Editor's Note: Core Intelligent Driving - A collection of the views of famous experts in production, education and research, a comprehensive analysis of AI chips, third-generation semiconductors and other opportunities and challenges in the era of "big deformation" of automobiles!
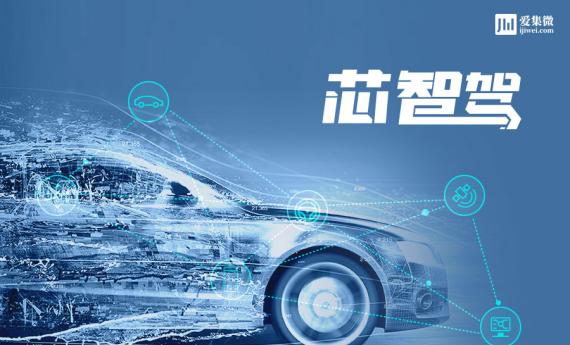
Jiwei Network reported that in 2021, when the global automotive industry is short of cores, Tesla seems to have not been greatly affected for most of the time. The electric car maker produced 930,000 vehicles and delivered 936,000 vehicles in the past year, exceeding Wall Street's previous expectation of about 900,000 full-year deliveries. Sales in 2021 are twice as high as in 2020. Meanwhile, Tesla has set a new quarterly delivery record for six consecutive quarters.
Other traditional car manufacturers such as GM and Volkswagen have lived very different lives. Suffering from chip shortages and price increases, almost all car companies around the world are spending 2021 in production cuts and shutdowns. Chip shortages have directly led to a sharp decline in revenue and production in the global automotive industry. According to AutoForecast Solution, the cumulative production reduction in the global automotive market in 2021 is about 10.2 million units due to chip shortages.
The Wall Street Journal called Tesla "the big winner in this chip crisis", and Tesla's ability to obtain key components such as chips is obviously more bright than the beautiful delivery figures.
How is Tesla coping with chip shortages?
The past year has been described by Musk as a "supply chain nightmare." In the first quarter of 2021, Tesla's Fremont plant in California was forced to close for two days due to chip shortages. Tesla also confirmed for the first time in a conference call after the release of the first quarter of last year that there was a shortage of chips, the main gap was the microcontroller chip (MCU). But tesla's engineering and software teams have since begun to solve these problems. Tesla wrote in its second-quarter earnings report: Tesla's team reacted quickly, mitigating the consequences of the chip shortage. At the time, Tesla revealed that its electrical and hardware teams were designing, developing, and validating new MCUs, with 19 types.
Source: Tesla official website
"We used alternative parts and programming software to alleviate the barriers posed by the shortage." Tesla pointed out in its third quarter 2021 report that relying on the company's strong software capabilities, Tesla can quickly rewrite software to use alternative chips. This has impressed traditional automakers. Herbert Diess, CEO of The German Volkswagen Group, has previously praised Tesla's ability to modify software to adapt to the new chips used within 2 to 3 weeks. Other traditional car companies have realized that they need to do some of what Musk and Tesla have been doing, for example, Mercedes-Benz plans to use fewer proprietary chips, more standardized semiconductors, and write their own software in future models.
In addition, some of the chips in Tesla's Autopilot system are designed in-house, and the company also manufactures a variety of components, including seats and lithium batteries, and it also has a fully self-operated network of direct retail stores, after-sales service stations and charging stations.
Morris Cohen, an emeritus professor at the Wharton School of the University of Pennsylvania who specializes in manufacturing and logistics, commented that Tesla's approach is in many ways an "autogenic" phenomenon in the automotive industry. In the early days of the automotive industry, Ford also had its own steel plant and rubber plantations.
Over the past few decades, traditional automotive supply chain thinking has held that OEMs should focus on design and final assembly, leaving the rest to suppliers. This helps reduce the excessive spending of money in factories by large companies, but also makes them more vulnerable to supply chain turbulence.
Morgan Stanley also pointed out in a recent report that tesla is "not lacking in cores" when analyzing the reasons for tesla's "no lack of cores", in addition to the chip's self-research capabilities and software capabilities, its strong supply chain vertical integration capabilities and ability to control the supply chain are more critical factors for it to become a big winner in the lack of cores.
One detail worth noting, Tesla CFO Zach Kirkhorn has said that the company expected the electric vehicle market to rebound quickly after the epidemic, so it did not cut chip orders from suppliers, a decision that led Tesla to better cope with the global chip shortage. At that time, most of the traditional automakers cancelled chip orders from suppliers.
From the Tesla supply chain to see the deep reasons for the lack of cores in cars
So behind this, what is the deep-seated reason for the lack of core in the car?
IC Insights' latest analysis believes that in addition to factors such as supply chain issues, the real reason for the shortage is the surge in demand for automotive chips in 2021, not the inability of semiconductor suppliers to increase capacity. According to IC Insights, semiconductor supplier shipments to the automotive industry increased by 30% in 2021 compared to 2020, much higher than last year's 22% increase in global semiconductor shipments. In addition, the supply of integrated circuit components to the automotive industry increased by 27% in 2021 compared with 2019 before the epidemic.
The increase in automotive semiconductor unit shipments in 2021 is the highest percentage increase since 2011 to date, and easily exceeds the 20% increase in automotive semiconductor shipments in 2017.
The sharp rise in the variety and quantity of automotive semiconductors is bound to bring more complex supply chain management challenges.
Sun Changxu, managing partner of Xiaomi Production and Investment, pointed out sharply at the first Jiwei Automobile Semiconductor Ecological Summit held at the end of last year that the deep-seated reason for the lack of cores in automobiles is not the shortage of goods, but the chaos of supply chain management. She pointed out that in recent years, intelligent electrification has also greatly increased the types and quantities of chips needed to be used in automobiles, and the difficulty of automobile supply chain management has also been greatly improved, at the same time, the rise of new forces to build cars has broken into the automobile supply chain, and the cooperation between these new forces and Tier-1 and chip factories is still in the run-in stage from zero to one. "The management of the entire automotive chip supply chain is a mess and completely chaotic. The more small the chip, the more chaotic the management, and the large chip is the chip factory directly facing the car factory, the two sides are in direct contact, and the probability of stock shortage is relatively low. "Therefore, the automotive chip industry chain looks out of stock, and the deep-seated reason is caused by the chaos of supply chain management."
To solve this problem, in her view, it is necessary for the car factory to make a forecast directly to the chip supplier and stabilize the procurement order in order to change the chaotic appearance of the automotive chip supply chain management. "This is like the mobile phone chip supply chain, when there is a shortage of goods, the mobile phone chip factory will do capacity allocation according to the past demand of the mobile phone terminal manufacturers, which is a very important means to manage the order of the market when it is out of stock."
At present, the development trend of the transformation of the automobile industry is almost similar to that of the mobile phone industry of that year, and as the chip becomes more and more important for the car, the supply chain system of the automobile chip needs to be established and improved. This is a new test for the global automotive supply chain, and it is imperative to reshape the situation.
Tesla has benefited a lot over the past year by relying on supply chain visibility and a high degree of vertical integration of supplier relationships. But even as the big winner of this chip crisis, Tesla has not been able to completely avoid the impact of chip shortages. On The fourth quarter of Tesla and the full year of 2021 earnings call on January 26, 2022 local time, Musk said that although the chip shortage will ease in the coming year, it will still be a problem. He warned that supply chain restrictions could drag down the company's overall performance "until 2022." The next year is a top priority for Tesla to maximize capacity and production throughout the supply chain, which will also be the key to continuous competitiveness in the field of smart electric vehicles.
(Proofreading/Jimmy)