In recent years, with the rapid development of the automobile industry, the most mature automotive lightweight materials for automotive applications include modified plastics and their composite materials and lightweight alloys based on alloys. Polymer material applications can be seen in automotive interior materials, load-bearing parts, and new energy power batteries. However, the performance of these materials in terms of flame retardancy is not ideal, so when these materials are applied to automotive parts, the first consideration is safety. Improving the flame retardant properties of such materials is an important means to improve the safety of automobiles at present.
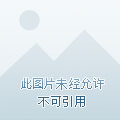
This article will start from the future direction of automobiles and introduce various flame-retardant polymer materials and their development directions.
The future development direction of flame-retardant polymer materials for auto parts
At present, the flame retardant polymer materials used in auto parts are mainly BASED ON PP, PU, ABS and PC materials, and a series of high-performance flame retardant polymer materials have been developed at the same time for the special needs of some auto parts. Flame-retardant polymer materials with environmental protection, high efficiency and excellent mechanical performance and mechanical properties will be the development direction of modified plastics for auto parts.
Compared with traditional fuel vehicles, new energy vehicles have added battery pack modules, charging piles and charging guns and other components, and the use of engineering plastics for a single new energy vehicle battery pack module is about 30kg, and the plastic shell of new energy vehicles is currently mainly used for modified PP, PPS, PPO, etc. Charging pile due to high use standards and harsh use of the environment for engineering plastics demand, each charging pile needs about 6kg of engineering plastics, the current common main PBT, PA and PC.
The application of polymer materials to auto parts must ensure that the flame retardant and fireproof properties of the materials meet national standards. Most polymer materials are not ideal in flame retardant performance, so when applied to automotive parts, they need to be flame retardant modified, prepared into polymer materials with flame retardant properties, and increased their limiting oxygen index (LOI) to 25. 0% ~ 35. 0%, effectively improving the car safety index.
Combustion mechanism and flame retardant mechanism of polymer materials
>>>>
Combustion mechanism of polymer materials
Temperature, combustibles, and oxygen are the three elements of a fire.
When the temperature rises to a certain value, the polymer material is first degraded into a macromolecular compound when heated, and then continues to be cracked into a low molecular weight compound. These low molecular weight compounds are volatile combustible substances, when they accumulate in the air to a certain concentration, the phenomenon of combustion occurs, and the release of combustion heat further promotes the degradation of polymer materials. The combustion of polymer materials is divided into two processes, namely the degradation and combustion of thermal oxygen.
Flame retardant mechanism of polymer materials
From the combustion mechanism of polymer materials, it can be seen that flame retardancy can be achieved by slowing down or blocking one or more elements. The flame retardant mechanism of polymer materials is generally divided into three types: gas phase flame retardant, condensed phase flame retardant and interrupted heat exchange flame retardant.
1) Gas phase flame retardant mechanism:
Flame retardants decompose by heat to produce non-combustible gases, reducing the concentration of combustible gases and oxygen in the system, so that the combustion process of the flame is terminated; Flame retardant polymer materials release a large amount of inert gas when burned, diluting O2, terminating the combustion process, in addition to the release of a large amount of high-density steam, so that the combustion suffocation, the combustion process is terminated.
2) Flame retardant mechanism of condensed phase:
The addition of flame retardants will accelerate the breaking of chemical bonds in polymers of polymers, and the thermal decomposition and endothermic process of flame retardants will reduce the surface temperature of combustibles and slow down or stop combustion; During the thermal decomposition of the flame retardant, the flame retardant will produce a flame-retardant, thermally insulated porous carbon layer covering the surface of the combustible, and the carbon layer protects the internal matrix of the combustible, blocking the diffusion of combustible gases and heat, and slowing down or terminating the combustion of the polymer material.
3) Interrupt heat exchange flame retardant mechanism:
Refers to the combustion of flame retardant polymer materials generated part of the heat transfer away, reduce the temperature of the combustible so that it is lower than the material thermal decomposition temperature, can not maintain the production of volatile substances, combustion stopped, so as to achieve the purpose of flame retardant. Based on different blocking combustion mechanisms, flame retardants are generally divided into two types: additive flame retardants and reactive flame retardants. The research on the combustion and flame retardant theory of polymer materials can provide a theoretical basis for finding new high-performance flame retardants, determining appropriate flame retardant methods and improving the flame retardant level, and providing more efficient flame retardant solutions for polymer materials used in automotive parts.
Application of flame retardant polymer materials in automotive parts
At present, in automotive parts such as automotive load-bearing parts and new energy vehicle battery packs, polymer material applications can be seen everywhere. The application of polymer materials in automotive parts and components, as well as the need to improve automotive safety, have promoted the development of flame-retardant polymer materials. At present, the flame retardant polymer materials used are mainly PP, PU, ABS and PC, and according to the special needs of auto parts, there are also composite materials (alloying), PA, PBT and PMMA.
Flame retardant PP
Polypropylene (PP) is the largest amount of polymer material used in automotive plastics, with excellent chemical resistance, and simple processing, low cost, widely used in automotive dashboards, battery pack shells, door guards, columns, seat shields, bumpers and so on. Due to the poor flame retardant type of PP before the flame retardant was added, its limiting oxygen index (LOI) was only 17. 8%, easy to burn after an accident. At present, the research on AUTO FLAME Retardant PP at home and abroad mainly focuses on the modification of the polypropylene matrix, and at the same time, by adding low-toxicity, halogen-free flame retardants, polypropylene composite materials with excellent mechanical properties and flame retardant effects are developed to meet the flame retardant needs of auto parts.
At present, the flame retardants suitable for polypropylene are mainly additive flame retardants, and the more used halogen flame retardants (commonly used are brominated flame retardants or bromine-antimony co-effect flame retardants), inorganic filler flame retardants (commonly used are magnesium hydroxide and aluminum hydroxide), phosphorus (melamine polyphosphate, melamine phosphate, ammonium polyphosphate, phosphonitrile, phosphate, etc.), nitrogen (MCA, APP, MPP, etc.), and intumescent flame retardants (IFR). With the implementation of strict environmental protection policies and the promotion of halogen-free, it is the trend of the times that flame retardants for polymer materials are halogen-free.
Using polypropylene as the matrix and long glass fiber as the filling material, adding phosphorus and nitrogen halogen-free expansion flame retardant, melamine urate, and melamine polyphosphonate salt was added to obtain a long glass fiber reinforced halogen-free flame retardant polypropylene battery cell. In the preparation process, the double masterbatch preparation method is also adopted, and the flame retardant PP products are prepared by preparing the long glass fiber long glass fiber masterbatch and the halogen-free flame retardant masterbatch respectively, and the two are mixed evenly and then directly injected to obtain flame retardant PP products. The double masterbatch preparation method avoids the problems of flame retardant degradation caused by excessive shear zone temperature caused by excessive shearing in the manufacturing process of long glass fiber masterbatch and the mechanical performance degradation caused by short length of glass fiber.
Polypropylene fiber/wood fiber/hemp fiber ternary composite material is a common material for automotive interior parts.
Among the flame retardant PP halogen-free modification technology, IFR is considered to be one of the best prospects for halogen-free flame retardant PP because of its advantages of minimal impact on PP processing fluidity, low density advantage and excellent flame retardant efficiency, as well as the advantages of small dosage and low smoke and non-toxicity.
Flame retardant PP started late in the mainland, but developed rapidly. In particular, the rapid growth of the new energy automobile industry in recent years has directly promoted the rapid growth of flame retardant PP demand, and many domestic universities, scientific research institutions and enterprises have participated in the development of flame retardant PP for automotive parts. In the future, the research on automotive flame retardant PP will focus on high efficiency and environmental protection, and develop flame retardant PP materials with excellent performance by selecting halogen-free flame retardants, expansion flame retardants, phosphorus and nitrogen flame retardants and compound flame retardants combined with other additives.
Flame retardant ABS
ABS is the world's largest use of polymer materials for home appliances, and about 80% of ABS consumption in mainland China is used for home appliance production. ABS is a typical material suitable for automotive coating due to its strong durability and corrosion resistance to plastic surface coating, and it is also used in the production of automotive parts. Because ABS resin only contains C, H, O three elements, it does not have flame retardant properties, which makes ABS resin have poor stability at high temperature and is extremely easy to burn; The ignition process is also accompanied by the generation of odor gases and black smoke particles, which are directly used for auto parts and have safety hazards. Therefore, before use, it must be modified for flame retardant performance and heat resistance.
Halogen flame retardant flame retardant efficiency is relatively high, of which bromine flame retardant effect is better than chlorine system, although there is a strong pressure on environmental protection, bromine flame retardant rely on the outstanding flame retardant effect and low cost of the two major advantages, for some flame retardant standards strict requirements of the field and some difficult to flame retardant materials, bromine flame retardant is still the most practical choice. About 70% of electrical and electronic products are brominated flame retardants, of which decabromodiphenylethane is mainly used for ABS flame retardant. However, the promotion of environmental protection and halogen-free has also made halogen-free, phosphorus and nitrogen flame retardants used for ABS attract attention.
THE FUSION BLENDING OF ABS WITH POLYCARBONATE (PC) RESULTS IN PC/ABS COMPOSITES, WHICH COMBINES AND PC ADVANTAGES WITH HIGH HEAT DEFLATION TEMPERATURE AND STABILITY, IMPROVED PROCESSABILITY. PC/ABS alloy has become the largest and fastest growing resin alloy at present, and can be used in other parts such as automotive dashboards, battery packs, and automotive bodies. PC resin itself is a flame retardant self-extinguishing material, UL94 is V2 grade, but after blending with ABS, the flame retardant performance is reduced, so it needs to be modified before it can be used in automotive parts. At present, the flame retardants commonly used for the flame retardant modification of PC/ABS alloys include halogen flame retardants, phosphorus flame retardants, and nano flame retardants.
Flame retardant PC
As one of the top five engineering plastics, polycarbonate (PC) is used in the production of automotive components because of its advantages of high strength, high impact resistance and heat resistance. For example, automotive instrument panels, lighting systems, heating plates, defrosters and bumpers made of polycarbonate alloys. With the upgrading of consumption, new energy vehicles and lightweight development, domestic demand for PCs is also growing, in 2019 the global PC production capacity increased to 6.4 million tons, China accounted for 72%, reaching 4.6 million tons, 2015-2019 global production capacity average annual growth rate of 24. 8% 。 PC itself has a certain degree of flame retardancy, compared with other ordinary polymer materials (such as PE, PP, etc.) has a certain advantage, LOI can reach 21% ~ 24%, UL94 is V2 level. However, in applications where the flame retardant requirements for auto parts are relatively high, their flame retardant performance is still difficult to meet, and it is still necessary to modify the flame retardant.
Brominated flame retardants can significantly improve the flame retardant properties of PCs, commonly used are Decabromodiphenyl Ether (DBDPO), tetrabromobisphenol A (TBB-PA) and so on. However, flame retardant materials containing bromine are easily decomposed at high temperatures to produce corrosive gases, which will damage auto parts. In addition, the addition of brominated flame retardants can seriously affect the transparency of PCs, and also do not meet the requirements of the EU halogen-free and environmental protection policy. At present, the most used phosphorus flame retardants in industrial PC products are TPP (triphenylphosphonate), RDP (diphenyl phosphate) and BDP. TPP is solid at room temperature, the thermal stability is poor, it is easy to volatilize at pc processing temperature, and only plays a gas-phase flame retardant role. RDP and BDP at room temperature for liquid, with good thermal stability, can play a gas phase and solid phase flame retardant at the same time, while BDP and PC have better compatibility, can play a role in growth hardening, so PC + BDP system has become a more used system, BDP added proportion of 10%.
In addition, silicon-containing compounds, as a new generation of environmentally friendly flame retardants, have gradually attracted attention because of their high efficiency, low toxicity, no pollution and other characteristics, as well as the small impact on PC processing performance and physical properties, such as polysilanes, polysiloxanes, etc. PCs for auto parts are also moving closer to halogen-free environmental protection when selecting flame retardants, and improve the comprehensive performance of PCs by adding a variety of additives or preparing composite flame retardants. In addition, PC through the COMPOSITION of ABS, PBT and other composite materials is also the best choice to improve PC processing performance and flame retardant performance.
Other flame retardant polymer materials
PP, PU, ABS and PC are currently mainly used in the production of automotive parts flame retardant polymer materials, in addition, the two or more polymer materials melt blended composite materials are also currently used more of a material, such as PC / ABS, PC / PBT, PC / FR composite materials and so on. Polymaker Company, launched three PC-based 3D printing materials for the production of automotive parts, three products are Polymaker PC-ABS, Polymaker PC-PBT, PolyMaxPC-FR, these three products have their own characteristics, in terms of heat resistance, impact resistance, easy processing and flame retardant performance, have a good performance. The Polymaker PC-PBT is an improvement on the Makroblend range from Covestro to improve the overall performance of the material. Similarly, PolyMaxPC-FR has made significant improvements to the flame retardant properties of Makrolon products from Covestro, bringing the material UL94 to V0 and using the material for battery housings for new energy vehicles.