Corporation of the United States, showcased a glass fiber SMC's SUV rear tailgate that is 36 percent lighter than the steel rear tailgate and 9 percent lower recurring costs. Another IACMI project demonstrated that adding 10% cut recycled carbon fiber to polypropylene can reduce the weight of injection molded parts by 40% and part costs by 30% compared to pure PA/PPE engineered thermoplastics. These present opportunities not only for recycling carbon fibers, but also for fibers made from low-cost precursors such as textile PAN and coal tar bitumen.
So, is the use of traditional carbon fiber in the automotive industry a dead end? Not exactly! However, don't expect vehicles such as the i3, which use a lot of carbon fiber, to enter mass production. There is a narrow path to a carbon fiber structure with a 50% fiber content at a cost of $22/kg, which requires improvements in the entire production chain and will open up opportunities in a single component such as the B-pillar. More recently, we can see carbon fiber parts, possibly pultruded parts, used as rigid components in overmolded hybrid structures (including structural battery shells), where glass fiber reinforced polymers will act as a compensatory balance.
In short, under the leadership of glass fiber, coupled with the application of traditional carbon fiber in niche cars, composite materials have broad prospects in the automotive market. For suppliers of recycled carbon fiber and the use of alternative precursors to make carbon fiber, the space for opportunities will be brighter.