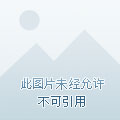
King literature at work
Blacksmith is a primitive forging process, the blacksmith puts the iron block in the fire, burns it until it is red, and then uses the pliers to clip the iron block out, put it on the anvil, holding a small hammer for forging, the apprentice picks up the sledgehammer, follows the part where the master has beaten the small hammer, alternately forging, a heavy and a light hammer sound, forming a "jingle" rhythm, where the hammer falls, Mars splashes around.
Wang Literature
With the development of society, industrialization gradually replaced handicrafts, once familiar blacksmiths, but also with the clanging of iron, is gradually fading out of people's vision, perhaps in the near future, traditional blacksmiths are just a cultural symbol in people's memory. There are also fewer and fewer craftsmen who can master the art of striking iron, and Wang Wenwen is one of them.
Before welding the iron block, put on the "sunglasses", adding a cool handsomeness
Welding iron blocks spark, like 30 years of blacksmithing career, fleeting
Wang Wen's craft of striking iron is passed down from family to family. Born in 1970, he was the third generation blacksmith in his family. Wang Wenwen's workshop is not large, but it is neatly packed, so that people can see this small workshop at a glance, the furnace wall has been smoked black due to perennial use, and each gray-black brick is a witness to the growth of this blacksmith shop, full of story.
Wang Literature's Blacksmith Workshop
Wang Wenwen gave his father a hand since he was a child, and his daily words and deeds made those blacksmithing skills remembered. At the age of 22, Wang Wenwen came alone to Caoguan Village, Baiyun District, Guiyang City, to start his blacksmithing career. Although the machined iron on the market is good-looking, lightweight and beautiful, he insists on serving the villagers by virtue of his reputation for many years of iron, and there are not only old customers who buy his things, but also well-known old and new customers, and everyone praises Wang Wenjia's iron tools for being easy to use and cost-effective.
Burn iron
In order to strike iron more efficiently, modern machines are also used
Iron set
"If you want to do a good job of iron, you must choose good iron and good steel, the ratio of steel and iron is very critical, the fire is also particularly important, more than a dozen processes can not be less, each step must be aware of the heart, bold and careful." Speaking of striking iron, Wang Wenwen gushed to us about his experience in striking iron for so many years.
A stove for burning iron
Now 52 years old, he spends every day with the clanging of iron. Basically, he can receive more than 10 orders for custom iron tools a day, start playing iron every morning from 8 o'clock to 7 o'clock in the evening, strictly control the quality of each step, and the high-quality finished products allow him to have a steady stream of "fans". "I'm in good health right now, there's no serious illness, my father is 67 years old, and I'm going to fight to be over 70 years old, a few years more than my father." Wang Wenwen said with a smile. From the age of 22 to the present, blacksmithing has gone through 30 years, burning iron, shaping, polishing every day, and repeating the cycle. Regardless of the vicissitudes of the world, what remains unchanged is the original heart that keeps the traditional blacksmithing technique.
Carry out iron work
"Blacksmithing is dirty, bitter and tired, the next generation has no interest in this craft, society is also developing, one day, this old craft may disappear, but this craftsman spirit needs to be passed on." If there are young people who are willing to take over the craft, I can teach him all of it, just as my father taught me. Speaking of this, Wang Wenwen's expression has pride and helplessness, proud that he has inherited the mantle passed down from generation to generation in his family, helpless is the heartache of being a blacksmith, with the rapid development of science and technology, more and more people have begun to choose industrial iron products with cheap prices, exquisite shapes, and convenient purchases, and handmade iron workshops have been left out in the cold.
Craftsmen can not empty the art, but also to let the craft go out, not only the inheritance of ingenuity, but also the process of craftsmen, Wang Literature hopes that there will be more young craftsmen in the blacksmith industry to join and pass on this skill together.
Blacksmithing tools
Read more
What is traditional blacksmithing?
Blacksmithing tools
Traditional blacksmith tools include blacksmith furnaces, wind boxes, hand hammers, anvils, sledgehammers, grinding stones, etc. The blacksmith shop is also known as the "blacksmith's furnace". There is a big stove in the middle of the room, and a bellows is set up by the side of the stove, and the bellows is pulled, and the wind enters the furnace, and the flames in the hearth jump straight up. Now the bellows have gradually been eliminated and replaced by blowers.
Blacksmithing tools
The iron is first burned red in the furnace, and then moved to the large iron pier, and the master holds the main hammer, that is, the small hammer, and the apprentice holds the sledgehammer for forging. Hold a small hammer in your right hand and iron tongs in your left hand. In the forging process, the hands must constantly flip the iron according to visual inspection to create a shape of the iron.
The finished iron
What are the processes of traditional blacksmithing?
1. Picking: Picking iron can save coal and forging time as firing material. Mainly rely on the experience of the blacksmith master, through visual inspection and hand sweeping to select the right iron.
2. Burning material: After picking the iron, feed it into the stove, immediately pull the bellows handle back and forth to blow the wind to burn the stove (now most of them use the blower instead, saving manpower). The blacksmith holds a long-handled iron tongs and clamps the iron to turn, so that the iron is fully heated and softened.
3. Forging: The iron that has been heated to a certain extent is clamped to the iron pier, and the hammer is lifted and beaten. If a small piece of equipment is made, the blacksmith alone can take a small hammer and repeatedly hammer the shape. If it is a large piece of equipment, two or three people must take turns to beat it with a sledgehammer.
4. Stereotyping: After forging the iron gradually loses its fiery red color and sufficient temperature, the blacksmith feeds it into the fire pit again and burns the material again. Stereotyping is a repetitive action until it takes shape.
5. Throwing steel: The instruments under the blacksmith, as long as it is a knife or the like, must be thrown steel. The amount and uniformity of the tool under the steel material often become the standard for customers to evaluate the quality of the tool. There are two ways to throw steel, one is bright steel and the other is dark steel. The so-called open steel is in the key part of the knife, the blade is all wrapped with steel; the so-called dark steel is to mix steel and iron together at the part of the blade.
6. Quenching (which is the most essential part of the iron strike process): In the process of striking iron, the two processes of shaping and throwing steel are mixed with the quenching process. Whether the iron is good or not, the mastery and cooling of the fire is the key. When quenching, the commonly used cooling medium is brine, clean water and oil. The most commonly used is ordinary cool water. The forged iron parts are put into the water, and with a "whoosh" sound, the hot air rises and it can be taken out. When quenching, the iron must be maintained at sufficient temperature.
7. Tempering: The hardness of the forgings becomes higher after quenching, but the brittleness is larger, it is easy to deform, and even fine cracks appear. It can be put back in the furnace and heated to adjust the hardness.
Photo, video/reporter Lin Jian, Li Jingcheng
Editor/Ting Xu
Editor/Liao Xun
Editor/Wu Qian, Xia Jin
Posted/Xu Ting