Recently, some car companies have turned their heads to do mobile phones, and some companies that do mobile phones have run to make cars again, looking like they are "not doing business". But from the perspective of technological development and integration, mobile phones and cars – especially electric vehicles – are actually somewhat similar.
More than a decade ago, the mobile phone battery still needed to be removed and charged separately, and now it has been integrated into the interior of the mobile phone, and some parts for packaging and protection can be eliminated without disassembly. Although the power battery of the car does not need to be removed to charge, with the improvement of the degree of integration, it is constantly discarding excess components. At the same time, like mobile phone batteries, it will continue to be optimized with the upgrading of OTAs.
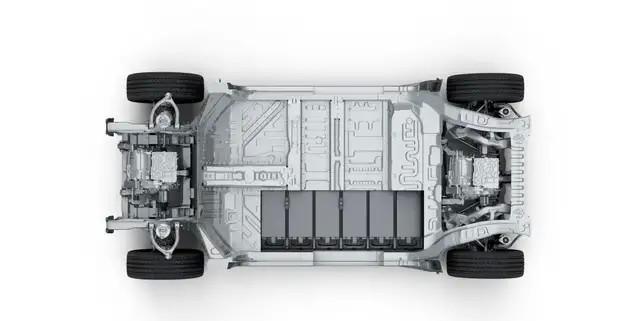
The "slimming history" of power batteries
The design of the power battery can be roughly divided into three major stages, namely the 1.0 era of standardized modules, the CTP 2.0 era of large modules, and the CTC 3.0 stage, which represents the highest level in the industry.
In the 1.0 era, power batteries are called standardized modules, and the structure is very cumbersome, from the inside to the outside are cells, modules and battery packs. Many cells are packaged into a module, and many modules are packaged into battery packs, which are finally installed on the car. But only the battery cell is used to supply power, this "over-packaging" not only needs to design and produce additional parts, but also occupies additional space, which leads to a reduction in the proportion of space in the battery cell.
The Standardization Module | Figureworm creative
The 2.0 era is known as the "big module" era, the main idea is to design larger modules, reduce the number of modules or even no modules, to reduce the number of parts and space occupation at this level as much as possible, the most representative is the CTP technology of the Ningde era and BYD's blade battery.
NINGD times: CTP technology and BYD: blade battery | CITIC Securities[2]
The 3.0 era marks the beginning of the introduction of integrated battery and chassis design solutions. CTC is the abbreviation of "cell-to-chassis", which means "the design of the fusion of battery and chassis". At the same time, there must be a smarter BMS (Battery Management System) to monitor, manage and optimize the use of batteries more intelligently.
The CTC scheme is compared to the traditional scheme
What is the difficulty of CTC technology?
It's easy to say, but there are many technical problems to really implement CTC. The purpose of integrating the battery and chassis is to reduce the number of parts, compress the space volume, and improve the power and endurance of the vehicle through this integrated design. But in the end how to integrate, how to ensure the waterproof performance of the battery, how to ensure the safety of the battery after reducing the layers of packaging, how to adjust the production line, how to test, mass production, maintenance, these are all issues that need to be considered.
In 2016, Zhu Jiangming, chairman of Zero-Run Auto, was inspired by the integrated design of smartphone batteries and took the lead in proposing the idea of integrating power batteries and chassis internally. After 6 years of continuous research and development, testing, and improvement, the mass production of CTC technology has finally been realized, and it will be installed in the simultaneous mass production of their new flagship model, zero-run C01.
In terms of CTC technology and hardware innovation, the most basic and the most critical is "how to make the chassis and battery integrated", and the answer given by zero run is "integrated pallet structure". The design idea is to install the battery into a battery tray, and then install this tray under the chassis, like an inverted dinner plate. In order to improve the firmness of the battery, the top and bottom of the battery are also fixed to the tray and chassis. The entire integrated design is both a body structure and a battery structure.
Just like most of the current mobile phones can achieve waterproof battery and circuit structure, electric vehicles also need to be well waterproof in rainy days and wading conditions. In the 1.0 2.0 battery structure, after layers of packaging, the waterproof performance of the power battery is actually not difficult to do, but in the CTC era of 3.0, the module and battery structure have been streamlined, how to rely on the chassis and tray structure to achieve waterproof, is a very difficult problem.
Large areas of metal plates are combined by welding, and considering the waterproof performance, the traditional welding and inspection methods are no longer applicable. In order to solve this problem, Zero Run adopts a special process to improve the welding quality, accuracy control and welding consistency, and also proposes a new airtightness detection method and a return-to-factory maintenance program. At the junction of the chassis and the tray, a combination of "rivets + sealing strips" is used to ensure waterproof performance.
Rivets and sealing strips for chassis and tray connections
In addition to waterproofing, bumps and bumps during driving are inevitable, and the battery should be able to remain "firm" under these external forces, and the structure of the integrated tray can also achieve this very well. For example, the tray is not a flat board, with horizontal and vertical beams as a skeleton, which can well enhance the strength of the chassis and tray. On the side of the body, it is also equipped with an energy-absorbing structure, and it really carries: when a violent lateral collision occurs, the impact force will be preferentially transmitted to the energy-absorbing plate, and the energy-absorbing plate will deform to absorb the impact force, minimize the impact on the support structure and the battery, and ensure the safety of the battery.
A skeleton structure composed of transverse and longitudinal beams
Increasingly "smart" batteries
With hardware innovation and breakthroughs, of course, there must be comparable software innovation as a support, zero run will combine BMS and cloud platform into AI BMS big data intelligent battery management system. It is like a smart housekeeper that can continuously learn and progress, guarding the battery all the time, and can perform software updates throughout the life cycle through OTA, making the battery safer, longer and more efficient.
For example, AI BMS can monitor the various indicators of the battery in real time, and send the data to the cloud for AI data modeling, get the current state of the battery, and feedback to the owner through the APP. With this data and status, the AI BMS can perform deep learning based on historical failures that have already occurred, and provide early warning before the next failure. It also automatically corrects incorrect battery usage patterns and provides smarter charging strategies to keep batteries working at their best.
If the integrated tray structure allows the battery to have a reliable and powerful "reinforced iron bone", then ai BMS gives the battery "mind" and makes the battery more and more "smart". The comprehensive evolution of the body and mind has made the zero-run CTC chassis an energy matrix for the new generation of models, which can not only adapt to highly integrated and modular production, but also have a very strong functional expansion in the future.
What is it like to sit on a battery and drive a car?
Zero-run CTC technology brings not only the improvement of the battery system, it has different degrees of improvement in the performance of the whole vehicle. In the upcoming zero-run C01 model, CTC technology has brought about improvements in safety, performance, driving experience and cost.
Battery safety is certainly the most basic and most important indicator of electric vehicles, before leaving the factory, the battery of electric vehicles must go through various tests such as "knife mountain and fire", zero run more than the national standard 8 more than the strict standard of detection, proving that through the complementary strength of the battery and body structure, coupled with the full-time protection of AI BMS, battery safety has been greatly improved.
Thanks to the structural design of the CTC chassis, coupled with the economic management of energy consumption by the AI BMS, the endurance of more than 700 kilometers can be achieved under comprehensive working conditions. At the same time, CTC technology has increased the torsional stiffness of the body by 25%, reduced the weight of the vehicle by 15kg, and further enhanced the handling performance.
The high degree of integration of the CTC eliminates the installation gap between the battery and the body, increases the vertical space of the body by 10mm, and adds a 5-meter-long horizontal body to make the interior space very sufficient, and the driving experience is excellent.
Finally, thanks to the structural simplification brought by CTC, the number of parts of the C01 vehicle is reduced by 20% compared with the traditional solution, and the cost of structural parts is reduced by 15%, which is more convenient for large-scale mass production.
Under these performance improvements, the zero-run C01 has become a medium and large sedan with large space, long endurance, handling and safety.
The most valuable thing is that zero running not only put forward the concept of CTC technology, but also through 6 years of efforts, research and overturning, so that this concept becomes a reality, and through zero running C01 to prove the improvement of CTC technology to the performance of the vehicle, so that power battery technology has officially entered a new era of 3.0. I believe that in the future, electric vehicles will definitely remove the heavy shackles again, complete another slimming, we no longer need to have the anxiety of electricity, and can be more free to "zero run" all the way.
bibliography
[1] An integrated structure of electric vehicle body and battery pack CN202121278218.5
Song Shaoling: Investment strategy of new energy vehicle power battery industry: global electric wave, high-quality supply chain benefits. CITIC Securities