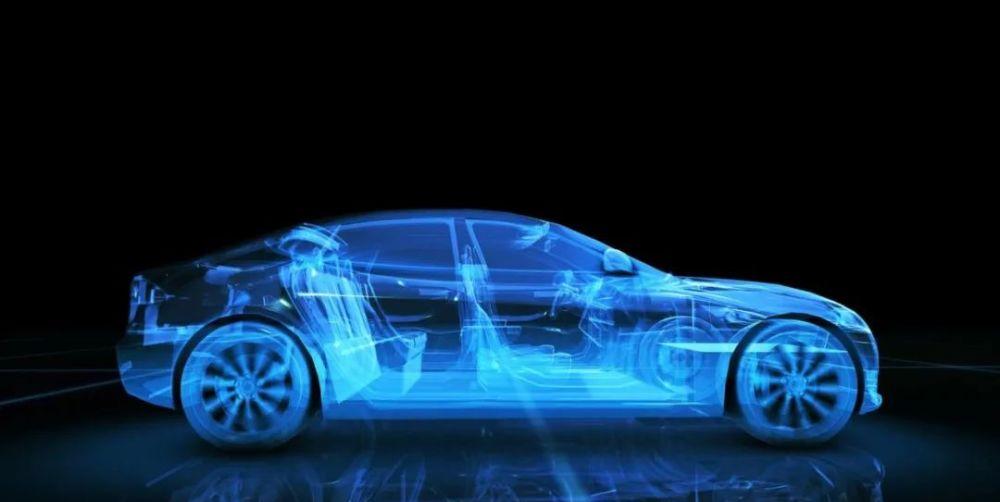
Wen/Zhang Dongsheng, Li Yanyun, Li Chao, Automobile Research Institute of Beijing Automobile Co., Ltd
The "Energy Saving and New Energy Vehicle Technology Roadmap 2.0" released the body lightweight technology roadmap, which plans the development direction of body lightweight in the next 15 years from the aspects of materials and processes. The Ministry of Industry and Information Technology, the National Development and Reform Commission, and the Ministry of Science and Technology jointly issued the "Medium- and Long-term Development Plan for the Automotive Industry", which clearly defined the development of advanced automotive materials and guided the automotive industry to carry out the application of high-strength steel, aluminum alloy, magnesium alloy, high-performance engineering plastic parts, and composite materials. According to the policy orientation and development route, the application of new materials and new processes cannot be delayed.
Figure 1 is the roadmap of lightweight materials in the "Energy Saving and New Energy Vehicle Technology Roadmap 2.0", according to the roadmap, it can be seen that in the near future (by 2025), the focus will be on improving the application system of high-strength steel, while increasing the application of lightweight alloys; in the medium term (2025 to 2030), the formation of a lightweight alloy application system will be the direction; and the long-term (2030~2035) will form a multi-material hybrid application system as the goal. Therefore, it is urgent to conduct in-depth research and application of 1.7GPa cold forming steel, 2.0GPa hot forming steel, and aluminum and magnesium alloy lightweight alloy materials.
Figure 1 Lightweight material roadmap
Figure 2 statistics of the 2020 European annual meeting 12 models of high-strength steel, aluminum alloy application ratio, 12 models, the proportion of high-strength steel between 34.7% and 70.2%, 7 models of aluminum alloy, the application ratio of between 0.5% and 11.3%, it can be seen that the application trend of high-strength steel and aluminum alloy is consistent with the planning direction of lightweight material roadmap.
Figure 2 2 2020 European Annual Meeting 12 models of high-strength steel, aluminum alloy application ratio statistics
In this paper, 8 kinds of forming processes were selected for process investigation, among which high-strength steel forming included 2.0GPa hot forming, hot air expansion forming, 3D roll forming, hydraulic forming, aluminum alloy forming including extrusion forming, high vacuum die casting forming, cold stamping forming, hot stamping forming, and the characteristics and advantages and disadvantages of 8 lightweight forming processes were analyzed. According to the promotion and application of the forming process at home and abroad in recent years, the development trend of lightweight forming process is obtained.
2.0GPa hot stamped steel
The hot forming process is to heat the blank to more than 900 ° C, keep warm for a period of time to organize all austenitic, and then quickly transfer the plate from the heating furnace to the hot forming press, quickly press on the press, and hold the pressure for about 10s, after the parts are all Martensitic, the hot pressing process parts are removed from the mold by the manipulator. 1.5GPa hot stamping steel has been widely used, 2.0GPa hot stamping steel is a new generation of hot stamping steel.
Compared with 1.5GPa press hardened steel, 2.0GPa hot stamped steel increases C content and increases V element. Element C is a solid solution strengthening element and an austenite stabilizing element, which plays the role of gap solution strengthening in martensitic, and the effect on martensitic strengthening is much greater than that of other replacement solid solution reinforced alloying elements. The mechanism of increasing the V element is the precipitation strengthening and fine crystal strengthening of VC, which improves the strength and plasticity.
Strengths and weaknesses analysis
The advantages of 2.0GPa hot forming steel are high strength, small rebound, and the hot forming process is basically the same as that of 1.5GPa hot forming steel, without the need for special production lines and tooling. The cost of 2.0GPa hot stamped steel is relatively high at this stage, and due to the increase in carbon content, the risk of hydrogen embrittlement is higher than that of 1.5GPa hot formed steel, and the dew point in the heating furnace needs to be strictly monitored.
Apply trend analysis
The main components of 2.0GPa hot stamped steel are A-pillar reinforcement plate, B-pillar reinforcement plate, seat beam and so on. BAIC has been mass-applied on the Lite door anti-collision beam of the new energy mass production model. At present, domestic and foreign models have begun to have mass production applications, but they are still in the application promotion stage, and the application trend is obvious. In the future, the amount of use will increase, the cost will be gradually reduced, and it is expected to replace the existing 1.5GPa hot stamping steel.
Hot gas flatulence forming
The thermometric expansion molding process is to heat the pipe or plate to a certain temperature through induction heating, so that the deformation ability of the material is improved, while the deformation resistance is significantly reduced, and then the pressure of the high-pressure gas is used to deform the blank, and then the air pressure is increased for shaping, as shown in Figure 3.
Fig. 3 Thermogastic expansion molding process
The advantages of the thermoflation molding process are high part strength (up to 2.0GPa), high material utilization, small rebound, controllable precision, variable closed section, high stiffness, and can reduce the number of parts and tooling. Applied to the A-column, it can effectively reduce the obstacle angle, improve the small offset collision and resistance to top pressure.
The disadvantages of the hot gas expansion molding process are that the mold cost is high, the cross-sectional change rate cannot be too large (the expansion rate < 15%), and it is difficult to directly process the installation features. Since the steel mill does not have finished pipes, the plates need to be processed into welded pipes. And first of all, pre-bending molding, and then hot gas expansion molding. Because the closed section is single-sided cooling, the cooling is slow and the production efficiency is low.
At the 2018 European Body Annual Meeting, the Wrangler demonstrated thermoflation tube beams, which extend from A-pillar all the way to D-pillars, forming a skeleton structure with a lateral upper girdle, as shown in Figure 4. Fox shows the upper beam of the thermoflation A-column, which combines the variable thickness plate to achieve the thickened thermostatic pipe beam A-column, as shown in Figure 5.
Fig. 4 Thermoflation molding parts of the Wrangler model
Figure 5 Thermoflation molding parts of Fox models
Linde Viemann of Germany took the lead in carrying out research on thermoflation technology, developed the ACCRA process, that is, the heating and air expansion molding and quenching process of pipe fittings, and developed anti-collision beams for Ford Mustang and Fox models. Sumitomo Heavy Industries of Japan developed the SATF technology of the hot air expansion process with welded edges in the cross-section and registered a patent, but no mass production application was found. At present, some foreign models have been mass-produced and applied, but there are fewer domestic suppliers and are still in the trial production and promotion stage, and the technology has a long-term application trend.
3D roll forming
3D roll forming can achieve up to 1700MPa martensitic steel parts production, hole processing requires laser cutting, the main production process includes online punching roll pressure high frequency welding shaping cut off 3D bending laser cutting.
The advantages of the 3D roll forming process are high part strength, closed cross-section, high stiffness, and can effectively reduce the number of parts and tooling. Applied to the A-column position, it can effectively reduce the obstacle angle of the A-column and improve the resistance to top pressure and small bias collision. Due to cold forming, the cost is relatively low and the material utilization rate is high. The disadvantage of the 3D roll forming process is that it must be an equal section, the design has limitations, the part is easy to rebound, and the accuracy control is difficult.
At the 2019 European Body Annual Meeting, the upper beam of the Ford Explorer A-pillar applied 1700MPa of 3D roll forming technology, which significantly reduced the obstacle angle of the A-pillar compared to the hydraulically formed A-pillar. This technology is mainly used in the Ford car series, and the independent brand is currently not a production application, because it is difficult to control the precision, and the future application trend is not significant.
Hydroforming
Process introduction
Hydraulic forming technology is to pretreat (end chamfering, deburring, elbow or pipe bend + pre-formed) after the fixed ruler pipe is placed in the mold cavity, inject high-pressure liquid into the pipe fittings at the same time at both ends of the pipe fittings for force feeding, so that the pipe fittings in the mold cavity constraints for mold expansion, until its outer wall and the mold cavity fit, forming the required various hollow parts, the process as shown in Figure 6.
Fig. 6 Pipe hydroforming process
The advantages of hydroforming are high part strength (up to 1000MPa); variable closed section, high stiffness, high integration, can reduce the number of parts and tooling quantity; can process a variety of materials, such as steel, aluminum, titanium alloys, etc.; high material utilization. The disadvantage of hydraulic forming is the higher cost of the mold. In addition, in the absence of finished pipes, the plate needs to be processed into welded pipes, and it needs to be pre-bent and formed, and then hydraulically formed.
At present, body hydroforming parts are mass-produced and applied in domestic and foreign models, and the future application trend is obvious. At the 2018 European Body Annual Meeting, Fox showcased the upper beams of the hydroformed front wheel cover.
Aluminum alloy extrusion forming
Extrusion is from the extrusion of aluminum casting rod, aluminum casting rod must be heated to soften before extrusion, and then the heated aluminum casting rod into the extruder's ingot barrel, by the high-power oil pressure to push the extrusion rod, the front end of the extrusion rod has a squeeze pad, so that the aluminum alloy that is heated and softened is extruded from the precision forming hole of the mold under the action of the extrusion pad to obtain the final product. According to the different extrusion directions, the extrusion process can be divided into: forward extrusion, reverse extrusion, and lateral extrusion.
The advantage of aluminum alloy extrusion forming is that the parts are closed complex sections, which effectively improve the stiffness and strength; the mold development cost is low, the cycle is short, the production efficiency is high, and the material utilization rate is high; it is applied to the front and rear anti-collision beams and the front longitudinal beam, and the energy absorption effect is obvious, increasing the passive safety of the body; the lightweight effect is obvious. The disadvantages of aluminum alloy extrusion forming are slow production and processing, many processes, limited structure, and certain limitations in application; difficulty in forming, poor consistency in pipe bending; and short mold life.
BAIC has applied aluminum alloy extrusion forming parts to many models. For example, the front and rear anti-collision beams of the fuel vehicle Beijing X7, the sills of the new energy vehicles Polar Fox αT and αS, the floor beams, the front and rear anti-collision beams, the front and rear longitudinal beams and other positions. At present, aluminum alloy extrusion formed parts have been applied in batches on domestic and foreign models, and the future application trend is obvious.
High vacuum die casting forming
Die casting process is the process of combining the three elements of die casting machine, die casting mold and die casting alloy and comprehensive application. It is a special casting method with less cutting, in which the molten metal is filled with molds at high pressure and high speed, and crystallized and solidified under high pressure to form castings.
The advantages of aluminum alloy die casting are to reduce the number of parts, highly integrated parts, reduce tooling costs, high production efficiency, simple process, save raw materials, and have obvious lightweight effects.
The disadvantages of aluminum alloy die-casting forming are poor casting precision, part accuracy is not high; casting parts are brittle compared to stamped parts, poor strength; cooling forming at high temperature, easy to appear stress concentration, parts have safety hazards; poor maintenance, due to high integration of parts, resulting in damaged parts replacement must be switched as a whole.
At present, body die-casting is widely used in front and rear turrets. It is also used in the rear stringer and D-column joint positions. For example, the Tesla Model Y applies two large cast aluminum parts to the rear of the car, integrating the front section of the rear longitudinal beam, the inner plate of the wheel cover, the beam in the rear floor, the rear floor rear beam, and other installation points. BAIC has applied aluminum alloy die-casting to the front and rear shock absorber seats of Jihu αT and αS, and the connection of rear stringers on new energy models. Aluminum alloy die-casting has been applied in batches at home and abroad, and the future application trend is obvious.
Aluminum alloy cold stamping forming
The manufacturing process of aluminum alloy cold stamped parts mainly includes plate production, natural aging treatment, stamping, manual aging and other processes, as shown in Figure 7.
Figure 7 Aluminum alloy cold stamping process
The advantages of cold stamping of aluminum alloy are obvious lightweight effects; can realize a variety of processes such as hemming and welding; are widely used in outer coverings, with good corrosion resistance; high surface quality and good gloss.
The disadvantages of aluminum alloy cold stamping forming are yield strength, low tensile strength, poor dentability; poor stamping formability, which has greater constraints on the structural design of parts, which is easy to cause neck shrinkage and cracking; serious stamping rebound, part design, stamping production and part matching are not easy to control; low hardness, easy damage to the surface, and higher requirements for production and logistics.
At present, the cold stamping of body aluminum alloy is mainly used in the body outer covering and the structural inner plate. For example, BAIC BJEV models Jihu αT and αS have a large number of applications in parts such as front and rear floors, front panels, cover inner panels, and back door inner panels. Domestic and foreign mass production models have also been widely used, and the future application trend is obvious.
Aluminum alloy hot stamping forming
The new technology developed in the past two years is similar to the hot forming technology of high-strength steel plate, combining heat treatment and hot forming, which is a hot solution forming for aluminum alloy materials - cold die quenching (HFQ) process, in order to obtain aluminum alloy parts with complex shapes and high strength.
First, the aluminum alloy blank is heated in the heating furnace (475 ~ 540 ° C / 30min), and then the blank is transferred to the cold mold to complete the stamping, and the pressure is held in the mold for a few seconds to complete the rapid quenching of the parts to room temperature, and then the artificial aging (160 ~ 420 ° C / 6 ~ 8h) significantly improves the strength of the parts by 15% to 20%.
The advantages of hot stamping of aluminum alloy are high strength and obvious lightweight effect; small rebound, high precision; good formability; and good corrosion resistance. The disadvantages of hot stamping aluminum alloy are long production cycles and higher costs.
At present, body aluminum alloy hot stamping is widely used in A-pillar reinforcement plate, B-pillar reinforcement plate, floor reinforcement and so on. Applied to aston Martin, Cadillac, Lotus Motors and other high-end models abroad, the country is still in the initial stage of promotion, WEI ES6 has begun to apply, with a long-term application trend.
Conclusion
This paper conducts research and summary on the content and application of new processes at home and abroad, and analyzes the development trend. 2.0GPa hot forming, hydraulic forming, extruded aluminum, die-cast aluminum, stamped aluminum technology is mature, the future application trend is more obvious. Hot air expansion molding and aluminum alloy hot stamping are in the initial promotion stage, with long-term application trends. Due to the technical characteristics and small supplier resources, the application trend of 3D roll forming is not obvious.
Zhang Dongsheng, senior engineer, mainly engaged in the research and development and management of body body, in 2021, completed the scientific research topics "Body Refinement Research and Application", "New Forming Process Development Trend and Feasibility Analysis of Parts", completed more than 40 research reports, 3 final reports, 2 papers, and 1 invention patent. He has won the titles of advanced employee of the hospital and "Top Ten Outstanding Young Engineers".
——Article excerpted from: Forging and Stamping, No. 2, 2022