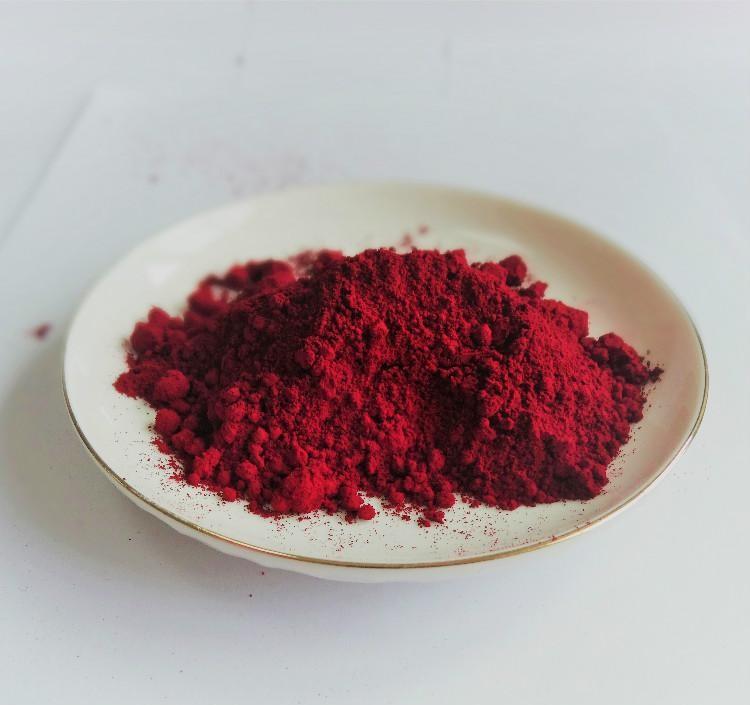
Plastic coloring, generally in the plastic in a hot melt state, coloring time is short, high processing temperature, so the colorant in a certain processing time, to be able to maintain the stability of color, and can be uniformly dispersed or dissolved into the plastic, after the molding coloring, the color of the product can have excellent light stability, migration resistance, weather resistance, solvent resistance and chemical resistance and other fastness properties, so not all colorants can be applied to plastic coloring, It is necessary to make an appropriate choice through experiments or with reference to the experience summarized by predecessors
In general, the main properties of the colorant used in plastics are: strong coloring power, bright color, good stability and reproducibility, good compatibility, good dispersion, and the colorant can be uniformly dispersed or dissolved in the plastic, so as not to cause color spots or stains. Here are a few highlights.
(1) Lightfastness. Because the coloring of plastic products in a long period of light, may cause a change in color, so should be selected according to the use of the product colorant with good lightfastness, the daily use of colorants generally require its lightfastness is not less than 5 levels (8 levels is the best), in the outdoor or long-term leakage in the outdoor products, coloring lightfastness requirements in 7-8 levels.
(2) Heat resistance. Different plastics have different processing temperatures, colorants under the action of high temperatures, may produce thermal decomposition, oxidation, causing the destruction and modification of molecular structure, resulting in discoloration or discoloration and other chromatic aberration phenomena, so the colorant has a certain heat resistance indicators, in the selection must be paid attention to, generally according to the processing temperature of the plastic varieties used to select the colorant. It should be pointed out that in the product information provided by the colorant manufacturer, the heat resistance index is not necessarily determined in the plastic coloring process, so there are also individual cases in which the heat resistance index of the colorant is low, but in fact it can still be applied to plastics with higher processing temperatures.
(3) Compatibility. Good compatibility means that after the plastic colorant is mixed into the plastic, it can coexist with the plastic composite components without producing adverse results. If the colorant reacts with the plastic, or if a chemical reaction occurs between the colorant and the catalyst remaining in the plastic, the processing aid in the plastic, the compatibility of the colorant with the plastic is not good, which will change the color of the plastic.
(4) Migration resistance. The migration of coloring in plastic refers to the fact that over time, the color of the processed coloring product is transferred from the colored part to the plastic part or other object at its junction, or the colorant precipitates from the inside of the product and concentrates on the surface of the plastic product (easy to be wiped down and causes pollution), and the phenomenon of colorant migration is common in polyethylene, polypropylene, soft polyvinyl chloride and other plastic products, and its generation is related to the type and dosage of the colorant selected.
(5) Non-toxic. In food packaging, children's toys should be used non-toxic colorants, generally containing rhodium, cadmium and other heavy metals of inorganic pigments are usually considered toxic, so some countries have made strict regulations on their application.
For your reference, the performance of commonly used plastic colorants that are more used in actual production is introduced below.
1. Pigments
Pigment is a solid substance with color, it is insoluble in water and general organic solvents, pigments are uniformly dispersed in the form of particles in the object or mixed with different color spreading agents, so that the object presents a variety of colors, pigments according to its composition can be divided into inorganic pigments, organic pigments and special pigments three categories.
Inorganic pigments are generally a class of insoluble colorants composed of salts (such as chromium yellow, molybdenum chromium red, ultramarines, etc.) and oxides (such as iron oxide yellow, iron oxide red, cadmium red, chrome yellow, titanium dioxide, etc.), sulfides, mercurides and black carbon, including iron, aluminum, zinc, chromium, titanium dioxide, etc.).
Inorganic pigments have good hiding power, other coloring intensity is higher, inorganic pigments generally have excellent thermal stability, chemical resistance and light stability, the disadvantage is that the ratio is significant, the color is not bright enough.
Organic pigments are insoluble in water and general organic solvents, coloring is stronger than inorganic pigments, organic pigments are brightly colored, from transparent to translucent, the proportion is small, in addition to some excellent varieties, most organic pigment varieties of thermal stability, light stability, migration resistance, chemical resistance and weather resistance are worse than inorganic pigments. According to the chemical structure of its molecules, organic pigments can be divided into azo pigments (including danazo, azo lake, dipazole, condensation azo), phthalocyanine pigments, reducing pigments, dioxazine pigments, isoindole ketone pigments, quesinone pigments and the like.
Special pigments mainly include metal pigments, pearlescent pigments and fluorescent pigments.
Metallic pigments such as aluminum silver powder is silver white fish scale silver powder, can produce blue and white bright light, has excellent hiding power, and has excellent thermal stability, weather resistance; and copper gold powder is a copper alloy pigment with metallic luster, according to the different copper and zinc components, can be made into different shades such as blue light, red light, blue red light, etc., often used for imitation gold, imitation copper, antique copper color and other plastic coloring, aluminum silver powder and ketone gold powder in the actual production of the color will become darker and not as bright as the original. The metal silver sheet sold on the market is also a class of metal pigments, it is made of aluminum foil through precision cutting, the commonly used varieties are 004 silver sheet, 008 silver sheet, 015 silver sheet, etc., the silver sheet added to the plastic will form a scattered little by little metal color point, very beautiful.
Pearlescent pigments are a layer of high refractive index transparent metal oxides with a tightly controlled thickness on the surface of transparent mica sheets, such as titanium dioxide, iron oxides, etc. Adjust the thickness of the coating layer to make pearlescent pigments with different rainbow colors, and the particle size of the pigment can show a shimmering metallic luster.
Fluorescent pigments refer to those used as colorants, with a strong fluorescent effect of the pigment, fluorescent pigments are generally divided into organic fluorescent pigments and inorganic fluorescent pigments, in plastics more use of organic fluorescent pigments, with the increase in the concentration of fluorescent pigments fluorescence intensity also increases, inorganic fluorescent pigments have a kind of light storage pigment, commonly known as luminous powder It has the ability to absorb and store sunlight or light, and release visible light in the dark, Its absorption ------ storage ------ the cycle of luminescence can be repeated countless times, and the light color emitted is yellow-green, which is easy for the human eye to identify, but the proportion of inorganic fluorescent pigments is heavy. Generally, the proportion of plastics added to plastics is 10% to 40% (mass fraction)
2. Dyes
Dyes are generally soluble in water or certain organic solvents and the medium of their colored plastics, and some dyes may be soluble with the help of appropriate chemicals. Since the dye is dissolved in the plastic, the colored transparent plastic still maintains its transparency. The main characteristics of fuel colorants are good transparency, bright colors, and strong coloring power, but because of the complete mobility, their application in some plastics (such as soft polyvinyl chloride containing plasticizers, polyethylene, polyenejing) has been limited, and he can only be applied to plastics that do not migrate.
The varieties of dyes commonly used for plastic coloring are mainly solvent dyes and some raw materials and disperse dyes with good solubility. The purity of the dye for plastic coloring should be high, and the presence of diluents or diffusers and other impurities should be avoided, so as not to affect the transparency and coloring effect of the plastic, so the vat dye and disperse dye should use pure dyes as plastic colorants.
Solvent dyes according to the chemical structure of the molecule can be divided into azo, anthraquinone, indigo thio and heterocyclic, etc., in general, dyes based on the chemical structure of diazo, the color is mainly yellow, orange and red, anthraquinone or phthalic chromophore dye, the main color dye is fluorescent yellow, orange, and red, the thermal stability, lightfastness and weather resistance of anthraquinone dyes are more excellent than those of azo dyes, and the heterocyclic dyes are better than those of indigo dyes.
3. Plastic coloring method
Plastic coloring refers to the process of mixing and dispersing a certain amount of pigment by uniformly mixing and dispersing the plastic with the natural color, so that it is evenly dispersed in the plastic, so that the plastic as a whole gets a uniform color.
Commonly used plastic coloring methods are dry coloring, paste colorant (color paste) coloring, color particle coloring, masterbatch coloring, etc. The following mainly introduces the widely used dry coloring.
Dry coloring refers to the powder colorant and auxiliary according to the proportion of the formula accurately measured, added to the plastic measured by the formula, in the presence of appropriate dyeing aids such as white oil, turpentine, so that they are evenly mixed, and then the mixture is directly sent into the molding equipment for injection molding or extrusion processing, so as to obtain a method of colored plastic products, although dry coloring has the disadvantages of easy to pollute the environment, poor dispersion effect, etc., but it is simple and easy, relatively low cost, easy to formulate a variety of colors, It is particularly suitable for the production of small batches of multiple colors, because the method is not as easy to be limited by the color of masterbatch varieties like the masterbatch coloring method, so it is still widely used in many small and medium-sized plastic processing plants.
Dry coloring requires good mixing, and more efficient mixing equipment such as paddle mixers, rotary drum mixers, slurry kneading mixers, etc. can be used. In the small factory with poor conditions can also be in a certain container, the metered colorant and plastic plus white oil and use manual methods to mix evenly, for dry coloring, some formulas may be due to the dispersion effect of the colorant in the production is not ideal, there are color spots, color spots defects, such as with carbon black dyeing gray may appear black spots, for this reason the author recommends the use of color particle coloring, that is, the mixture obtained by the dry coloring method is extruded into granulation and made into color particles, so that the coloring effect will be greatly improved, However, the cost has increased due to the increase in co-promotion.
Dry coloring requires that when measuring the colorant, it should strive to be accurate, otherwise it will produce color difference, it is recommended to use an electronic balance with an accuracy of 0.01g and a maximum weighing capacity of 500g as a measuring tool for the colorant, and the weighing error is minimized as much as possible.
For dry coloring, when changing colors, the metering container, injection molding machine hopper, mixing equipment, etc. should be cleaned well, otherwise the residue will affect the purity of the color, resulting in color difference.
4 Plastic coloring formulation process
Plastic color matching is currently the most artificial visual color matching method. Color matching personnel in a certain light source through the color matching sample or color card sample plate for visual analysis, conditionally in the reference to the existing color plate samples, according to the use of plastic varieties, select the appropriate colorant varieties and dosage, designed 250g (or selected quality) plastic with the preliminary formula. The sample is processed by injection molding according to the preliminary formula, and the sample is compared with the color matching sample. After many trials and errors, the required formula was obtained. This work requires great patience and rigorous and meticulous work of color matching workers, that is, from the accurate recording of each weighing, the number preservation of each injection molding swatch, to the final confirmation of the test formula converted into a production formula used in 25kg of plastic, can not be sloppy, otherwise, the resulting formula is used in production, and the color will appear large color differences.
In the process of matching, when visually comparing the made color plates and samples, the factors that affect the accuracy of visual inspection and the accuracy of color matching are mainly as follows:
(1) Light source, visual inspection of the light source is best to use natural light, conditional can use the standard light source box, so more realistic, otherwise in some lights to compare the color of the observation of 2 samples may be because of the "homochromatic spectrum" phenomenon and make the color seem to be the same, but in the natural light there is a large color difference.
(2) The surface state of the sample, for example, on the same plate, the color of the high-gloss surface and the matt surface obviously gives people a different feeling, so it is necessary to compare it with parts with similar surface states as much as possible.
(3) The material of the color matching sample is different from the material of the color matching plastic. For example, when using the "international color card" as a standard color sample and plastic color matching, because the "international color card" is used as a reference for ink color matching in the printing industry, it is different from the plastic material, so a comparative observation brings certain difficulties.
(4) Differences in the selection of colorants. Due to the wide variety of colorants, the colorants selected in the color matching test are in fact difficult to be exactly the same as the colorants used as standard color samples, and even if they are the same, it is difficult to achieve the same proportion of use, so the difference in color is inevitable.
(5) The batch number of the colorant. In mass production, the same batch number of the test formula should be used colorant, the colorant batch number is different, there may be an error of +5% to -5% in the coloring force, even if the same formula is used, it will produce color difference, so it should cause the necessary attention, it is best to test the colorant when it enters the factory
Due to the influence of the above factors, the color matching result is required to have no color difference with the sample, which is actually difficult to do, and the manual color matching can only be done to reduce the color difference to a minimum, to reach the allowable chromatic aberration range or to a degree acceptable to the design or customer.