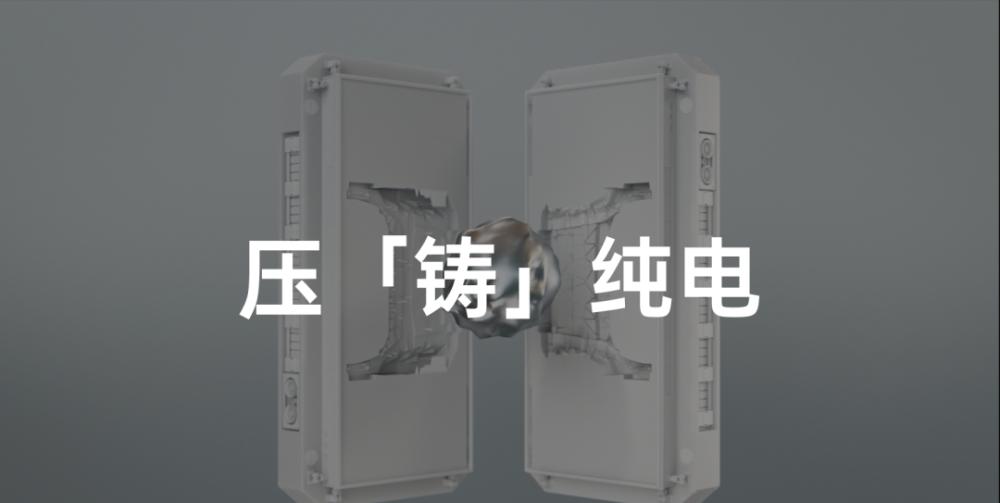
The battery is stable
Hey hey, I'm free
On October 29 last year, Volvo Cars successfully launched itself in Sweden. The current market capitalization is about 300 billion yuan, which is 30 times the $1.8 billion it was acquired by Geely 12 years ago. Of course, in addition to allowing Li Shufu and the old employees with options to get a good return, Volvo itself has also obtained a healthier cash flow.
So, what do you want to do when you have money after going public?
Of course, it is investment, the kind of full electrification transformation.
Co-branded batteries
Volvo Cars recently announced that it will invest about 21 billion yuan in battery manufacturing. The money will also be injected into Volvo and Sweden's own battery manufacturer Northvolt to build a power battery factory in the southern Swedish port city of Gothenburg, Volvo's home base. The plant is planned to have an annual capacity of 50 GWh and will also have an R&D center.
The new plant, which is scheduled to begin construction in 2023 and start operations in 2025, will supply batteries to 500,000 Volvo's pure electric models and the high-end sub-brand Polestar's pure electric models per year.
What about cars?
New bottlenecks
Vehicle production!
Together with the Swedish version of the "Ningde Era", Volvo has stabilized the future battery supply. However, according to the data, the Torslanda plant has an annual capacity of 300,000 units, which seems to be somewhat disappointing of the future 50 GWh of battery capacity.
In other words, the output of the car shell must also be matched with the output of the battery pack. As a result, Volvo, which became rich after the IPO, continued to throw money and recently announced that it would invest about 7 billion yuan in the next few years to the Torslanda manufacturing plant in Gothenburg, Sweden, in preparation for the production of the next generation of pure electric cars.
Engaged in die casting
These two days I saw an official Volvo press release that read:
As part of the planned investment, the company will introduce some new, more sustainable technologies and manufacturing processes into the plant. These include the introduction of a large aluminium body parts casting process, a new battery assembly plant and a completely refurbished paint and final assembly shop.
Wait, isn't the "casting process for large aluminum body parts" an integrated die-cast body?
Well, after watching the video, I found that it really is. Volvo also has to do the suppression of the body, and the parts are almost the same as the Tesla Model Y, and the position of the rear bottom plate is chosen.
This is Tesla
This is Volvo
In addition to THE ANNOUNCEMENT LAST YEAR OF WEILAI'S SUCCESSFUL DEVELOPMENT OF HEAT-FREE ALUMINUM ALLOY FOR Die Casting, Xiaopeng Wuhan Factory Will Introduce Large Die Casting Equipment, etc., the EQXX concept car displayed by Mercedes-Benz during CES also showed a highly organic shaped aluminum alloy die-cast back plate.
BIONEXX
In addition, there are also news that Ford and BMW will also apply integrated die casting technology in individual new generation models. However, Volvo's one-piece die-casting scheme called mega casting is one of the players with the clearest timeline in addition to Tesla, which has already landed.
Mega casting?
Where is die casting good?
You draw I guess
As can be seen from the screenshot of this official promotional video with a strong Nordic design style and a bit of asceticism, volvo believes that there are three main advantages of one-piece die casting.
1. Reduce the number of parts;
2. Reduce carbon footprint;
3. Reduce the weight of the car.
And this is a complementary triangular relationship, not abstinent at all.
A single aluminum rear back plate can reduce weight and increase the range of the car. One-piece molding eliminates some of the processes such as heat treatment and welding, simplifying the complexity of production. Excess waste removed on site can also be recycled on the spot, which in turn saves costs in terms of materials and logistics, which in turn reduces the overall environmental impact of the manufacturing process and supply chain.
If you are a little dissatisfied with the popular science of this technology, then you can also read my previous popular science article on this technology, "Punch production? No! "Cast" production is sexy! (Link at the end of the article).
If you spent 2 seconds seeing this, you may also have a problem such as "one-piece die casting cannot be repaired".
Well, you're worried. Even if it is a stamping + welding process, if your car is rear-ended to this extent, it is also a big accident cutting car, which is basically equivalent to waste. Anyway, we still believe that the future OF AI autonomous driving technology can improve the active safety performance of each car!
The big guy answers questions
Dr. Mikael Fermér – Head of Platform Architecture for Volvo Vehicles
On the first day of construction in the Year of the Tiger, I also had the privilege of having a video conference with Dr. Mikael Fermér, volvo's head of the project, to gain further information about mega casting.
Q1: What are the models that use integrated die casting technology? When to go offline?
We will introduce an integrated casting process on a new all-electric platform, around 2025. The first product will be announced at a later date.
Q2: Has the supplier of the die casting machine been determined and what specifications will it be?
We are in the final stages of negotiations, so we are negotiating with some leading manufacturers and will make a decision as soon as possible. The one-piece cast rear baseplate would be a starting point. These machines can also be used in the front structure or the middle, and if you want to cast the entire bottom, it may be at least twice or triple the size of the machine now, but these machines are not yet on the market, so the largest machine you can find today is about 12,000 tons. Our goal is to use a machine with 8,000 tons of clamping force on the production of the rear baseplate, with a beat of 140 seconds. The Torslanda plant has a capacity of 60 units per hour, and the number of die casting machines we purchase is determined by this target.
Q3: What are the engineering challenges of integrated die casting? Is the aluminum alloy used the same as Tesla and does not require heat treatment?
You must respect the physical principles of molds and castings. Usually, when you use steel structures, you will use specific closed beam structures, but the one-piece die casting is an open section, if you want, you can close these structures, but it will increase the cost, weight. Obtaining optimal stiffness where it is really needed is a new development challenge. We have developed a heat-free aluminum alloy material, and if not, the alloy is like potato chips, very brittle. We are currently working on different alloys, and the difficulty we face is that, from a sustainability point of view, we need alloys that contain a lot of recycled aluminum. We are looking at 50% recycled aluminum. We are also working on alloys containing 100% recycled aluminum, but none of these alloys have yet to meet our target standards.
Q4: What are some of the environmental considerations for Volvo, which has set a vision of zero climate burden 2040?
Furnaces in the plant are heated with biogas. But overall, if you want to reduce carbon dioxide emissions, you have to keep track until mining, because the bulk of the energy consumption is the smelting of aluminum metal, which of course is the main source of carbon dioxide emissions. So we have to sign up with aluminium suppliers that offer low CO2 emissions, and the CO2 emissions per 1 kg of aluminum are less than 4 kg, which is our standard. The aluminum alloy scrap generated at the site can be directly returned to the furnace, reducing transportation costs and waste of materials. This is also a major advantage of aluminum alloy integrated die casting. In contrast, the stamping process produces about half of the scrap that needs to be transported.
Q5: The mold cost of one-piece die casting is very high, so where are its advantages?
I think the benefit of the all-in-one casting process is that you can really optimize the product for every product or every market segment. Thus, this avoids the limitations of traditional platforms, where scaling has been predetermined. I think that's very important as we prepare for the transition to better electric vehicles. Will there be new energy storage methods, new motors, and wheel hub motors in the future? I mean, there can be a lot of new things, so you have to master flexible technology. And this technique is much more flexible than the traditional pre-determined everything setup.
Guess and think
The one-piece die-casting technology is only used in the case of the rear baseplate, and the wheelbase of the vehicle and the shape of the upper body still have degrees of freedom. Then the narrowing will not immediately be the variety of models, but the types of platforms. That's why the SPA2 architecture will be the workhorse of Volvo in the future.
XC 40 Recharge
Volvo CTO Henrik Green once said in a media interview that the SPA2 pure electric version will have a tiled battery chassis, rather than the hybrid design of the current volvo pure electric model saddle-shaped battery pack. Therefore, I venture to guess that mega casting will most likely be used on SPA2 pure electric models.
Traditional brands have been working the battlefield for many years, and in order to eat more market segments, it is inevitable that complex product lines will gradually form. In order to survive in this increasingly volumetric pure electric intelligent car track, the pressure on pricing and gross profit margins of OEMs will inevitably make more companies adopt the single product explosion logic of new forces such as Tesla.
The high amount of mold means that its life must be squeezed to the limit is a good business, which also means that the longer the cycle of the body itself, the more reasonable it is. As a result, as the number of models is further reduced, larger areas of one-piece die casting and even the entire body will become a reality due to market drive. The premise is the ability of car companies to grasp market demand and the rationality of initial product planning.
SPA2 platform with Concept Recharge of Luminar lidar
Then in addition to the hardware itself, intelligent product experience and sustainable software iteration capabilities, as well as the effectiveness of user operations, are also crucial. Whether the above crossover SUV that looks like the V70 of that year can create ripples in this red sea after mass production depends on whether Volvo can quickly light up these new car-making skills.