在“雙碳”目标的指引下,各行各業都加速了節能減排的腳步,汽車行業亦是如此。這一點從近年來新能源汽車的快速普及便可展現。在剛剛過去的2021年,新能源汽車總銷量達到了352.1萬輛,同比2020年增長了1.6倍,新能源乘用車銷量為333.4萬輛,同比增長167.5%。根據最新統計的結果,新能源汽車在中國乘用車上的滲透率達到了15.5%,傳統燃油車的比重在不斷下滑。
與此同時,新能源汽車的普及對節能減排的貢獻也是可以用資料來展現的。在近日國家發改委、商務部等部門聯合舉行的關于促進綠色消費的新聞釋出會上,有這樣一組資料,目前新能源汽車保有量超過780萬輛,每年新能源汽車減少碳排放1500萬噸左右。
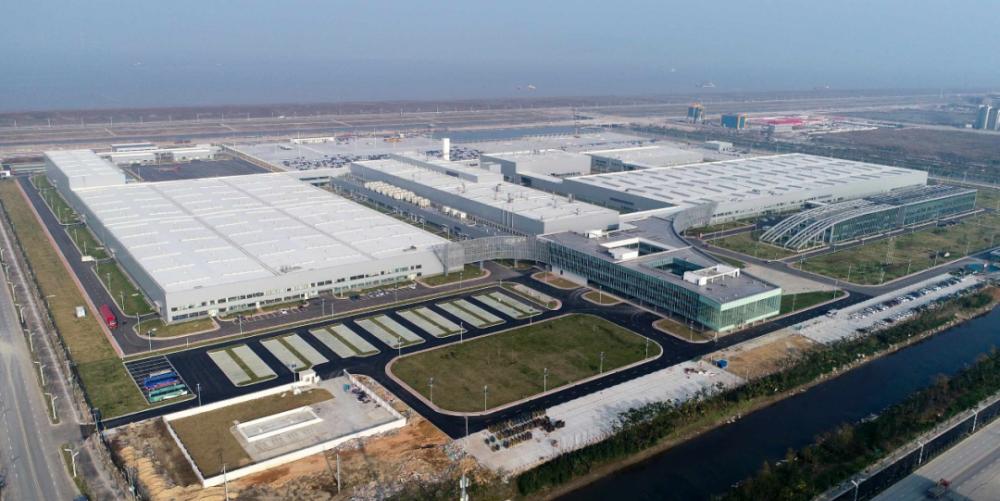
而節能減排光靠新能源汽車在路面上的普及還是不夠的,衆所周知,汽車産品是從工廠生産出來,然後進入市場銷售的,在汽車生産過程中,工廠需要發電、消耗水資源,同時工廠的建設和運作過程中,也會産生排放。是以,注重全産業鍊,尤其是生産端的節能環保也同樣重要。
為了死磕節能減排,各大車企都開始重點發展綠色工廠。盡管在智能化方面大家都有所共識,但由于企業文化背景與環保了解等不同,細緻分析來看各家也有所差異。
1
綠色工廠必須是高科技的
作為近幾年獨資車企的典型代表,特斯拉無疑是當下新能源汽車市場上的一大“明星”。2021年全年,特斯拉全球銷量為93.6萬輛,同比增長87%,這一表現可謂十分亮眼。而在銷量的增長外,特斯拉在節能環保方面也值得一提,其中尤其是其利用高科技在生産端節能減碳方面的表現。
在上海特斯拉自建的超級工廠,特斯拉自研4680電芯,這一電芯的陰極材料為無钴化的 "高鎳陰極 ",減少了對钴這種稀有材料的使用,其生産線可降70%能耗、廢物回收率96%。
與此同時,特斯拉自動化生産線的各個角落都覆寫了高可靠性的工業網絡,為裝置自動化、生産裝置無線聯接、生産資訊資料采集、智能化決策等提供完善的網絡服務,提高工作效率,以達到節能減排的目的。
而作為老牌傳統車企,大衆不僅有曆史底蘊,同時也順應時代潮流轉型,MEB平台就是一個最好的證明。以上汽大衆MEB工廠為例,上汽大衆MEB工廠全面接入5G技術,時刻掌握生産動态。節能減排方面,中央監控系統中的能源智能管理系統,通過在耗能裝置上安裝智能表具,可以對工廠5大能種實作動态監測、預警高耗能名額。
同時,能量管理系統還可以利用大資料和雲計算手段,分析和預測工廠中的房間能耗,實作精細化的能源管理,基于能源資料資訊,對耗能和産能排程提供優化政策和優化方案,在能耗和排産上給出最優政策。
近些年來,實作量産傳遞的造車新勢力,大部分都取得了不錯的成績,2021年蔚來、小鵬、理想、威馬傳遞量均實作快速增長。随着傳遞量的增長,資金逐漸充裕,一些造車新勢力已實作自建工廠,例如威馬汽車,威馬新能源汽車智能産業園溫州基地是中國造車新勢力首個智能制造基地,其總投資額25億人民币,威馬黃岡基地項目總投資202億人民币。
以威馬溫州工廠為例,該工廠在設計之初,就圍繞“智能化、自動化、品質保證體系”三大核心,意在成為中國未來新能源智能化汽車工業4.0園區的标杆。車身生産部通過24套西門子程式設計控制器+132台發那科機器人等先進裝置,3台自動螺柱焊接機器人+4台自動二氧化碳保護焊焊接機器人,讓工廠中的房間實作螺柱焊接自動率90%,主線自動化率100%,領先凱迪拉克等國内巨頭制造廠。
沖壓工廠中的房間使用的壓力機潤滑系統采用自動定點、定量、定時的稀油循環潤滑系統,壓力機整線采用連續模式,帶有能量回報單元,比普通斷續線節能30%以上。車身工廠中的房間點焊工作站配合自行設計、制造的全套工裝,總體工藝水準達到世界先進水準,機器人焊接效率高、品質穩定,相比普通機器人焊接,效率提升30%,電能消耗降低20%;
同時在塗裝工廠中的房間,威馬還采用了薄膜前處理工藝、國際領先的幹式紙盒漆霧收集系統,實作了氮、磷零排放,且無廢液廢渣産生。可見面對雙碳目标,各大車企都不遺餘力進行節能減排工作,而差異化在于,特斯拉的節能減排重點在核心技術的運用與核心零部件的生産上,大衆通過智能中台控制全廠能耗,威馬則通過選擇先進的環保裝置,降低生産能耗。
2
節能減排,還需從細節點滴做起
高科技裝置的廣泛使用,是綠色工廠建立的基礎,但想要實作全方位節能減排,還需要關注細節,因為很多細節之處的節能減排光靠高科技裝置是無法做到的,隻能靠車企對待節能減排的正确态度和積極行動,是以細節之處的節能減排,更能展現車企對節能減排的死磕程度。怎樣少用水,怎樣少用電,怎樣提升材料的回收使用率,以及廢氣如何處理等問題都是綠色工廠需要解決的。而在死磕細節方面,各大車企都做出了肉眼可見的成績。
上汽大衆MEB工廠還通過水力發電和光伏發電,讓制造每台車的二氧化碳排放減少了60%,外加熱電聯供、餘熱回收、雨水回收利用、中水回用技術、揮發性有機物淨化系統等環保技術,使得工廠在能源、水、二氧化碳、揮發性有機物和廢棄物5個關鍵環境名額上下降了20%。為減少運輸排放,特斯拉将運載生産材料的卡車直接在生産線所需部件的道口卸料。目前特斯拉上海超級工廠已實作92%的電池原材料金屬再利用和96%的制造廢棄物回收。
同樣,威馬也将節能減排落實到了點滴之處,以威馬溫州工廠為例,首先從工廠建設上,威馬就提出了環保可回收的要求,建築材料選用蘊能低、高性能、高耐久性和本地建材,減少建材全生命周期中的能源消耗。整車方面亦是如此,目前威馬整車可再使用率為95.10%,可回收使用率為98.10%。
工廠的日常運作必然要消耗電與水,減少火力發電并節約用電是節能減排的有效方案,為此威馬溫州工廠安裝分布式光伏發電系統,實際裝機容量為8.7MWp,廠區使用率近80%,建成至今總發電量近3000萬度,可供溫州瓯江口常住居民(4.19萬)日常用電一年半(511天)。
威馬分布式光伏發電系統
在節約用電方面,威馬也是不遺餘力,工廠總計909盞LED燈代替普通電燈,年節電7.2萬KWh,可供一輛威馬汽車行駛3,600公裡,用以排出邊角料的排渣機實行間隔運作,年節電2.4萬KWh。
節約用水方面,溫州廠區大量使用循環水降低資源消耗,生産用水重複使用率超過 97.3%,2021年1-11月,廠區用水總量僅198557噸,工廠建廠至今節水90463噸,相當于為512個溫州居民提供了1年的用水總量。
此外威馬溫州工廠還在很多細節層面死磕節能減排,例如,工廠工作用車為387輛威馬自産純電汽車,年減碳近822.5噸;工業節能吊扇取代傳統工業壁扇,節能率>50%;制冷機組制冷劑選用環保制冷劑R134a;廠區燃油叉車更換為電瓶叉車等。
當然工業生産,廢氣的排放是不可避免的,威馬溫州工廠則通過機廢氣氧化處理與熱能回收裝置,燃燒對烴類轉化成水與二氧化碳,可以實作99.8%的淨化效率,塗裝清漆噴漆廢氣采用沸石料吸附濃縮裝置與廢氣焚燒系統處理,去除效率>98%。
綜合看來,不論是在高科技裝置還是工廠能耗把控方面,威馬這家剛入局造車不久的新造車企業,都與大衆、特斯拉這些國際不相上下,可見威馬在節能減排方面的表現,足以說明其對傳統造車工藝的敬畏。特斯拉、大衆、威馬這三家車企分别代表了國内獨資車企、國内合資車企和中國品牌車企,它們從點滴之處做起的節能減排,不僅是用實際行動支援國家“雙碳”目标,也起到了不錯的行業示範效果,對整個汽車行業的低碳發展起到了帶頭引領作用。