Recently, knowing that the car is almost without dead ends to dismantle the Tesla Model Y, we will use the way of graphics to explain the mystery of the interior of Tesla vehicles one by one.
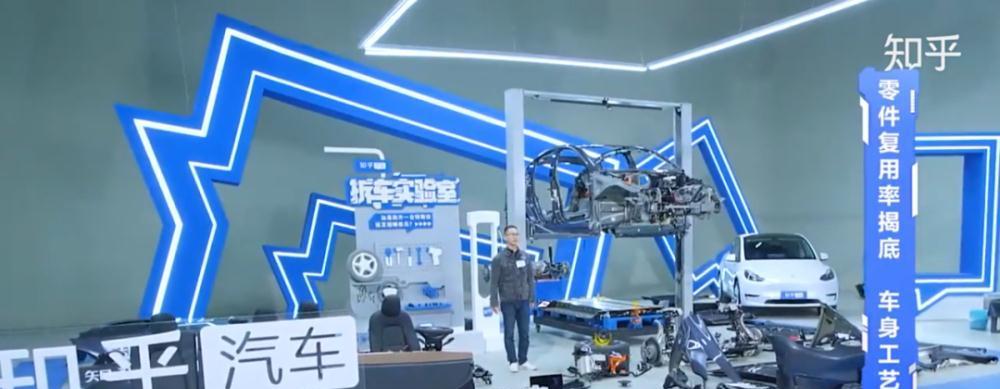
Those "mouth cannons" that Model Y didn't implement
Mouth cannon one: After the Model Y was unloaded eight pieces, testers found that the Model Y's body was not the overall die-cast body mentioned in the patent, but one-third of the floor structure behind the body was a huge cast aluminum part.
Mouth cannon two: Before the media analysis Model 3 and Model Y parts common rate of up to 70%, but in fact, not, from the number of parts to see the common rate of 25%.
Mouth cannon three: Before the model Y was listed, Musk had been advocating that the harness length of this car would reach less than 100 meters to advertise its high degree of integration, but after the actual dismantling, it was confirmed that the Model Y was far from reaching this level.
However, for reducing the length of the wiring harness, Tesla is not without solutions, but it has not been done for the time being.
Musk belongs to the early bragging.
Tesla has no hesitation in using "cast aluminum parts"
There is a saying that although only the back floor is a one-piece cast aluminum, tesla has been very ahead of the industry with such a large volume of individual cast aluminum parts. With this technology, parts can be reduced by 10-20%, greatly reducing the design cost and development cycle of fine parts.
Specifically, the rear floor structure of the general vehicle will be made of about 60 stamped steel plates spliced together, and the integrated die-casting process integrates a bunch of parts into one, and the original number of connection points is reduced from 700-800 to 50 now, and the manufacturing time is shortened from the original 1-2 hours to 3-5 minutes.
The reason why Tesla uses cast aluminum without hesitation is based on two concepts of its own vehicle development: 1. Constantly pursuing the integration efficiency of the whole vehicle; 2. Small steps and fast running, rapid iteration; there is gossip that Tesla is developing an integrated front cabin structure, followed by an integrated mid-cabin structure.
As we all know, the material cost of aluminum alloy parts is very expensive, but regarding the cost of maintenance, consumers do not have to worry for the time being. Taking a step back, everything is handed over to insurance, and the cost of maintenance is not a worry.
Brain-opening heat pump design and ingenious motor type
Although the Model Y has a front load compartment, the front compartment is still clean. Opening the front trunk shell, it is full of parts, the most eye-catching is the heat pump air conditioner, it can be directly shaken by hand, the advantage of suspension is to reduce vibration as much as possible, but for durability to hide hidden dangers.
Compared to competitor heat pumps, Tesla is different in a design called an eight-way valve. Through the eight-way valve, all the heat of the whole vehicle, including the power system, battery, cockpit, etc., can be collected, and the intelligent thermal management system will then manage these heats uniformly.
Model Y superimposes two four-way valves to form an eight-way valve, which integrates air conditioning and three electricity, and the valve can change the connection of nine pipelines to achieve twelve kinds of heating and three kinds of refrigeration. As a result, the front compartment radiators were reduced from two to one, relying entirely on complex control strategies to achieve a rational distribution of heat.
What's more, after Model Y canceled PTC heating and switched to heat pumps, it also added a compressor, which can also directly generate heat. The principle of the compressor is like opening the refrigerator door in winter to heat up, on the surface the refrigerator is refrigerating, in fact, the compressor will release the heat. The Model Y is equipped with a compressor power of 5-6 kilowatts, which is almost equivalent to mainstream PTC, so it can provide enough heating power.
Regarding the motor arrangement, the Model Y uses an AC induction motor on the front axle and a permanent magnet synchronous motor on the rear axle.
In addition to the industry's common practice of calling the front axle a mechanical clutch, Tesla's strategy is to use the rear motor as a rear-drive vehicle under medium and low loads; while at high load, the front motor participates in the work as a four-wheel drive vehicle.
Without the many hidden dangers of lidar, the "fool" may be Musk himself
As we all know, Tesla's autopilot is a set of vision-based, ultrasonic radar as a supplementary solution. Currently at the L2 level, Musk's goal is to achieve L5.
The camera gives the collected images to the neural network, and the computer will recognize these objects, but it is difficult to avoid the long-tail problem, and many uncommon objects cannot be accurately identified. For example, in last year's Tesla accident in Taiwan, because the computer did not recognize the "strange object" such as the white roof of the truck, it directly hit it.
In order not to hit similar objects again next time, Tesla's shadow mode will unit test the data that was not recognized at the time, and the failed data will be rebuilt and relabeled, and trained to become version 2.0 of the data until all the long-tail scenes are covered.
Until now, however, static object recognition at high speeds has been a major bug in assisted driving.
In addition to the well-known self-developed FSD chip, through disassembly, Tesla's millimeter-wave radar is also the fourth generation of mainland products, released 5 years ago, has been very old, and this generation of millimeter-wave has a congenital defect, it can only measure the distance and speed, but can not measure the height of the target.
The recognition of static objects has always been a headache for driver assistance, especially in tunnels and basements, the signal of millimeter-wave radar will be reflected many times, so the conventional practice of the depot is simply to filter out the static target, and the task of identifying static objects is completely handed over to the camera, if the camera does not give force, then the target is missed, and the probability of collision will occur.
The most effective way is to install a lidar, but for cost reasons, Musk can't listen to it at all, and even scolds the people who use lidar as fools.
Battery safety is systems engineering, and Tesla is great
Taking Model Y as an example, the battery cost basically accounts for 20% of the vehicle, which is a very expensive component.
Disassembly found that the upper and lower shells of Tesla battery packs used a lot of structural glue in order to reduce metal connections, and could only use violent disassembly, similarly, the integration of the battery module is also very high, once there is a problem inside, Tesla does not have maintenance from the inside to the outside. In other words, even if a battery cell is broken, the entire battery pack must be replaced.
It must be complained that the battery pack is bolted to the bottom of the car, in addition to loosening the bolts at the bottom of the car from the bottom up, it is also necessary to remove all the seats and loosen the bolts in the car from the top down, so that the battery pack can be removed smoothly, so once there is a problem, the working hours cost of replacing the battery will be very high.
In addition, the battery pack is located at the lowest point of the vehicle, with only 140mm of ground clearance, and there is no additional skid plate and spray protective material, which is very easy to support the bottom.
However, compared with the previous generation of batteries, the amount of potting glue between modules is significantly reduced, and the plastic plate of the module is eliminated. Domestic manufacturers in order to stabilize the module are using metal fasteners, and Model Y is actually plastic, and the original ten threaded holes on the side of the module have also been simplified with two, and even the two fixed points with the stringer have been cancelled, it can be said that the cost is not even spared. As for whether such a design will have an impact on later use, it will take time to prove.
Tesla's BMU circuit board responsible for battery management is designed to be very advanced, using high-voltage to low-voltage isolation DC/DC, which can power the high-voltage system and 12V electrical appliances respectively, compared with domestic products, saving a relay and pre-charging resistance to achieve the effect of cost reduction.
Of course, this battery pack also has a conscience, such as the minimum pipe diameter of the fast plug from two claws to three claws, improving the reliability of the interface; the connection between the two cooling plates inside the module has also been upgraded.
Here it must be stated that the thermal runaway of a single cell does not represent the thermal runaway performance of the whole package, which is a systematic work.
However, compared with the imported version, the cost of Tesla's domestic batteries has declined, and the structural safety, system safety, and bottom impact safety have indeed declined, and the entire performance performance needs to be tested by time.
There's also a "compromise" on safety on the back of the crazy cost reduction.
With annual sales of 137,000 units, Tesla topped China's new energy vehicle sales list in 2020. The price exchange through discounts is an important factor in Tesla's soaring sales, and the underpinning of crazy price reductions is Tesla's strong cost control ability.
From the Model 3 to the minimalist interior to integrate the lights, rearview mirrors, and entertainment systems into the central control touch screen, Tesla's material cost is 1000-2000 yuan less than competitors. Taking a 12.3-inch meter as an example, including a controller, the cost of the part is more than 1,000 yuan.
Although the cost of the central control is saved, it increases the user's interaction cost and sacrifices a certain degree of security.
Unlike the autopilot chip, Tesla's car machine chip is still purchased, but Tesla uses the Intel Atom A3950 chip with the x86 architecture that is not very popular on the market, and from the perspective of computing power, this chip is extremely cost-effective. The fatal drawback is that the ecology under the X86 architecture is stretched, but Tesla does not care, so that Tesla's car application has always been much less than that of domestic brands.
Because Intel's car chip is not popular, as a large customer of the receiver, Tesla can naturally get a very attractive supply price. Overall, the Model Y electrical architecture can save more than 10,000 yuan compared to competitor models of the same class, which is reflected in the terminal price of 20,000-30,000.
Cost-saving places also have ambience lights monochromatic non-adjustable, headlights without turning headlights, door speakers using the cheapest fabric wrapping, door storage slots using non-woven wrapping, etc., all of which are sorry for the price of 300,000.
Under the operation of reducing costs at an all-round way, according to Benchmark, the hardware cost of Model 3 is 170,000-220,000, and the hardware cost of Model Y is estimated to be about 190,000-250,000.
However, there is a saying that the cost ratio of Model Y's power system, intelligent network connection and electrical architecture is higher than that of traditional luxury brands, while the cost ratio of Model Y in the mechanical system part is very low.
Objectively speaking, this is a domestic chassis + advanced intelligent electric system car.
AutoLab overview
From the perspective of the dismantling of Tesla, Tesla is undoubtedly the most integrated electric vehicle at present, and the company is still making unremitting efforts for further integration. Integration thinking does not mean bottomless cost savings, in some ways, Tesla saves money in some ways is somewhat "unscrupulous", preferring to sacrifice the user experience to save money, or even disregard the safety of users. Especially the hardware problems of automatic driving, knowing that there are defects and using the mainland's old millimeter-wave radar, after many accidents, knowing that deep learning can not cover many long-tail scenarios, but insisting on not using the less expensive lidar.....
Source: AutoLab