Whether the road to industrialization and scale of HJT batteries is smooth, the key is still determined by its economy, that is, the LCOE indicators that we discussed before. LCOE emphasizes the whole life cycle, and the pursuit of lower LCOE comes from "cost reduction" on the one hand, and "efficiency improvement" on the other hand. The "cost reduction and efficiency improvement" path of HJT batteries can be summarized as "more efficient", "thinning", "de-banking", and "indium-free".
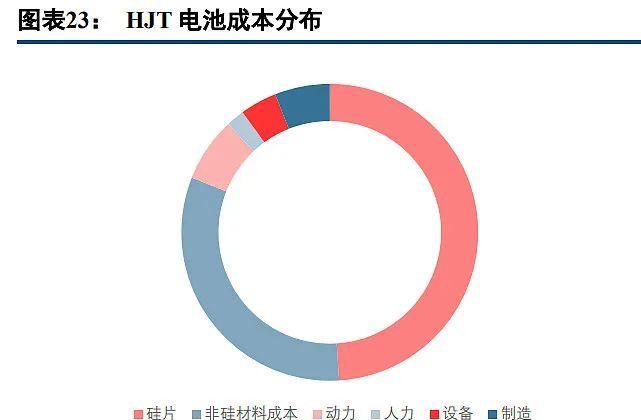
In the cost composition of HJT cells, silicon wafers account for nearly 50%; in the cost composition of non-silicon materials, silver paste and target materials account for more than 70% of the total. In 2021, due to the limited supply of upstream silicon materials and the fluctuation of commodity prices, the price of the photovoltaic industry chain showed a short-term abnormal state, and the study of the composition factors of battery costs was greatly disturbed. Excluding the above factors, in general, silicon wafers account for about 50% of the HJT cost structure. In terms of the cost composition of non-silicon materials, silver paste and target materials account for up to 59% and 14% respectively.
The cost of HJT batteries at the end of 2022 is estimated on the assumptions as follows:
Wafer price: Based on PV infoLink's end-of-2021 wafer price, assuming a 30% price reduction in 2022.
Wafer size: 182 WACs.
Wafer thickness: 165μm perC and 130μm HJT.
N-P Wafer Spread: Type N wafers are 8% more expensive than Type P.
Depreciation period: Costs are calculated at 5-year depreciation for more realistic reaction equipment iteration speeds.
HJT battery cost estimates at the end of 2022:
Wafer cost, 2022 HJT battery wafer cost of 0.37 yuan / W, PERC battery is limited by the high temperature process, its wafer thickness is limited space for further decline.
Non-silicon cost, HJT batteries mainly focus on cost reduction measures such as the decline in silver paste consumption, the localization of low-temperature silver paste, and the decline in equipment investment. The estimated non-silicon cost of HJT in 2022 is 0.42 yuan/W, which is 0.22 yuan/W higher than PERC+.
Total cost: 2022 HJT battery cost is expected to be 0.78 yuan / W, the cost of silicon wafers has been lower than PERC+, non-silicon cost is still higher than PERC+, further reduction is mainly through silver consumption decline (SMBB, silver-clad copper, copper plating gradually matured), low-temperature silver paste localization and so on.
Analysis of wafer thickness and silver paste consumption sensitivity: Under the premise that other assumptions remain unchanged, we made a sensitivity analysis between silicon wafer thickness and silver paste consumption. Based on 182 wafers:
When the thickness of the silicon wafer is reduced to 120μm and the silver paste consumption is still 190mg/piece, the cost of the HJT battery is reduced to 0.75 yuan/W, and the reduction is 0.03 yuan/W;
When the wafer thickness is reduced to 120μm and the silver paste consumption is reduced to 170mg/piece, the HJT battery cost is reduced to 0.73 yuan/W, a decrease of 0.05 yuan/W.
When the thickness of the wafer is maintained at 130μm and the silver paste consumption is reduced to 170mg/piece, the cost of the HJT battery is reduced to 0.76 yuan/piece, a decrease of 0.02 yuan/W.
We discussed the specific path of "cost reduction" and "efficiency improvement" of HJT batteries in 2022:
Cost reduction: In the 3 years from 2019 to 2021, the localization of HJT equipment has been relatively smooth, and it has dropped from the early imported equipment of 10+ billion yuan / GW to about 400 million yuan / GW of the current domestic equipment (some production lines have dropped to less than 400 million yuan / GW), and it is expected that the price of equipment in 2022 will be further optimized through scale and gradual localization of core components.
On the other hand, in the whole life cycle dimension, depreciation accounts for a large proportion of the unit cost of cells, and we believe that the device side has no longer become the core factor restricting the decision-making of new entrants in the industry. As far as 2022 is concerned, the "thinning" of silicon wafers, the exploration of the decline in silver pulp consumption in non-silicon costs is particularly important, becoming the main contradiction.
Efficiency improvement: As far as the HJT cell link is concerned, the more important observation window in 2022 is the smooth introduction of the "microcrystalline process" on the industrial mass production line. The microcrystallization process is already relatively mature in the laboratory, and if it can be successfully introduced into the industrial production process, it is expected that the effect of improving the efficiency of HJT's batteries will be very obvious. Combined with the continuous breakthrough of the "cost reduction" end, the road to large-scale industrialization of HJT batteries may become clearer.
2.2.2 Continue to reduce costs around "flakes" and "silver consumption reduction"
Flake process: HJT batteries are double-sided symmetrical structures, superimposed on their low-temperature process properties, which is more suitable for the thinning of silicon wafers in large-scale mass production. At present, the general thickness of N-type silicon wafers is 150μm, and the industry is expected to be thinned to 130μm in 2022 and further thinned to 120μm in 2023. According to calculations, every 20 μm thinning of the wafer can reduce the cost by 10%.
The idea of "reducing silver consumption" is divided into two types. One is to reduce the absolute value of the amount of silver paste, and reduce the use or loss of silver pulp in the metallization process as much as possible through process improvement, such as thinning the grid line and improving the aspect ratio. Another idea is to replace silver with base metals to achieve the purpose of reducing, and even not needing silver pulp in the future.
The implementation path corresponding to the first idea includes SMBB, screen graphic optimization, steel plate printing, laser transfer printing, etc.:
(1) SMBB cost reduction and efficiency improvement mainly comes from optimizing the current transmission path, the length of the fine gate between the main gates is shortened, which can effectively reduce the fine gate resistance, and the fine grid can become thinner; the number of main gates increases, significantly reducing the photogenerated current transmission path and reducing power loss. The thinning of the grid width and the use of the mesh-free mesh version can further reduce silver consumption. Taking 12BB as an example, it can reduce the silver paste consumption of HJT batteries to about 130mg.
(2) The industry is also actively exploring the realization of metallization in addition to traditional screen screen printing, with the purpose of improving the aspect ratio, such as improving the material of the existing screen, optimizing the screen graphics, laser transfer printing, etc. Laser transfer printing can achieve ultra-fine line width metal grid line contactless printing, its advantages mainly include reducing silver paste consumption, grid line width can be reduced to 18μm, saving 30% of the paste; reduce the shading area, the front fine grid thinning to reduce shading, improve electrical performance; reduce battery damage rate, because laser transfer for non-contact printing, hidden crack scratches and other issues have been solved.
The realization path corresponding to the second idea is to use base metals instead of traditional silver paste, including silver-clad copper, electroplated copper, etc.: HJT batteries are low-temperature processes, from this point of view, in the current battery technology, relatively speaking, it is relatively most suitable for the introduction of copper processes. From the gradual decline in the silver content of silver-clad copper to the electroplated copper process, the ultimate goal is to get rid of the use of silver.
(1) The new silver-clad copper paste has the potential to reduce the cost of HJT battery electrodes by 30%, and the silver-clad copper technology is expected to be introduced into the HJT battery mass production line in 2022.
(2) The electroplating copper process can realize the complete replacement of copper for silver, but at this stage, it is mainly subject to the fact that the process is not yet fully mature and the equipment investment is high, and it is expected that it will take 2 to 3 years of industrialization cultivation time, which is an important silver consumption reduction method after the silver-clad copper technology. In terms of laboratory performance, in September 2021, SunDrive and Maiwei Co., Ltd. used Maiwei's HJT equipment and SunDrive electroplating process to achieve a photoelectric conversion efficiency of 25.54% on full-size (M6) monocrystalline HJT batteries.
2.2.3 HJT batteries with microcrystalline structure will be industrially produced in 2022
HJT battery version 1.0 (that is, the current mass production), its intrinsic layer, P-doped layer, N-type doped layer are amorphous silicon. HJT version 2.0 is defined as the introduction of a microcrystallization process on the positive surface of HJT cells on the basis of version 1.0 to dope microcrystalline silicon oxide. Version 2.0 battery back surface remains unchanged.
Introducing a microcrystalline process on existing HJT cells will help increase conductivity, reduce pressure on the TCO layer, and improve its light transmittance: nanocrystalline silicon (nc-Si) and amorphous silicon (a-Si) are allotropes of silicon. Nanocrystalline silicon has small amorphous silicon grains, sometimes also known as microcrystalline silicon (μc-Si), the difference is mainly in the size of the grain particles. Microcrystalline silicon materials have a continuously adjustable band gap and a wide spectral response range, making them ideal for HJT cells. The advantages of hydrogenated microcrystalline silicon are high doping efficiency, high conductivity, large carrier mobility, etc., compared with hydrogenated amorphous silicon has a wider spectral response range, which can be extended to the infrared part.
HJT cells with microcrystalline structures are expected to be industrially produced in 2022. The 600MW HJT line for Diamond Glass is planned to use a microcrystalline process and the production facility will be entered in December 2021. In November 2021, CWAS and Maxion reached a cooperation on the joint development of a single-line production capacity of more than 500MW heterogeneous junction single-sided microcrystalline (target 25%, Huasheng Phase II) and a bifacial microcrystalline (target 25.5%, Huasheng Phase III) battery production line, the production line plans to use the single-sided microcrystalline and bifacial microcrystalline process developed by Huasheng and the large-capacity PECVD and PVD developed by Maxis, and the equipment is scheduled to be moved in in February 2022.
For PECVD equipment, the introduction of the microcrystalline process, the equipment also needs to be slightly modified. The high hydrogen dilution ratio of microcrystalline silicon causes its deposition rate to be slower and requires a VHF power supply. At the same time, due to the standing wave effect, the carrier board cannot be too large. (Source: Future Think Tank)