At the Shanghai Auto Show in April this year, Jihu showed off its Alpha S Huawei Hi version model in cooperation with Huawei, and tested its L3 level automatic driving capability on the real car road, which made many people interested in the brand.
ARCFOX Is a brand new brand of BAIC BJEV, focusing on high-end; two models on sale are currently available, including the Alpha S and Alpha T.
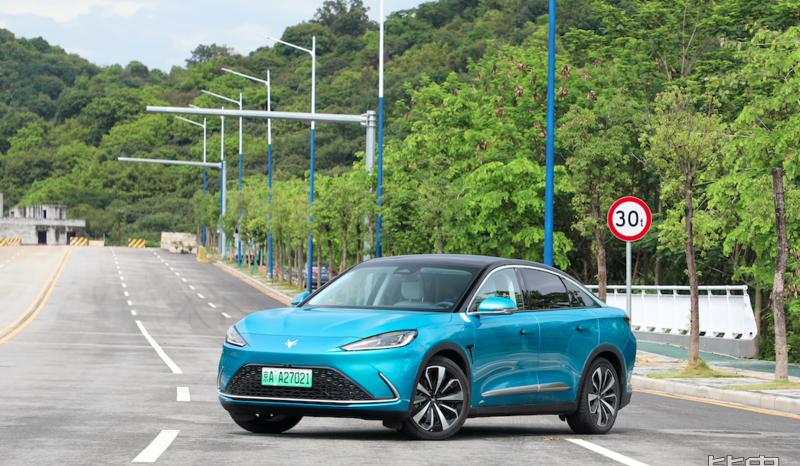
In addition, if you have a friend who pays attention to this car, you may notice that its tail tag is a bit strange, hanging is the Blue Valley Magna, which can make many people feel dazed.
In fact, arcfox models are manufactured by Magna, which is the first time Magna has opened a complete vehicle manufacturing plant outside of Europe. In addition to being a well-known parts supplier, Magna is also involved in vehicle manufacturing and development, with more than 100 years of experience and history in high-end automobile manufacturing, manufacturing more than 3.7 million luxury models.
The well-known Aston Martin, Mercedes-Benz G-Class, BMW 5 Series/Z4, Toyota GR Supercar, MINI Countryman/Paceman, Peugeot RCZ, Jaguar I-PACE/E-PACE and many other luxury models are mainly supplied by Magna and assembled and produced at Magna's Graz, Austria.
Therefore, the cooperation between BAIC BJEV and Magna is also a new model in China. In the "new joint venture" model between BAIC and Magna, BAIC values Magna's century-old experience in vehicle manufacturing and engineering, the development process of electronic and electrical architecture, and lightweight technology. So where is the advanced nature of the Magna factory, and The Electric Brother has the honor of being invited to visit and unveil the mystery of the factory.
Factory overview
Beiqi Blue Valley Magna high-end intelligent manufacturing base is located in Dantu District, Zhenjiang City, Jiangsu Province, automotive ecological industrial park, is a high-end new energy vehicle manufacturing joint venture joint venture jointly built by BAIC Group and Magna, with a total investment of 6 billion yuan, covering an area of about 1.37 million square meters, with a planned total production capacity of 300,000 vehicles / year, is the production base of ARCFOX Jihu series models, and will be open to other customers in the future, providing electric vehicle research and development and vehicle manufacturing services.
1. Stamping workshop
The stamping workshop is the first step in vehicle manufacturing, and the Magna plant has now completed the stamping A line, which is a fully enclosed, high-speed automated production line that can realize the mixed production of steel and aluminum.
The production line consists of a 2400T, a 1200T, three 1000T with a total of 5 presses and a fully automated transmission system composed of a swiss GUID single-arm crossbar manipulator.
Mainly responsible for the production of large and medium-sized stamping parts of the body such as side walls, fender plates, door covers, etc., with four major characteristics, one is fast, the press continuous mode can reach 12SPM (number of punches per minute / number of strokes); second, the whole line realizes automatic replacement of sheets, automatic replacement of molds, automatic transmission of stamping scrap; the third is strong, which can meet the stamping production of different materials such as non-galvanized steel plates, galvanized steel plates, laser welded plates, aluminum plates, etc.; fourth, the provincial, high-speed synchronous continuous line, which is 15%-20% energy-saving than the traditional intermittent line.
In terms of product qualification rate, the stamping workshop has a total of 40 self-made parts (including 15 aluminum parts), according to the MAFACT system standards, from the material to the final product, from appliances to equipment, all-round in-depth control, so as to achieve a pass rate of 97%, most OEMs The indicator is about 90%.
2. Body workshop
Magna factory has the first 30JPH steel and aluminum mixing production line in China, a fully automated production line composed of 290 German KUKA robots and 206 sets of connecting equipment, and is the first 30JPH (30 production capacity per hour) steel and aluminum hybrid body production line in China.
In the scene, the electric brother also saw a lot of German KUKA robots, which is known as the first of the four major families of robots in the world, which can achieve high-precision positioning at the millimeter level, the highest control accuracy, and also avoid the drawbacks of manual operation, process consistency can not be perfectly guaranteed. Kuka robots can be found on the production lines of luxury brands such as Mercedes-Benz, BMW, and Porsche.
The automation rate of all connection points (riveting, welding) reaches 100%, the automation rate of gluing reaches more than 95%, and the riveting process affects the stability and consistency of various parts of the car. According to reports, the current domestic one-time pass rate level is basically around 95% to 97%, and the intelligent manufacturing base in accordance with the MAFACT standard has now reached 99%, and is moving towards 100%.
3. Painting workshop
In the process of the painting workshop, Magna adds an additional effect pigment coating in addition to electrophoresis, color paint and varnish, so that the body color is more vivid and layered. The overall coating process allows the paint to have better durability and protection, and the corrosion resistance can reach more than ten years.
Coating part, it adopts LASD water-based damping coating, which is formulated by adding an appropriate amount of filler and auxiliary materials to the polymer resin, which has better noise reduction performance and better adaptation to the thermal expansion and contraction needs of different steel and aluminum structures compared with traditional coatings.
The paint part is selected with the PPG brand paint used in Mercedes-Benz, BMW and other luxury models.
In the spraying operation, a total of 52 ABB high-performance robots, fully automatic conveying system, the use of circulating air, RTO (regenerative thermal incinerator) waste heat recovery, hot and cold water integrated machine and other process technologies to reduce energy consumption. While using exhaust gas heat energy recovery, the removal rate of exhaust gas organic matter reaches more than 99%.
In addition, it also has a quantitative wax injection process, which accurately controls the amount of wax injection in different models and different positions to ensure that the anti-corrosion wax can completely cover the inner cavity area to improve the anti-corrosion performance of the body.
4. Final assembly workshop
In the final assembly workshop, we also saw Magna's different approach, in the conventional situation, the main line is moving, the operators move with the main line, and pick up materials along the way for assembly.
In this mode, because workers will inevitably consume a certain amount of time when they pick up materials back and forth, which will affect production efficiency. Static assembly technology through the use of materials and vehicles in reverse simultaneous movement, in the mobile production line, to create a stationary station, to achieve complex process assembly, thereby minimizing the personnel in the material and walking around the non-value-added assembly time, while greatly reducing the labor intensity of workers.
The static assembly concept originated from Magna, which is the first time in the mainstream OEMs in China that this linear structure form has been adopted. The biggest advantage of this technology is that it improves the quality of assembly, reduces the fatigue strength of workers, and is suitable for a variety of scenarios.
The most important thing in the final assembly workshop is the consistency and stability of the assembly, magna factory has online real-time monitoring of vehicles, automatic reporting of vehicle positions, automatic identification of key processes, automatic tightening. The key equipment of the chassis automatically measures and automatically adjusts to the qualified range, and at the same time can be automatically calibrated and calibrated at regular intervals.
In addition, the current electric vehicles have advanced driving assistance functions, the calibration of these induction components in the factory settings is crucial, this factory has advanced driver assistance ADAS calibration table, in order to cooperate with L2.5 level driving assistance, through the independent ADAS calibration table, set HUD head-up display, MRR forward detection millimeter wave radar, MPC forward camera one-stop automatic calibration, replacing the traditional four-wheel station calibration, improve production cycle and efficiency.
In order to achieve L4 advanced driver assistance, the one-stop calibration table of the new redundancy concept can realize the automatic calibration of lidar, millimeter wave radar, gyroscope, and camera at the same time, and the whole process does not require manual participation.
5. Battery PACK workshop
The battery used in the Polar Fox model is an SK battery module, and its battery cell will be assembled into an AR battery pack module through 20 processes. The energy density is as high as 194Wh/kg, while the Tesla Model3 is only about 160 Wh/kg.
It has a 53% automatic rate across the line, including automatic on-line of modules, automatic detection, gluing, cleaning, module installation, fixing, FDS riveting process and so on. Through high automation, the precision and consistency of the overall process are guaranteed, as well as higher production efficiency.
Magna's MAFACT system
MAFACT is Magna's manufacturing operations management system, one of its two core systems, dedicated to the cost-effectiveness of high-quality products, the continuous improvement of all processes and the maintenance of core competencies. This world-class standard system has hatched a number of luxury models such as Mercedes-Benz G-Class/M-Class, BMW X3/5 Series, Chrysler 300C, Jaguar, etc., representing the strongest strength of European century-old automobile manufacturing.
In this factory is also the introduction of the MAFACT standard system, it is divided into 8 sections, namely: safety, health and environmental protection, quality, manufacturing excellence, material control and logistics, engineering design and pre-quality planning, management, human resources, cost; each plate has different goals and tools, through the application of lean tools to achieve the corresponding goals, and then the overall realization of SQTCM (safety, quality, timeliness, cost, incentive) business indicators, so that customers are satisfied, employees are satisfied, shareholders are satisfied and partners are satisfied to achieve world-class manufacturing.
In addition, Magna also has special arrangements for staff training, and all employees who join the Beiqi Blue Valley Magna high-end intelligent manufacturing base will have the first lesson of MAFACT training.
Using lego-like building blocks to simulate the production site, the trainees play the role of production personnel, logistics personnel, quality personnel, warehouse personnel, the red, blue, green three kinds of building blocks into a complete product, delivered to customers. After all these steps are completed, the results are recorded in the KPI form as the team's first phase of performance. Through all the people talking and continuous improvement, gradually integrating the MAFACT concept, tools and methods, and then proceeding to the second and third rounds. Through a fun and educational approach, this training allows everyone to better experience how MAFACT improves quality, efficiency, cost KPIs and operations management performance.
In the scene, the electric brother also personally experienced such a training, the whole process is still relatively easy to understand, but also reflects the advanced nature of the MAFACT system.
Write at the end
After the rise of new energy vehicles, many new car-making forces are produced through OEM production, so the OEM production of Jihu Automobile seems to be no different, in fact, the difference is still relatively large.
Many of the foundries of the new car-making forces are temporarily rectified, using existing factory machines for production, and the production process, precision and advanced nature of the machines are very different.
The Magna plant is specially built for partners, and the adaptability and advanced nature of the model are guaranteed, so this cooperation between BAIC and Magna will be more scientific and reliable.