Author: Cooper
Editor: Kou Jianchao
Typography: Li Xuewei
If the robot can perform the same functions as the human hand, it can have a high degree of flexibility in performing the task.
However, while maintaining important functions such as human-like dexterity and grip, it was a challenge to develop integrated robotic hands that did not require additional drive components. Because the drive components make it difficult for these robots to integrate into existing robotic arms, their wide applicability is limited.
Now, a new solution has arrived, and a team of scientists from South Korea has developed a dexterous anthropomorphic robotic hand with integrated linkage drive based on the linkage drive mechanism, called ILDA, which has 15 degrees of freedom (20 joints), 34N fingertip force, compact size (maximum length: 218 mm), no additional components, low weight and haptic sensing capability of 1.1 kg.
It's worth noting that the robot can be mounted directly onto existing commercial robotic arms and perform a wide variety of tasks — from clutching eggs to using scissors and forceps , a paper published in Nature Communications.
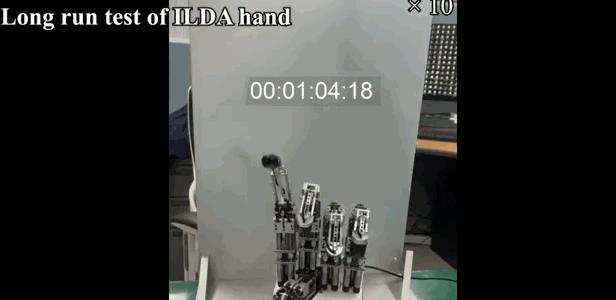
Figure | ILDA Robotic Finger Flexibility Demonstration (Source: Nature Communications)
The robot solution complements each other's strengths
In order to achieve effective grasping movement, the industry has actually developed a lot of relatively dexterous anthropomorphic robotic hands, they can adaptively grab some objects. In this paper, the researchers focused on the analysis and development of multi-degree of freedom hands with high dexterity, and the representative core elements of the dexterous robotic hand are divided into the following aspects: direct motor drive, tendon drive, and connecting rod drive mechanism.
The hand developed based on the motor's direct drive mechanism is a common structure that intuitively positions the motor relative to the joint, directly or using a gear or timing pulley to drive the joint. This structure can have a high joint drive efficiency and easily place the joint in the desired position.
Pictured| MPL robotic arm developed by Johns Hopkins APL Labs (Credit: Johns Hopkins University)
In terms of specific cases, the MPL v2.0 robot manual, developed by Johns Hopkins APL Labs, has demonstrated high dexterity, an active type with 22 degrees of freedom, and a compact design, integrated actuators and electronic devices capable of natural motion and haptic feedback at the human level. However, the size and performance of the hand is highly dependent on the motor, especially the finger part, the use of high-end specifications of the motor or drive force transmission components will increase the cost, in addition, due to the weight of the motor, the inertia at the finger is very high, so the need for complex control mechanisms, without the innovation of actuator technology, it is difficult to achieve compact, lightweight and high performance.
Picture | Shadow Robot robot (Source: Shadow Robot)
The hand based on the tendon drive mechanism is most similar to the human hand drive mechanism. Typically, their actuators are located on the forearm and connected to joints through tendons to transmit driving force, and the robotic hand developed by NASA, the David hand developed by DLR, and the Shadow dexterous hand developed by Shadow Robot can be seen as representatives of having such an mechanism, which is a method that is very suitable for developing a single humanoid robot, but the actuators and electrical components of such robotic hands are quite large, and it is difficult to combine these robotic hands with many existing commercial robotic arms.
Connecting rod drive mechanism is a mechanism commonly used in our daily life. The hand developed on the basis of this mechanism promotes the movement of the joint in the desired direction through a structure that combines multiple connecting rods to transmit power from the actuator, which has the advantages of two-way control of the joint, robustness, and ease of manufacturing and maintenance. However, they have a hard time achieving multi-degree-of-freedom movement and maintaining a large working space, especially in tandem robots such as fingers. The tendons are thin and flexible, so each joint can be driven independently by a rotating shaft, but the connecting rods are relatively thick and stiff, making this configuration difficult to achieve.
Through an analysis of existing robotic hand solutions, the researchers concluded that robotic hands must have the following advantages: flexibility, fingertip power, controllability, robustness, low cost, low maintenance, and compactness. In addition, all components should be embedded in the hand itself and include all of the above functions, thus developing a dexterous anthropomorphic robotic hand (ILDA) with integrated linkage drive.
Figure | an overview of the ILDA, the configuration includes five robotic fingers with fingertip sensors, palm side of an integrated actuator, and controllers and accessories (Source: Nature Communications)
The new scheme is constructed through the fusion of parallel and tandem mechanisms, and realizes the 2 degrees of freedom movement of the metacarpophalangeal joint (MCP) and the 1 degree of freedom movement of the proximal interphalangeal joint (PIP) through the combination of connecting rods, and the selection, placement and configuration of small parts that can play the role of each joint to achieve the desired degree of freedom of motion and drive angle, as well as an efficient power transmission structure for high fingertip force and its subsequent drive capability. By attaching a six-axis force/torque (F/T) sensor to your fingertip, you can ensure the force sensing ability of your hand. Using the designed fingers, the researchers developed a five-fingered robotic hand with 15 degrees of freedom and 20 joints.
Figure | structure of the robot's finger (Source: Nature Communications)
In practical applications, it is built by solving board layout and routing problems, ensuring the compactness of electronic devices. All motors are integrated in the palm of the hand, have five finger and fingertip sensors, and can be easily attached to a general robot arm with a simple connection configuration.
In experiments, this new robotic hand has the possibility of grasping objects of various shapes, providing a powerful grip and ensuring fineness when grasping. Finally, through the use of scissors to cut paper and experiments with tweezers to pick up small objects, the high utilization of the hand was verified, replicating the tool operations performed by hand in daily life.
Figure | ILDA robotic hand flexible grip capability (Source: Nature Communications)
Performance takes to the next level
The researchers did some analysis of ILDA robotic robot performance. In terms of linkage drive mechanism, the key to the design is to implement a connecting rod-driven robot finger mechanism with 3 degrees of freedom movement similar to that of a human finger, with a narrow finger-sized workspace to ensure the dexterity of the robot hand.
Most connecting rod-driven robotic fingers achieve only 1 or 2 degrees of freedom movement dependent on two joints, and through linear displacements at three prismatic joints, the researchers developed a combination of 3 degrees of freedom movement of the fingers, which produce three linear displacements through the combination of a rotating motor and a ball screw, and the three motors can simultaneously produce three degrees of freedom motion and produce a high force output.
Figure| kinematic structure of the finger mechanism of the machine (Source: Nature Communications)
To achieve the set target requirements, the researchers mainly considered the following factors: (1) selecting and configuring parts of the right size to achieve the desired degrees of freedom movement: Implementing the functions of the above kinematic model in a narrow space in the shape of a finger should be properly arranged in the configuration of the model. Therefore, it is important to choose the right size of the widget from a design point of view. (2) Efficient power transmission structure to minimize friction between assembled parts. In order to obtain a high fingertip force, a compact structure is required while minimizing the friction of the power transmission section. (3) Easy to manufacture and assemble. In order to increase the market penetration of developed manipulators, it is also important to evaluate them in terms of cost and maintenance. Therefore, it is very important to design a simple, robust robot structure.
Figure | detailed dimensions of the robot (Source: Nature Communications)
Finally, all power transmission components and motors are integrated into the palmar side of the hand, five F/T sensors are mounted on each fingertip of the configured finger parts, the sensor wiring is complete so that it does not interfere with the movement of the fingers, and finally, this integrated robot with a maximum length of 218 mm and a weight of only 1.1 kg is developed.
To verify the performance of the ILDA hand, the researchers assessed it from three dimensions: (1) dexterity within the workspace; (2) fingertip force; and (3) tactile perception.
In experiments, the MCP connector can be driven from 0° to 90°, the PIP connector can also be operated from 0° to 90°, and in addition, the PIP connector can operate independently of the MCP connector, with finger abduction and adduction angles of ±35°.
Figure | performance analysis (Source: Nature Communications)
The size of the contact force at the contact point is determined by the fingertip sensor and the same force is applied to the fingertip and the reference sensor, and the force applied by the finger is increased sequentially, while the 25 mA current is increased every 2 seconds, and the maximum force applied by this finger is 28 N in the extension position and 34 N in the bending position, verifying the accuracy of the static force applied by the finger, with an average error of 0.9 N. Responses are generally well-matched, with no critical errors, and great potential for force control when performing delicate tasks.
Figure | robot for various grip tests and fine operations (Source: Nature Communications)
During the test session, the developed hand was used to pinch the flattened aluminum can, at that time the maximum force measured on each finger was 25 N; the egg could also be grasped safely with this hand without crushing; in order to confirm the possibility of using the robot to manipulate the tool, the paper-cutting experiment was carried out by connecting the hand with the commercial manipulator, since paper-cutting with scissors in daily life is a task that requires a high degree of dexterity.
The last test involves clamping and moving small objects with forceps, the manipulator moves so that the tip of the forceps is able to hold the chiplet, the hand performs a gripping action, the forceps peel off the lid of the chip and grab the chip, next, move the object to another position, loosen the forceps to complete the operation, and everything is done smoothly.
Figure | robot clips the chip with tweezers (Source: Nature Communications)
Lower the barrier to entry for commercial applications
The researchers say that the unimpeded anthropomorphic manipulator based on the linkage drive mechanism ensures the original advantages of the linkage drive mechanism, such as two-way control of joints, robustness, and ease of manufacturing and maintenance, while at the same time, it ensures 15 degrees of active movement with 20 joints, sufficient working space between fingers, and higher fingertip force, which is also smaller in weight, compact in size, and provides room for sensor integration.
The ILDA robotic hand can be easily attached to an existing commercial robotic arm or a robotic arm under development without the need for additional components, with the key advantage being that the hand exhibits high performance and the part configuration is combined with the hand itself.
This robot can perform different types of gripping depending on the shape of different objects. Scissors and forceps are used to determine the likelihood of operating a tool in everyday life, and while it is difficult to quantify exactly how effective the hand is when operating a tool with scissors, they use multiple degrees of freedom of the hand and perform combined movements through bidirectional control of the joints.
The development of dexterous anthropomorphic robotic hands with ultra-high degrees of freedom remains an open question that requires ongoing research from a scientific and engineering perspective. But in this study, the researchers tried to maximize the robot's performance in all dimensions.
So far, the industry has developed many relatively dexterous robot hands, but due to the complex manufacturing process and maintenance difficulties caused by the high cost limits their commercial use, and the applicability of this ILDA robot hand, through the comprehensive optimization of functions and costs, can be extended to the actual research field and many industry applications, to promote the further research of the robot hand.
Such a flexible robot hand, can it be used on people in the future to help the disabled complete some daily operations? We'll see.
Resources:
Click here to follow I remember the star ~