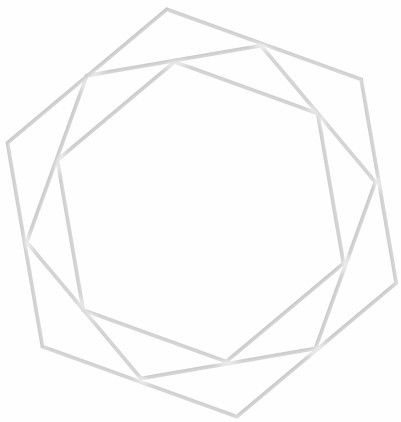
Follow the voice of the storm
Elevate your thinking
Guide
The development of electric vehicles is approaching a critical threshold.
This article is excerpted from Engineering, No. 8, 2021, journal of the Chinese Academy of Engineering
Written by Peter Weiss
来源:Better Battery Management Boosts Electric Vehicle Prospects[J]. Engineering,2021,7(8):1041-1043.
Editor's Note
At present, the development of the electric vehicle market is accelerating, and global automakers generally attach importance to the future development of the electric vehicle field. Most of the world's leading automakers, such as Volkswagen, GM, Honda, Daimler, Ford, Volvo and Dongfeng Nissan, announced that they will only produce electric vehicles in the future or significantly increase their production. On the basis of new breakthrough achievements in the development of electric vehicle batteries, other promising research results, such as the optimization of battery management systems, are expected to inject new vitality into the development of electric vehicles.
The 8th issue of Engineering, the journal of the Chinese Academy of Engineering, published "Optimizing the Battery Management System and Improving the Application Prospects of Electric Vehicles", which reported on a component that is more common in the safety and performance of electric vehicles, that is, the development and research status of the battery management system and the huge potential in promoting the application prospects of electric vehicles. Although the battery management system is not a component of the electric vehicle battery itself, this microprocessor module and its related circuitry monitor the voltage, current, and temperature of the battery, and adjust the level of these parameters through control signals to help maintain the best performance of the car, while ensuring that the battery is safe and adequate and operates within the parameters.
Global automakers are betting heavily on electric vehicles. With countries around the world explicitly demanding drastic cuts in gasoline-powered vehicles, most of the world's leading automakers, such as Volkswagen, GM, Honda, Daimler, Ford, Volvo and Dongfeng Nissan, have announced that they will only produce electric vehicles in the future or significantly increase production of electric vehicles. With the rapid growth of the number of charging infrastructure around the world and the standardization of charging infrastructure, as well as the advancement of technology, the introduction of preferential policies, and the decline in the price of electric vehicles, the development of electric vehicles is approaching a key threshold. After breaking through this threshold, its convenience (how convenient it is to charge anytime, anywhere), range (when the battery is fully charged), life (mainly related to the life of the battery pack), and performance will all be expected to exceed the equivalent indicators of affordable internal combustion engine-powered vehicles.
Although the new breakthroughs in the development of electric vehicle batteries have attracted most people's attention, other inconspicuous but promising research results are also expected to make a great contribution to the development of electric vehicles. In September 2020, General Motors, a Detroit-based U.S. automaker with the largest domestic market share, grabbed attention with an automotive component. This is a component that is more common in terms of the safety and performance of electric vehicles, and its name is called a battery management system (BMS). While the battery management system is not a component of the ev's battery itself, this microprocessor module and its associated circuitry monitor the battery's voltage, current, and temperature, and adjust the level of these parameters through control signals to help maintain optimal performance in the car while ensuring that the battery is safe and adequate and functioning within the parameters.
GM plans to spend $27 billion to transition to electric vehicles, replacing all of its light internal combustion engine-powered models with electric vehicles by 2035. As part of the implementation of the program, the automotive giant and its BMS partner, Analog Components Corporation (ADI), a large electronic components company in Wilmington, Massachusetts, have unveiled a new system for producing wireless BMS (wBMS) for cars that removes nearly 90 percent of the common wiring. GM said the enhanced BMS will increase the energy density of electric vehicle battery packs (an important factor affecting the driving range of electric vehicles), improve the design and production of electric vehicles, and reduce costs.
Meanwhile, other EV BMS innovators are working on "model-based" BMS (mbBMS), the most sophisticated of which can simulate the detailed physical and chemical state of a car's battery in near real time, but is still experimental. In terms of guiding the response to sensor signals, the BMS of an average electric vehicle refers to the internal empirical data sheets installed at the factory (and regularly upgraded), or simulates a battery with a simple model, such as a circuit containing several electronic components. However, high-end mbBMSs, through more complex but more rapid and precise simulations, can also continuously predict internal battery states that cannot be directly measured, such as charge levels within the electrodes or internal voltages that may be too high or too low. By directly sensing voltage and other battery signals and receiving model guidance provided in near real time, mbBMS can adjust battery operating conditions more precisely than standard BMS (wired or wireless), making rapid responses to real-time environments.
Lab tests conducted by developers on mbBMS show that this technology can greatly improve the drivability, range, battery life, and charging capacity of electric vehicles, while minimizing the prevention of premature aging or other damage to the car's power supply. If the next major breakthrough in batteries is still some time away, mbBMS alone has the potential to make many people opt for electric cars and abandon fossil fuel-powered cars.
Electric vehicle battery packs must be carefully monitored and managed, otherwise the lithium-ion technology devices inside them may be in danger of overheating or other failures. Fiona Meyer-Teruel, a GM engineer and head of wireless battery electronics, said: "Almost all electric vehicles have a management system of some kind. You need to know the state of your car's battery before you can drive safely. Many other rechargeable electronic devices, including cell phones and other portable electronic devices, also employ BMS to monitor and display battery charges. However, the price of electric vehicle high-voltage battery packs accounts for more than one-fifth of the purchase price of the car, which may have hundreds to thousands of electrochemical batteries. Venkat Subramanian, a professor of chemical engineering and mbBMS expert at the University of Texas at Austin, said: "The risk of cars is much higher than that of mobile phones. ”
A standard electric vehicle BMS is typically tightly connected to each part of the car's battery pack via a network of wires (Figure 1). By removing the wires, GM's new wBMS frees up space for up to another 15 percent more electrochemical battery packs. Increasing the number of batteries in a highly surplus space increases the energy density of the car's power supply, thereby increasing the car's range. Meyer-Teruel said switching to wBMS is also a way to directly help GM's upcoming new electric vehicles gain a place in competition with internal combustion engine-powered vehicles. After the mileage increases, consumers will not worry about whether electric vehicles can drive to their destinations, which has been an important factor hindering the sales of electric vehicles.
Figure 1 In February 2020, multiple battery modules were wrapped around tightly encapsulated electrochemical batteries under the neat surface of the high-voltage electric vehicle battery pack cover in the GM Battery Electrical Laboratory. These modules can communicate wirelessly with each other and with a battery monitoring system for microprocessors developed jointly by General Motors and electronic component manufacturer ADI. Source: Jeffrey Sauger/GM (public domain)
Meyer-Teruel said GM announced plans to launch 30 new electric vehicles in the next 5 years, of which the application of wBMS has brought some advantages to its design and production, although this advantage is not obvious. GM's rapid mass production of a range of previously unproducted sedans, light trucks and sport utility vehicles (SUVs) challenges are enormous. To that end, GM plans to build the aforementioned models using various drive modes of its so-called "Ultium Drive." The "Ultium Drive" consists of 5 electric drive units (from the front wheel, all wheel to special type) and includes an electric vehicle engine, a single-speed transmission and power electronics. The drive unit can contain two of the three powerful motors, and some cars will be equipped with more than one drive unit. The manufacturer will select a different number and configuration of drive components for each new model on the assembly line, install them on the prefabricated four-wheel battery "Ultium Platform" (i.e. chassis), and then encapsulate the components in a body adapted to the model.
But different types of battery packs also vary greatly in size, shape, and number of electrochemical cells. To power GM's upcoming electric vehicles, GM has worked with South Korea's LG Chem Co. Ltd. to develop a new type of lithium-ion electrochemical battery, Ultium, which contains a new chemical composition. A $2.3 billion plant for mass production of batteries is being built near the town of Lodz, Ohio, and in April 2021, the U.S. government announced plans to build a second plant in Tennessee with the same funding. While the way the same batteries in an electric vehicle battery are stacked is modular, Ultium batteries can be stacked horizontally or vertically, diversifying the form and configuration of battery pack modules. Thanks to the new wBMS, as well as the use of wireless transmitter and receiver communication between different modules and management via encrypted signals, the hard wiring of these modules is greatly reduced, thus simplifying the design and assembly of the battery pack. As a result of these improvements, Meyer-Teruel said: "WBMS will speed up the speed at which we can build and redesign battery packs, shortening the time it takes us to launch new cars." For example, it took GM engineers just two years to develop an unusually complex battery pack containing nearly 600 batteries for the 2022 Hummer All Electric Sport Utility Truck (SUT) of up to 746 kW (1000 hp), which is expected to be available later in 2021 (Figure 2).
Figure 2 The 2022 Hummer electric SUT will be the first electric vehicle to feature GM's new wireless BMS. The system controls a 200 kW·h battery pack with an output voltage of 400 V and can be charged by a charger with a power of up to 350 kW and an output voltage of 800 V. The battery pack consists of 24 battery modules, divided into two layers, and is the most powerful (maximum power of 746 kW) in the first-generation Ultium battery pack. GM also announced that it will launch the 2024 Hummer electric SUV in the fall of 2023, with a peak power (619 kW) about 20% smaller than the 2022 Hummer electric SUT. Source: GM (public domain)
MbBMS R&D engineer Subramanian and others have been working on how to quickly and accurately simulate the physical and chemical processes of lithium-ion batteries to provide better battery performance in real time for electric vehicles, renewable energy storage units, and other battery-powered devices. Subramanian co-founded BattGenie, a company based near Seattle, Washington, with his student Manan Pathak. Pathak is now the CEO of the company. Subramanian calls his engineering team the "reformers." They focused on simplifying mathematical representations based on physical/chemical models and translating these simplified versions into exceptionally fast computer algorithms and software. Subramanian said that the simulation scheme designed according to this can produce significant results in tens of milliseconds, fast enough to keep up with the speed of running and charging cars. For example, over the past few years, they have successfully applied a quasi-two-dimensional model known as a lithium-ion battery to mbBMS. Previously, the model was considered too complex to be applied in an effective mbBMS.
Subramanian said his mbBMS work in 2012 while teaching at Washington University in St. Louis, Missouri, received attention. The U.S. Department of Energy has allocated $5 million to him and his colleagues at the National Renewable Energy Laboratory (NREL) in Golden, Colorado, to demonstrate several improvements to the performance of lithium-ion electrochemical batteries by mbBMS control. This includes fast charging without shortening the battery life, which is annoying. Since then, they, as well as experimenters at universities and government laboratories around the world, have reported the results, using objective methods to demonstrate the wide potential of model-based methods to significantly improve the performance of electric vehicle batteries. For example, the University of Texas team and BattGenie have shown that model-based management can extend battery life by 100 to 150 percent (Figure 3) and reduce the number of charges by 50 percent.
Figure 3 Laboratory findings show that the average life of 16 A·h nickel-manganese cobalt bag lithium-ion electrochemical batteries increased by more than 100% (>) under mbBMS control (green line) compared with the standard charging mode (2CC-CV; red line). 1800 charge/discharge cycles). The experimenters said the discovery was "the first time experimentally demonstrated ... Model Predictive Control (MPC) based on real-time physics has a significant improvement in battery performance." Electric vehicles can no longer use batteries with less than 80% capacity. SOH: health; CC-CV: constant current and constant voltage; 5C: 16 A·h battery discharge rate, it takes more than 12 minutes to discharge 80 A. Source: Institute of Physics, with permission
Pathak said BattGenie has demonstrated mbBMS technology at the battery and modular levels for several electric vehicle manufacturers, and the company's next goal is to run full battery pack simulations and use its first mbBMS for mass production of electric vehicles by the end of 2022. Subramanian said that based on the early research of the NREL project, BattGenie also showed customers through a selection of electrochemical batteries that the mbBMS control can also reduce the battery footprint and weight by 20% without affecting the performance of the battery. "In general, model-based control is good for all aspects of the battery, not just to extend the life of the battery and speed up the battery charging speed," he said. ”
Note: The content of this article is slightly adjusted, if necessary, you can view the original text.
Adapted original text:
Peter Weiss.Better Battery Management Boosts Electric Vehicle Prospects[J]. Engineering,2021,7(8):1041-1043.