Text—ANN STEFFORA MUTSCHLER
Source of the article — Semiconductor Engineering
When dealing with different types of massive amounts of data, multi-type chip fusion has more advantages than single chips. But for automotive applications, it's unclear how or even whether these chips should be packaged together.
The biggest problem facing in-vehicle electronics is the extreme temperature difference between the inside and outside of the vehicle. If not cooled adequately, the chip will experience premature aging, signal drift, and in some cases, the chip will even stop working properly. Still, cooling systems will make car manufacturing more complex, costly, and even other failures. This is clearly a huge challenge for automakers and chip designers.
"Every module is closed in every way, so these modules have thermodynamic limitations," said Willard Tu, senior director of Xilinx's Automotive Business Unit. "They always try to cram these modules into weird little places. Some modules are susceptible to ambient heat buildup. ”
For example, the front-view camera on the windshield is in an extremely harsh environment because the sun is shining directly on the windshield. "This means that the module itself will naturally heat up, not just from the electronics, but also from the environment." Tu said. "Regardless of the temperature of the electronic device, the fluctuation of temperature always makes automotive electronic design full of challenges."
Proximity to the engine makes chip package design more difficult. "The engine heats up and makes up the power circuit system," says Marc Swinnen, product marketing director at Ansys. "At the same time, there are a lot of electronics in cars that are not so close to the engine, such as infotainment systems. In addition, autonomous driving electronics do not need to be tightly connected to the engine, so specific thermal constraints only apply to some electrons. Other electronics can be installed in a common electronic enclosure, under a seat or in an instrument cluster. ”
While these decisions may not even catch the attention of most consumer electronics design teams, extending the life of cars and trucks and the amount of data processed in vehicles requires some complex design and cooling techniques. The problem is that under such extreme conditions, advanced chip design experience is still shallow, and these designs have not yet been applied in advanced process nodes or advanced packages.
Consider chips that contain high signal processing, such as 4D imaging radar or lidar.
"Fever is always a problem in this regard," Tu said. "In general, the industry usually follows Moore's Law, reducing the transistor gate length to solve this problem. In this case, the dynamic power consumption is always low when the device is running. When the device stops running, the static power consumption is actually a bit high, but the device is usually in the 'on' state most of the time, not the 'off' state. Our concern is that the battery may be affected when 'turning off' the device app. This is an area of interest, so most automakers are increasing the size of their batteries. ”
Moore's Law has historically provided added value for reducing heat and improving performance, but this feature is gradually reaching its limits as process nodes are updated and iterated. "Not every vendor is moving the lithography node down from 28nm down to 16nm, then to 7nm, to 5nm to 3nm, and so on," Tu said. "The challenge is now gradually shifting to cost-oriented, which means that many companies struggle to afford the high cost of 5nm or 3nm nodes, and they are avoiding moving to 5nm or 3nm nodes." So they're looking to solve the heat dissipation problem in other ways and are starting to look at the system level rather than downsizing. ”
This takes advantage of the FPGA, which can perform more calculations per clock cycle than traditional ASICs. "One of the biggest contributors when looking at heat dissipation is the clock frequency of the SoC," Tu says. "If the device is operating at 1 or 2GHz, then this is the primary generator of thermal computing power consumption. But in FPGAs, this is not a pipeline passing through, and the spawn can be configured as five or six pipes. Therefore, five to six instructions are executed per clock cycle. Instead of having one CPU or multiple CPUs running on a single clock frequency, the device has 10 or 20 pipelines dedicated to processing signals. ”
In some parts of the car, the advantages of advanced packaging are highlighted. However, some methods are more effective in some parts of the vehicle than others, and this is only now being studied.
Strategies for solving heat dissipation problems
For all chipmakers targeting the automotive market, as well as companies developing advanced packaging technologies, the thermal challenge clearly comes first.
"The basic challenge is always the same for every part that uses a chip." Melika Roshandell, director of product marketing for cadence's multiphysics systems analysis, said. "In the automotive sector, challenges follow. Because starting up at higher ambient temperatures means the challenges will be even more daunting. But any strategy being used in other industries can be applied to the automotive sector. Cars also have the advantage of more space, so other heat dissipation improvements can be used in the design compared to mobile phones. This means that the fan is an option. radiator? This is also an option. ”
Doing this work as planned requires recording the heat of different electrical components. In the past, records were done by performing steady-state analysis of the PCB, but this did not provide enough detail to evaluate.
"For this reason, electrothermal co-simulation has become very important in automobiles due to reliability requirements," Roshandell said. "You don't want to throw away your car in two years. You want to extend its lifespan. This type of co-simulation shows how temperature can transiently affect heating and voltage drops, for example, over a certain period of time. ”
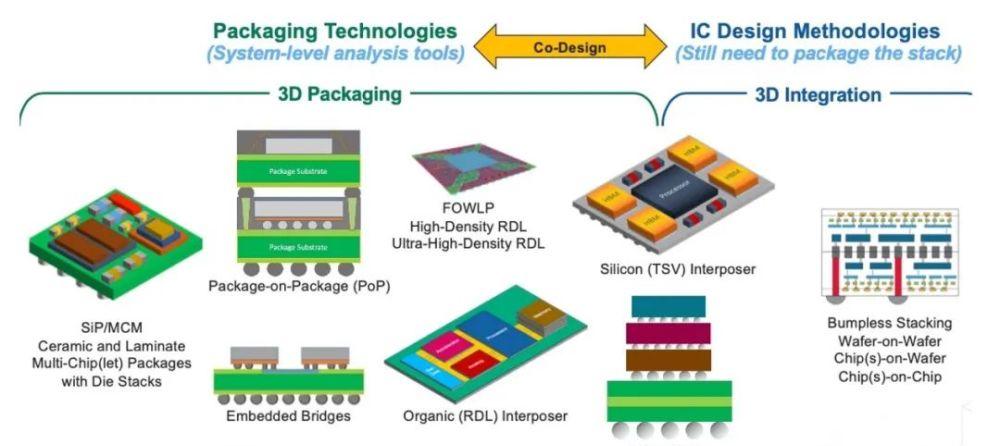
Figure 1: Different Types of Advanced Packages (Source: Cadence)
Despite the automotive industry's lack of experience in advanced electronics, the process is well understood. "The automotive industry has a lot of strict regulation, which forces companies to do a lot of analysis and a lot of records." Said John Ferguson, director of product management for digital industrial software at Siemens. "They have characterized the temperature conditions well and the reasons for their induction within the system. Once you know this, you're at least one step closer to asking how to design a bunch of chips that might produce this. ”
Heat and storage
One of the key problems with advanced electronics is the effect of heat on memory. Even DRAM, which is considered very reliable, can become less reliable in extremely hot environments. This is particularly cumbersome in automotive applications, where the vast amount of safety-related data generated by all on-board sensors needs to be processed and stored somewhere and needs to be accessed quickly. In addition, you need to keep your data intact and undamaged.
High-bandwidth memory (HBM) is a possible solution, basically stacking drAM chips inside the module. "Since HBM2, users have been thinking about using HBM for cars." Brett Murdock, product marketing manager for Synopsys Memory Interface IP, said. "The real challenge is in terms of memory, as the heat in the car environment makes it challenging. The temperature around the device quickly becomes high after the car is started, and the memory emits an unpleasant odor due to heat. Interestingly, for HBM3, the standard task force has shown great interest in calculating the automotive temperature range of HBM3 devices. If suppliers can solve their automotive problems in this regard, that will open up a high-demand market for HBM equipment. ”
To do this, they must be able to withstand automotive-grade temperature fluctuations. "Today, HBM is primarily used in graphics processors, equipped with a large number of heat sinks and/or water cooling," Murdock said. "That's the first problem to be solved. HBM was originally supposed to be a 3D technology that was planned to be installed directly above the CPU, but could not be achieved due to temperature reasons. Due to the severity of the heat generation, the device uses an intermediate layer up to 2.5D. To dissipate heat, a huge heatsink needs to be placed on top of the entire package, which means that chip stacking is difficult. Then putting it in an automotive environment will still be a problem. Vendors are trying to solve this problem because they see the needs and opportunities there. ”
From a reliability perspective, using mediation layers increases potential risk. "The mechanical connection of the intermediary layer in the automotive environment needs to be handled when making the circuit board, but I don't think anyone has actually completed the process of thinking about or certifying the appearance of the intermediary layer," he says. "But this is not a big problem, and if the heat dissipation problem is solved, then the mechanical problem is secondary."
If these issues can be addressed, the ecosystem can quickly create automotive memory IP for HBM3. "In late 2023/early 2024, we may actually start to see car design starting with HBM and equipped with qualified auto parts." Murdock said.
Chip stacking
So far, there has been no true 3D package in automotive chips, and this trend is not obvious due to issues such as heat dissipation and form factor.
"It may be easier to have very thin components that can be placed in almost any position inside the engine or integrated in the car itself," says Siemens' Ferguson. "If you have half an inch or an inch of space, the chip might be harder to put in. This is certainly one of the considerations. ”
But vehicles are only part of the car's infrastructure. Stacking chips can play an important role within data centers that will collect and quickly process data generated by millions of cars.
"In the case of a car manufacturer like Tesla, the electronics in the car must be highly reliable, not affected by vibration and heat, lightweight, and do not require a lot of cooling," said John Park, director of product management for packaging and cross-platform solutions at Cadence IC. "The vehicle talks to the server, using a lot of artificial intelligence tools. Images are quickly sent to an AI platform that can be in a water-cooled environment. As far as the car itself is concerned, I don't think there's a need for a lot of 3D integration, not just because of heat dissipation, but also because of cost, reliability, and other factors. At the home center Tesla talked to, however, the situation was quite different. If you're a car company, I don't think you're going to stick to that in mainstream cars. For companies like Tesla, and all the things people want to do about driving automation/self-driving, people are willing to pay a premium for it. There, that could make sense for those types of cars that are being produced. ”
More likely, multiple multi-chip methods will be used inside the vehicle. "There's definitely evolution here." Brad Griffin, director of product management for cadence's multiphysics systems analysis, said. "Maybe the need for heterogeneous integration in the car is not as demanding as in smaller devices, but we are seeing more and more components in the automotive market becoming electrified, so automotive electronics is gradually moving in the direction of silicon intermediation layer 2.5D integration."
In the automotive ecosystem, work is underway on ECUs and other types of devices that will be used in automotive applications. "A big part of what happened during the migration was concerns about how to keep all electrical modeling running effectively." Griffin said. "Engineering teams are used to leaving more space between signals from different chips or components, and everything is compressed in a 2.5D, 3D IC, or hybrid chip stack, so there are a lot of signals between those signals. They are very close to the silicon interpolar layer, so these signals must be modeled and extracted. And not just one or two, or the worst-case scenario. They want to do the full data bus or the complete system itself. ”
Cosmic ray failure mechanism
In addition to the above problems, there are other issues that need to be solved urgently. Different packaging technologies will play a particularly important role in this area. As more and more electronic devices are used in automobiles, these electrons are affected by the same cosmic rays as other electronic devices. The more advanced the chip, the denser the circuitry, and the more likely it is that a single alpha particle will flip multiple memory bits, not just one.
"Cosmic rays are everywhere, and if they break through a particular memory bit at a certain time, they can flip that memory bit." Ansys' Swinnen said. "So if you're hit by a specific cosmic ray at a particular time, any trigger in the chip can flip randomly at any time." In military/aerospace applications, they try to protect the device by placing the circuit in a metal box that can provide some degree of protection for these particles. ”
Due to the high radiation in the upper and upper atmospheres, designers of avionics devices are well aware of this effect. "On Earth, this is an IT transient failure mechanism that can be solved by shielding. These effects are usually not completely masked, so you can only attenuate the impact as much as possible," Swinnen argues. "But these effects can happen at any time." This is one of the reasons why there were five redundant computers when the space shuttle took off. Four are the same and the fifth is different. That's why, because in that high-radiation zone, at any time, you can get the wrong answer from any of the four computers. The answer to the fifth computer is the tiebreaker. ”
This is also a common concern in today's automotive industry, and in this regard, advanced packaging may be able to solve these challenges. "It's worse in cars because cars have a lower fault tolerance," he said. "If your phone goes down and you do something weird, you just have to call back. But if your car breaks down, it's going to be bad. ”