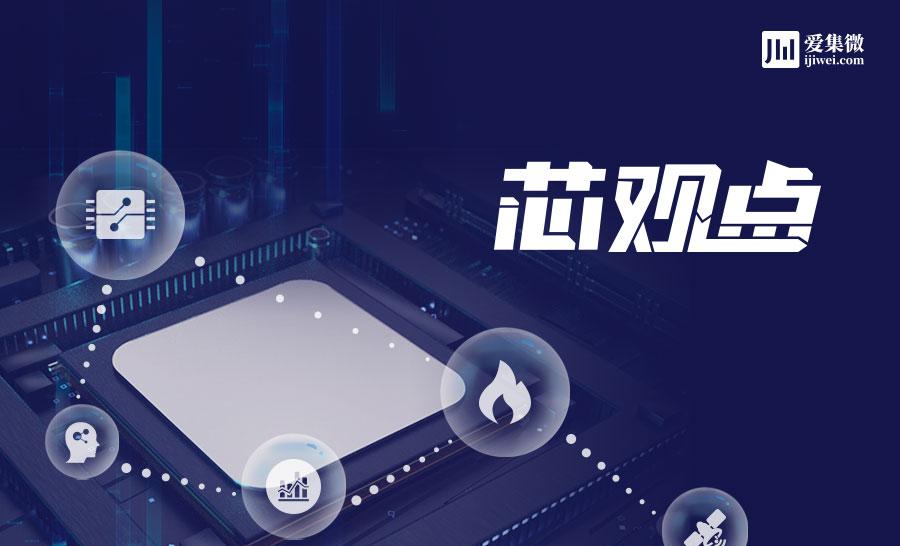
Core view - focus on major events in the industry at home and abroad, gather the views of Chinese and foreign celebrities and experts, analyze the development of the industry, and take you to understand the future trend!
After the end of the first quarter of 2022, the global chip shortage crisis has not yet shown signs and signs of significant alleviation, and the continuously lengthened delivery time of equipment in the front and back roads reminds major players in the global semiconductor market to monitor their inventory and upstream and downstream connectivity at all times. In this context, the issue of the expansion cycle of pure foundries will never be sidelined as a non-hot topic. Similarly, the market trends of large chip manufacturers with IDM attributes are also the focus of various research institutions. The "Core View" column once published an article titled "Shen Yin's Lack of Core Initiators "TI" Sit Firmly on the Diaoyutai? "" has done a certain degree of analysis of idM's role in the new situation.
Ten years ago, the famous research organization McKinsey released data showing that the global pure foundry capacity is a quarter of IDM enterprises, as shown in the following figure:
But today, if the memory chip is removed, the production capacity of the two sides can be tied (the American Semiconductor Industry Association SIA reported data in September last year), which shows that the production capacity of pure foundries has soared in the past decade. It can also be inferred that the proportion of outsourcing in major IDM companies is also increasing.
This paper selects the in-production/outsourcing routes of NXP and STMicroelectronics (ST), two IDM-type companies, as research objects, and mainly observes whether the connotation of the concept of "outsourcing" is undergoing some subtle changes.
NXP, with clear boundaries and clear routes
For fifteen years, NXP has been asserting in its reports to the U.S. Securities and Exchange Commission (SEC) that it uses its own FAB and outsourcing to ensure that companies achieve economies of scale in terms of asset utilization, procurement volumes, and cross-business overhead leverage. In a series of announcements to the SEC, NXP also clarified that the company mainly focuses its internal and joint venture wafer manufacturing operations on operating proprietary special process technologies, with the main purpose of differentiating products on key performance characteristics, for which NXP has divided the 90nm process node.
Typically, NXP chooses to outsource processes of 90nm and higher specifications, and since 2018 until the massive spread of global "core waste", the company has focused on in-house manufacturing on competitive 8-inch wafer facilities that operate primarily on 140nm, 180nm and 250nm process nodes. And that strategy has hardly changed in the last fifteen years. This can be seen in a quote from 2010 when NXP's then-CEO Rick Clemmer said: "We will not produce our own 65nm high-performance mixed-signal chip in-house, and the added value of the product is more about the company's design than the process of its design." ”
Over the years, NXP has repeatedly reiterated this strategy in its earnings reports. NXP has fabs in Nijmegen in the Netherlands and Austin, Arizona, Texas, North America, and the local team has the longest history, relying on 8-inch devices to focus on CMOS RF front ends, automotive wireless receiver chips, and high-power DC-DC power management chips and LED driver chips, these product types represent NXP's self-production strategy. Of course, a large part of the reason is that the process specifications of the above analog integrated circuits are quite stable and slow to iterate, and under the clear boundaries of 90nm, NXP's senior management can freely allocate capacity without having to make a big fuss.
It is worth noting that almost all of NXP's high-end automotive chips are outsourced to TSMC, including the interconnected cockpit, high-performance domain controllers, advanced vehicle networks, hybrid propulsion control and integrated chassis management, using the vehicle-grade TSMC 5nm SoC technology, in addition, the NXP S32G2 vehicle network processor and S32R294 radar processor are also operated by TSMC. Last year, when the global core famine spread around the world, NXP preemptively advanced up to $4 billion in orders, stealing a part of TSMC's valuable vehicle-grade chip production capacity. It should be noted that automotive chips currently account for only about 5% of TSMC's total production capacity.
Among the large semiconductor IDM companies in Europe, if the relationship with TSMC is deep, it is difficult to have a better than NXP. NXP was formerly the semiconductor division of the Dutch electronics industry group Philips, and Philips was an important shareholder and investor in TSMC's takeoff. When NXP spun off from Philips in 2006, Philips executives discussed whether to transfer some of their stake to NXP, and finally decided to let NXP go public. After NXP withdrew from the Crolles2 alliance in which TSMC, STMicroelectronics and Freescale participated, in order to retreat into the future, not only with TSMC to build a joint venture with TSMC in Singapore SSMC (Systems on Silicon Manufacturing), but also for a large sum of nearly $12 billion to buy Freescale, then, in this series of attacks, NXP's self-produced/outsourced ratio has been adjusted?
SSMC joint venture between NXP and TSMC (@NXP LinkedIn)
For NXP, it is difficult to summarize this ratio with a precise number. NXP, which has just been independently listed, has about 7% of the capital support for outsourcing and about 20% of the capacity outsourcing, and today, about 57-58% of NXP's wafer supply comes from outside. But this is also an estimate from the outside world, and the subtlety is that NXP does not clearly indicate how the joint venture SSMC with TSMC is divided, after all, there is no need to make a clear distinction between the financial and accounting audit and the overall market strategy. SSMC is now 24 years old, and NXP currently holds more than 60% of the shares, using leading CMOS, embedded flash, analog and high-performance mixed-signal, RF, BCD and sensor process technologies ranging from 250nm to 150nm, based on NXP's 8-inch device system. At the very least, it can be seen that NXP does not produce all of its own analog chips that are more mature than 90nm. SSMC also plays an important role in process supervision and market pulse monitoring, and is an indicator of NXP's significant industrial trends.
Frans van Houten, a former CEO of NXP (now CEO of Philips Group), has given instructions on the proportion of outsourcing, believing that once the total capital expenditure or total capacity ratio reaches 40%, it is a red flag. "Based on pareto optimization principles, outsourcing is capped at about 40 percent, and beyond that, you could become too dependent on vendors," he says. "The cautious approach to outsourcing allows NXP to constantly test whether the purchase cost of outsourced products is higher than the manufacturing cost of home production to assess gross margins. The price of the OEM product will also vary depending on the supplier's capacity utilization rate, demand, and product technology. In the case of chip shortages, outsourcing costs are likely to increase significantly, after all, lead times and operating costs are directly linked.
Of course, in order to balance costs and market risks, NXP, which is cautious first, obtained part of the capacity of UMC's expansion in the mode of jointly building a fab, injected funds into the expansion of fab 12A P6 plant of UMC's 12-inch factory, and allocated the production capacity of financial transaction chips, smart cards, digital ID cards and other chips that require higher level of security certification to GF.
STMicroelectronics strives for broadness rather than independence
At the end of last year, a piece of news made ST a hot topic of discussion in the industry. Samsung Electronics has received an OEM order from ST To produce MCUs for Apple's next-generation iPhone, using a 16nm process. This is the first time ST has outsourced MCUs to major customers such as Apple. Although Samsung did not respond directly to this matter, presumably the information channel is not a catch.5
After losing Huawei, a large customer that once accounted for nearly 10% of revenue, ST further hugged Apple's thigh, and the annual revenue of the company of 2.5 billion to 3 billion US dollars came from Apple products, accounting for about 25%, which is also the semiconductor company that relies most on consumer electronics in all semiconductor IDMs in Europe, outsourcing Apple's MCU needs to Samsung, forming a chain of production capacity demand, so that the relationship between Apple and Samsung in the mobile phone market has become more and more delicate.
In fact, as early as 2014, Samsung and ST began a tentative in-depth cooperation, Samsung in South Korea's Kiheung (Kiheung) plant S1 factory for ST based on the FD-SOI process to manufacture low-power communication chips for smart phones and wearable devices; from Samsung's point of view, this is one of the means to test soI and Intel FinFET technology route competition; for ST, after the wireless business cooperation with Ericsson stagnated, It's been refocusing its business in new market segments and trying to tap into new customers, so the two sides hit it off.
ST has a diverse product portfolio and its strategy has led it to firmly develop high integration of chips. Its low leverage, prudent shareholder distributions and limited M&A activity offset its lower profitability, lower margins and cash flow (compared to Infiniton and NXP). As a result, ST's ability to seek breadth rather than independence makes their outsourcing strategies more diversified than their European counterparts.
ST's 12-inch fab in Agrate Brianza (source@eetime)
At the beginning of this century, ST and UMC allied in the foundry business, but at about the same time, ST and NXP switched to the TSMC 90nm process technology platform to carry out HCMOS wafer and nonvolatile memory technology cooperation. At present, the two sides are working together to accelerate the gallium nitride process technology, focusing on consumer electronics and automotive-grade power semiconductor business, but ST and the old partner UMC have maintained a close relationship, the company's 65nm CMOS CIS BSI technology, using 12-inch wafer equipment, long-term OEM by UMC. In addition, the main partner of GF's SOI technology expansion capabilities is ST. After the partnership deployed the industry's first 28nm FD-SOI technology platform, ST expanded its commitment and roadmap by adopting GF's production-ready 22FDX process and ecosystem, and ST went further than NXP in support of the FD-SOI technology route.
What's more, last year, ST and The Israel-based analog chip foundry TowerSemi also played a model of settlement and cooperation, and the two shared a 12-inch AgileT R3 fab, which made the outside world even speculate at one point whether ST had an attempt to acquire TowerSemi, but this rumor was completely silenced with the latter being acquired by Intel.
If only in terms of the breadth of the product line rather than the end market, the analogy with ST is Texas Instruments (TI) on the other side of the Atlantic. The underlying market logic and corresponding technical route of TI's own production and outsourcing can be used as a reference. In this regard, Ma Dongli, research director of Jiwei Consulting, pointed out: "After 2008, ti's mobile phone business accounted for a rapid reduction, the product line has a new layout, the current 70%-80% of the business comes from analog chips, the most advanced process is 28nm, and then there is no more." TI's self-production ratio is much higher than that of IDM in Europe, and its dependence on external foundries is low. Outsourcing is mainly MCU with logic chip nature, such as the MCU of the MSP430 product family outsourced to TSMC, in addition to cooperation with UMC and GF. ”
TI and ST are also investing heavily in 12-inch fabs and will increase their own production capacity in the future, but from the perspective of the game between technology routes and R& D costs, TI is more similar to NXP's outsourcing routes.
epilogue
Overall, in the past decade or so, the world's largest semiconductor IDM manufacturers are more or less increasing the proportion of outsourcing, especially in the European region of IDM packaging and testing is also highly dependent on East Asia and Southeast Asia OSAT companies, NXP and STMicroelectronics have different corporate cultures, in many segments are also in different tracks, choose different in-house production/outsourcing strategies. The former mainly considers the product process characteristics and the customer group connection under historical factors, setting a clear boundary outsourcing moat; the latter, in addition to the cost, has also chosen a more divergent and diversified outsourcing route because of the breadth of its own products.
With the expansion of analog chips towards a wider horizontal level, and the expansion of logic chip computing power in the direction of depth, supplemented by the wide application of new wide bandgap materials, the importance of operating costs in the IDM outsourcing factor may be coated with a more different meaning, that is, foundry partners will increasingly play the role of market probe and track simulation, this judgment, but also need more IDM or fab-lite enterprises to do more in-depth research. (Proofreading/Stan)