Introduction: In 2021, The application of China's metal 3D printing market has developed rapidly, and a number of enterprises have emerged, and their annual shipments of metal 3D printers exceed 50 units, or even up to 100 units. From the perspective of product and technology, in the past year, what breakthrough metal 3D printing technologies have emerged in China? Antarctic Bear 3D Printing Network rated the domestic heavyweight metal 3D printer in 2021 according to factors such as technical difficulty, innovation, and industry influence.
1. Qingyan Zhihuan breaks through the scanning technology of large-format metal 3D printing electron gun array
On November 30, 2021, Antarctic Bear learned that Tianjin Qingyan Zhishu Technology Co., Ltd. used the 2×2 electron gun array independently developed in China to complete the printing of titanium alloy parts with a diameter of 400mm, marking that China took the lead in realizing the scanning of large-format electron gun arrays in the world, laying a solid foundation for further realizing large-size electron beam selection melting (EBSM) technology.
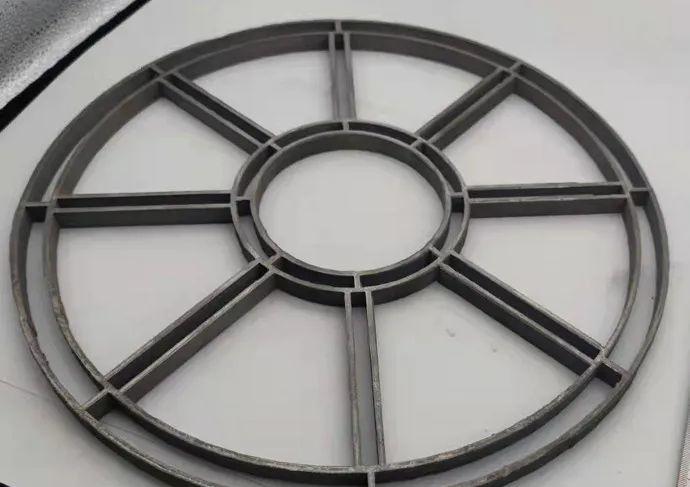
△ Titanium alloy parts prepared by electron gun array scanning (diameter 400mm)
Electron Beam Selective Melting (EBSM) is a powder bed melting additive manufacturing technology based on high-energy electron beams, which can be used for the processing and manufacturing of complex overall structures such as hollow, porous, and mesh, and realizes lightweight and high performance of product structure.
EBSM technology has the characteristics of high energy efficiency, high power, high powder bed temperature, low stress in the parts, etc., which can realize the additive manufacturing of high-performance, refractory materials such as titanium alloys, titanium aluminum alloys, high-temperature alloys, refractory metals, etc., and the forming efficiency is high, the cost is low, and it can meet the rapid response manufacturing needs of large-scale mass production and emergency state, and has been applied to the large-scale manufacturing of metal parts in the aerospace, medical equipment and other industries in Europe and the United States. However, the difficulty of EBSM equipment and process is relatively high, only a few countries have mastered it at present, and they are all single electron gun technology, with small forming format and limited size of formed parts, which is difficult to meet the needs of aerospace large-scale component manufacturing.
During the 13th Five-Year Plan period, Tianjin Qingyan Zhishu Technology Co., Ltd. cooperated with Tsinghua University, the Institute of Electrical Engineering of the Chinese Academy of Sciences and other units to undertake the project of "High Power, Long Life, Multi-mode Electron Gun and Array R&D and Additive Manufacturing Application" of the Key R&D Program of Additive Manufacturing and Laser Manufacturing of the Ministry of Science and Technology. With the support of the project, it has broken through the design and manufacturing technology of domestic long-life and high-stability electronic guns, and successfully developed a large-format EBSM research and verification prototype equipped with 2×2 electron gun arrays, which solved technical problems such as inter-gun interference, scanning splicing, and multi-gun integration. After the hard work of the project team, the EBSM of large-size titanium alloy parts based on the electron gun array was realized for the first time in the world, which made China come to the forefront of the world in this field.
△Large format EBSM research verification prototype equipped with 2×2 electron gun array (scanning size 430mm×430mm)
The breakthrough of electron gun array technology not only means that China has made key technological progress in large-size EBSM additive manufacturing technology, but also shows that China has fully mastered EBSM technology, especially the high-precision, high-reliability electronic gun system relied on by EBSM industrial applications to achieve independent controllability, which provides a guarantee for the industrial application of EBSM, an efficient and high-performance additive manufacturing technology in China.
The lead unit of this project, Tianjin Qingyan Zhishu Technology Co., Ltd., independently developed the cathode life of the 3kW single crystal cathode electron gun has reached more than 800 hours, reaching the level of similar products in the world. At the same time, in order to ensure the scanning of the electronic gun array, the company has also developed functions such as electronic gun status monitoring, electronic gun self-diagnosis and self-recovery, and real-time correction of processing parameters to ensure the stable operation of the multi-gun complex system.
2. Brilliant launched the 10 laser metal 3D printer S800, entering the era of large production
Antarctic Bear learned that at the 2021 Asia 3D Printing and Additive Manufacturing Exhibition (TCT Asia), the metal 3D printing listed company Polarite launched the 10 laser metal 3D printer BLT-S800.
△BLT-S80
BLT-S800 is a new product released by The exhibition, the scene is displayed is ten laser equipment, its application areas include aviation, aerospace, engine, medical, automotive, electronics, molds, research institutes, materials support titanium alloys, aluminum alloys, superalloys, stainless steel, high-strength steel, mold steel, the forming size is 800mmX800mX600mm. The biggest feature of BLT-S800 is the large size and efficient forming ability, which can be equipped with 6/8/10 three multi-laser schemes, which is an automated and intelligent masterpiece.
It is born according to the application needs of parts
Rotary body parts are more common and important parts structure types in aerospace engine applications, the general size is within Φ800mm, the finished parts not only need to achieve high precision, performance and quality standards, affected by the development and manufacturing rhythm, the production of this type of parts needs a high production efficiency guarantee.
The forming size of BLT-S800 breaks through to 800mm×800mm×600mm, which can meet the forming requirements of large-size parts to a greater extent, and solve the integration of complex structures such as large-scale special-scale space surface features, multi-feature cross-scale structures, hollowed-out mesh and spatial continuous topological envelope in high-end application fields.
Ten laser advanced technology, multi-optical splicing quality is stable
Multiple high-quality fiber lasers are linked to collaborative printing, and the efficiency of 10-optical equipment can be increased by more than 30% compared with 6-light equipment, which greatly improves the printing efficiency. At the same time, the equipment adopts two-way powder laying technology to reduce the invalid time of one-way powder laying and improve the printing efficiency of parts. Under the premise of ensuring the quality of parts, the maximum printing efficiency of the equipment can reach 250cm3/h (related to the shape, size, material and parameters of the parts, and related to the number of lasers in the equipment).
Polarite has advanced multi-optical splicing technology to ensure the consistency and stability of the energy input and mechanical properties of the material in different batches and different forming areas.
Polarite adopts a self-developed power correction system, so that the laser power output is stable and consistent to an accuracy of ±5W. With a mature flow field design, it effectively ensures the thickness of the powder layer and takes away a large number of large particles produced by sintering, improving the surface quality of parts, reducing defects, and making the full-format forming effect better and more stable.
Polarite has integrated and optimized key technologies such as multi-optical splicing, so that the deviation of various mechanical properties (tensile strength, yield strength, elongation and cross-section shrinkage) between the lap area and the non-lap area on the print format is controlled within 5%.
"Ultra-long standby" filter, stable production
BLT-S800 equipment is equipped with a permanent sintered plate filter as standard, which realizes the "ultra-long standby" of the filtration system, greatly reduces the cost of equipment consumables and labor costs, and improves the utilization rate of equipment. In addition, the internal wind speed of the equipment is monitored in real time and the closed-loop control is adopted to make the blowing more stable.
Automatic powder supply does not stop, to ensure quality
The automatic powder supply system is used in stainless steel, mold steel, titanium alloy, super alloy and aluminum alloy and other powder powder supply. The whole powder supply system operates under the protection of inert gas, and the real-time detection of oxygen content, pressure, differential pressure of the filter element, level detection and so on can realize the automatic addition of equipment powder, uninterrupted production process, and ensure the forming quality of parts with process control. The powder supply system is highly compatible in design, allowing one or more powder supply systems to serve one or more BLT metal additive devices of the same or different models.
With years of production experience, intelligent software escorts the quality of parts
Before the light scanning, BLT-MCS calculates the actual height of the part print according to the actual position of the grating ruler feedback of the working platform, and compares it with the theoretical height of the split file, if the error exceeds the quality requirements, it is prompted that the software automatic compensation or shutdown inspection is required. Avoid the loss of part height caused by uncontrollable factors and improve the success rate of printing once.
Polarite has many years of printing experience and has accumulated a large amount of powder laying defect data. In the monitoring process, the monitoring system will classify the typical powder laying defects found: such as powder lack of powder, scraper stuck, powder scraping, powder shaking powder, more powder impurities, collapse of small areas of the platform and other image features, and then extract database data through the network for comparison and introduce the algorithm of the neural network after multiple rounds of iteration to form a repair scheme.
3. Sidymour 2 meter large size metal 3D printer XDM 2000
△XDM 2000
Suzhou Sidmo released the ultra-large laser selection melting equipment XDM 2000 at the 2021 TCT exhibition, which uses 6 sets of galvanometer systems, metal 3D printing table forming size of 2000mm×2000mm, which is one of the largest models in the same category.
Mobile scanning system
The equipment adopts a single column 6 sets of galvanometers 6 stations of parallel mobile scanning scheme, the specific implementation method is: the 2000mm × 2000mm processing table is divided into 6 × 6 areas of equal size, a single column of 6 areas distributed 6 sets of galvanometer system, at the beginning of the processing 6 sets of galvanometers at the same time, the current station scanning after the completion of the movement of the galvanometer platform to the next station, and then 6 sets of galvanometer synchronous scanning, in turn to complete the processing of 6 stations after the end of the layer scanning, waiting for the completion of the powder laying and then enter the next cycle, Until the end of the entire part. In this way, six sets of parallel synchronous scanning methods can achieve efficient processing and greatly reduce costs.
Mobile soot treatment device to make "big" small
The product is designed with a mobile smoking blowing device, the device moves synchronously with the position of the galvanometer, as shown in the following figure, the blowing smoking device is the same as the laser galvanometer, with six stations in the process of moving, so 6 pipe interfaces are designed on both sides of the molding chamber, for the gas convection of each station for blowing and smoking, when the blowing smoking device moves to this position, the electromagnet at the pipe interface starts to combine the blowing smoking pipe to form a circulating gas convection environment, and then the laser galvanometer begins to scan, The soot generated during processing can be effectively treated in such a gas convection environment. The 2000mm span soot treatment problem is translated into a 350mm span.
4. Huashu Hi-Tech 8 laser metal printer FS721M, the printing efficiency is innovative
With the in-depth development of 3D printing technology to industrial applications, additive manufacturing is developing in the direction of multi-laser, large size, high efficiency and low cost, which brings many new challenges in print quality, stability and consistency. Based on the customization of the individual needs of industrialization users in the automotive industry, Huashu Hi-Tech, an industrial-grade 3D printing leader, took the lead in releasing the 8 laser metal additive manufacturing technology and the FS721M equipment equipped with 8 lasers in May 2021, and demonstrated its sintering process on the spot for 3 consecutive days at TCT Asia 2021.
At present, the molding efficiency of the international first-line brand large equipment is about 200-250ml/h, Huashu Hi-Tech 8 laser FS721M is equipped with 8 1000W lasers, combined with large layer thickness process, 8 laser FS721M forming rate up to 250-300ml/h, setting a new height for metal 3D printing efficiency. FS721M has 720×420×420mm large-size molding cylinders, which can meet the needs of large-size, complex structure, industrialized additive manufacturing, and the molding materials include titanium alloys, nickel-based superalloys, aluminum alloys, stainless steel, etc. At the same time, the FS721M is equipped with an efficient powder handling system protected by inert gas and a circulating filtration system, which ensures molding quality through intelligent slicing algorithms and unique wind field design and multi-laser collaborative scanning.
△8 Laser FS721M forming rate up to 250-300ml/h
Although the cost of the laser has increased, because of the improvement of printing efficiency, the overall printing cost of the user has been reduced, which has won the user's recognition. As of December 2021, Huashu Hi-Tech 3D printing equipment has installed more than 600 sets of global clients, including more than 80 sets of medium and large metal equipment with a size of more than 400mm, with continuous innovation and excellent product strength, Huashu Hi-Tech continues to lead the industrial 3D printing market.
Self-developed software supports in-depth development and functional customization
Huashu Hi-Tech independently developed additive manufacturing integrated open source software operating system, set manufacturing and fault diagnosis temperature field control, remote monitoring, data feedback and integrated control and other functions in one, is the additive manufacturing of multiple module functions integrated into one of the system control software, but also with open source characteristics of the 3D printing software system, breaking through the European and American additive manufacturing enterprises original closed software technical limitations, become an open software platform in the field.
At present, Huashu Hi-Tech has a full range of additive manufacturing systems, which open up multiple types of core key technical parameters, and support users in in-depth development and functional customization:
● Laser parameters (such as laser power, laser spot, etc.)
● Path planning parameters (e.g. stripe partitioning, upper and lower surface partitioning strategies, etc.)
● Motion control parameters (such as powder laying speed, coating thickness, etc.)
● Size calibration parameters
● Support design parameters
Get the best workpiece quality and performance through the best matching of equipment and materials, while being compatible with third-party software such as Siemens NX software, Netfabb, etc.
Comprehensive real-time monitoring system escort
In the printing process, the metal powder melting process is quite complex and challenging, and the phase change of the metal, the cooling rate and other process parameters will affect the melting process and microstructure of the metal powder. FS721M is equipped with a comprehensive real-time monitoring system, which can carry out powder testing, alarm processing, quality traceability, can grasp the molding situation after each layer of laser scanning in real time, and carry out each layer of powder testing and intelligent processing, quality traceability, effectively ensure the high output value and high yield of the equipment, and escort the stable operation of the equipment.
△ Lightweight wing rudder
Product size :665*55*252mm
Printing equipment: FS721M
Print material: FS IN718
Application: Aerospace
The use of dot matrix, honeycomb, grid skeleton skin integration, internal dot matrix filling, product weight reduction of 60%. At the same time, shorten the cycle, reduce costs, and improve the comprehensive performance by 20%.
5. Yijia three-dimensional EP-M650 series products · Four-laser large-size metal additive manufacturing system
Antarctic Bear learned that ep-M650 series products use MMBF metal powder bed melting technology, equipped with four laser quadrellers, multi-laser precision positioning + splicing area precision control technology to ensure the high quality, high efficiency and high stability of the equipment printing, of which the basic equipment configuration of the molding chamber size up to 655 * 655 * 800mm3. It can realize the printing of titanium alloys, aluminum alloys, nickel-based superalloys, die steel, stainless steel, cobalt, chromium, molybdenum and other materials, and is suitable for the direct manufacture of large-size, high-precision and high-performance parts in the fields of aviation, aerospace, and military.
EP-M650 was incubated in the national key R&D program "Additive Manufacturing and Laser Manufacturing Special Project" - "Large-size Powder Bed Selection Laser Melting Additive Manufacturing Process and Equipment Research and Development" project (Beijing Yijia 3D Technology Co., Ltd. is the lead unit of the project). At present, the equipment has been mass-produced, officially put into service and serve the market.
In the process of equipment research and development, Yijia 3D has overcome the common technical difficulties of a number of large-scale additive manufacturing equipment, including beam quality control, multi-laser splicing accuracy control, cyclic wind field homogenization, cyclic filtration system stability optimization, multi-laser path planning, online quality inspection and other key technologies, and developed a series of common platform equipment through technology extension. According to customer needs, the dimensions of the molding height direction of this series of equipment can be customized, up to 2000mm.
High efficiency, high production capacity
Basic EP-M650 molding chamber size 655*655*800mm3, volume >340L; Equipped with four lasers, the molding speed can reach up to 120cm3/h, which is 3.5 times higher than that of a single laser printing, and it can achieve large layer thickness printing (≥60μm), further increasing production capacity.
Stable quality and good consistency
Excellent high beam quality (M2≤1.1) and detail resolution ensure the molding accuracy and mechanical properties of printed parts; the accuracy deviation of the printing splicing area is ≤±0.1mm, and the consistency of mechanical properties is no obvious difference from that of a single laser; the wind field structure is optimized to ensure the effective removal of smoke and splashes, and the printing of full-format parts is uniform and consistent.
Humanized design, high degree of automation
User-friendly interface, with one-click printing function; after printing, you can control the software "one piece of pickup", the molding cylinder is automatically moved out, side slid to the powder cleaning module; the equipment information during the printing process is displayed in real time, and the electronic printing report is automatically generated after printing.
Real-time monitoring, high security
Safety design, anti-misoperation, anti-electric shock, fire prevention, anti-pollution; the overall sealing of the equipment is good, powder use and recycling are in a closed state; real-time monitoring of the working environment and air supply status, safe and reliable.
Adhering to the concept of "technology-driven development", Yijia 3D has been deeply cultivating in the field of additive manufacturing, pragmatic and innovative, providing more professional, more reliable and more suitable manufacturing-grade 3D printing equipment for industrial production, and helping the manufacturing industry to upgrade with practical actions.
6. Tianjin Leiming 1.5 meters high size metal 3D printer LiM-X650H
Tianjin Leiming LiM-X650H was successfully developed in June 2021, the size of the printable parts is 650mmx650mmx1500mm, which is the international leading level, especially the printing depth, which is one of the highest levels of metal additive manufacturing equipment that can be commercially sold; the equipment is equipped with a complete closed-loop powder automatic conveying system, the parts printing process without manual intervention in the powder loading and unloading and screening process, equipped with parts powder cleaning and recovery module, efficient, practical and safe.
Laser's LiM-X650H equipment is equipped with 4 sets of 1000W lasers, up to 8 sets, with optimized process parameters, the molding efficiency is greatly improved; the optical system adopts high-quality digital scanning galvanometer and f-theta mirror, the scanning accuracy is high and the operation is stable; the sintered plate filtration system is adopted, the filter life is long, the printing process is not interrupted, avoiding the downtime caused by the replacement of the filter element or filter core cleaning, and improving the safety; in addition, The unique powder laying system provides high-quality powder layers for the printing process, the switchable powder conveying system provides basic functions for convenient production, the interesting screening mechanism provides reliable guarantee for the ultra-long printing process, and the 10L/min conveying efficiency provides sufficient raw materials for high-speed printing.
LiM-X650H series equipment can be widely used in aviation, aerospace, automobile manufacturing and other fields, has titanium alloy, superalloy, aluminum alloy and other materials mature printing parameter package, the equipment in the forming efficiency, printing quality, use costs and other aspects have excellent performance, has successfully printed a height of 1400mm for an aerospace customer parts, recognized by customers.
7. Wuhan Tianyu's new generation of intelligent casting forging and milling short process green composite manufacturing machine tools were completed and put into operation
On July 1, 2021, Antarctic Bear learned that Wuhan Tianyu Intelligent Manufacturing Co., Ltd., which is determined to "make key breakthroughs in high-end fields and transform and upgrade traditional industries", has completed and put into operation the "new generation of intelligent casting, forging and milling short-process green composite manufacturing machine tools" (TY4000L). The machine tool is facing the urgent needs of high-quality short-process manufacturing of national high-end equipment, combining metal additive-isomaterial-subtractive material into one, integrating Wuhan Tianyu's experience in design, materials, processes, software, core devices and product composite manufacturing, integrating domestic CNC machine tool host, NUMERICAL control system, functional components and universal micro-casting and forging system, with completely independent intellectual property rights, is the core technology of Wuhan Tianyu - "metal 3D 'micro-casting and forging' technology" The fourth generation of industrial application of large-scale full rigid inert atmosphere protection rapid manufacturing equipment.
The fully enclosed atmosphere environment is formed in a larger size
The effective forming size of TY4000L is 3m×2m×2m, which is more than 6 times larger than the previous version.
Functional integration is more intelligent
TY4000L will be micro-casting forging and milling system, online monitoring system, feedback repair system, atmosphere protection system fully modular for central control, compared with the previous version, feedback adjustment response efficiency is higher, equipment operation is more stable.
Wider product coverage
TY4000L is equipped with a complex forming casting forging head for the first time, which can realize the free switching of arc/plasma arc dual heat source double wire in a closed environment, and the multi-process seamless connection, while ensuring the quality of the forming, the efficiency is greatly improved, covering more special materials and complex features of high-end forging manufacturing needs.
Tianyu Intelligent Manufacturing Chief Scientist, Huazhong University of Science and Technology Professor Zhang Haiou team dedicated to more than 20 years of invention of multi-field regulatory laser / arc micro-casting forging and milling integration intelligent manufacturing high-performance large-scale metal component technology (referred to as "intelligent micro-casting forging" technology), broke through the "casting and forging synchronization, control control, defect monitoring, independent repair" and other problems, the integration of 3D printing, semi-solid fast forging, flexible robot three major technologies, the metal additive - equal material - subtractive manufacturing into one, can be used to manufacture forging-grade parts with one equipment, There is no need for heavy equipment and giant molds and more than 20 repeated heating and forming processes.
This technology comprehensively improves the strength, toughness, fatigue life and reliability of the parts, changes the traditional manufacturing mode of casting and forging separation at home and abroad, belongs to the subversive innovation and leading the international advanced manufacturing technology, and has made major breakthroughs in the key technologies and processes of low-cost, high-efficiency forming of high-performance large-scale complex parts, and has both the complex structure, moldless, lightweight advantages of additive manufacturing and the high quality of traditional forging parts. Product performance has been tested and certified by authoritative institutions and fully affirmed by users: The international 3D printing authoritative white paper Wohlers Report evaluated "invented a novel casting, forging and milling composite additive manufacturing technology"; the international arc forming pioneer Cranfield University evaluated "in situ rolling to improve microstructure performance, morphology, stress, deformation"; the application unit believes that "the manufacturing cycle is only 1/3 of the traditional way, and the performance exceeds the forging"; the results are identified as "the overall technology is at the international leading level".
8. Sublimation three-dimensional breakthrough of large-size refractory metal 3D printing technology
△ Tungsten alloy shielding
Powder Extrusion Printing (PEP) is a new 3D printing method proposed by sublimation three-dimensional, combining "3D printing" and "powder metallurgy". The first step is to control the material molding, form the raw blank of the complex refractory metal structure at low temperature (300 °C), and then sinter it at high temperature to finally achieve high-performance product preparation with large size (500mm*500mm*600mm), uniform composition and complex structure.
Based on powder extrusion printing technology, Sublimation 3D independently developed a large-size independent double nozzle indirect 3D printer UPS-556, with large format printing size, effective printing size up to 500mm×500mm×600mm, through the independent double nozzle design, can print dual materials at the same time, with automatic feeding function, can achieve continuous uninterrupted printing for more than 72h. The UPS-556 offers simple operation, high precision, high quality and cost performance.
△UPS-556
For high specific gravity tungsten alloys, due to the variety of compositions, large differences in performance, the highest difference in melting point of 2400 °C, and the saturation vapor pressure of each element is different, the use of SLM technology can not ensure the controllability and accuracy of each alloy composition. The PEP technology, through the low temperature section forming, high temperature section into the way, so as to effectively solve this problem.
Sublimation 3D, together with Central South University and Tianjin University, developed a suitable printing process using UPS-556, and successfully prepared a high-density 99.1±0.2%, tensile strength of 801MPa, and elongation of 22.1% of high-specific gravity tungsten alloy (96W-2.7Ni-1.3Fe). After heat treatment, the performance is further improved, the tensile strength is 838MPa, and the elongation reaches 26.1%. For refractory metal materials, PEP technology is a new 3D printing method.
Antarctic Bear learned that Sublimation Three-dimensional is also developing an oversized metal/ceramic indirect 3D printer with a print size of 1m*1m*1m or more.
9. Raise3D Shanghai Fuzhi launched FFF desktop-level metal 3D printing equipment
At TCT Asia 2021, Rise3D Shanghai Fuzhi announced that it will launch MetalFuse, a 3D printing solution that includes desktop-grade metal. This end-to-end solution provides a fully integrated ecosystem for metal 3D printing, including desktop 3D printers for metal FDM/FFF, catalytic degreasing furnaces, sintering furnaces, metal fuse manufacturing optimization software, and a metal wire portfolio from BASF Forward AM.
Dr. Chen Li (right), Director of Business Management and Operations for BASF's 3D Printing Solutions Asia Pacific region, and Mr. Mai Wei, Technical Director of Radio3D (left), jointly unveiled the MetalFuse metal 3D printing system
Raise3D MetalFuse is mainly for metal prototyping, compared with SLM/PBF technology, its entry barrier and difficulty of use are greatly reduced, customers with low frequency of use can purchase printers, and use outsourcing methods for degreasing and sintering processing. At the same time, compared with other metal printing processes, what you see is what you get, which can effectively solve the problem of slow development cycle and high development cost in the metal processing, mold and powder metallurgy industries.
△ Metal parts printed with Forge1
Raise3D's innovation also lies in a different way, not using the solvent degreasing process used by two other desktop metal 3D printing companies, Desktop Metal and Markforged, but combining 3D printing and the gas-catalytic degreasing process of the traditional MIM industry to greatly improve the yield of the final part, compared with the previous generation of solvent degreasing, MetalFuse shortened the molding time by 60% and increased the metal density to 97%.
10. Yunyao Shenwei (Jiangsu) independent innovation technology micron-level metal 3D printer Precision-100
△Precision-100
The micron-level metal additive manufacturing technology independently developed by Yunyao Shenwei expert team realizes the 3D one-time printing molding of complex precision structure metal materials, controls the laser spot to 20 microns, and the flattening layer is as thick as 5 microns (equivalent to 1 hair thickness of 20), realizes the metal printing accuracy to 2-5 microns, and the surface roughness of the printed parts Ra value is 0.8-1 microns, and is committed to filling the market gap of small, high-precision additive manufacturing parts, and its main advantages are as follows:
- Ultra-high precision: micron-level printing realizes metal printing accuracy to 2-5 microns, which can make the design of products more free, break through design limitations, and realize micron-level porous, hollow, hinged, multi-dimensional accompanying runners and other precision structures;
- Smooth surface: micron-level printing reduces the maximum height of the contour to between 5 and 10 microns, and the Ra value is 0.8-1 micron, which can reduce a large number of post-processing links;
- Supportless printing: micron-level 3D printing can achieve most structures above 10 degrees angle without support, free printing;
Micron-level metal printing technology is suitable for the current traditional precision manufacturing in the manufacturing cycle, manufacturing difficulties, multi-process parts manufacturing costs, molding complexity, design freedom and other aspects of the difficult parts manufacturing.
Key application areas include:
- Aerospace
In the Yunyao Deep Dimensional Micro 100 series, it has successfully molded nickel-based superalloy aero engine components with high surface finish and internal complex structure, which greatly improves its performance and effect;
- Medical field
Can directly form minimally invasive surgical instruments / surgical consumables / surgical robot joints, quickly manufacture personalized implants / interventions;
-In the field of microelectronics
Print a closed complex microstructure runner system in the heat dissipation parts to realize the complex parts that cannot be processed by traditional processes, and greatly improve the heat dissipation performance of the product;
- Precision mold field
Rapid manufacturing of micron-level electronic connector molds, and can realize the precision mold into the multi-dimensional conformal cooling flow channel, improve cooling efficiency, prolong the service life of equipment and increase equipment productivity.
summary
The above are some of the blockbuster products released by domestic metal 3D printing manufacturers in 2021, from electron beam EBM, SLM selective laser sintering, FFF melt extrusion, micro-nano metal printing and other different technical processes, which are very representative of the industry breakthrough technology equipment. Some manufacturers have made more advanced machines (such as the SLM metal 3D printer with 20 lasers), but due to lack of maturity, customer confidentiality requirements and other reasons, I hope that Antarctic Bear will not publish the exposure first, and will be grandly launched in 2022. Stay tuned.
If there are other unique metal 3D printers, please feel free to add them in the message area.
Antarctic bear year-end hot article
"More than 60 billion yuan: 2021 global 3D printing investment and financing report"
"Summary: Top Ten Applications of Global 3D Printing Cars in 2021"
"Summary: 16 3D Printing Industry Reports in 2021"
"This Year: Antarctic Bear's 3D Printing Conjectures Are Wrong 3, Right 6"
"China's 3D printing pattern is undecided, they are all dark horses"
"Total investment of more than 5 billion yuan, 2021 China's 3D printing major industrialization project construction"
"Entry-level metal 3D printers are on the rise"
"High Energy Review of 2021 Highly Innovative 3D Printing Startups"