According to the latest data from the China Automobile Association, in 2021, the production and sales of mainland automobiles reached 26.082 million units and 26.275 million units, respectively, an increase of 3.4% and 3.8% year-on-year, ending the downward trend. Car sales rebounded strongly, which means that the number of cars in mainland China has exceeded 300 million units. At the same time, global warming poses a major threat to human beings and the earth's ecology, and puts forward a major test for whether human beings can survive sustainably, and the countries of the world have gradually formed a consensus on the seriousness of global warming, and many countries have elevated "carbon peak, carbon neutrality" as a national strategy. The dual carbon target also forces OEMs and suppliers to explore new technology paths to achieve energy conservation and emission reduction.
The industry found that when the vehicle is reduced by 10%, fuel consumption can be reduced by 6%-8%, vehicle emissions can be reduced by 10%, in addition to increasing the life of tires by 7%, reducing acceleration time and braking distance. Lightweight not only brings the gospel of energy saving and emission reduction, but also improves driving comfort, so the penetration rate of lightweight die casting technology in automobiles will continue to increase driven by demand.
Materials, processes, and structures seek optimal solutions
In order to meet the technical needs of lightweight die casting in automobiles, the industry currently mainly makes breakthroughs in materials, processes and structural design:
In terms of materials, the materials used in lightweight automobiles mainly include: high-strength steel, aluminum alloy, magnesium alloy and carbon fiber composite material. From the perspective of weight reduction effect, high-strength steel, aluminum alloy, magnesium alloy and carbon fiber composite materials show an increasing weight reduction effect between the four; from the perspective of cost, there is an increasing trend between the four.
Combining the four materials, it can be found that the aluminum parts are lighter in quality and have better extrusion, corrosion resistance and recyclability. Aluminum alloy can achieve better braking, better handling, better driving comfort and more prominent power while reducing weight. At present, cast aluminum alloy accounts for about 77% of the amount of aluminum used in automobiles, so aluminum alloy materials will be widely used for a long time.
In terms of process, almost all well-known automobile manufacturers have adopted laser welding technology, using rolled plates of unequal thickness, and the spacing of rolls is controlled and adjusted in real time by computer to obtain sheets that change continuously according to pre-customized thicknesses in the rolling direction. Tesla's integrated die casting technology leads the way in both the manufacturing process and the materials.
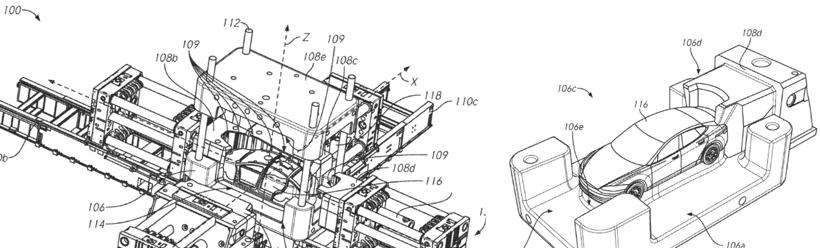
Image source: electrek.co
In addition, in the automotive process, there are internal high-pressure forming (hydraulic forming) manufacturing technology; ultra-high-strength steel hot stamping forming technology; roll forming technology; high pressure casting molding technology; low (difference) pressure casting molding technology and automotive lightweight connection technology.
In terms of lightweight body structure, that is, by using advanced optimization design methods and technical means, without affecting the basic state of the body, by optimizing the body structure parameters, improving the utilization rate of materials, removing redundant parts of parts, and at the same time making the components thin-walled, hollowed out, miniaturized, and compounded to reduce weight and achieve lightweight. Structural lightweight, according to the design variables and optimization problem types, can be divided into topology optimization, size optimization, shape optimization, topography optimization four types.
The starting point of Continental's lightweight vehicles began with the application and development of new materials such as high-strength steel, aluminum and composite materials, and achieved the three-step goal of weight reduction through the joint action of materials, design and process. In recent years, the output of aluminum alloy die castings in Mainland China has increased year by year and developed rapidly. Driven by the trend of automobile lightweighting, there is a huge demand in the global aluminum alloy die casting market, and in recent years, the automotive industry is constantly optimizing and upgrading, gradually replacing gray iron castings with aluminum castings, thus stimulating the growing demand for aluminum alloy die castings.
Catalytic die-casting quality track
In 2018, China's automotive industry will consume 3.84 million tons of aluminum, of which 72% will be consumed by passenger cars. Total aluminium consumption is forecast to grow at a CAGR of 8.9% by 2030 and reach 10.73 million tonnes. Combined with the market can be found that Guangdong Hongtu, Wencan shares and other aluminum alloy die casting track leading enterprises performance eye-catching, highlighting market confidence, with the drive of the policy and the urgent needs of the automotive industry for lightweight, aluminum alloy die casting market capacity is expected to expand, there are strong material preparation, design capabilities and master the advanced technology of aluminum alloy die casting enterprise development potential is huge.
According to the European passenger car aluminum volume report released by the automotive research institute Duckerfrontier, the demand for aluminum for engines, wheels, transmissions, chassis and heat transmission in the various component systems of passenger cars is relatively large, 70.2, 64.2, 32.3, 31.4 and 310,000 tons, respectively, and the aluminum consumption of engines and wheels accounts for 45% of the total aluminum used in automobiles. In order to meet the needs of automobile lightweighting, the current aluminum alloy die-casting products are mainly used in the chassis of automobiles, three-electric systems and body-in-white.
Image source: Orient Securities
In 2021, China's new energy electric vehicle sales of more than 3 million vehicles are eye-catching, showing unexpected growth, as the output of electric vehicles continues to accelerate, the average amount of aluminum used in battery boxes and motor shells will grow rapidly. In 2021-2025, electrified components will be the main growth areas for aluminum alloy die-casting products, and battery boxes and body bodies will become the biggest beneficiaries of the average increase in aluminum consumption. Among them, the amount of aluminum used in the battery box accounts for nearly two-thirds of the average increase in future aluminum consumption.
The chassis carries 70% of the body weight, and the lightweight chassis helps to reduce the underspring weight, thereby improving the acceleration, handling and comfort of the car. At present, the main path of chassis lightweight is to replace steel with aluminum alloy, according to the data of China Industry Information Network, in 2020, the penetration rate of aluminum alloy steering knuckles, auxiliary frames, brake calipers and control arms in the Chinese automotive market is 15%, 8%, 40% and 5%, respectively, with broad room for improvement. Many domestic aluminum alloy precision die casting companies are in the field of chassis lightweight layout, with the increasing demand for automotive lightweight, it is expected that aluminum alloy components will accelerate penetration in the chassis field, related parts companies are expected to continue to benefit from the chassis lightweight trend.
Not to be outdone The prospect of lightweight body in-white is huge
Automobile body is the highest proportion of vehicle weight, but also the field with the greatest potential for lightweight, traditional cars with high-strength steel instead of ordinary steel can reduce weight by about 11%, the use of aluminum alloy can reduce weight by about 40%, lightweight material weight reduction effect is significant. In view of the body strength requirements, the price of lightweight materials and the level of processing technology, the status of steel as the main material of automobile body is difficult to shake in a short period of time.
Image source: Gaz Cars
At present, some pioneering automobile manufacturers such as American, Zongshen Power, and Aikodi are solving the problem of body lightweight through the layout of integrated die-casting technology. At the end of the manufacturing process, this technology can make the body one-time molding, greatly simplify the manufacturing process, and can eliminate the cumulative error caused by the connection of a large number of parts, and the manufacturing accuracy can be improved, while saving a lot of debugging time and money costs. At the material end, the traditional automobile manufacturing process widely uses steel that is easy to stamp and weld as the body material, and in the integrated die-casting technology, the aluminum alloy that is convenient for die-casting will become the main material of the body, driving the application of aluminum alloy parts on the whole vehicle to increase, solving the problem of stamping-welding-painting-assembly difficulties caused by the yield strength, tensile strength and low elongation of aluminum alloy materials, and further improving the degree of lightweighting of the car. At present, Seiko Die Casting has signed a contract to purchase a set of 8000T super large die casting islands, deploying integrated body structural parts research and development and production, aiming to use integrated die casting to achieve weight reduction, simplify production process and reduce labor.
However, in addition to the material properties, for aluminum alloy body, the biggest challenge in performance is the improvement of NVH and crash performance. The density of aluminum alloy is only one-third of that of steel, and how to improve the sound insulation effect and crash safety of automobiles without increasing the aluminum alloy material has also become a problem that plagues the industry.
Product + Technology When body manufacturing will achieve lightweighting
According to the "Energy-saving and New Energy Vehicle Technology Roadmap" released by the Society of Automotive Engineers of China, by 2025, cars need to achieve a weight reduction of 30%, and expand the application of aluminum, magnesium alloys and carbon fiber reinforced composites on car bodies. Combined with the body field, the use of aluminum alloy materials has become a trend in the future development of the body, while the output of continental alumina and electrolytic aluminum is the world's first, which also provides a good development foundation for the development of the continental aluminum alloy die casting industry. In terms of technology, integrated die casting is still in the introduction period, how to develop in the future has not yet been determined, Weilai and other new car-making forces are actively trying to do this aspect.
Body-in-white is the most important basic part of the car, with the improvement of the level of technology in the automotive industry, the relevant technology in the body-in-white field is also constantly improving, new materials, new processes, new design concepts continue to emerge, whether in the field of traditional energy vehicles or new energy vehicles, as well as the field of intelligent networked vehicles in the future, body technology has always been the core part of automobile performance.
How to break the barriers of the body-in-white body in terms of process, material, structural design, etc., and truly achieve lightweight, urgently need to be continuously explored in the industry. In order to fully grasp the trend and find a breakthrough in the challenge, Gaz Auto specially hosted the second body conference in 2022, and invited people of insight in the industry to study and develop together and seek the future.