在德州工廠Show的時候,Elon Musk提及很重要的一個地方,就是生産基地的問題。
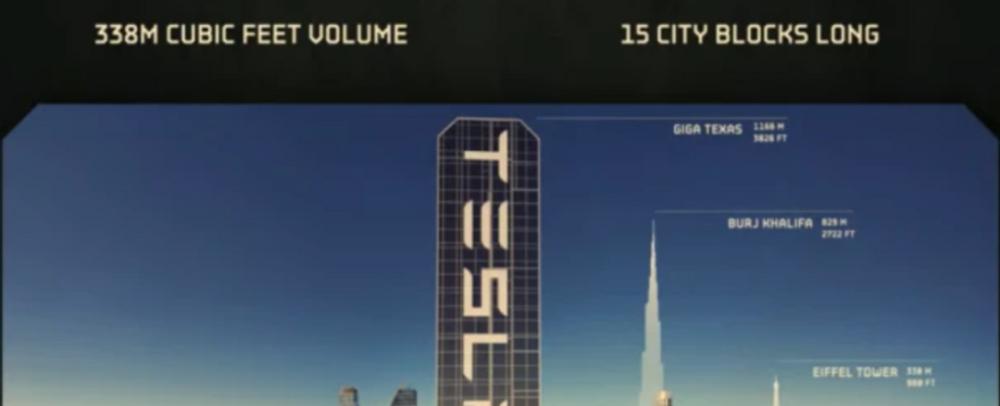
▲圖1. 特斯拉的工廠
從整個特斯拉的發展路徑來看,核心是更容易和快速去制造一台車,不管是一體化制造、線纜變短,本質還是在設計之初主要是考慮在工藝上進行系統性改革。能夠在整個制造效率上,讓整車供應鍊變短,整車的用時和時間變少,用的人工變少,然後讓幾個制造基地快速撐起來巨量的車。
▲圖2. 當天的參觀路線和開放的區域
根據今天微網誌上傳的AFS對于特斯拉的Roadmap來看,特斯拉的量的核心還是這麼幾台車,最多從皮卡擴充到Van,整個就是來來回回的S、X Model 3和ModelY,就是車型平台會有Model E這種新版本的擴充。
備注:特斯拉擴充産品線到底會多快,總體來看很克制。
▲圖3. AFS 預測的特斯拉産品規劃和美國制造基地分布
Part 1 一體化鑄造
在2021 年 3 月推出一體壓鑄後底闆,把70 多個零部件減少最少,是對于傳統沖壓焊接工藝進行重構。也就是說,在成功推出之後,汽車行業都認識到這種投入巨大的設計,在成本經濟性、工藝流程和生産節拍、材料使用率等方面具備較強優勢。國内新勢力企業,包括蔚來、小鵬、 理想都在研究,而國外沃爾沃、奔馳相關全球性企業,也在思考之前的工廠是否能符合下一代電動汽車制造效率的節奏,是以沃爾沃作為傳統車企的代表,第一個推進一體壓鑄廠房改造和底盤一體化結構件。
主要的優點包括:
(1)成本經濟性提升:鋼制白車身的品質在 300-400kg 左右,鋁材料代替鋼材料可以減輕重量 30-40%,從材料價格和循環使用的角度,鋁壓鑄車身可以在長周期唯獨做到和鋼制車身平價的水準,兼顧輕量化和成本因素。更重要的是,零件的制造費用也将得到改善
▲圖4. 制造的成本和節奏
(2) 整車生産節拍優化和工藝流程簡化:整車制造流程和工時将通過一體成型得到較好的優化,以特斯拉的Model Y 為例,之前放的視訊,後底闆工藝的切換将從 1-2 小時的工時減少到 3-5分鐘,随着擴充到前部和電池托盤,整個整車制造設定壓鑄機設定單獨工位,隻需要中轉倉庫就可以滿足單台裝置全天 24h無休,也支援德州工廠單線50萬台年
▲圖5. 中間結構總成的中轉也簡單了
(3)産品複雜性降低:這個通過之前的視訊看出來了,Model Y 的設計和制造,有希望從設計和制造實作一體化,不光是把焊點減少,整個産品總成的複雜度得到簡化,把供應鍊環節直接縮短了
▲圖6. 這個複雜度在持續降低,結構上越來越簡化
(4)可持續發展,材料使用率提高:壓鑄熔煉材料和回收鋁,我的了解是特斯拉的生意模式變成可回收的,整個車用完了,車交給它,電池交給它,通過處理給你再做一台出來,這種思考方式為汽車行業走出了一條有意思的路
▲圖7. 車子本體和電池材料将來都能回收,整個生命周期都是永續的
在電動皮卡采用鎖模力達到 8000T 的 Giga Press壓鑄裝置,這個新興的車輛黑科技比較多,也需要加速生産節拍和簡化生産複雜度,将整個下車體總成進行一體壓鑄,包括後底闆總成、前艙總成都進行工藝替換,大幅度提升生産制造效率。這個對于電動汽車的發展,是實體骨骼上的變化,我覺得很有意思。
Part 2 高低壓線束
還有就是這個吊起來的線纜,Model Y的100米更像是一個梗,但是從整體的設計來看,目前高低壓線束都在簡化。随着高壓系統內建化(PTC逐漸被邊緣化),DCDC和OBC內建化。整個高壓系統,必要的連接配接是:
● 直流充電輸入接口(1對),外部是充電槍
● 電池包快充接口(1對),充電用
● 電池包放電接口(1對),後驅動用
● 電動壓縮機輸入接口,這個存疑,可能将來3-5年和驅動系統內建在一起
● DCDC,輸入接口存疑,現在已經部分沒有了
● OBC,在ET7上已經被拿走了
● 驅動系統:輸入一對,如果是四驅系統拉的線會長一些,在Model S Plaid裡面走銅排設計的方式。
是以算算,以後高壓後驅系統的話,整個高壓連接配接主要是圍繞電池包的2對必不可少,其他都在內建化裡面被簡化。
▲圖8. 特斯拉的高壓線束
特斯拉的低壓控制器和整體的負載也在不斷的簡化中,目前來看各種燈、電機複雜很難被優化,內建化的控制線路更可能把功能合并,我覺得終極就是電源供給和信号控制優化,部分無線化,在智能化的路上其實多種路徑都在發展。
▲圖9. 特斯拉的線束設計
小結:我覺得新勢力的門檻是50萬台,就像電池企業要爬到20GWh、50GWh這樣的門檻點,汽車制造和電芯制造都在努力做簡化,回歸合理性。除開軟體,汽車制造裡面的重構怎麼去找合适的爆點,也是我要去持續思考的。