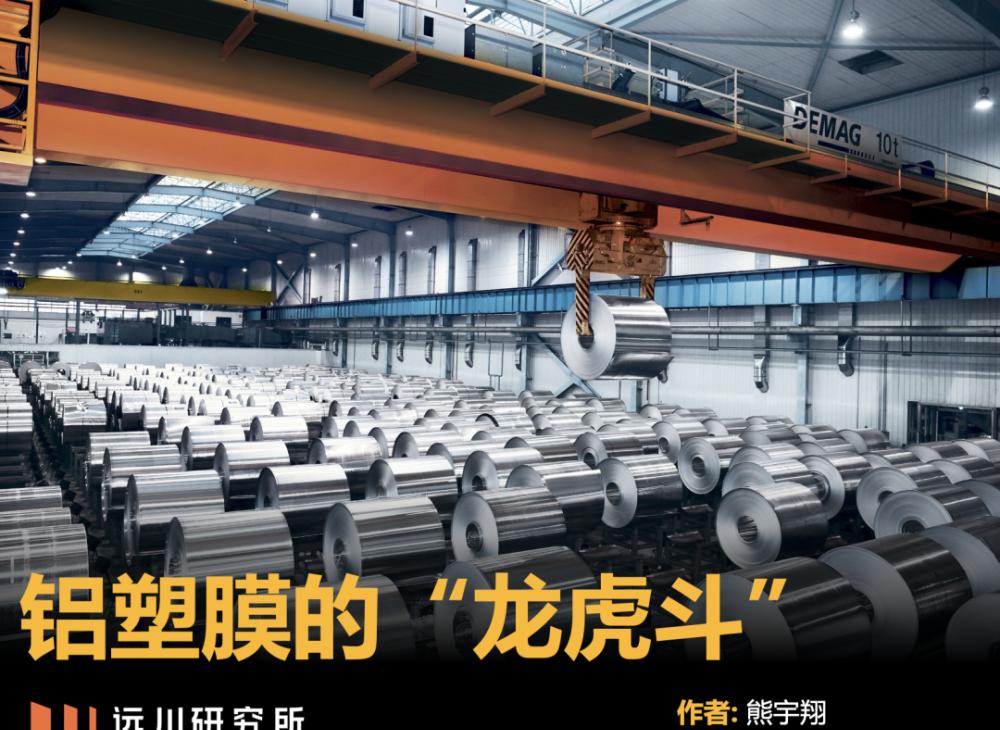
The history of changes in the global lithium battery industry in the past two decades is a history of China's lithium battery counterattack. Chinese companies have captured almost every key position held by Japanese and South Korean companies, but there is one that they cannot attack for a long time: aluminum-plastic film.
Although it sounds strange, in fact, the aluminum-plastic film is very close to us. At the moment you're holding your phone, a layer of less than 0.1 millimeter-thick aluminum-plastic film is wrapped around the battery under the phone's case. And this layer of silver film that you can't see and touch is one of the most technically difficult structural parts in the battery, and the unit price is ten times that of the battery separator, and the price per square meter is 13-35 yuan.
On this high-value track, China started late, only rolled off the production line in 2004, and has been catching up since then, but the progress is not satisfactory. By 2020, Japan and South Korea still occupy 73% of the market, of which the two giants of Japan DNP (Great Japan Printing) and Showa Denko are in an absolute dominant position.
The sudden outbreak of the epidemic has changed the industry pattern of aluminum-plastic film. On the one hand, the outbreak of the global new energy vehicle market has promoted the soaring demand for power batteries, while the expansion of Japanese and Korean companies is relatively conservative. In such a situation, domestic enterprises see the opportunity to make up for the position.
Focusing on the aluminum-plastic film with the lowest localization rate, this article mainly focuses on three issues:
1. Why is the localization rate of aluminum-plastic film so low?
2. Why did domestic aluminum-plastic film companies not occupy the market after achieving technological breakthroughs?
3. Where is the opportunity for the outbreak of domestic aluminum-plastic film?
Barriers: Materials and processes
According to the appearance, lithium batteries have three classifications: cylindrical, square shell, soft package, each battery needs a shell package, aluminum-plastic film is a layer of "soft shell" set on the outside of the soft pack battery.
As the first line of defense to protect the battery cell, the aluminum-plastic film must be both thin and light, but also must ensure extremely high barrier and insulation, can not react with the active substance, can not be easily punctured by external forces, in addition, on the basis of ensuring good cold stamping formability, but also need to take into account the strength and toughness.
All in all, the aluminum-plastic film must meet the complex and even contradictory performance indicators at the same time, and the technical threshold is very high.
If the battery aluminum plastic film is black, then congratulations, you are a high-end mobile phone user
In order to meet these needs at the same time, the aluminum-plastic film must be made of several layers of film with a thickness of only a few tens of microns (external resistance layer, anti-permeable layer, heat sealing layer), and the layers are bonded with glue or hot melt resin.
The technical difficulty of aluminum-plastic film is that whether it is the production of upstream raw materials or the process of fitting them, there is a large number of know-how, and a slight difference will affect the strength and life of the product.
Image source: Tianfeng Securities
Compared with the aluminum-plastic film that is difficult in material technology, the steel/aluminum shell used to encapsulate square/cylindrical batteries is much lower in technical difficulty: steel and aluminum are bulk commodities, easy to obtain and relatively cheap; the processing is simple, stamping, stretching, welding technology are very mature, and domestic enterprises have long mastered. The whole set of material systems and process systems of aluminum-plastic film comes from Japan.
In 1998, Showa Electric and Sony jointly developed aluminum-plastic film, which was later carried forward by DNP. Because of the simultaneous mastery of raw materials and processes, Showa Electric and DNP became the duopoly of this industry, occupying more than half of the global market share for a long time, and after that, Japan's letterpress printing and South Korea's Kurimura Chemical ranked third and fourth in the industry.
China's catch-up in the field of aluminum-plastic film began in 2004.
In that year, "Zijiang Enterprise" set up a separate aluminum-plastic film research and development team. As a well-established packaging materials company in China, Zijiang made its fortune by supplying plastic bottles to Coca-Cola and PepsiCo, and has accumulated many years in the field of aluminum-plastic composite film materials for packaging. It was originally thought that "the structure of aluminum-plastic film is similar to that of flexible packaging composite films", but with the research findings, it is impossible to overcome the technology of aluminum-plastic film along the original road [3].
In July, the first batch of aluminum-plastic film samples for trial production in Zijiang rolled off the production line, and a number of domestic battery factories came to the scene, but found that compared with imported products, there was a big gap in depth, corrosion resistance, appearance and performance [2].
In technology-intensive manufacturing, new companies can easily fall into the dead cycle of chickens or eggs because of the technology gap - the product is immature, and large customers dare not be the first guinea pig. Without large-scale use by customers, technological improvements are difficult. Fortunately, Zijiang's main business is stable and continuous blood transfusion, starting from cooperation with some small manufacturers, and the product has been developed and iterated many times to preserve a flame of domestic aluminum-plastic film.
In 2012, Zijiang established a subsidiary specializing in the production of aluminum-plastic films, "Zijiang New Materials". In 2014, Zijiang aluminum plastic film business landed for the 10th year, and the third generation of products entered the supply chain of ATL, the world's largest polymer lithium battery company.
He Aizhong, deputy general manager of Zijiang New Materials, mentioned that the cooperation with ATL has benefited Zijiang a lot in quality management, ATL has put forward many strict rectification requirements in the audit of Zijiang, and Zijiang spent a lot of money to start TPM lean production in 2014, in order to promote the quality stability of aluminum-plastic film [3].
However, ATL is only a "working boy", without the permission of downstream major customers (such as Apple), can not change suppliers without authorization, therefore, ATL to Zijiang to purchase a very limited number of square meters, at the beginning of only tens of thousands of square meters per month.
Although the shipment volume is not much, Zijiang has achieved a breakthrough of zero in the siege of Japanese and Korean enterprises, giving domestic counterparts a lot of confidence.
Since then, a number of domestic enterprises such as Dongguan Excellence, Selen Technology, TD Optics, Mingguan New Material, Huazheng New Material and so on under Putailai have poured into the aluminum-plastic film industry. However, they have fallen into the embarrassing situation of "having strength and nowhere to go".
Detour: The Vanishing Lead Big Brother
Do purification business from the New Lun, cross-border aluminum-plastic film when there is a gambling ingredient.
In 2016, Selen Technology (which has been renamed "Selen New Material"), which was eager to turn around the loss, took the lead and spent 550 million yuan to acquire the aluminum-plastic film business of the Japanese letterpress printing company, including factories, raw materials and patent authorization, becoming the world's third and domestic first aluminum-plastic film enterprise.
At that time, China was setting off a new round of subsidies for new energy vehicles, but the problem of short endurance and weak safety of electric vehicles was still prominent, and compared with squares and cylinders, the advantages of soft pack batteries were precisely in energy density, safety and cycle life, directly hitting the pain points of the market. Selen chose stud to directly enter the soft pack power battery market with unlimited potential.
After the acquisition, the market seems to be moving in the direction expected by Selen. From 2016 to 2018, the installed capacity of domestic soft pack power batteries increased from 3.3GW to 7.6GW, accounting for 13.2%, and the demand for aluminum-plastic film increased from 0.9 billion square meters to 160 million square meters.
In the same period, Selen aluminum plastic film was successfully put into production in Changzhou, and received orders from jiewei, fu neng and other soft package manufacturers. Since then, it has turned a profit, and its revenue has soared from 1.32 billion yuan to 3.15 billion yuan, becoming a model student in the eyes of its peers.
However, this model student was proved by the CSRC to be a fraudster: from 2016 to 2018, Selen Technology took the aluminum-plastic film business as the main body for three consecutive years, inflating revenue by 730 million yuan and inflating profits by 180 million yuan. Beautify a non-profitable business into a new business that can make the company change its life against the sky.
As an upstream enterprise, although Selen mastered a good technology at that time, the biggest pain was that it could not find the leading big brother in the downstream: on the one hand, LG Chemical, the global soft package boss at that time, was blocked from the Door of China's new energy vehicle market because of the whitelist policy, on the other hand, domestic battery factories chose square shells instead of soft packages that required aluminum-plastic film on the packaging technology route.
Compared with soft bags, the cost of square shell shell is low, the supply of raw materials is sufficient, the energy of the cell unit is large, and the shape is regular and suitable for vehicle use. Because of these advantages, the two major speakers of China's power battery, Ningde Times and BYD, invariably chose square shell, and with their market dominant position, the domestic market share of square shell power batteries was pushed up to more than 80%.
CTP (Cell to Pack) technology and blade batteries successively launched by NINGDE Times and BYD have given the soft pack power battery a fatal blow in China - they not only improve the safety of the battery, but also go further in the cost and system energy density indicators, and the soft pack not only weakens the original advantages, but also the cost disadvantage is more prominent.
Soft pack power batteries not only failed to become mainstream, but the market share was squeezed to only 5.5% in 2020, which made the upstream domestic aluminum-plastic film difficult.
Taking Selen as an example, the company's revenue in 2019 was 3.32 billion yuan, but the net profit was only 9.88 million, and last year it considered selling half of the equity of the aluminum-plastic film subsidiary. Zijiang enterprises, which started the earliest, the shipment volume and revenue growth during this period are also far from the scene of domestic power batteries drying up and fast.
In contrast, the Days of Kodali, which supplied the C-shell battery housing for the Ningde era and BYD, were much better. In 2019, the company's net profit reached 237 million yuan, an increase of 188% year-on-year.
In the final analysis, for domestic aluminum-plastic film companies, in addition to catching up with technology, they must rely on the breakthrough of downstream products in order to win the battle of turning around.
Dawn: Opportunities to trade between them
Since the second half of last year, the European new energy vehicle market has been in short supply due to subsidies, and the supply of soft pack batteries used by the mainstream of European car companies has exceeded demand, at the same time, the production of aluminum-plastic film companies in Japan and South Korea has been affected by the epidemic, and it is a priority to supply LG Chem and SKI, flawlessly scrupulous about China, and imported products were once out of stock.
In the long run, in the next two years, the global demand for aluminum-plastic film will grow from 240 million square meters to 400 million square meters. However, the two giants of DNP and Showa Electric are not willing to expand production, and the current annual production capacity is only 200 million square meters. Companies including Selen, Zijiang, Enjie, Huazheng New Materials and other companies are taking the opportunity to expand production.
Compared with the expansion of production, the more important benefit is the smooth flow of the road to downstream customers.
Selen finally obtained an order from LG Chemical after 3 years of production of the domestic aluminum-plastic film production line, and the second phase of the project was also put into operation in July this year, and Zijiang's cooperation objects in addition to Fu Neng, Guoxuan Hi-Tech, And Yiwei Lithium Energy also cooperated with BYD to successfully break into the blade battery supply chain.
Since its launch last year, BYD has made great strides in the market with blade batteries, but its blade batteries were in a state of insufficient supply in the early days, and the key problem was that the blade batteries were too long, such as the battery used in the "Han EV" was up to 1.28m long, and the production efficiency and yield rate were affected.
At the beginning of this year, when BYD launched the DM-i hybrid model, it used a "small blade" battery different from that of pure electric vehicles - replacing a single long battery cell in the aluminum shell with a number of short batteries with aluminum-plastic film soft packs to reduce the difficulty of production. As the DM-i model becomes a blockbuster series with monthly sales of more than 30,000 units, the demand for millions of square meters of aluminum-plastic film will be released. Zijiang's stock price has soared 130% in one year.
The reason why Zijiang can get BYD's orders is that it is a domestic enterprise, the degree of localization of upstream raw materials is relatively high, the supply of products is relatively guaranteed, and under the premise that the product performance parameters and the gap between Japan and South Korea are not large, the price is more than 20% lower than that of foreign counterparts.
At the event in November this year, BYD said that it will start next year, and on the "big blade" used in pure electric models, it will also use aluminum-plastic film soft-packed battery core + external aluminum shell packaging scheme to improve yield. Tianfeng Securities predicts that by 2023, the demand for aluminum-plastic film from BYD will reach 62.34 million square meters, equivalent to 4.2 times of Zijiang's shipments in 2020.
In the short term, BYD and LG will promote the domestic soft pack power battery volume, and Selen and Zijiang will continue to maintain the situation of "double power" in China for a period of time.
Epilogue
In essence, the counterattack of China's lithium battery industry is a common wealth movement of "downstream driving upstream, first rich driving later".
The first to get rich is the Ningde era, BYD and other downstream factories, and behind them are hundreds of upstream raw materials and equipment suppliers, many companies have not only completely realized domestic substitution, but also have gone abroad, followed by battery factories to overseas layout. For example, the pilot intelligence, relying on selling lithium battery equipment to "Ning Wang", sold a market value of 100 billion.
In contrast, domestic aluminum-plastic film is still in a state of catching up due to the lack of downstream orders and technology accumulation, but with the production of soft pack batteries by BYD, Ningde times, Guoxuan Hi-Tech and other leading enterprises, the trend of domestic substitution is becoming clearer under the blessing of home battles.
Resources:
[1] Overview of China's Aluminum-Plastic Film Industry in 2019, Head Leopard Research Institute
[2] Ten years of memory| Zijiang New Materials: growing together with the aluminum-plastic film market, gaogong lithium battery
[3] Zijiang New Materials: R&D First Focus on the localization of aluminum-plastic film High-tech lithium battery
[4] Lithium-ion Electronics Industry Development White Paper (2021 Edition), CCID Think Tank
[5] Soft pack battery discharge Aluminum-plastic film industry ushered in the inflection point, Shanghai Securities
[6] In-depth research on the electrical equipment industry: review overseas, aluminum-plastic film domestic substitution to see equipment, material localization and Know-how accumulation, Tianfeng Securities
Article from: Far River Business Review