On April 27, 2022, under the guidance of the Guangzhou "Chain Chief System" Office (Guangzhou Municipal Bureau of Industry and Information Technology), Tree Root Interconnection, as the "chain master" enterprise of the "software and xinchuang" industrial chain in Guangzhou, jointly held the "Automotive Manufacturing Digital Transformation and Upgrading" activity of the Series of Live Broadcasts of Tree Root Interconnection to Help the Digital Transformation of the Industrial Chain, and specially invited GUANGC Honda and FAW-Volkswagen digital experts to bring professional sharing of automotive manufacturing digitalization.
This activity has received great attention from practitioners in the automotive industry chain, receiving 7500+ likes, accumulating nearly 3,000 online views, and the attention has reached 170,000+. The digital practical experience of Tree Root Interconnection, together with Guangqi Honda and FAW-Volkswagen, has brought new inspiration to the digital exploration of the majority of car companies.
The full text totals 1883 words
It takes about 8 minutes to read
01.
Tree Root Interconnection:
Empower automotive intelligent manufacturing with "all-factor digitalization"
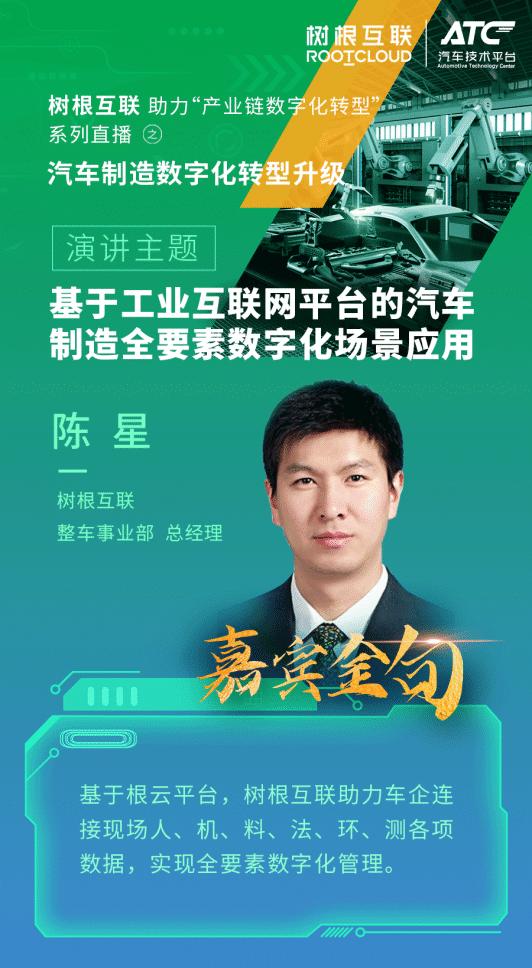
In the face of the intelligent manufacturing evolution of the automotive industry, Chen Xing, general manager of the Vehicle Division of Treeroot Interconnection, pointed out: "The process of intelligentization in the automotive industry can be shortened, but it cannot be omitted. From the transparent factory to the advanced of the intelligent factory, the car company should realize prediction and adaptation from the management of on-site people, machines, materials, laws and rings, to the transparent visualization of data in the manufacturing process, the lean management, and then to the manufacturing intelligence of business operations. ”
As an enterprise selected by the Ministry of Industry and Information Technology for three consecutive years in the "Cross-industry and Cross-field Industrial Internet Platform List", the root cloud platform that Tree Root Interconnection focuses on building can help car companies connect various data such as on-site people, machines, materials, laws and rings to achieve digital management of all elements. Chen Xing said: "The all-factor digital solution provided by Treeroot Interconnection is highly suitable for the field of automotive intelligent manufacturing, which can accurately solve management difficulties such as unclear equipment performance, energy consumption monitoring, processing process optimization, process quality testing, etc., and help car companies to optimize and improve production and management equipment in terms of efficiency, energy consumption, processing technology, tooling use, and processing quality." ”
Talking about how to help car companies build "lighthouse factories", Tree Root Interconnection believes that through the extensive connection of the root cloud platform, the digital collaboration of all elements of people, machines, materials, laws and environments can be realized to ensure safe production. Through the connection and analysis of the root cloud, we break the data islands, activate the value of data to help digital production, and achieve all-round improvement of operation efficiency, management efficiency and accurate decision-making. Finally, we will deeply integrate business, data and technology, and create a "digital twin" through the root cloud platform to achieve the improvement, cost reduction and efficiency improvement of the whole process.
02.
GUANGQI Honda:
IOT technology helps the digitalization of engine production lines
Wen Zhuozhan, a digital expert and chief of the casting section of Guangqi Honda, shared the digital transformation exploration of the engine production line. Regarding the core manufacturing links such as engine casting, machining and assembly, the chief of the liberal arts department shared the common management elements of car companies from the aspects of quality, efficiency and safety and environment. He said: "Guangqi Honda is currently in the stage of digitalization to intelligence, and its goal is to achieve comprehensive intelligent manufacturing. Through the extensive connection of the tree root interconnection root cloud platform, the interconnection and integration of various management elements are realized; combined with the MES system, the intelligent linkage of data and production is realized, and the tightening torque of each engine is intelligently managed."
He also shared the linkage between data and machining production, AI vision applications based on deep learning, innovation of big data in casting, intelligent equipment management systems, and applications of mobile Internet in aluminum supply. In terms of the application of IOT technology, he focused on sharing: "Relying on the root cloud platform to monitor the operation status of moving equipment in real time, and realize preventive maintenance according to data model operations." For example, through IOT for high-frequency vibration and load monitoring, to achieve equipment status visualization and real-time intelligent calculation, to prevent the outflow of defective products, it is expected to reduce 5 times of defects; in terms of tool management, from the number of times of use to the degree of wear and tear of the tool replacement, the tool life is increased by 5%, and the turnover rate is increased by 0.4%. ”
03.
FAW-Volkswagen:
Comprehensive transparency + partial intelligence, build a comprehensive smart factory
Zhang Rui, head of digitalization of FAW-Volkswagen Tianjin Branch, shared: "In the welding workshop of FAW-Volkswagen, 1178 kuka robots work in an orderly manner, and the automation rate has reached the industry-leading level. In addition to robots, we also attach great importance to the full independent digital application of employees, in 2021 to launch the full digital strategy, T-π Innovation Association from the initial small team of 7 people to 18 people, and now to achieve 100% coverage of the department, the formation of 6 agile teams, with 91 members. ”
Through the independent digitization of all employees, FAW-Volkswagen mobilizes every employee to participate in digital construction, the core is to base on the scene, focus on pain points, through model training + projects, learn in practice, and grow in actual combat. According to statistics, 95 digitization projects have been completed, the number of codes written has exceeded 500,000 lines, cost savings and development costs have been 23 million yuan / year, and man-hours have been saved by more than 90,000 / year.
With the digitalization of all employees blossoming everywhere, FAW-Volkswagen is more aware of the importance of digital top-level design. In 2022, FAW-Volkswagen will take comprehensive transparency and partial intelligence as its development goal, build a comprehensive smart factory, and carry out overall planning in every field such as quality, equipment, supply chain, cost, and energy. Taking the energy field as an example, we will work together with Treeroot Interconnection to build an energy management platform to achieve transparency in energy management, and promote the construction of an early warning mechanism for energy use through AI prediction + data mining.
In terms of intelligent construction, he also shared the tightening big data analysis, stamping parts surface recognition, paint surface quality identification, to tighten big data analysis as an example, by tightening the data acquisition system, tightening the monitoring dashboard and mobile terminal APP, to create a replicable intelligent tightening quality management master, through machine learning instead of manual analysis, improve efficiency, the current accuracy rate of up to 99.3%, full data analysis to solve accidental problems.
In the future, Shugen Interconnection will continue to deepen the field of automobile manufacturing, and join hands with more car companies to realize the interconnection, analysis and application of human, machine and production big data through industrial Internet technology and services, helping them to reduce costs, increase efficiency and improve quality in production and operation, and contribute to the digital transformation and upgrading of car companies.