First, the material characteristics: high performance but also high barriers
Carbon fiber is a kind of inorganic fiber material. Fiber-reinforced composites (FiberReinforcedPolymer: FRP) are composites formed by forming processes such as winding, molding or pulling around the fiber material and the matrix material. According to the different reinforcing fiber materials, it can be divided into two categories: organic fibers and inorganic fibers, inorganic fibers include glass fibers, carbon fibers, boron fibers, silicon carbide fibers, etc., and organic fibers include aramid fiber, nylon fiber, polyolefin fiber, etc.
Carbon fiber (carbonfiber, referred to as CF) is a high-strength, high-modulus inorganic polymer fiber with a carbon content of more than 90%, and a variety of substrates after the composite process made of carbon fiber composite materials (CFRP), can be applied in aviation, military industry, wind power blades, automotive components, sports and leisure products and other industrial and civilian fields. Carbon fiber materials have two significant characteristics of high performance and high barriers, and are known as "black gold".
Carbon fiber is classified by raw materials. Carbon fiber is mainly divided into PAN (polyacrylonitrile) based carbon fiber, asphalt-based carbon fiber, viscose-based carbon fiber and so on. PAN-based carbon fiber is the mainstream product of the current carbon fiber market due to the simple preparation process and the better performance of the product, accounting for about 90% of the total global carbon fiber production. Therefore, at present, carbon fiber generally refers to PAN-based carbon fiber.
Carbon fibers are classified by strength and modulus. The main mechanical properties of carbon fiber are tensile strength and tensile modulus, which are divided into general carbon fiber, high-strength carbon fiber, high-mold carbon fiber, ultra-high-strength carbon fiber, and ultra-high-mold carbon fiber. In actual use, due to Toray's leading position in the industry field, its product number is used as an industry standard, such as T300, T800, M55, etc. corresponding to carbon fibers with different properties, the high strength type is T sequence, and the high model is M sequence.
Carbon fiber is divided into small tows and large tows according to the number of fibers. Single carbon fiber can not be applied, the actual use of carbon fiber is made of a certain number of carbon fiber filament bundles, 1K represents a bundle of carbon fiber in 1000 wires, usually less than 24K carbon fiber is called small tow carbon fiber, small tow carbon fiber is mainly used in national defense and military industry (missiles, rockets, satellites, etc.), aerospace and sports and leisure fields, so it is also known as "aerospace-grade" carbon fiber, the price is more expensive than large tow carbon fiber. Carbon fibers above 48K are usually called large tow carbon fibers, which are mainly used in transportation, wind power blades, medicine and health, textiles, electromechanical and other industrial fields, so they are called "industrial-grade" carbon fibers.
Large tows are relatively small, and downstream applications are more popular. In the global carbon fiber demand structure in 2020, the sales volume of large tows accounted for about 45%, the sales volume of small tows accounted for about 55%, and the proportion of large tow sales showed an increasing trend. Large tows have relatively low product performance but low preparation costs compared to small tows. From the perspective of the average selling price of the global market, the average price in the wind power field is about 90,000 yuan / ton, mainly based on domestic and foreign T300-level 24K, 48K, 50K and other products.
1, high performance: lightweight and high strength, excellent lightweight materials
Lightweight, strong, modulus, carbon fiber has excellent performance and is difficult to catch up with. Carbon fiber has excellent mechanical properties and chemical stability, low density than aluminum, strength than steel, is currently mass-produced high-performance fibers with the highest specific strength and the highest specific modulus of fibers, with light weight, high strength, high modulus, conductivity, heat conductivity, corrosion resistance, fatigue resistance, high temperature resistance, small expansion coefficient and a series of other materials are difficult to replace the excellent performance.
From the perspective of physical properties, carbon fiber has small density, light weight and high specific strength.
First, the density is small, the density of carbon fiber is 1.5 ~ 2g / cm, equivalent to 1/4 of the steel density, 1/2 of the density of aluminum alloy, and its specific strength is 16 times larger than steel, 12 times larger than aluminum alloy.
Second, the strength is high, the tensile strength of carbon fiber can reach 3000~ 4000MPa, the elasticity is 4 to 5 times greater than steel, and 6 to 7 times larger than aluminum.
The third is anisotropy, the coefficient of thermal expansion is small, the thermal conductivity decreases with the increase of temperature, it is resistant to sudden cold and rapid heat, and even if it suddenly drops from a high temperature of several thousand degrees to normal temperature, it will not explode.
The fourth is conductivity, high modulus fiber is 775μΩ/cm at 25°C, and high-strength fiber is 1500μΩ/cm. Fifth, high temperature resistance and low temperature resistance is good, carbon fiber can be used at 2000 °C, and does not melt and soften under a non-oxidizing atmosphere of 3000 °C. At temperatures of -180°C, steel becomes more brittle than glass, while carbon fiber is still soft and not brittle. However, the impact resistance of carbon fiber is poor and it is easy to damage. (Carbon fiber composites are not resistant to pulling and puncture, so avoid letting carbon fiber products touch sharp small stones or sharp objects in life to prevent cracking.) )
From the perspective of chemical properties, carbon fiber has acid resistance, oil resistance, radiation resistance and other properties. Carbon fiber is inert to acid and can resist the erosion of concentrated hydrochloric acid, phosphoric acid, sulfuric acid, benzene, acetone and other media. Carbon fiber is placed in 50% hydrochloric acid, sulfuric acid, phosphoric acid, after 200 days its elastic modulus, strength and diameter are basically unchanged; in 50% nitric acid concentration is only slightly expanded, its corrosion resistance exceeds that of gold and platinum. However, carbon fibers will oxidize under the action of strong acids, and metal carbonization, carburizing and electrochemical corrosion will occur when they are composited with metals, so surface treatment must be carried out before use.
Carbon fiber is an excellent lightweight material. Carbon fiber's superior specific modulus and specific strength make it an excellent lightweight material. In automotive applications, compared with high-strength steel, carbon fiber can achieve 60% weight reduction, so in a number of areas that require structural lightweight, such as sports, aerospace, etc., carbon fiber can be seen.
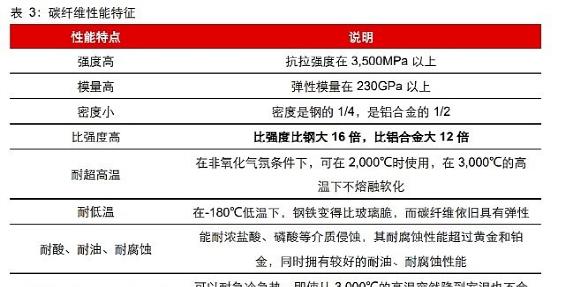
2, high barriers: high technical barriers, leading enterprises moat deep
The carbon fiber production process is complex and requires extremely high equipment and technology. The preparation process involves many control points, each control point has a corresponding parameter, the accumulation of these parameters often takes several years of cycle, and only if each parameter is optimal, the performance of the product produced can reach the best. Taking the pre-oxidation link as an example, the link needs to accurately control the accuracy and range of the temperature, otherwise it will significantly affect the tensile strength of carbon fiber products and even cause the phenomenon of wire breaking.
Funding barriers are high. Carbon fiber production line investment threshold is higher, from the enterprise announcement of the production capacity plan, 10,000 tons of investment is generally 2 billion yuan or more, if it is a high-performance carbon fiber production line, then the investment of 10,000 tons is more than 10 billion, high capital barriers make it difficult for a large number of enterprises to enter this industry. In addition, when the core technology in the early stage has not yet been broken, not only the investment in the production line is high and the return on investment is low, but in recent years, due to the improvement of production efficiency, the return on investment of enterprises has improved. Even so, taking the industry leader Zhongfu Shenying as an example, the net profit of carbon fiber tons in 2020 is about 23,000 yuan, and the return on investment period is about 10 years.
The technical barriers have a long breakthrough period, and the moat of leading enterprises is deep. The technical barriers in the carbon fiber industry are very high, which are reflected in three aspects: formula barriers, process barriers and engineering barriers, and the difficulty of the three increases in turn. Although the formula can be obtained by directly purchasing and digging up technicians, it still takes time to absorb and digest, and the breakthrough time of the formula barrier is 1-2 years; if you want to break through the process barrier, you also need to invest a lot of energy to run in and adjust on the basis of having the formula, which usually takes 3-5 years; the engineering system requires coordination between the production processes, and requires the enterprise to invest a lot of capital to design, transform, adjust the equipment and train personnel, and the barrier breakthrough time is more than 5 years. Therefore, the breakthrough period of the three major technical barriers of carbon fiber is more than 10 years in total, and the first-mover advantage of enterprises that have mastered mature technologies is great, and the moat is deep.
The added value of the industrial chain is as high as 200 times. Due to the high difficulty of carbon fiber preparation and complex process, the higher the added value of its products downstream, especially the high-end carbon fiber composites used in the aerospace field, because downstream customers have very strict requirements for their reliability and stability, and the product price is also geometrically higher than that of ordinary carbon fibers. According to the statistics of Jiangsu Hengshen Public Transfer Prospectus (2015), the price per kilogram of the same variety of raw silk, carbon fiber, prepreg, civil composites, automotive composites and aviation composites is about 40 yuan, 180 yuan, 600 yuan, less than 1000 yuan, 3000 yuan and 8000 yuan, respectively, and the price of each first-level deep processing product will achieve a leap, and the price of aviation composites has increased by 200 times compared with the original silk.
The price of carbon fiber far exceeds that of other alternative materials. According to the average price per kilogram, the average price of ordinary carbon fiber is about 160 yuan / kg, which is 6-7 times that of alloys such as aluminum and magnesium, and 8 times that of glass fiber. And even taking into account the amount of carbon fiber used, this huge price difference still cannot be smoothed out. According to BMW's calculation of the unit weight reduction cost of the car, the unit weight reduction cost of using carbon fiber is about 32 /kg, which is still 7 times that of aluminum.
Second, the qualitative change of the industry: when the domestic substitution is accelerated
Chinese mainland carbon fiber mainly relies on imports, and the effective production capacity is insufficient. Under the pressure of overseas leading technology blockade and price war, the domestic carbon fiber industry has developed slowly.
Carbon fiber has a very high strategic position. High-performance carbon fiber can be used to manufacture missiles, fighters and other defense heavy weapons, and has long been on the US embargo list against China, along with atomic energy and semiconductor core technologies.
The policy attaches great importance to the development of carbon fiber. In the decades since Jilin Petrochemical began PAN-based carbon fiber research in 1962, carbon fiber has benefited from the high attention of the policy, and has been led by General Zhang Aiping and Academician Shi Changxu twice. In the 863 and 973 programs, carbon fiber is also regarded as a key research and development project. With the beginning of Sino-US trade frictions, foreign countries have further tightened the supply of carbon fiber to China, and the localization of carbon fiber is becoming more and more urgent.
Under the policy increase, domestic enterprises attach great importance to research and development, and the number of patent applications continues to rise. With the joint efforts of the whole industry, the mainland carbon fiber technology has entered the world's leading level, and after the technological breakthrough, the demand has exploded synchronously, so the industry has ushered in qualitative changes.
1. Technological breakthrough: The technical path of large and small tows is different, and the barriers are also different
Small tow and large tow carbon fiber have achieved technological breakthroughs, there are differences in the technical routes of the two, large tow due to the cost-effective advantage, it is easier to usher in the large-scale industrial field. At present, the development path of domestic carbon fiber enterprises is mainly two categories: one is small tow, domestic substitution is more urgent, and the three major leaders have risen. Small tow carbon fiber is used in the military field, so domestic substitution is more urgent, under the support of key investment and demand, small tow carbon fiber enterprises to achieve domestic substitution earlier.
Taking the dry spray wet method as an example, the earliest was zhongfu Shenying in 2013 to take the lead in breaking through the thousand-ton carbon fiber precursor dry spray wet spinning manufacturing technology and achieved stable operation in 2015, and then Guangwei Composite, Zhongjian Technology, Hengshen Shares and other enterprises have successively realized the dry spray wet spinning process.
The second is the large tow, the use of acrylic process is the development trend, Jilin Carbon Valley took the lead in achieving a breakthrough. In recent years, the mainland large tow carbon fiber technology has achieved a breakthrough: 1) Jilin Carbon Valley in the original Qifeng chemical fiber 20 years of acrylic preparation on the basis of research and development, in 2008 set up has obtained DCC as a solvent wet two-step method proprietary technology, in 2013-2015 gradually realized the small tow products OF MAC as solvent wet two-step method technology update and optimization, 2017-2019 breakthrough 24K, 25K, 48K and other large tow products stable industrial production technology, Break the monopoly of the international carbon fiber giant in the production technology of the raw silk; 2) Shanghai Petrochemical was once the largest acrylic fiber production enterprise in China, and in 2018, it officially said that it broke through the 48K large-tow carbon fiber, and began to build a 24,000-ton large-tow raw silk and a 12,000-ton 48-karat large-tow carbon fiber project in 2021.
Preparation difficulties: There are differences between large and small tows. Large tow carbon fiber performance is not as good as small tow, but under the same production conditions can increase carbon fiber single-line capacity, reduce production costs, thereby enabling large-scale industrial applications. Due to the high throughput of large tow carbon fiber, there are many complex technical and engineering problems in multiple system links such as primary silk, polymerization, pre-oxidation, and carbonization. Including but not limited to: one is the consistency, the number of fibers is more, it is more difficult to maintain the consistency of each fiber; the second is the problem of hair, the more fibers there will be more hair, and the proportion of hair needs to be controlled within a reasonable range; the third is carbonization, and the carbonization link of the hair wire may undergo a violent chemical reaction, resulting in some bond breaks in the molecular structure of the fiber. From the perspective of the development path of Japan's Toray, Toray continues to break through high strength and high mold on small tows, but does not have large tow carbon fiber production capacity, but through the acquisition of the United States Zoltek to obtain large tow carbon fiber production capacity.
The technical route of large tows: Extending downstream from the acrylic process is an overseas trend. The basis of acrylic fiber process is an important evaluation index for the development of the potential of large tow carbon fiber, and the raw silk preparation technology of overseas large tow carbon fiber is derived from the acrylic fiber industry. The world's acrylic technology route is relatively concentrated in the two-step wet spinning production with DMAC as the solvent and NaSCN as the solvent, the former is an organic solvent and the latter is an inorganic solvent. At present, in the field of large tow carbon fiber, enterprises that have broken through or are expected to break through the original yarn technology have the basis of acrylic process and have mastered the production of solvents, including Jilin Carbon Valley and Shanghai Petrochemical.
2, strong demand: wind, solar and hydrogen and other fields of demand outbreak, leading the world
China's demand for carbon fiber is growing rapidly, and its growth rate is leading the world. In 2015, the domestic demand for carbon fiber was only 17,000 tons, an increase of more than 3 times in just five years, reaching 49,000 tons in 2020, and the domestic demand for carbon fiber achieved more than 30% growth for three consecutive years, far exceeding the growth rate of the global market. With the expansion and development of downstream applications, China may become a major consumer of carbon fiber in the world, and the demand for carbon fiber has room for substantial growth.
The demand for carbon fiber in the new energy field (wind, light, hydrogen) ushered in rapid growth. Sports demand accounts for 30% of the downstream applications of the mainland, and the demand has maintained steady growth; although the amount of aerospace is not high, the unit price is far more than other fields, and the future is expected to grow steadily with military expenditure. In recent years, carbon fiber has been widely used in wind power blades, photovoltaic silicon crystal thermal field materials (carbon carbon composites), winding composite hydrogen storage cylinders, etc. because of its good performance, which has significantly benefited from the growth of the new energy industry.
Third, new energy strong boost 1, wind power: a breakthrough in the rise of demand
In the more than 100 years of wind power development, blade materials have successively appeared in wood, cloth, aluminum alloys and so on. However, in the process of development, composite materials with high specific strength and strong designability have become the main manufacturing materials of commercial-grade blades, and the wind power field has also become one of the most important application areas of composite materials.
Wind turbine blade is a thin shell structure made of composite materials, generally composed of blade girder, web, outer skin, composite materials in the entire wind power blade weight generally accounted for more than 90%. Composite blades were originally made of glass fiber reinforced unsaturated polyester resin systems, which are still the materials used in most blades to this day. However, with the increase of fan power, the length of the blade continues to increase, and the weight of the blade also increases, in this case, carbon fiber composites with high strength and high mold and low density begin to emerge.
Carbon fiber blades are mainly used in the main beam or segmented blade connection area in structural materials, bearing the main load and using a large amount. In 2020, the global wind power carbon fiber consumption is about 30,000 tons, of which at least 90% is used in the form of pultrusion board to the blade main beam; the earliest foreign pultrusion carbon plate is applied to the blade, so far there have been more than ten years of batch application experience; some domestic manufacturers have completed the trial production or small batch application of the pultruded carbon plate on the new leaf type, and the research and development of the new leaf type of the pultruded carbon plate in the industry has accelerated. 2021 is the research and development and reserve period of the new leaf type of the pultruded carbon plate, and it is expected that the market demand for the pultruded carbon plate will soar in 2022.
The use of carbon fiber can help reduce the weight of the blade, but in the current price gap between carbon fiber and glass fiber, it will also increase the cost. Taking the SNL100-00 wind power blade developed by the Sandia National Laboratory in the United States as an example, if the glass fiber of the main beam is replaced by carbon fiber, the total weight of the blade can be reduced by 35%, but the material cost can be increased by 37%. After replacement, the final carbon fiber accounts for 13.6% of the blade weight and 53.1% of the cost of the blade material.
The penetration rate of carbon fiber has increased to the core growth logic in recent years. With the rapid advancement of the construction process of wind power in the mainland, wind power has also grown into the largest part of the current downstream application scale of carbon fiber, with domestic demand of about 20,000 tons in 2020, a significant increase compared with 0.3 million tons in 2016, and the proportion of carbon fiber demand in 2020 will reach 40%. From 2016 to 2019, the installed capacity of wind power was relatively stable, and the demand for carbon fiber still increased significantly, mainly due to the continuous increase in penetration rate, which is behind the large-scale wind turbines that put forward higher requirements for wind power blades.
Fan large capacity, large blade has become a trend. The sweeping area of high-power wind turbines has increased significantly, which can effectively improve the utilization rate of wind energy. Therefore, the increase in the individual rated power of the fan can reduce the unit power generation cost of the fan. In 2018, the average installed power of the mainland was 2.2MW, an increase of 108% over the 1.06MW in 2007, and the trend of large-scale is obvious. According to the survey data, the length of the fan blade is directly proportional to the power of the fan. At the same wind speed, the longer blade has a larger sweeping area, and the increase in wind catching capacity provides a guarantee for the high-power operation of the fan. Around 2000, 32-47.9 meters were dominant; around 2005, 48-59.9 meters were dominant; and after 2010, 60-90 meters became dominant.
Glass fiber materials are gradually difficult to meet the needs of large blades, and carbon fiber is expected to accelerate penetration. The traditional blade manufacturing materials are mainly glass fiber composites, and when the blade length exceeds a certain value, the full fiberglass blade weight is larger, and there are more deficiencies in performance, or resonance problems, torsion problems and so on. Glass fiber can no longer meet the requirements of large-scale and lightweight wind power blades. The carbon fiber composite material has a lower density and higher strength than the glass fiber composite material, which breaks through the performance limit of the glass fiber composite material, and can ensure that the wind power blade is greatly reduced in length while the weight is greatly reduced. Under the current trend of continuous large-scale wind turbines, the penetration rate of carbon fiber will continue to increase.
Installed capacity growth and penetration enhance resonance, carbon fiber ushered in a breakthrough in the rise of demand. The Beijing Declaration on Wind Power puts forward clear goals for the development of wind power, and the State Council also proposes to accelerate the construction of large-scale wind power bases, and the growth rate of total installed capacity in the future can be expected. At the same time, with the increased emphasis on the development of low wind speed wind areas and the continuous development of sea wind, the trend of wind turbines to develop high power has accelerated, the requirements for blade length are higher, and the penetration rate of carbon fiber will continue to increase. According to this calculation, the demand for wind power carbon fiber is expected to reach 85,000 tons in 2025, with an average annual compound growth rate of 34%, corresponding to a market space of 6.8 billion。
2, photovoltaic: benefit from the double pull of penetration and demand
Carbon carbon composites are excellent thermal field materials. Carbon / carbon composite material is a carbon matrix composite material with carbon fiber as the reinforcing phase, which is currently one of the very few materials that can maintain high mechanical properties above 2000 °C, it has excellent properties such as low specific gravity, high specific strength, high specific mold, low coefficient of thermal expansion, thermal shock resistance and ablation resistance, and is a type of strategic high-tech materials that are focused on research and development in the field of new materials.
Carbon carbon composites have been widely used in the photovoltaic industry. In the early stage of the development of the photovoltaic industry, its single crystal drawing furnace and polycrystalline ingot furnace thermal field system component materials were mainly made of high-purity, high-strength isostatic pressing graphite imported from abroad. Graphite thermal field system products have the characteristics of high cost, long supply cycle and dependence on imports, which hinders the development process of the photovoltaic industry to reduce costs and expand scale. With the rapid expansion of the capacity of monocrystalline silicon drawing furnaces, from the 16-inch to 20-inch (1 inch = 25.4mm) thermal field around 2011 to the current 26-inch and 28-inch thermal fields, isostatic graphite, as a brittle material pressed by graphite particles, has been unable to adapt to the requirements of large thermal fields in terms of safety, and has lagged behind carbon-based composites in terms of economy. With the development of domestic advanced carbon matrix composite material preparation technology, advanced carbon matrix composite materials have become the best choice to reduce the cost of silicon crystal preparation and improve the quality of silicon crystals, and are gradually forming an upgrade of graphite material components in the crystalline silicon manufacturing hot field system, which is currently mainly used in single crystal drawing furnaces and polycrystalline ingot furnaces.
Carbon/carbon composite products are developing in the direction of high purity and large size. In the photovoltaic industry and semiconductor industry, due to the development of technology and the rapid iteration of products, the development of silicon wafers to high purity and large size is its basic trend, so in the application of high-temperature thermal field systems, the development of carbon/carbon composite products to high purity and large size is also an inevitable trend.
3, high-pressure hydrogen cylinders: a broad vision of fuel cell vehicles
High-pressure hydrogen storage is currently the mainstream way of vehicle hydrogen storage. Hydrogen as a new type of clean energy has been applied to fuel cell vehicles, and its hydrogen storage system is an important part of the car. Hydrogen energy can be stored in three states: gaseous, liquid and solid, and according to the different storage mechanisms, it can be divided into high-pressure hydrogen storage, liquid hydrogen storage, solid hydrogen storage, organic liquid hydrogen storage and other ways, of which high-pressure hydrogen storage is the most widely used way. This method uses gas cylinders as containers to store gaseous hydrogen through high-pressure compression, which has the advantages of low cost, small energy consumption, fast filling and degassing speed, and is also the mainstream way of hydrogen storage for current vehicles.
Carbon fiber winding high-pressure hydrogen cylinders enables high-pressure hydrogen storage to shift from stationary applications to automotive applications. In the high-pressure hydrogen storage technology, the most mature and low-cost technology is the steel hydrogen cylinder, the current industry widely uses 20Mpa steel hydrogen cylinder, but the steel hydrogen cylinder due to high weight, large volume-to-weight ratio, low hydrogen storage density, so it is not suitable for automobiles. At present, the international mainstream technology of automotive high-pressure hydrogen cylinders is to improve the structural strength of hydrogen cylinders and reduce the overall weight as much as possible by using aluminum alloy or plastic as the inner tank, and the outer layer is coated with carbon fiber. At present, 70MPa carbon fiber winding IV bottle has been the mainstream technology of foreign fuel cell passenger car hydrogen storage, 35MPa carbon fiber winding III bottle is still the on-board hydrogen storage mode of mainland fuel cell commercial vehicles, and 70MPa carbon fiber winding III bottle has been applied in small quantities.
Fuel cell vehicles are the key development direction of the country. The "New Energy Vehicle Industry Development Plan (2021-2035)" issued by the General Office of the State Council mentions the commercialization of fuel cell vehicles. In 2020, the five ministries and commissions of the state jointly issued the "Notice on carrying out the Demonstration Application of Fuel Cell Vehicles", which intends to carry out a four-year work on the creation of fuel cell vehicle urban agglomerations, adopt the method of "replacing compensation with awards", and reward the shortlisted demonstration city clusters according to their goals, and finally in September this year, the three urban agglomerations of Beijing, Shanghai and Guangdong led by Daxing District of Beijing, Shanghai and Foshan in Guangdong Province were officially selected. The demonstration city cluster focuses on the development of the fuel cell vehicle industry chain link, which is the middle and lower reaches of the hydrogen energy industry chain, involving the whole industrial chain of hydrogen energy production, storage, transportation, addition and use, which is conducive to promoting the development and reform of the hydrogen energy and fuel cell automobile industry.
Fuel cell vehicles are expected to break out in the future, and the hydrogen cylinder market is promising. "Mainland China will reach 50,000 fuel cell vehicles/year by 2025 and 5.2 million/year by 2050, and it is expected that the penetration rate of fuel cell vehicles in commercial vehicles will be 7% and 37% in 2030 and 2050, and 3% and 14% in passenger cars." According to this calculation, the demand for carbon fiber in the field of hydrogen cylinders will reach 16,000 tons in 2025, corresponding to a market size of 1.9 billion; the demand in 2030 will reach 171,000 tons, corresponding to 18.9 billion market size; and the demand in 2050 will reach 782,000 tons, corresponding to a market size of 62.6 billion.
Fourth, the qualitative change of the industry: supply optimization encounters demand outbreaks, and the replacement is fully accelerated
With technological breakthroughs and demand outbreaks, the carbon fiber industry ushered in a period of high-quality development. First of all, small tow and large tow carbon fiber have achieved technological breakthroughs, especially the low-cost advantage of large tow carbon fiber, which makes it possible for carbon fiber to increase the scale of carbon fiber in the industrial field; secondly, the domestic demand for new energy sources such as wind, photovoltaic and hydrogen has ushered in rapid growth, and the capacity utilization rate of enterprises has increased, which has further brought about cost reduction, thus promoting the overall acceleration of carbon fiber replacement applications. In the past few years, the unit cost of the head enterprise has decreased significantly, which verifies the downward shift of the supply curve under the technological breakthrough and strong demand.
Japanese and American companies are far ahead, but domestic companies are catching up quickly. In 2020, the total global carbon fiber production capacity is about 170,000 tons, of which Toray alone will reach 50,000 tons, whether it is the large tow market or the small tow market, it is divided up by Japanese and American companies. However, in recent years, the effective production capacity of mainland carbon fiber enterprises has expanded rapidly, which has changed the long-term phenomenon of "having production capacity but no output" in the industry, and the proportion of imports has continued to decline. The industry's capacity utilization rate was only 15% in 2015 and increased to 51% in 2020.
Technological breakthroughs superimpose scale effect, carbon fiber industry supply curve downward. In the past few years, the unit cost of the head enterprise has decreased significantly, which further verifies the downward shift of the supply curve under the technological breakthrough and strong demand. It can be seen that compared with the large tow, the cost of small tow carbon fiber leading enterprises ushered in a decline earlier, and the reason for judging is that the import substitution of small tow carbon fiber is more urgent, and the domestic aerospace demand supports the enterprise to usher in a faster cost decline. According to the Prospectus:
1) Jilin Carbon Valley has reduced its unit cost by 36% in 2018-2020;
2) The cumulative unit cost of Zhongfu Condor in 2018-2020 will decrease by 19%;
3) Guangwei composite carbon fiber business in 2014-2015 unit cost decreased by 65%, the business caliber of the last two years has been adjusted, only the cost structure of carbon fiber and fabric business was announced, and its unit cost decline rate slowed down;
4) The cumulative unit cost of the carbon fiber business of Zhongjian Technology has decreased by 33% from 2016 to 2018, and the decline rate has slowed down in the past two years.
From the perspective of material costs, the unit consumption of acrylonitrile has declined. The main raw materials consumed in the production process of carbon fiber precursor are acrylonitrile and oil agent, and the cost of acrylonitrile and oil agent accounts for about 90% of the total material cost; because the military products of Guangwei Composite and Zhongjian Technology are relatively high, the price of products is higher, so the direct material cost is relatively low. Due to its proximity to Jilin Petrochemical, Jilin Carbon Valley mainly purchases acrylonitrile from Jilin Petrochemical, and the oil is mainly from Japanese oil and fat producers Takemoto Oil & Fat Co., Ltd. and Matsumoto Oil & Fat Pharmaceutical Co., Ltd. Zhongfu Condor Acrylonitrile is mainly purchased from Jiangsu Sierbang Petrochemical Co., Ltd., and the oil agent is independently developed. For the largest proportion of raw materials - acrylonitrile, the unit consumption of Jilin Carbon Valley and Zhongfu Shenying is relatively ahead of other enterprises, and Jilin Carbon Valley has a slight advantage in procurement prices.
In the future, the cost of carbon fiber will continue to decline. In the future, starting from raw materials, processes, energy utilization, equipment, large-scale construction and other aspects of superimposed scale effect boost, carbon fiber cost reduction potential is larger. The production and preparation cost of carbon fiber is mainly included in PAN filament (purchase or preparation), pre-oxidation, carbonization (low temperature carbonization, high temperature carbonization), surface slurry and winding costs, the specific cost components are: primary wire (51%), pre-oxidation (16%), carbonization (23%), surface treatment (4%), packaging and other remaining costs of 6%.
It is estimated that with the increase of production scale, the production costs of raw silk and carbon fiber have decreased significantly, mainly due to the dilution of large-scale direct costs, and the impact of indirect production control factors on the total cost of production has gradually weakened. For example, the unit cost of raw silk with a production capacity of 3300t is 38,000 yuan / ton, which is 20% lower than the unit cost of 47,800 yuan / ton of the 1100t production line. The unit cost of carbon fiber with a production capacity of 1500t is 117,000 yuan / ton, which is 27% lower than the unit cost of 159,000 yuan / ton of the 500t production line.
Fifth, enterprise competition: carbon fiber filament is the core of competition
At present, the effective production capacity of the carbon fiber industry is highly concentrated, mainly from Jilin Carbon Valley (and downstream enterprises), Zhongfu Shenying, Guangwei Composite, Zhongjian Technology, etc., of which the corresponding share of Jilin Carbon Valley can account for about 50%. Benefiting from the prosperity of the new energy industry and the impact of the global epidemic on the import of overseas enterprises, the income of domestic carbon fiber enterprises has ushered in rapid growth, especially the Jilin Carbon Valley, which took the lead in breaking through the large-scale production of large-scale tows, the Zhongfu Shenying, which started in industrial applications, and Guangwei Composite, which attaches equal importance to the development of military industry.
The concentration of carbon fiber production capacity in the mainland is relatively high. In 2020, the theoretical production capacity of the domestic carbon fiber industry cr3 is 46%, CR5 is 60%, and CR10 is 72%, and the production capacity is concentrated in the head enterprises. However, this data does not represent the effective production capacity, and the production cost of some production lines in the industry is very high or cannot be continuously achieved, so the operating rate of industry capacity is not high.
Effective production capacity is highly concentrated, and the industry competition pattern is better. In 2020, the domestic carbon fiber production capacity is about 36,000 tons, but the domestic supply is about 18,500 tons, if the raw silk sales of Jilin Carbon Valley are converted into carbon fiber sales (assuming a conversion coefficient of 2.1:1), the sales volume of the top four domestic enterprises (Jilin Carbon Valley, Zhongfu Shenying, Guangwei Composite, and Zhongjian Technology) is about 16,000 tons, and CR4 is about 86%. Considering that Hengshen shares still have some self-produced raw silk, the industry raw silk is basically occupied by the above enterprises. At the same time, the head enterprises also have their own advantages in market segmentation, such as the main military products of Zhongjian Technology, the main military products of Zhongjian Technology, the military and civilian of Guangwei Composite, the main small silk of Zhongfu Shenying, the main of Jilin Carbon Valley, and the industry competition pattern is better.
The scale and profitability of the leader have increased rapidly
The rapid growth of domestic demand for new energy has made the income of leading domestic enterprises significantly faster than overseas. From 2017 to 2020, the domestic demand for carbon fiber will increase from 23,000 tons to 49,000 tons, with a compound growth rate of about 28%, and its demand pull is mainly wind power blades and carbon-carbon composites, and the compound growth rate of wind power blades and carbon-carbon composites in 2017-2020 will be 87% and 49% respectively. Benefiting from the prosperity of domestic wind power and photovoltaics, and the impact of the global epidemic on the import of overseas enterprises, the income of domestic carbon fiber enterprises has ushered in rapid growth, especially the Jilin Carbon Valley, which has taken the lead in breaking through the large-scale production of large-scale tows.
The revenue growth of leading enterprises confirms the changes in industry demand. Taking Zhongfu Shenying and Jilin Carbon Valley as an example, zhongfu Shenying's sales compound growth rate in the past three years is about 17% (production capacity is its core bottleneck), of which the compound growth rate of sales in wind power blades, carbon carbon composites, pressure vessels, and aerospace fields is 180%, 142%, 57%, and 47%, respectively, and the company has appropriately adjusted the product structure and basically grasped the mainstream boom direction; the compound sales growth rate of Jilin Carbon Valley in the past three years is about 65% (the production capacity basically matches the demand), of which the compound growth rate of 24K/25K product sales is about 86% The large tow carbon fiber volume stems from the strong demand for wind power.
Gross profit margin: The gross profit margin of enterprises bound to military products continued to be high, and the marginal improvement of the gross profit margin of Jilin Carbon Valley and Zhongfu Shenying was significant. Guangwei Composite and Zhongjian Technology are bound to military enterprises, so the gross profit margin has remained at a high level in the past few years. The sales of the first major customer of Zhongjian Technology accounted for a high proportion, while the proportion of Guangwei Composite Military Revenue continued to decline, from 65% in 2014 to about 50% at present. The gross profit margin of Jilin Carbon Valley and Zhongfu Shenying has improved significantly, which is judged to be due to the optimization of the cost of demand improvement, among which the gross profit margin of products in various demand areas of Zhongfu Shenying has steadily increased, indicating that the company's production efficiency has increased significantly.
1. Jilin Carbon Valley
Jilin Carbon Valley was established in 2008, the main products are carbon fiber precursors, which can be divided into 1K, 3K, 6K, 12K/S, 24K, 25K and 48K. Before 2017, the company's products were mainly small tows, and in 2018, the large-scale production of 24K and 25K products was realized, and the large-scale production of 48K products was realized in 2019. Since 2018 ushered in a new stage of development, relying on 24/25K products to achieve rapid sales growth in the wind power field, the overall operation has changed significantly, the gross profit margin has increased from -4% in 2018 to 35%, and the net profit margin attributable to it has increased from -37% in 2018 to 13%.
Large tow raw silk has become the company's core business. The company divides 24K/25K/48K products into large tows, and the sales volume of large tow raw silk accounts for about 57%, 79% and 75% of the total raw silk sales in the past three years. Among them, the revenue of 25K in 2019-2020 is about 200 million yuan and 370 million yuan, accounting for 67% and 64% of the revenue of carbon fiber precursor. The company's downstream is mainly in the field of wind power, wind power blades mainly use 24K and above carbon fiber, large tow carbon fiber (≥24K) cost-effective advantages make it a general trend in the field of wind power blades, especially the use of large tow carbon fiber pultrusion beam plate process to reduce costs.
The production capacity has been accelerated, laying the leading position of carbon fiber raw yarn. In 2020, the company's carbon fiber precursor production capacity is 24,500 tons, the company plans to build a new carbon fiber precursor production capacity of 40,000 tons (5,000 tons per strip, a total of 8), as of the end of 2020 has been put into production capacity of 20,000 tons, and the production capacity under construction is 20,000 tons. The Group plans to form a whole industrial chain of 200,000 tons of carbon fiber at the end of the "14th Five-Year Plan", including 150,000 tons of carbon fiber raw silk in Jilin Carbon Valley, 15,000 tons of large tow carbon fiber in Jilin Guoxing, 600 tons of carbon fiber in Kemerk, 35,000 tons of large tow carbon fiber of Jilin Chemical Fiber Group, 10,000 tons of carbon fiber and composite materials of Jilin Guoxing Composites, and other 5 key planning projects, at which time the production capacity of Jilin Carbon Valley raw silk is expected to reach 200,000 tons.
Some enterprises purchase raw silk from Jilin Carbon Valley to produce carbon fiber. From the perspective of the top five customers in Jilin Carbon Valley, jinggong series revenue accounts for about 50%, including Jilin Jinggong carbon fiber Co., Ltd., Zhejiang Baojing Carbon Material Co., Ltd. (formerly Zhejiang Jinggong Carbon Fiber Co., Ltd.), Zhejiang Jingye Emerging Materials Co., Ltd., Shaoxing Baojing Composite Materials Co., Ltd.; Hongfa series revenue accounts for about 15%, of which Hongfa New Materials is mainly engaged in glass fiber and carbon fiber multi-axial reinforcement materials, and the downstream is wind power blade enterprises. It is worth noting that Jilin Jinggong Carbon Fiber, as the largest customer of Jilin Carbon Valley, its equipment is mainly purchased from Zhejiang Jinggong Technology Co., Ltd.
2. Zhongfu Condor
Founded in 2006, Zhongfu Shenying is a joint venture between China Composite Materials Group Co., Ltd., Lianyungang Eagle Textile Machinery Co., Ltd. and Jiangsu Aoshin Group Co., Ltd.
In 2008, the company built a 1,000-ton SYT35 (T300-class) carbon fiber production line and achieved continuous production. In 2009, the company launched the international advanced dry spray wet spinning carbon fiber technology research, and began to approach the international advanced level in the process. Only three years later, the company independently broke through the dry spray wet spinning thousand-ton SYT49 (T700 grade) carbon fiber industrialization technology. In 2015, the company broke through the 100-ton SYT55 (T800 level) carbon fiber industrialization technology. In 2017, it broke through the large-scale production and stable supply of dry spray wet spinning thousand tons of SYT55, and won the first prize of the National Science and Technology Progress Award in that year. Almost every 2-3 years to achieve the large-scale production of new products.
Winning by volume, capacity utilization rate is much higher than that of the industry. The company is mainly based on the sales of civilian carbon fiber, although the sales unit price is lower than that of Guangwei Composite, Zhongjian Technology, which is mainly based on military products, but according to the statistics of the China Chemical Fiber Industry Association, the company's carbon fiber production ranks second in China in 2020, with a market share of 7.4%, and the capacity utilization rate remains above 90% all year round, far exceeding the industry average, which makes the company the fastest industrial carbon fiber enterprise to achieve profitability.
The Xining base was put into operation, the production capacity bottleneck was alleviated, and the cost was reduced simultaneously. The company's production base in Lianyungang has an existing production capacity of 3500 tons / year, which is currently running at full capacity, and the Xining 10,000 tons carbon fiber project is expected to be completed in batches this year and put into operation, which will not only solve the company's production capacity bottleneck after commissioning, but also be expected to reduce manufacturing costs. According to the prospectus, the company's current spinning speed has reached 400m/min, and the single-line scale has reached 5,000 tons/year, but the spinning speed design capacity of the Xining 10,000-ton carbon fiber project has reached 550m/min, and as of now, the Xining base has been completed and put into operation with a production capacity of 6,000 tons/year.
Backed by CNBM, it has a good customer base. Zhongfu Shenying is backed by the China National Building Materials System, and the downstream customers are mainly wind power blades, carbon-carbon composites, sports and leisure, and most of them are industry leaders, such as The carbon-carbon thermal field industry leader Jimbo Shares, the largest blade manufacturer Sinoma Technology, etc., with a good customer base, with core customers and the first-mover advantage of the market. In addition, Zhongfu Shenying is also moving towards the material end to the application end, launching the aerospace high-performance carbon fiber and prototype silk test line project, and the carbon fiber aviation application research and development and manufacturing project has also landed in Shanghai, which will help the localization process of China's large aircraft.
(Reference report: Changjiang Securities Carbon Fiber: High Performance, High Barriers, Creating the Era of Black Gold)
Source of this article: Strictly speaking