Original title: Hainan Weekly | There is a pottery garden under the Luobi Peak
Hainan Daily reporter Xu Huiling
In the afternoon, the sun shines obliquely on the branches of the trees, and the dappled light and shadow crawl slowly on the walls made of clay pots and tiles. In the courtyard, several students either slapped the dirt in front of the drawing machine, or carefully trimmed the pottery with a turning knife, indulging in the world of pottery. Outside the courtyard, birdsong and dog barking are an idyllic scene. This is the Dongya Firewood Burning Studio hidden in the next village of Luobi Peak in Sanya. The studio is an off-campus practice platform for students of Sanya College, and the main task is to burn pottery.
Pottery is the art of Mother Earth, a fusion of mud and fire. In the past 9 years, Yang Dan, a teacher at the School of Art of Sanya College, and his students have used primitive methods to make pottery and burn pottery in this small world, exploring the soul of pottery in their hearts.
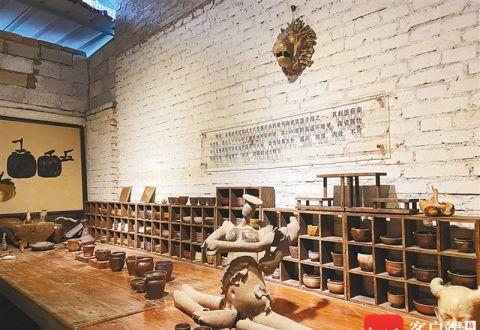
The works on display at the East Cliff Wood Burning Studio.
Build a wood kiln to burn pottery
The chicken coop was converted into a studio
"The students of Sanya College's sculpture major and product design major have some understanding of pottery and have mastered some theoretical knowledge, and our original intention in establishing the studio is to provide students with a practical platform." Yang Dan said straight to the point.
One day in November 2013, Yang Dan and his friends walked around the Li village near the school, and their idea was simple: find a suitable place to build a wood kiln to burn pottery. After several turns, they found a dilapidated red brick house in The village of Nanding, not far from the school, the chicken coop of the villagers' old Li family. Later, it was transformed into the East Cliff Wood Burning Studio.
The studio is named "East Cliff" because it is located at the foot of the mountain east of Luobi Peak. Wood-fired refers to the studio firing ceramics from wood as fuel. In the era when there were no gas kilns and electric kilns, wood firing was the most common way of firing ceramics.
This flat-roofed brick-concrete building with three courtyards embodies the painstaking efforts of Yang Dan, Uncle Yang and a class of students. Uncle Yang, who is over seventy years old, is the father of Yang Dan's friend. In 2014, Uncle Yang moved from Henan to Sanya. His addition has made substantial progress in the construction of the studio. Leveling the land, planting trees, building walls, building kilns... In order to save costs, Yang Dan and Uncle Yang worked as construction workers and gardeners.
On a wall on the west side of the courtyard, there are more than 30 dirt blocks with names and dates engraved on them. Most of these are the works of students who go to the Dongya Wood Burning Studio to participate in off-campus practice. A small "building" in the courtyard that is less than 3 meters high is particularly interesting, and Yang Dan calls it a "pottery tower", which is made of some unburned pottery. Yang Dan has strict selection criteria for finished pottery, and after each kiln opening, slightly flawed works will be discarded. Nevertheless, he also believes that even burned-out works are alive, and that piling them into "towers" is to commemorate those pottery that have fulfilled others and sacrificed themselves.
Every spring, a few tender green vine seedlings protrude from the "pottery tower", as if to tell the new life of the clay.
Clay pots fired in the East Cliff Wood Burning Studio.
To be a pottery is like to be a human being
Focus on selflessness to achieve wonderful
The inconspicuous soil under people's feet is the raw material for the creation of potters in the hands of potters. They are constantly rubbing and trimming, giving new forms and life to the soil.
"Doing pottery is like being a person, every step must be walked steadily." Yang Dan said that it takes a week or more to make and fire a piece of pottery, and only by focusing, forgetting oneself and striving for excellence can the brilliance of pottery be achieved. This is Yang Dan's understanding of pottery making, and it is also his requirement for students.
Dongya Wood Burning Studio uses the original method to make pottery, and the output is relatively low. Since the first kiln of pottery was fired on February 22, 2014, a total of 80 kilns have been fired.
The pottery process is cumbersome, which is first reflected in the selection and processing of clay. "There are many types of clay for wood-fired pottery, and it is often necessary for potters to match to meet the requirements. Today, the clay used in the Dongya wood-burning studio has been stored for nearly 8 years. The mud in Yang Dan's hand became particularly soft and smooth after being slapped and kneaded.
This mud material was found by Yang Dan and his students in 2014 in a village near the Sanya Tianya Haijiao Tourist Area, and the mud is fine and soft, dark red, known as "Red Pond Mud". Yang Dan said that most of the clay collected from the wild has "wildness", the mud is too delicate, easy to crack, need to be refined by drying, crushing, soaking fermentation, filtering mud and other processes, repeat more than a dozen times, and then mixed with other clay and porcelain clay, in order to be used for pottery.
Kneading mud, pulling blanks, spinning blanks, repairing blanks... Pottery is the process of turning ideas and ideas into reality. The kneaded clay is placed in the center of the turntable of the drawing machine, and after the turntable begins to rotate, the hands cooperate to operate, and the prototype of the pottery blank begins to appear.
"Repairing the billet is a delicate work, and if you are not careful, the pottery billet will break." Deng Jiaying, a student at the School of Art of Sanya College, said that most of the utensils produced by Dongya ChaiYao Studio are teapots, teacups and other utensils, and the repair of the billet requires the direction and strength of the knife, which cannot be learned from books, and can only be explored in practice, and the feeling can be found through continuous "trial and error".
Yang Dan (left) instructs students in making pottery blanks.
Mounting the kiln looks simple, but in fact it is also learned. Yang Dan and Uncle Yang will place different ceramic blanks in different positions according to the path and skewer of the fire burning in the kiln to achieve the best results.
"The wood used in the kiln needs to be prepared a month in advance, and our studio has a principle that we will never cut wood for the kiln, and we will only pick trees or dead wood that have fallen naturally." Yang Dan said that after the typhoon, he and his students often went to the back mountain of Sanya College to collect wood, and nearby villagers would also send trimmed longan trees and lychee branches to the studio.
The process of firing the kiln is both exciting and uncertain, success or failure, in one fell swoop. This uncertainty may also be one of the charms of pottery. For 3 to 5 days, Yang Dan and the students took turns throwing firewood, the firewood crackled, and the flame temperature reached 1200 ° C.
Inside the kiln, mud, fire, and wood played against each other and began to create miracles; outside the kiln, there was a long wait.
Clay pots on display at the Dongya Wood Burning Studio.
Pursue rustic beauty
I look forward to the color of the sea that can be burned
The beauty of wood-fired utensils, the beauty in the original simplicity. Burning pottery in the form of firewood pursues nature, simplicity and uniqueness.
"The shape of the wood-fired utensils is concise, and we pay attention to preserving the traces of handcraft and the original texture of the clay in the process of production, and do not glaze the body." Yang Dan said that when the pottery is burned in the way of wood burning, the choice of date is more casual, and when there is enough pottery blank that can fill a kiln, it can enter the kiln, seal the kiln, and burn the kiln, and will not wait for the smoke and rain weather in order to burn out the azure sky like the kiln porcelain. The glaze produced by the wood-fired ashes gives the pottery a rough texture and a simple color.
Wood-fired pottery, each kiln, each piece has its own characteristics, can be described as "into the kiln one color, out of the kiln colorful". Yang Dan said that in ancient times, people often used the phrase "ten kilns and nine failures" to describe the difficulty of wood-fired ceramics, even if 80 kilns have been burned, he is not fully sure of the kiln.
The day of the opening of the kiln was the most lively day of the Dongya wood-burning studio. Pottery enthusiasts, villagers and studio staff crowded the courtyard, and pieces of pottery were presented with warmth.
Yang Dan said that when the kiln was opened, the potters did not know what their works "looked like", but only looked for beauty and hope from the ashes. If the work shows an unexpected ash or fire mark effect, it will feel like a treasure. Some works only feel ordinary when they first see it, but after a period of time, they can find their beauty.
After nearly 9 years of development, Dongya Wood Burning Studio has formed a complete chain of pottery production, firing and sales. Some students learn pottery making here and sell excellent works to the outside world, and many foreigners come here to learn pottery skills.
The students who came to the studio to participate in the off-campus practice walked in batches one after another, and only Yang Dan, Uncle Yang and the two stray dogs that had been adopted for several years, "Ears" and "Ice Cream", insisted here.
In recent years, Yang Dan has integrated Sanya marine cultural elements such as shell powder into pottery making, hoping to burn pottery artworks with unique Sanya characteristics. Although the effect is not ideal, he is still groping, "For the Dongya Wood Burning Studio, the best burner is always the next kiln." Yang Dan said that he looked forward to the day when the studio could burn out the colors of the sea. (Huiling Xu)
Source: Hainan Daily