Source of this article: Time Weekly Author: Yang Lingling
【Editor's Note】
The global manufacturing industry is experiencing a new round of industrial transformation and transformation and upgrading. As one of the most developed manufacturing regions in the world, the manufacturing transformation of the Guangdong-Hong Kong-Macao Greater Bay Area has always been at the forefront of the industry, playing the role of forerunner and pathfinder.
In 2022, the Times Weekly Sankei News Department launched the annual special topic of "Bay Area Intelligent Manufacturing Power", which went deep into the manufacturing industry belt of the Greater Bay Area, recorded the major changes in the manufacturing industry under the new wave, and provided samples and experience for manufacturing enterprises.
The difficulty of recruiting workers in the manufacturing industry has attracted widespread attention from society. According to data from the Ministry of Human Resources and Social Security, in the fourth quarter of 2021, 43 of the 100 occupations in the country's "most under-needed jobs" are "manufacturing and related personnel", and it is expected that by 2025, the talent gap in the ten key areas of China's manufacturing industry will be nearly 30 million people, with a gap rate of up to 48%.
Previously, "going into the factory or delivering takeaways" has triggered discussions, manufacturing factories want to retain young people, and improving the attractiveness of jobs has become the key.
"What made me more anxious before was that many manufacturing workers left the factory and entered new occupations." Recently, Li Weijun, CEO of Guangzhou Ligong Industrial Co., Ltd. (hereinafter referred to as "Ligong Industry"), said in an interview with the Times Weekly reporter that after the robot was put into the production line, the dirty work in the factory was operated by the robot, and the turnover rate of front-line workers was greatly reduced.
Small and medium-sized enterprises are the "capillaries" of China's economy, and by the end of 2021, the number of small and medium-sized enterprises like Ligong Industry in Guangdong Province will exceed 6.3 million, accounting for about 1/7 of the country, which is an important pillar for stabilizing employment and ensuring people's livelihood. Digital transformation has become an important way for small and medium-sized manufacturing enterprises to solve the problems of recruitment difficulties and labor shortages.
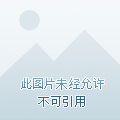
Leave young people in the factory
As a small and medium-sized manufacturing enterprise with a history of 37 years, the digital transformation of Ligong Industry is fraught with difficulties. From the perspective of product line, Ligong Industry not only does the whole machine equipment, but also produces parts, both its own research and development department, as well as OEM business. Over the past 37 years, the business has changed, and its organizational structure and personnel composition have become intricate.
"In 1985, my father founded Ligong, when the main rubber sealing ring, I joined the company after graduating from university, just in time for China's accession to the WTO, we had the opportunity to contact foreign customers, slowly transformed into the production of mechanical parts, and then transitioned to the whole machine equipment." Li Recalled.
Li Weijun gave an example to the Times Weekly reporter that at present, there are both junior high school teachers with more than 20 years of working experience in the factory, as well as R&D personnel from returnees and Internet factories. "We also hope that like many traditional companies, we can find a fast track in digitalization, but we still have to respect history, and some things change without just ringing their fingers."
In the process of business operation, what makes Li Weijun more anxious is the continuous loss of manufacturing workers. "We realize that the operation of enterprises, especially the operation of production-oriented enterprises, talents play a decisive role, and what we urgently need to solve is also the problem of the shortage of people in the scattered manufacturing of small and medium-sized enterprises."
"Let's assume that this colleague doesn't do this line of work, but goes to the salary received by another line, and we can rewind the salary we should give." For example, suppose these workers make more money delivering food than in factories, then he must not be dry, and young people do not like jobs, but they do not like low-paying jobs. Li Weijun said.
In addition, 7 years ago, Ligong Industrial began to develop and manufacture robots. Li Weijun introduced that there are currently 219 employees in the industry, of which half of the production line employees. "In the past, our colleagues had to put parts into the production machine, tighten a certain thing to let it process, etc., the hands that drank water were dirty, the kettle was also touched black, young people were more willing to send takeaways and did not want to enter the factory, and now the workers do not have to directly operate the production equipment, and the hands are cleaner than those with the keyboard."
Small and medium-sized manufacturing enterprises accelerate digital transformation
After the use of robot human-machine collaboration, a significant change is the gradual equalization of the proportion of men and women. In the production line of precision manufacturing, especially mechanical parts, men have always been in an absolute dominant position.
"3 years ago, the ratio of men to women on our production line was about 8:1, and now it has dropped to 4:1, and I believe that it will decline in the future," said Huang Yuanyuan, COO of Guangzhou Ligong Industrial Co., Ltd., plus functional departments, and the overall male-female ratio of Ligong is about 1:2.3.
Digitalization penetrates into all aspects of the enterprise, so that every link can be digitized, becoming one of the most important jobs in the present and future of Ligong Industry, among which the digitalization of management is also another short board that small and medium-sized manufacturing enterprises need to make up.
"We've been experimenting with digital management tools." Li Weiyong said that the most frequently used digital platform is DingTalk, including OA approval, management, logs, attendance, CRM and financial management. "Next, we will apply ERP in the DingTalk ecosystem, and we will also put the digital tools we have developed on DingTalk to help other peers achieve digital management."
"At present, China's digital economy has entered a new stage of development. Based on the background of the era of digital technology serving the real economy, DingTalk's strategy and business priorities have changed, as an important link in the digital economy chain, the common choice of DingTalk and toB enterprise service ecological partners is to do a good job as a service provider of the digital economy and jointly promote progress. DingTalk President Ye Jun said at DingTalk's 2022 press conference held on March 22.
There are not a few manufacturing companies like Ligong Industry that are seeking digital transformation. At present, Guangdong is actively promoting the digital transformation of the manufacturing industry, and it is clear that by 2025, the digital level of strategic industrial clusters will be significantly improved, promoting the digital transformation of more than 50,000 industrial enterprises above designated size, and driving 1 million enterprises to go to the cloud to reduce costs and improve quality and efficiency.
2022 is a year of full development of the digital economy, and it will also be a year for small and medium-sized manufacturing enterprises in Guangdong to accelerate their digital transformation.