**Welcome to pay attention to the WeChat public account #Metamaterial Frontier#, share the latest research results every day, introduce high-quality articles and excellent teams. Welcome readers and friends to share to the circle of friends or Weibo! **
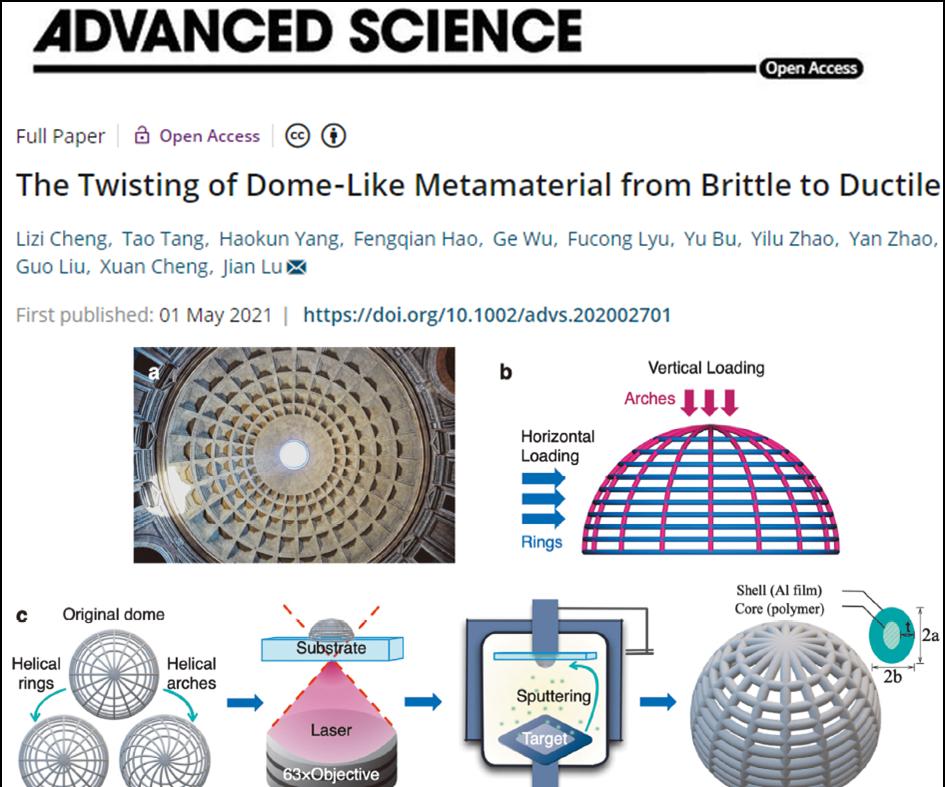
1.
2. 73
3.
The most common cause of metamaterial failure is the brittleness of the film. Ductile deformation and recoverability have been reported to be attributed to the ratio between film thickness (wall thickness t) and the semi-major axis (a) of the cross-section of the elliptical pillar. When t/a < 0.02, the nanolattice is deformed by the buckling of the shell and recovers under the action of external forces; when t/a ≥ 0.03 (called thick-walled), the nanolattice fails catastrophically and almost does not recover. Until now, much of the work has focused on creating hollow nanolattices by etching polymer substrates or reducing wall thicknesses below 100 nm to achieve size-induced brittleness-toughness transitions (referring to smaller/thinner size effects) that mitigate catastrophic failures. However, the reduced wall thickness in turn limits its strength and stiffness. Therefore, it is necessary to explore more efficient structures, which can serve as a template for deforming solid and fragile layers in an malleable way.
Recently, a team of Professor Lu Jian of the City University of Hong Kong reported on a high-strength and ductile mechanical metamaterial in Advanced Science under the title "The Twisting of Dome-Like Metamaterial from Brittle to Ductile". Inspired by the Dome of the Pantheon in Rome, spiral beams were introduced into the dome structure to improve ductility, and metamaterials with gradient spiral structures were designed. The micro-dome structure was prepared by two-photon lithography (TPL) 3D printing combined with AlNiY thin film deposition technology, and its compressive strength was 156.09± 12.92 MPa cm3 g-1, which was 73 times that of other ductile microlattices at present, and the density was much lower than that of water. Experimentally and theoretically, it has been proved that the torsional effect of the spiral vault helps to alleviate transient instability in soft materials through rotational deformation, and inhibits the catastrophic collapse of brittle composites through energy dispersion. This structural design strategy is also feasible for many other brittle material systems, maximizing the advantages of the film and overcoming the strength-ductility contradiction.
(a) Classical dome architecture of the Pantheon in Rome. (b) The intersecting 10 rings (blue) and 16 arches (red) are articulated together to form a 3D compression system. (c) Description of the manufacturing process for the core shell dome structure, with characteristic sizes of 2a (spindle pillar diameter) and t (AlNiY coating thickness). (d) SEM image of the micro-dome composite. (e) FIB cutting composite structure. (f) TEM image of graded nanostructured aluminum alloys. (g) HRTEM image of the Al film, where the nanoparticles are surrounded by an amorphous phase. Illustration: Fast Fourier transform (FFT) image of almost pure fcc Al nanocrystals labeled with dotted lines, pointing to the [011] zone axis.
(a) Force displacement curve for TPL (solid polymer) preparation of microdomes. (b-d) SEM image after micro-dome compression, indicating that the dome structure has good recoverability, the inclination angle is 60°, and the illustration is a top view image. (e-g) The original dome (black) has a through response at 10% strain, while the dome with spiral arch (blue) does not collapse at the top. (h) From the top view, the torsional angular displacement curve of the spiral vault surrounded by images of different stages. The twist angle is defined as the tangent direction along the origin of the red curve, which verifies its twisting properties as a new metamaterial. Scale bar 10 μm.
(a) Force displacement curves of alNiY films (composites) deposited by microdomes. (b-d) Scanning electron microscopy images of micro-dome composites with different spiral structures. (e-j) SEM snapshot of the compression process of three different micro-dome composites, showing catastrophic brittle damage and recovery after compression of microdomes without spiral arches (black and red), while reversible ductility deformations of microdomes of spiral arches (blue). Scale bar 10 μm.
(a) t/a (ratio of wall thickness to rod major axis) with fracture strain of the ductile structure and compared with other high-performance metamaterials. (b) t/a with respect to compressive strength. (c) Uniaxial compression finite element simulation of ductile microdome composites. The illustrations are top views of the different stages. (d) Strength is a function of the density of various materials.
5
(a) The load-displacement cycle curve presents recoverable deformation. (b-c) Changes in maximum force, recoverability and energy loss coefficients. (d-g) SEM image of the composite during multiple cycles, indicating distortion during uniaxial compression. Scale bar 10 μm. (h) In catheter-based interventional surgery, with the dome as the tip of the catheter. The magnified image shows the direction of control of the tip of the catheter. (i) Light components: turbine blades and full-wing structures. (j) Face-centered cubic (fcc) elements and dome-shaped metamaterials.
Article information:
Cheng, L., Tang, T., Yang, H., Hao, F., Wu, G., Lyu, F., Bu, Y., Zhao, Y., Zhao, Y., Liu, G., Cheng, X., Lu, J., The Twisting of Dome‐Like Metamaterial from Brittle to Ductile. Adv. Sci. 2021, 2002701.
https://doi.org/10.1002/advs.202002701
Disclaimer: This article is intended to convey more scientific research information and share, only for personal study, reference, academic exchanges, not for commercial purposes, the authors and sources cited in the articles have been identified. Due to the limited level, there may be inaccurate interpretations, such as intellectual property protection or other issues, please contact the mailbox in time [email protected], we will coordinate the handling as soon as possible.