3D printing technology is not suitable for mass production, after all, the cost is there. However, for the special needs of small batches, it has an irreplaceable advantage.
For the R&D department of the depot, 3D printing technology can convert the CAD design model into a solid part without the need to go through the mold step, saving time and cost.
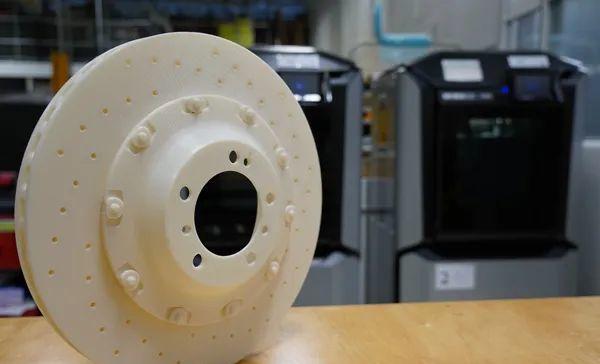
For ultra-luxury brands like Bentley, 3D printing equipment will be able to meet the production of small batches of parts and the individual needs of customers.
Bentley recently invested £3 million to double 3D printing capacity at the Crewe uk facility. In 2021 alone, the number of components manufactured by high-tech equipment reached 15,000.
These parts come in a variety of types, from the traditional tools needed to make parts for Bentley Blower's continuations, to auxiliary tools on the production line, such as lightweight polishing blocks commonly used in woodworking workshops. Even protective masks for the epidemic.
The favorite of the R&D department of 3D printing technology can transform caddy design models into solid parts when designing and manufacturing prototypes, such as engine models and aerodynamic wind tunnel models according to the scale of the original car.
Bentley also makes accessories for models that broke records at the Peak Pikes Challenge.
In addition, ultra-luxury brands like Bentley will create a lot of personalized customized models for customers. In the past, this was a very time-consuming and costly job, but with the increase in Bentley's 3D printing capacity, more auto parts were manufactured and more personalization possibilities were opened up for customer vehicles.
3D printing equipment installed at Bentley's headquarters plant can save up to 50% on parts costs. Operating around the clock, the plant can produce parts of more than 25 material types.
Jaguar Land Rover, also a British brand, used a Labrador dog named Yogi when developing a new Land Rover Defender model.
Yogi's task was to jump up and down the suitcase of the Defender model, and the test team recorded its relevant data through synchronous use of pressure map technology as a reference for real-world use scenarios, including the pressure applied by dog paws and foot pads.
Land Rover used 3D printing technology to introduce Yogi's "dog paw" model to help with the development. In the end, after up to 5,000 cycle wear tests, the paint setting of the rear bumper of the guard was set, and the durability of about ten years could be achieved after considering the use of pets on and off the car.
For Porsche in Germany, 3D manufacturing processes have long been used in many fields. Including 3D printed full barrel seats for the 911 and 718 series models, parts of the seat's central area (i.e., the seat cushion and backrest surface) are produced using 3D printers.
In 2020, Porsche even partnered with Mahle to develop a new application for 3D printing – the production of high-performance engine pistons for the GT2 RS, the flagship model of the Porsche 911, the highest performance Porsche production model available.
Pistons manufactured by 3D printing technology weigh 10% less than traditional mass-produced forged pistons. Reducing the weight of the most critical drive components directly improves the engine's high-rotational power performance.
In addition, the 3D printed piston is actually better than the traditional piston performance. The reason is that the 911 GT2 RS, as a high-performance model, places extremely high demands on the heat resistance of the piston, and 3D printing can integrate a closed cooling pipe in the piston head, which is not possible with traditional processes.
The new, lighter piston increases engine speed, reduces temperature loads on the piston and optimizes combustion, which increases the output of the 911 GT2 RS 700Ps twin-turbo engine by up to 30 Ps while increasing efficiency.
3D printing technology is like a tool of artistic creation, which is based on digital model files, and constructs objects by printing them layer by layering adhesive materials such as powdered metals or plastics. With the advantages of streamlining the process and saving production costs, it creates unlimited possibilities.