Guided by the "double carbon" goal, all walks of life have accelerated the pace of energy conservation and emission reduction, and the automotive industry is also the same. This can be seen in the rapid popularization of new energy vehicles in recent years. In the past 2021, the total sales of new energy vehicles reached 3.521 million units, an increase of 1.6 times over 2020, and the sales of new energy passenger vehicles were 3.334 million units, an increase of 167.5% year-on-year. According to the latest statistics, the penetration rate of new energy vehicles in China's passenger cars has reached 15.5%, and the proportion of traditional fuel vehicles is declining.
At the same time, the contribution of the popularity of new energy vehicles to energy conservation and emission reduction can also be reflected in data. At the recent press conference on promoting green consumption jointly held by the National Development and Reform Commission, the Ministry of Commerce and other departments, there is such a set of data that the current number of new energy vehicles exceeds 7.8 million, and the annual carbon emissions of new energy vehicles are reduced by about 15 million tons.
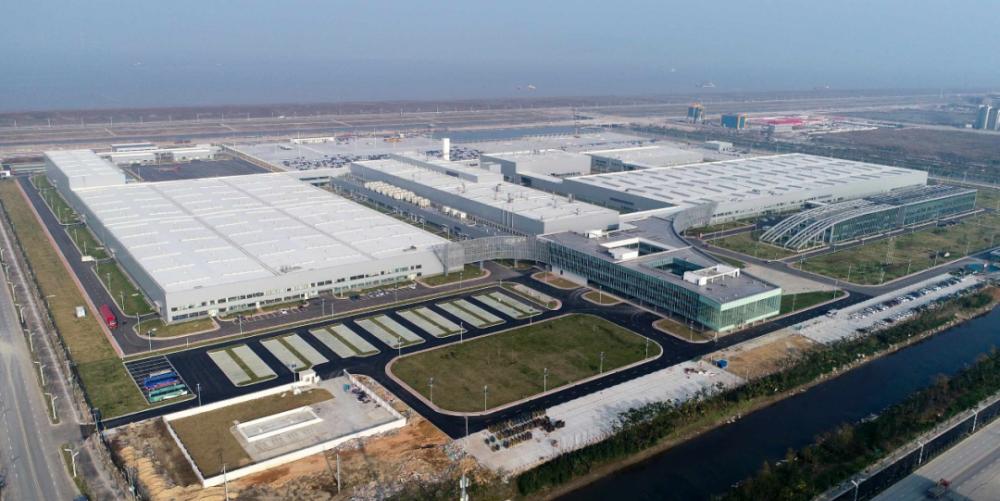
As we all know, automotive products are produced from the factory, and then enter the market for sale, in the automobile production process, the factory needs to generate electricity, consume water resources, and at the same time, the construction and operation of the factory will also produce emissions. Therefore, it is equally important to pay attention to the whole industry chain, especially the energy conservation and environmental protection at the production end.
In order to save energy and reduce emissions, major car companies have begun to focus on the development of green factories. Although everyone has a consensus on intelligence, due to differences in corporate culture background and environmental protection understanding, careful analysis shows that each company is also different.
1
Green factories must be high-tech
As a typical representative of sole proprietorship car companies in recent years, Tesla is undoubtedly a major "star" in the current new energy vehicle market. For the full year of 2021, Tesla's global sales were 936,000 units, an increase of 87% year-on-year, which is a very impressive performance. In addition to the growth of sales, Tesla is also worth mentioning in terms of energy conservation and environmental protection, especially its performance in the use of high technology in energy conservation and carbon reduction at the production end.
In Shanghai Tesla's self-built super factory, Tesla developed its own 4680 battery cell, the cathode material of this cell is a cobalt-free "high nickel cathode", reducing the use of cobalt, a rare material, and its production line can reduce energy consumption by 70% and waste recovery rate by 96%.
At the same time, all corners of Tesla's automated production line are covered with high-reliability industrial networks, providing perfect network services for equipment automation, wireless connection of production equipment, production information data collection, intelligent decision-making, etc., and improving work efficiency to achieve the purpose of energy conservation and emission reduction.
As a veteran traditional car company, Volkswagen not only has a historical background, but also conforms to the trend of the times, and the MEB platform is the best proof. Taking the above-mentioned Volkswagen MEB plant as an example, the SAIC Volkswagen MEB plant is fully connected to 5G technology and always grasps the production dynamics. In terms of energy conservation and emission reduction, the energy intelligent management system in the central monitoring system can achieve dynamic monitoring and early warning of high energy consumption indicators for the five major energy types of the factory by installing smart meters on energy-consuming equipment.
At the same time, the energy management system can also use big data and cloud computing means to analyze and predict workshop energy consumption, achieve refined energy management, provide optimization strategies and optimization schemes for energy consumption and capacity scheduling based on energy data information, and give optimal strategies in energy consumption and scheduling.
In recent years, most of the new car-making forces that have achieved mass production and delivery have achieved good results, and the delivery volume of Weilai, Xiaopeng, Ideal and Weima has achieved rapid growth in 2021. With the growth of delivery volume, funds are gradually abundant, some new car-making forces have realized self-built factories, such as WM Motors, WM New Energy Automobile Intelligent Industrial Park Wenzhou Base is the first intelligent manufacturing base of China's new car-making forces, with a total investment of 2.5 billion yuan, and the total investment of WM Huanggang Base Project is 20.2 billion yuan.
Taking the WM Wenzhou factory as an example, at the beginning of the design, the factory revolved around the three cores of "intelligent, automated and quality assurance system", which is intended to become the benchmark of China's future new energy intelligent automobile industry 4.0 park. Through 24 sets of Siemens programming controllers + 132 sets of advanced equipment such as Fanuc robots, 3 automatic stud welding robots + 4 automatic carbon dioxide protection welding welding robots, the body production department has enabled the workshop to achieve 90% automatic stud welding rate and 100% main line automation rate, leading cadillac and other domestic giant manufacturing plants.
The press lubrication system used in the stamping workshop adopts the automatic fixed-point, quantitative and timed dilute oil circulation lubrication system, and the whole line of the press adopts continuous mode with energy feedback unit, which is more than 30% energy-saving than the ordinary intermittent line. Body workshop spot welding workstation with self-designed, manufactured a full set of tooling, the overall process level reached the world's advanced level, robot welding efficiency is high, stable quality, compared with ordinary robot welding, efficiency increased by 30%, power consumption reduced by 20%;
At the same time, in the painting workshop, WM also adopts the film pretreatment process and the international leading dry carton paint mist collection system to achieve zero emission of nitrogen and phosphorus, and no waste liquid waste residue. It can be seen that in the face of the double carbon target, major car companies spare no effort to carry out energy conservation and emission reduction work, and the difference is that Tesla's energy conservation and emission reduction focus on the application of core technology and the production of core components, Volkswagen controls the energy consumption of the whole plant through the intelligent middle platform, and WM reduces production energy consumption by selecting advanced environmental protection equipment.
2
Energy saving and emission reduction, but also need to start from the details
The widespread use of high-tech equipment is the basis for the establishment of green factories, but if you want to achieve all-round energy conservation and emission reduction, you also need to pay attention to details, because many details of energy conservation and emission reduction alone can not be done by high-tech equipment, can only rely on the correct attitude and positive action of car companies to treat energy conservation and emission reduction, so the energy conservation and emission reduction in the details can better reflect the degree of death of car companies on energy conservation and emission reduction. How to use less water, how to use less electricity, how to improve the recycling rate of materials, and how to deal with exhaust gases are all issues that green factories need to solve. In terms of dead details, major car companies have made visible achievements.
Saic-Volkswagen's MEB plant also reduced carbon dioxide emissions per vehicle through hydroelectric power generation and photovoltaic power generation, and environmental protection technologies such as external heating and power generation, waste heat recovery, rainwater recycling, reclaimed water reuse technology, and volatile organic matter purification system have reduced the plant's five key environmental indicators of energy, water, carbon dioxide, volatile organic compounds and waste by 20%. To reduce transportation emissions, Tesla will unload trucks carrying production materials directly at the crossings of the required parts of the production line. At present, Tesla's Shanghai Gigafactory has achieved 92% of the recycling of battery raw materials metal and 96% of manufacturing waste recycling.
Similarly, WM will also implement energy conservation and emission reduction to the point, taking the WM Wenzhou factory as an example, first of all, from the factory construction, WM put forward the requirements of environmental protection and recyclability, building materials with low energy, high performance, high durability and local building materials, reducing the energy consumption of building materials in the whole life cycle. The same is true in terms of vehicles, the current WM vehicle recyclability rate is 95.10%, recyclable rate is 98.10%.
The daily operation of the factory is bound to consume electricity and water, reduce thermal power generation and save electricity is an effective solution for energy conservation and emission reduction, for this reason, Weima Wenzhou factory installed distributed photovoltaic power generation system, the actual installed capacity of 8.7MWp, the plant utilization rate of nearly 80%, the total power generation since the completion of nearly 30 million degrees, can be used for Wenzhou Oujiangkou residents (41,900) daily electricity for one and a half years (511 days).
WM distributed photovoltaic power generation system
In terms of saving electricity, WM also spares no effort, the factory a total of 909 LED lights instead of ordinary lights, the annual power saving of 72,000 KWh, can be used for a WM car to travel 3,600 kilometers, used to discharge scrap material slag discharge machine to implement interval operation, the annual power saving of 24,000 KWh.
In terms of water conservation, the Wenzhou plant uses a large amount of recycled water to reduce resource consumption, the reuse rate of production water exceeds 97.3%, from January to November 2021, the total water consumption of the factory area is only 198557 tons, and the plant has saved 90,463 tons of water since its establishment, which is equivalent to providing 512 Wenzhou residents with a total water consumption of 1 year.
In addition, the WM Wenzhou factory is also dead energy saving and emission reduction at many details, for example, the factory work car is 387 WM self-produced pure electric vehicles, with an annual carbon reduction of nearly 822.5 tons; industrial energy-saving ceiling fans replace traditional industrial wall fans, with an energy saving rate of >50%; refrigeration unit refrigerants use environmentally friendly refrigerants R134a; the factory fuel forklift is replaced by a battery forklift.
Of course, industrial production, exhaust gas emissions are inevitable, Weima Wenzhou factory is through the exhaust gas oxidation treatment and heat recovery equipment, combustion of hydrocarbons into water and carbon dioxide, can achieve 99.8% purification efficiency, painting varnish spray paint exhaust gas using zeolite adsorption concentration device and waste gas incineration system treatment, removal efficiency > 98%.
On the whole, whether it is in terms of high-tech equipment or factory energy consumption control, WM, a new car manufacturer that has just entered the game of car manufacturing, is on par with Volkswagen and Tesla, which shows that WM's performance in energy conservation and emission reduction is enough to show its reverence for traditional car-making processes. Tesla, Volkswagen, WM these three car companies represent the domestic wholly-owned car companies, domestic joint venture car companies and Chinese brand car companies, they start from the drops of energy conservation and emission reduction, not only with practical actions to support the national "double carbon" goal, but also played a good industry demonstration effect, the entire automotive industry low-carbon development has played a leading role.