Everyday Finance exclusive, quick attention
Robot arms flying up and down, workers are skillfully operating, logistics vehicles are shuttling in an orderly manner, and quality inspectors are carefully "looking for stubble"... A few days ago, the reporter participated in the GAC Toyota "One Day Craftsman" Quality Open Day and learned that thanks to the leading scientific and technological advantages and the concept of ingenuity and quality, the one-time pass rate and quality of the GAC Toyota production line continued to improve, and the sales of many of its products continued to grow strongly this year.
According to the data, from January to October 2021, GAC Toyota's dual-engine hybrid models sold a total of 134,000 units, an increase of 84% year-on-year, ranking first among mainstream joint venture car companies.
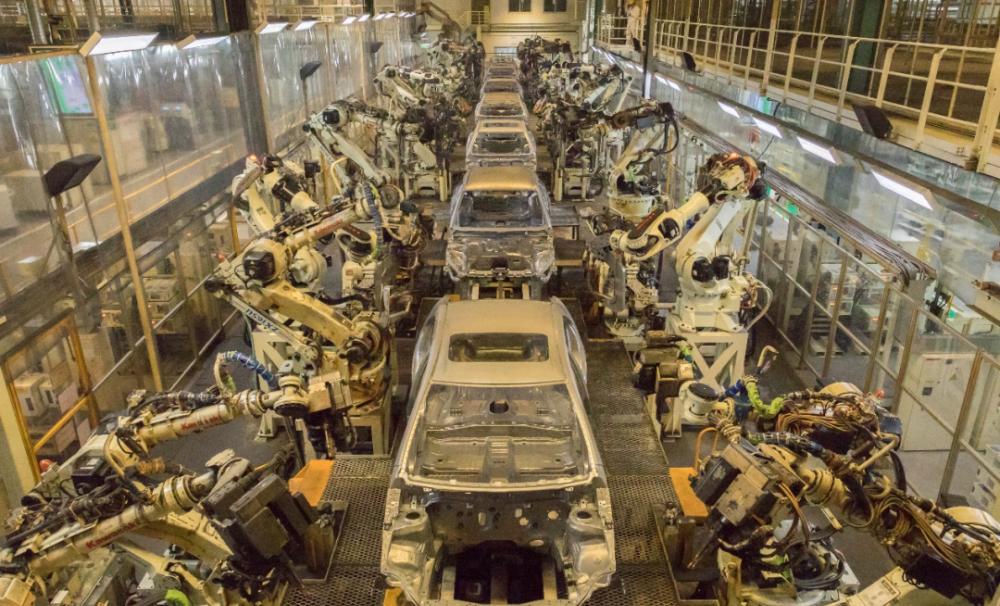
Image source: GAC Toyota
Any production line employee has the right to stop the production line
The reporter visited the second production line of GAC Toyota. According to reports, GAC Toyota Camry, Willanda, Highlander and other models are from the production line. Each car needs to go through five manufacturing links: stamping, welding, painting, final assembly, and inspection, each of which is produced in accordance with Toyota's highest standards.
According to reports, GAC Toyota relies on just in time (JUST IN TIME) and automation "two pillars" to steadily control the quality of final assembly. "Punctuality" avoids waste and improves efficiency; automation requires people and machines to automatically judge the quality of the process, stop and improve in time when problems are found, do not let quality problems flow into the next process, prevent parts assembly errors, and meet Toyota's highest standards.
"Quality is manufactured in the process, not by inspection." Huang Zonghao, chief of the quality management department of GAC Toyota, said that this is also regarded as the secret of GAC Toyota's ingenuity.
On the production line, the reporter saw that yellow and red drawstrings were set up above each workstation. There is also an eye-catching monitoring display next to the production line, which shows the operation of the production line in real time.
According to reports, this is an Anton system launched by GAC Toyota that visualizes quality problems. Whenever the production line employees encounter an abnormal situation that cannot be solved, immediately pull the Anton pull rope, the display screen will timely feedback the problem point and the station, the line work team leader immediately deal with it, if the vehicle is still not solved before reaching the next station, the production line will automatically stop. Any production line employee has the right to stop the production line and let the quality problem be solved "at the time and locally", which also ensures the first-class quality control level of GAC Toyota to the greatest extent.
For example, in order to avoid the problem of poor tightening caused by human factors, The Anton System has introduced a "error-proofing system" with an automatic alarm device for tri-color lampposts. When workers start tightening the bolts, the blue light is lit. Only by tightening the bolts can the green light be lit and the station can be passed. Otherwise, the Anton system will automatically alarm, the red light will be lit, and the production line will stop. It is not until the problem is solved that the production line can be started again.
The one-time pass rate of the production line reaches 99%
The reporter also found that in each workshop of GAC Toyota, there is a quality corner to display the key quality improvement activities and effects from the production line to the present. Every new employee needs to go to the quality corner to learn and experience, so that they can develop a sense of quality priority and understand the importance of adhering to standard operations before they participate in actual production.
According to reports, GAC Toyota adheres to the concept of "building cars and educating people", the company formulates corresponding growth plans according to the level of each employee, and adjusts the plan through regular training and assessment, so that everyone can grow efficiently.
At the same time, GAC Toyota also carried out the "Best of The Best - All-Staff Ingenuity Action" internally, from managers, engineers to front-line craftsmen more than 8,000 employees actively participated in continuous improvement, and submitted 12,000 quality improvement cases every year, with an adoption rate of 99%.
With the efforts of all the craftsmen, the manufacturing quality of GAC Toyota has continued to improve. In 2020, the one-time pass rate of GAC Toyota's production line increased to 99%, 10 percentage points ahead of the industry average; the vehicle defect decreased to 0.01 pieces/unit; and the supplier parts defect rate decreased to 0.29 PPM (that is, only 0.29 defects out of 1 million parts).
More than 1500 audits control the production level
The reporter also learned that in the GAC Toyota plant, there is an independent inspection class of the quality assurance department independent of the manufacturing department, which is responsible for controlling the production level of GAC Toyota.
At this secret quality base, inspectors wearing the black hat of the SQA (Independent Quality Assurance Inspection) logo evaluate the quality of the vehicle from the customer's point of view according to toyota's global methods and benchmarks, and evaluate more than 1,500 items. Even vehicles that are qualified by the production line must strive for excellence, constantly discover new problems, and find the source to improve.
According to reports, in order to further improve the quality, the independent inspection class has even set higher standards on the basis of Toyota standards.
GAC Toyota's sales performance continues to grow strongly, and the key behind it is the ingenuity that GAC Toyota has always adhered to throughout the process of ingenuity infusion and the ingenuity of all employees. The reporter also learned that although the current new crown epidemic is still repeated, and the shortage of chips in the industry has not been fundamentally solved, by strengthening supply chain management, maximizing stable production and ensuring delivery, GAC Toyota will produce and sell more than 800,000 units this year. In addition, next year, GAC Toyota will challenge 1 million units to launch an impact on the head camp of joint venture car companies.
Editor: Wang Yin