What is it like for a media person to walk onto a car production line? A set of MAFACT production and operation management system can actually make the process engineers incarnated by media people change from "fighting for each other" to "collaborative production", and the efficiency will increase several times in an instant? In fact, such an interesting and magical scene occurred in the High-end Intelligent Manufacturing Base of Magna in Beiqi Blue Valley.
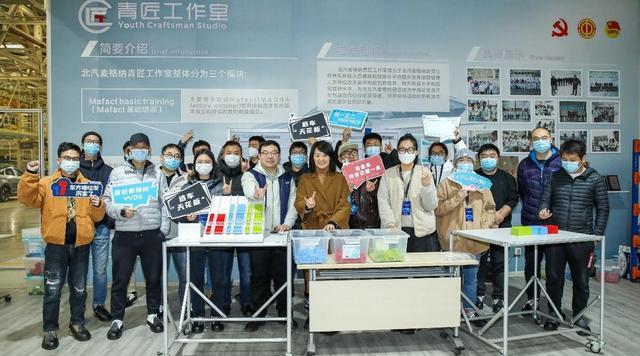
On December 23rd, at the OPEN DAY of Jihu Jizhi Factory, many media came to this high-end intelligent manufacturing base known as "Oriental Graz" as "process engineers" competitors, visited the intelligent workshop production line, learned about the world's super-first-class MAFACT production system, and experienced Magna's world-leading manufacturing process and management system at zero distance in an immersive experience, and the mystery behind the high quality of Jihu Auto was solved.
Integration of international luxury car manufacturing standards Magna top management system blessing
When magna is mentioned, people who follow cars will understand that it is a diversified global auto parts supplier with more than 100 years of experience and history in high-end automobile manufacturing, and its plant in Graz, Austria, has produced more than 3.7 million cars so far, including top luxury cars such as Mercedes-Benz G-Class and Aston Martin Rapide.
In December 2019, the Beiqi Blue Valley Magna high-end intelligent manufacturing base was completed, and Magna opened a vehicle manufacturing plant outside Europe for the first time, which is also the first Magna joint venture high-end intelligent manufacturing base in Asia. Beiqi Blue Valley Magna high-end intelligent manufacturing base fully introduced Magna MAFACT production and operation management system, with first-line luxury vehicles of the same level of world-class manufacturing standards, bringing comprehensive and reliable high-end quality assurance.
Automated production lines are standard with highly sophisticated operations in one step
In the digital era, automated production has become inevitable. In the high-end intelligent manufacturing base of Magna in Beiqi Blue Valley, whether it is a stamping workshop, a body workshop, a painting workshop, a final assembly workshop or a battery PACK workshop, you can see the busy figure of automated production lines and robotic arms everywhere.
The fully enclosed, high-speed automated production line of the stamping workshop is mainly responsible for the production of large and medium-sized stamping parts of the body such as side walls, fenders, and door covers. According to the stamping process engineer Zhou Fang, the stamping workshop has a total of 40 self-made parts (including 15 aluminum parts), according to the MAFACT system standards, from the material to the final product, from the appliance to the equipment, a full range of in-depth control, a pass rate of 97%, and most of the main engine factories Of this indicator is about 90%.
In the body workshop, Beiqi Blue Valley Magna high-end intelligent manufacturing base has the first 30JPH steel and aluminum hybrid production line in China, which is a fully automated production line composed of 290 German KUKA robots and 206 sets of connected equipment. Germany's KUKA Robot is known as the first of the four major families of robots in the world, which can achieve high-precision positioning at the millimeter level and the highest control accuracy in its peers.
In addition, in the painting workshop, 52 ABB high-performance robots form a fully automatic conveying system, and after multiple coating processes, the LASD water-based damping coating prepared by adding the appropriate amount of polymer resin to the appropriate amount of filler and auxiliary materials will be automatically sprayed to the body.
In the battery PACK workshop, the automatic rate of the whole line has also reached 53%, including automatic on-line of the module, automatic detection, gluing, cleaning, and module installation, fixing, FDS riveting process and so on. Zhu Juncheng, battery PACK process engineer, said: "Through high automation, the precision, consistency and higher production efficiency of the overall process are guaranteed, and the battery safety is more secure. It is understood that after the precision production, the power battery used by Jihu must be verified by more than 200 tests, and the coverage and strength are much higher than the national standard requirements. For example, the national standard humidity and heat cycle test cycle is only 3 days, and Jihu Automobile should do a high temperature and high humidity cycle test equivalent for more than 10 years and more than 3 months, and an alternating test under full-use temperature conditions for more than 8 months to ensure that the power battery system adapts to the use scenarios in the environment across the country.
Production standards exceed the industry level and hard-core quality to withstand the ultimate test
Magna MAFACT production and operation management system sets standards, automated production lines to ensure product accuracy and production efficiency, coupled with Jihu Automobile's excellence in the whole process of material selection, manufacturing and testing, there are a number of "ceiling-level" product performance. Whether it is the "China Top Ten Body" and "Best Material" double material award, or CA-CAP's first batch of corrosion resistance evaluation platinum grade, Jihu Automobile's product power halo is becoming more and more dazzling.
In order to achieve better body lightweighting, Jihu Automobile uses a hybrid body of upper steel and lower aluminum, and the manufacturing process of this hybrid body is more complex than that of all-aluminum body and requires more advanced technology. For example, more mechanical connection methods such as SPR and FDS are used in the connection, and the problem of contact corrosion needs to be taken into account; the method of pickling passivation before welding or preset coating by material suppliers is used to solve the problem of dense oxide film with high hardness on the surface of aluminum alloy.
The mixed body of aluminum under the upper steel is composed of a cage frame structure surrounded by high-strength steel, and in the most critical A-pillar and B-pillar parts of the cage structure, the pole fox adopts hot-formed steel of more than 1500MPa. According to engineers, this thermoformed steel is mostly used in tanks, submarines and space shuttles, and can withstand more than 10 tons of pressure per square centimeter, equivalent to the weight of two adult elephants. According to reports, the torsional stiffness of the new generation of intelligent luxury pure electric sedan Alpha S vehicle reached 63,000Nm/deg, reaching the industry ceiling level, and the all-terrain performance pure electric SUV Alpha T vehicle torsional stiffness reached 50,000Nm/deg, even higher than the Rolls-Royce Phantom.
In terms of wading depth, the industry standard of the sedan is 300mm, and the polar fox can still reach the excellent level of wading test at 800mm, which not only ensures the safety of the cockpit occupants, but also effectively avoids the risk of accidents caused by battery water. In addition, in the fully transparent shower room in the workshop, Jihu Automobile can easily pass the simulated mid-rain, heavy rain and even heavy rain and other vehicle all-round no dead angle flushing test, and the airtightness of the whole vehicle reaches 58SCFM, far exceeding the industry standard.
It is worth mentioning that all models of Jihu Automobile will be put into production at the High-end Intelligent Manufacturing Base of Beiqi Blue Valley Magna, including the high-profile Alpha S new HI version of the world's first high-end intelligent driving mass production car that supports urban roads. In addition, the new car has been delivered internally at the Baiqi Blue Valley Magna High-end Intelligent Manufacturing Base on December 20, and this delivery will be for the core members of the project team of Huawei and BAIC 1873 Davidson Laboratory who have paid the deposit, and will be delivered in small quantities. "The first-of-its-kind test experience with internal employees will further ensure reliability and user experience when the product is delivered to market." Wang Qiufeng, deputy general manager of BAIC BJEV and vice president of Jihu Automobile, said.
With the blessing of Magna's leading production system, the help of automated production lines, and production standards far beyond the industry level, Jihu Automobile has cultivated excellent quality and strength, in the tide of new energy automobile industry development, Jihu Automobile will promote China's new energy automobile industry to achieve upward breakthroughs and enhance the global competitiveness of "China's intelligent manufacturing".