At the Texas factory Show, Elon Musk mentioned that one of the most important places was the problem of production bases.
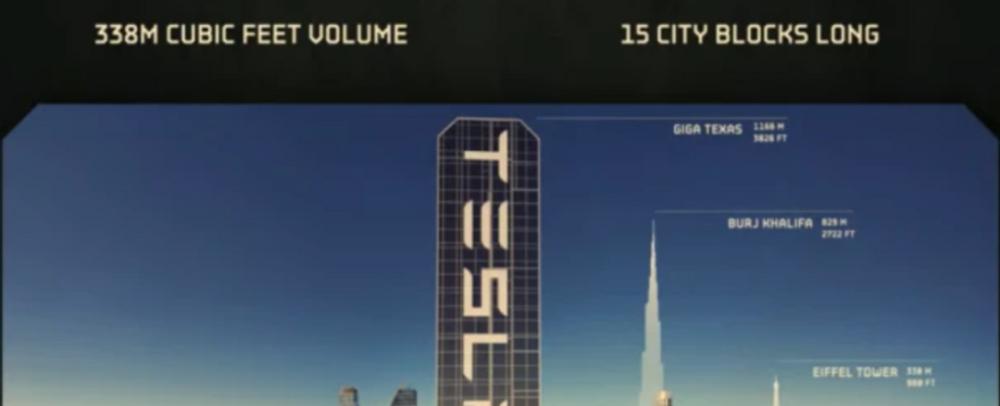
Figure 1. Tesla's factory
From the perspective of the development path of the entire Tesla, the core is to make it easier and faster to build a car, whether it is integrated manufacturing, the cable becomes shorter, the essence or at the beginning of the design is mainly to consider the systematic reform of the process. In terms of the entire manufacturing efficiency, the vehicle supply chain can be shortened, the time and time of the whole vehicle will be reduced, and the labor used will be reduced, and then several manufacturing bases will quickly support a huge number of vehicles.
Figure 2. The route of the day's visit and the open area
According to today's Weibo upload of AFS for Tesla's Roadmap, the core of Tesla's volume is still so many cars, up to expand from pickup trucks to Van, the whole is back and forth S, X Model 3 and ModelY, that is, the model platform will have a new version of the Model E version of the expansion.
Remarks: How fast Tesla will expand its product line, overall very restrained.
Figure 3. AFS forecasts Tesla's product planning and U.S. manufacturing site distribution
Part 1 Integrated casting
In March 2021, the one-piece die-cast backplane was introduced, which minimized more than 70 parts and rebuilt the traditional stamping welding process. That is to say, after the successful launch, the automotive industry has recognized that this investment in the design has strong advantages in terms of cost economy, process flow and production cycle, material utilization and so on. Domestic new forces enterprises, including Weilai, Xiaopeng, ideal are studying, and foreign Volvo, Mercedes-Benz related global enterprises, are also thinking about whether the previous factory can meet the rhythm of the next generation of electric vehicle manufacturing efficiency, so Volvo, as a representative of traditional car companies, was the first to promote the transformation of integrated die-casting plants and chassis integration structural parts.
Key benefits include:
(1) Cost economy improvement: the quality of steel in-white body is about 300-400kg, aluminum materials instead of steel materials can reduce weight by 30-40%, from the perspective of material price and recycling, aluminum die-cast body can be only achieved in a long period of time and steel body parity level, taking into account the lightweight and cost factors. What's more, the manufacturing cost of parts will also be improved
Figure 4. The cost and rhythm of manufacturing
(2) Vehicle production beat optimization and process flow simplification: the vehicle manufacturing process and working hours will be better optimized through integrated molding, taking Tesla's Model Y as an example, the video before playing, the switching of the rear base plate process will be reduced from 1-2 hours of man-hours to 3-5 minutes, with the expansion of the front and battery tray, the entire vehicle manufacturing set up a die-casting machine to set up a separate station, only need the transit warehouse can meet the single equipment 24h 24h non-stop, but also support Texas factory single line 500,000 units a year
Figure 5. The transfer of the intermediate structural assembly is also simple
(3) Product complexity reduction: This is seen through the previous video, the design and manufacture of Model Y is expected to achieve integration from design and manufacturing, not only to reduce the solder joint, the complexity of the entire product assembly has been simplified, and the supply chain link has been directly shortened
Figure 6. This complexity continues to decrease, and the structure is becoming more and more simplified
(4) Sustainable development, improved material utilization: die-casting smelting materials and recycled aluminum, my understanding is that Tesla's business model becomes recyclable, the whole car runs out, the car is handed over to it, the battery is handed over to it, and through processing, you can make another one out, this way of thinking has opened up an interesting road for the automotive industry
Figure 7. The car body and battery material will be recycled in the future, and the entire life cycle will be sustainable
In the electric pickup truck using giga press die casting equipment with a clamping force of 8000T, this emerging vehicle black technology is more, but also need to accelerate the production cycle and simplify the production complexity, the entire car body assembly for integrated die casting, including the rear floor assembly, the front cabin total Chengdu process replacement, greatly improving production and manufacturing efficiency. This is a change in physical skeleton for the development of electric vehicles, which I think is very interesting.
Part 2 High and low voltage wiring harnesses
There is also this hanging cable, the Model Y's 100 meters is more like a stem, but from the overall design, the current high and low voltage wiring harnesses are simplified. With the integration of high-voltage systems (PTC is gradually marginalized), DCDC and OBC are integrated. For the entire high-voltage system, the necessary connections are:
● DC charging input interface (1 pair), external is a charging gun
● Battery pack fast charging interface (1 pair), for charging
● Battery pack discharge interface (1 pair), for rear drive
● Electric compressor input interface, this is doubtful, may be integrated with the drive system in the next 3-5 years
● DCDC, the input interface is doubtful, and now it is partially gone
OBC, which has been taken away on ET7
● Drive system: Enter a pair, if the four-wheel drive system pulls the line will grow longer, in the Model S Plaid inside the copper row design way.
So calculate, in the future high-voltage rear-drive system, the entire high-voltage connection is mainly around the battery pack of 2 pairs essential, the others are simplified in the integration.
Figure 8. Tesla's high-voltage wiring harness
Tesla's low-voltage controller and the overall load is also constantly simplifying, at present, it is difficult to optimize the complexity of various lights and motors, and the integrated control line is more likely to merge the functions, I think the ultimate is the power supply and signal control optimization, partial wireless, in fact, a variety of paths are developing on the road of intelligence.
Figure 9. Tesla's wiring harness design
Summary: I think the threshold of the new forces is 500,000 units, just like battery companies have to climb to the threshold point of 20GWh and 50GWh, automobile manufacturing and battery cell manufacturing are trying to simplify and return to rationality. In addition to software, how to find the right explosive point in the reconstruction of automobile manufacturing is also what I have to continue to think about.