近年來,随着汽車工業的快速發展,汽車應用最為成熟的汽車輕量化材料包括改性塑膠及其複合材料和以合金為主的輕質合金等材料。在汽車内飾材料、承重零部件,以及新能源動力電池等零部件中均能看到高分子材料應用的身影。但是這些材料在阻燃方面的性能不盡理想,是以,将這些材料應用于汽車零部件時,首要考慮的問題就是安全性。提升這類材料的阻燃性能是目前提高汽車安全性的重要手段。
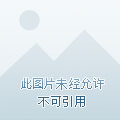
本文将從汽車未來方向講起,介紹各種阻燃高分子材料及其發展方向。
汽車零部件用阻燃高分子材料未來發展方向
目前,應用于汽車零部件的阻燃高分子材料主要以PP、PU、ABS 及 PC 等材料為主,針對一些汽車零部件的特殊需求,還同時開發出一系列高性能的阻燃高分子材料。環保、高效以及優異的機械加工性能和力學性能的阻燃高分子材料,将是汽車零部件用改性塑膠的發展方向。
相比于傳統燃油車,新能源汽車新增了電池組子產品、充電樁及充電槍等部件,單台新能源車電池組子產品工程塑膠的使用量約30kg,新能源車塑膠殼體目前主要使用改性PP、PPS、PPO等。充電樁由于較高的使用标準和嚴苛的使用環境對工程塑膠需求較大,每個充電樁約需6kg工程塑膠,目前常見的主要有PBT、PA和PC等。
将高分子材料應用到汽車零部件中,必須保障材料的阻燃防火性能達到國家标準。大部分高分子材料的阻燃性能不盡理想,是以應用于汽車零部件時均需要對其進行阻燃改性,制備成具有阻燃性能的高分子材料,将其極限氧指數 ( LOI) 提升至 25. 0% ~ 35. 0% ,有效提升汽車安全指數。
高分子材料燃燒機理與阻燃機理
>>>>
高分子材料的燃燒機理
溫度、可燃物,以及氧氣是火災發生的三要素。
當溫度上升至一定數值時,高分子材料受熱首先降解為大分子化合物,然後繼續裂解為低分子量化合物。這些低分子量的化合物是具有揮發性的可燃物質,當其在空氣中積累到一定濃度時,就會發生燃燒現象,燃燒熱量的釋放又進一步促進了高分子材料的降解。高分子材料的燃燒分為兩個過程,即熱氧的降解與燃燒。
高分子材料的阻燃機理
從高分子材料燃燒機理可知,阻燃可通過減緩或阻止一個或多個要素來實作。高分子材料阻燃機理一般分為氣相阻燃、凝聚相阻燃和中斷熱交換阻燃三種。
1) 氣相阻燃機理:
阻燃劑受熱分解産生不燃性氣體,降低了體系中可瓦斯體和氧氣的濃度,使得火焰的燃燒過程被終止; 阻燃高分子材料燃燒時釋放出大量惰性氣體,稀釋了 O2,終止了燃燒過程,此外還可能釋放大量高密度蒸汽,使燃燒窒息,燃燒過程被終止。
2) 凝聚相阻燃機理:
阻燃劑的添加會加速高分子材料聚合物中化學鍵斷裂,阻燃劑熱分解吸熱過程使可燃物表面溫度降低,減緩或終止燃燒; 阻燃劑熱分解過程中會産生難燃、隔熱的多孔炭層覆寫在燃燒物的表面,炭層保護着可燃物内部基體,阻斷可瓦斯體和熱量的擴散,減緩或終止了高分子材料的燃燒。
3) 中斷熱交換阻燃機理:
是指将阻燃高分子材料燃燒産生的部分熱量轉移走,降低可燃物的溫度使其低于材料熱分解溫度,不能維持産生揮發性物質,燃燒終止,進而達到阻燃的目的。基于不同的阻斷燃燒機理,一般将阻燃劑分為添加型阻燃劑和反應性阻燃劑兩種類型。對高分子材料燃燒及阻燃理論的研究,可為尋找新型高性能阻燃劑,确定合适的阻燃方法以及提高阻燃水準提供理論依據,為汽車零部件用高分子材料提供更加高效的阻燃解決方案。
阻燃高分子材料在汽車零部件中的應用
目前,在汽車承重件、新能源車電池組等汽車零部件中,随處可見高分子材料應用的身影。高分子材料在車用零部件中的應用,以及提升汽車安全性的需求,促進了阻燃型高分子材料的發展。當下應用的阻燃高分子材料主要以PP、PU、ABS和PC為主,根據汽車零部件的特殊需求也相應有複合材料 ( 合金化) 、PA、PBT和PMMA等材料的使用。
阻燃PP
聚丙烯 (PP)是車用塑膠中用量最大的高分子材料,具有優異的耐化學腐蝕,并且加工過程簡單、成本低,廣泛應用于汽車儀表盤、電池包外殼、門護闆、立柱、座椅護闆、保險杠等。由于未添加阻燃劑前的PP的阻燃型較差,其極限氧指數 ( LOI) 僅為17. 8% ,發生事故後容易燃燒。目前,國内外對汽車阻燃用 PP 研究主要圍繞對聚丙烯基體進行改性,同時通過添加低毒、無鹵阻燃劑,開發具有優異力學性能和阻燃功效的聚丙烯複合材料,以滿足汽車零部件的阻燃需求。
目前,适用于聚丙烯的阻燃劑主要為添加型阻燃劑,應用較多的有鹵系阻燃劑 (常用的有溴系阻燃劑或溴-銻協效阻燃體系) 、無機填充型阻燃劑 (常用的有氫氧化鎂和氫氧化鋁) 、磷系 (三聚氰胺聚磷酸鹽、三聚氰胺磷酸鹽、聚磷酸铵、磷腈、磷酸酯等) 、氮系 ( MCA、APP、MPP 等) ,以及膨脹型阻燃劑( IFR) 。随着嚴苛的環保政策的施行,以及無鹵化推廣,高分子材料用阻燃劑無鹵化已是大勢所趨。
以聚丙烯為基體,以長玻纖維為填充材料,加入磷氮系無鹵膨脹型阻燃劑、三聚氰胺尿酸鹽、多聚膦酸密胺鹽制備得到長玻纖增強無鹵阻燃聚丙烯電池槽。制備過程中還采用了雙母粒制備法,通過分别制備長玻纖維長玻纖母粒和無鹵阻燃母粒,将兩者混合均勻後直接注塑制得阻燃PP制品。雙母粒制備法避免了長玻纖母粒制造過程中由于過度剪切引起的剪切區溫度過高引起阻燃劑降解和玻纖長度短引起的力學性能下降問題。
聚丙烯纖維/木纖維/麻纖維三元複合材料是一種常見的汽車内飾件材料。
阻燃PP無鹵化改性技術中,IFR因其對PP加工流動性,低密度優勢影響最小且優異的阻燃效率,以及用量少和低煙無毒等優點,被認為是無鹵阻燃PP中最優前景的發展方向之一。
阻燃PP在大陸起步較晚,但發展很快。特别是近年來增長迅猛的新能源汽車行業直接推動了阻燃PP需求量的快速增長,國内衆多高校、科研機構以及企業參與到車用零部件阻燃PP的開發中來。今後,車用阻燃PP的研究将重點聚焦于高效和環保,通過選擇無鹵阻燃劑、膨脹型阻燃劑、磷氮系阻燃劑以及複配型阻燃劑同時結合其他助劑,開發出性能優異的阻燃PP材料。
阻燃ABS
ABS是全球用量最大的家電用高分子材料,大陸約 80% 的ABS消費量是用于家電生産。ABS 由于具有很強的塑膠表面塗裝的耐久性和防腐性,是适合汽車塗裝的典型材料,也将其應用于汽車零部件的生産。由于ABS樹脂隻含有C、H、O三種元素,自身不具備阻燃性能,這使得ABS樹脂在高溫階段穩定性差,極易燃燒; 在點燃的過程中還伴有異味氣體和黑煙顆粒的産生,将其直接用于車用零部件存有安全隐患。是以在使用前必須對其進行阻燃性能、耐熱性能做改性處理。
鹵系阻燃劑的阻燃效率比較高,其中溴系阻燃效果又好于氯系,雖然有着環保方面的強大壓力,溴系阻燃劑依靠異常突出的阻燃效果和低廉的成本兩大優勢,對一些阻燃标準要求嚴格的領域和某些難于阻燃的材料,溴系阻燃劑還是最實際的選擇。電子電器産品中約有 70% 為溴系阻燃劑,其中十溴二苯乙烷主要用于ABS的阻燃。但環保無鹵化的推廣,也讓無鹵、磷氮系阻燃劑用于ABS 受到關注。
ABS與聚碳酸酯 (PC) 熔融共混可得到PC/ABS複合材料,該材料兼具ABS和 PC的優點,具有較高的熱變形溫度和穩定性,改善了加工性能。PC/ABS合金已成為目前産量最大、增速最快的樹脂合金,可用于汽車儀表盤、蓄電池組、汽車車身等其他零部件。PC樹脂本身是屬于阻燃自熄材料,UL94 為 V2級,但與 ABS 共混後,阻燃性能下降,是以在用于汽車零部件前需要進行阻燃改性。目前,針對 PC /ABS合金阻燃改性常用的阻燃劑有鹵系阻燃劑、磷系阻燃劑、以及納米阻燃劑等。
阻燃PC
聚碳酸酯 (PC) 作為五大工程塑膠之一,因其具有高強度、高抗沖以及耐熱等優點被應用于汽車零部件的生産。例如,汽車儀表闆、照明系統、加熱闆、除霜器及聚碳酸酯合金制的保險杠等。伴随着消費更新,新能源車及輕量化發展,國内對 PC 的需求也在不斷增長,2019 年全球PC産能增至640萬噸,中國占比 72% ,達到460萬噸,2015-2019 年全球産能年均增速 24. 8% 。PC 本身具有一定阻燃性,相較于其他普通高分子材料 ( 如 PE、PP 等) 擁有一定優越性,LOI 可到 21% ~ 24% ,UL94 為V2級。然而對汽車零部件阻燃要求相對較高的應用領域,其阻燃性能還是難以勝任,仍還需要對其進行阻燃改性。
溴系阻燃劑能明顯提高PC的阻燃性能,常用的有十溴二苯醚 ( DBDPO) 、四溴雙酚A (TBB-PA)等。但含溴的阻燃材料在高溫下容易分解産生腐蝕性氣體,生會使汽車零部件受損。此外,溴系阻燃劑的添加會嚴重影響 PC 的透明性,同時也不符合歐盟無鹵化、環保政策的要求。目前,工業化的 PC 産品中使用最多的磷系阻燃劑主要是 TPP ( 膦酸三苯酯) 、RDP ( 二苯基磷酸酯) 和 BDP。TPP 常溫下為固态,熱穩定性較差,在 PC 加工溫度下容易揮發,僅發揮氣相阻燃作用。RDP 和 BDP 常溫下為液體,具有較好的熱穩定性,可同時發揮氣相和固相阻燃作用,同時 BDP 與 PC 有較好的相容性,可起到增速硬化的作用,是以 PC+BDP 體系成為使用較多的一種體系,BDP添加比例 10%。
此外,含矽化合物作為新一代環保型阻燃劑,因其高效、低毒、無污染等特性,以及對PC加工性能和實體性能影響較小也逐漸受到關注,如聚矽烷、聚矽氧烷等。汽車零部件用PC在選用阻燃劑時也在向無鹵環保靠近,通過添加多種助劑或者制備複合型阻燃劑等途徑,提升PC的綜合性能。此外,PC通過與ABS、PBT 等組成複合材料也是提升PC加工性能和阻燃性能的不二選擇。
其他阻燃高分子材料
PP、PU、ABS和PC是目前主要應用于汽車零部件生産的阻燃高分子材料,此外,将兩種或以上高分子材料熔融共混制備的複合材料也是目前使用較多的一種 材 料,如 PC/ABS,PC/PBT,PC/FR複合材料等。Polymaker 公司,推出三款基于 PC 的3D 列印材料,将其用于車用零部件的生産,三款産品分别為Polymaker PC-ABS、Polymaker PC-PBT、PolyMaxPC-FR,這三款産品各有特色,在耐熱性、耐沖擊、易加工以及阻燃性能方面,均具有較好的表現。Polymaker PC-PBT 在科思創 Makroblend 系列産品基礎上進行改進,提升了材料綜合性能。同樣 PolyMaxPC-FR是在科思創 Makrolon 産品上對阻燃性能做了較大改進,使材料UL94 達到 V0 級,将該材料用于新能源汽車電池外殼。