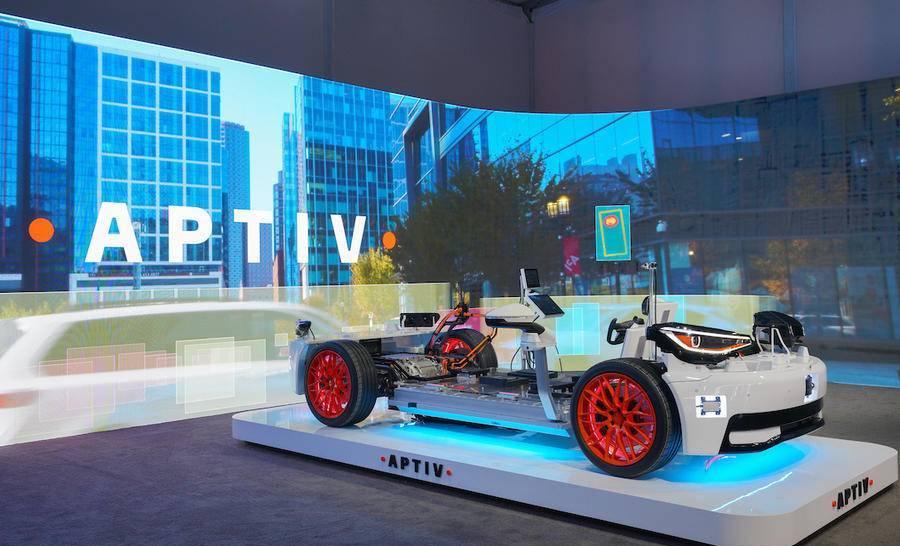
At this year's CES, Aptiv showcased a series of latest developments around SVA, and is bringing the future of cars and mobility into the real world through continuous technological innovation.
The launch of the Aptiv Intelligent Vehicle Architecture (SVA) design concept dates back to CES in 2020. Intelligent Vehicle Architecture (SVA) is an upgradable, open vehicle architecture platform that reduces total cost of ownership and facilitates mass production of feature-rich, highly automated vehicles. It is not a single product, but a layered architecture that provides a platform for automotive software innovation, greatly simplifying the entire vehicle architecture, and combining different applications with each other.
Under the SVA architecture, the development and upgrading of new functions has become easier and more efficient, improving the lifecycle management of the car and enabling OEMs to define the user experience functions they want to provide.
At CES, Aptiv unveiled a series of SVA-based developments. In particular, area controllers such as power data centers (PDCs) and vehicle central controllers (CVCs) have enabled SVA to be fully operational, supporting the implementation of software-defined vehicles.
One of the highlights of Aptiv's exhibition is the Central Vehicle Controller, or CVC for short. It is the latest system from Aptiv. As a key component of the SVA architecture, it is responsible for translating software code into physical action.
As a router for all data communication, CVC connects various devices in the vehicle in real time to handle the ordering and information scheduling of network traffic.
CVC is a key component of all advanced automotive architectures, especially suitable for the Zal architecture (partition architecture). In this application scenario, the CVC is the zone master, responsible for coordinating the operation of all zone controllers in the vehicle. PDCs still retain I/O, but most of the body control functions are located within the CVC.
In fact, CVC can integrate all functions such as power and body controllers, driver and chassis controllers, data network routers, gateways, firewalls, area masters, and data storage centers. That is, it can perform all these functions.
CVC also manages time synchronization, a feature that determines how effectively multiple systems in the car work together. By defining the network in CVC, expensive router hardware configured for other devices can be removed, further reducing the cost of the vehicle.
In the case of managing turn signals, when an application needs to turn on the left light, the CVC selects a specific area controller to communicate to send a flash signal, while managing the timing of all area controllers and isolating these details from the application. In hybrid networks, this approach ensures that more critical traffic, such as radar data, is transmitted in a timely manner.
In addition, in software-defined cars, a transport layer is needed that translates programming into car functions, just as a transport layer between the human brain and the nervous system translates the brain's decisions into action.
SVA middleware such as PDC and CVC is the bridge between signals and actions.
Aptiv also showcased its Open Service Platform (OSP). With an open domain control, Aptiv shows how OSP can improve the scalability of automotive features and functions.
These technological breakthroughs are enabling Aptiv and its vehicle customers to apply radar-centric solutions more widely, significantly reducing system cost and power consumption.
At present, the traditional automobile development method has become a major bottleneck in technological innovation.
Real-time response is a key consideration for automotive system development, not only for the safety of the car, but also for the user's perception.
Therefore, in general, engineers need to test the corresponding software on the hardware to ensure that the operation of the software will not be affected by changes in the operating environment, so the time required for testing is also extended by the need to assemble the corresponding hardware.
As software is used more and more in the automotive, continuous integration development methods are gradually being introduced in the development of automotive systems.
Aptiv's successful development of an Android version of its in-car infotainment system for Volvo in collaboration with Google and Volvo is a good example of continuous integrated development. The platform was first applied to the Polestar 2 and then extended to models such as the XC40.
In addition to an excellent user experience, the development process of this open infotainment platform reflects a high degree of collaboration and mutual achievement between the project's partners (Volvo, Google and Aptiv). At one end of the development is Google's headquarters in Silicon Valley, USA, and at the other end is Volvo Cars' headquarters in Gothenburg, Sweden. These two ends also represent two different industries: automotive and technology.
With the demand for higher range, batteries are getting bigger and bigger, which means that charging power needs to be increased. As a result, battery technology is steadily moving towards high-voltage systems.
Aptiv's charging guns and charging plugs meet fast charging needs – whether ac or DC.
The key to increasing the charging speed is to manage the heat to be compatible with higher currents. Aptiv's charging systems measure the temperature of the connection nodes and use this data to actively optimize the charging cycle. Aptiv's modular, serviceable charging jacks integrate active cooling channels to extract heat to support high voltages and fast charging.
Apfort uses the first-on-the-market direct contact technology to increase the current intensity from 200 amps to 500 amps, charging up to 5 times faster than existing products.
Battery life and cost are another major challenge for electric vehicles. At present, the best way to improve battery life is still to reduce the weight of the car. Aptiv offers a range of lightweight solutions for this purpose.
The Aptiv high-voltage system uses a flat busbar as a conductor, which is not only robust and flexible, but also reduces the height by about 70%, thus taking up less battery space, which not only helps to load more battery packs, but also helps to dissipate battery heat. In addition, compared with the soft cotton wiring harness, the flat busbar is more conducive to automated assembly, which is conducive to improving the level of automated assembly.
Aptiv's unique 4-way junction connector adopts a conventional equipment connection system and can also be used as a connection board, which effectively reduces the number of vehicle connectors and corresponding cables, and makes cable routing more efficient.
Aptiv's wiring harness portfolio is also centered on optimizing the vehicle system, helping the vehicle to optimize harness assembly, improve wiring, and improve the level of automated assembly.
Aptiv is uniquely positioned to help vehicles optimize vehicle systems for more efficient and scalable eviction architectures by reducing system complexity and applying its "Smart Vehicle Architecture".