3D列印技術不适合大批量的生産,畢竟成本擺在那裡。但對于小批量的特殊需求,卻有着不可替代的優勢。
對于車廠研發部門來說,3D列印技術可将CAD設計模型轉化為實體部件,不需要經過模具這一步,節省時間又省成本。
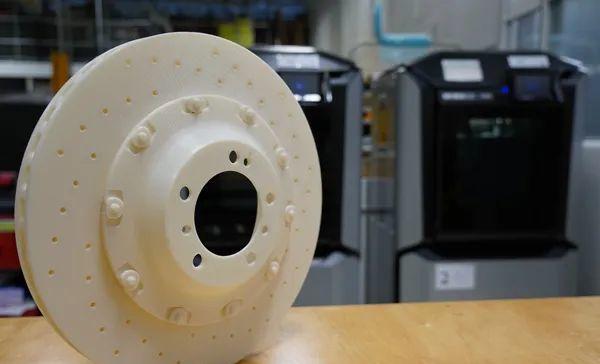
對于賓利這樣的超豪華品牌來說,3D列印裝置将可以滿足小批量的部件生産及客戶的個性化需求。
最近賓利投資300萬英鎊,将英國克魯工廠内的3D列印産能提升一倍。僅2021年,由高科技裝置制造的部件數量達到15000個。
這些零部件類型多樣,包括制作賓利Blower延續版車型配件所需的傳統工具,生産線上的輔助類工具,例如木工工廠中的房間内常用的輕質抛光磨塊。甚至是應對疫情的防護面罩等。
3D列印技術研發部門的至愛,在設計制造原型車時,就可以将CAD設計模型轉化為實體部件,例如根據原車比例制作引擎模型與空氣動力學風洞模型。
賓利還為曾在派克斯峰挑戰賽中打破紀錄的車型制作配件。
另外像賓利這樣的超豪華品牌,都會為客戶制造非常多的個性化定制車型。以往這是非常費時和成本的工作,而随着賓利3D列印産能的提升,制造更多汽車零部件,為客戶車輛拓展更多的個性化可能性。
賓利總部工廠内安裝的3D列印裝置能夠節省50%的零件成本。經過晝夜運作,該裝置可生産超25種材料類型的部件。
同為英國品牌的捷豹路虎,在研發新路虎衛士車型時候,動用到一隻名叫Yogi的拉布拉多犬。
Yogi的任務是在衛士車型的行李箱上跳上跳下,測試團隊通過同步利用壓力地圖技術記錄下其相關資料,作為真實使用場景的參考,包括狗爪和腳墊所施加的壓力情況等。
路虎利用3D列印技術推出Yogi的“狗爪”模型幫助研發。最終經過高達5000次的循環磨損測試,定下了衛士後保險杆的漆面設定,在考慮到寵物上下車使用場景後,可實作十年左右的耐久性。
對于德國的保時捷來說,早已經在多個領域采用3D制造技術。包括為911和718系列車型提供3D列印的全桶型座椅,座椅的部分中央區域(即座墊和靠背表面)使用3D列印機生産。
2020年保時捷甚至與馬勒(Mahle)合作,共同開發一項3D列印的全新應用——生産保時捷911旗艦車型GT2 RS的高性能引擎活塞,911 GT2 RS是目前最高性能保時捷量産車型。
通過3D列印技術制造的活塞重量,比傳統量産鍛造活塞輕10%。在最關鍵的驅動零部件實作輕量化,等于是直接提升了引擎的高轉動力表現。
另外3D列印的活塞竟然比傳統活塞性能更好。原因是911 GT2 RS作為高性能車型,對活塞的耐熱性提出的極高的要求,而3D列印可以在活塞頭内內建了一條封閉式冷卻管道,這是傳統工藝所無法實作的。
更輕的新型活塞能夠提高引擎的轉速,降低活塞上的溫度負載并優化燃燒,這使得911 GT2 RS 700Ps雙渦輪增壓引擎的輸出功率再提高多達30 Ps,同時提高效率。
3D列印技術就像一件藝術創造的工具,它以數字模型檔案為基礎,将粉末狀金屬或塑膠等可粘合材料,通過逐層列印的方式來建構物體。具備工藝精簡、節約生産成本等優勢,創造無限可能。