1. Who does the enterprise consult to meet the certification conditions?
In order to achieve the conditions that must be met to obtain quality certification qualifications, enterprises often need to ask experts for consultation, especially how to establish a quality system according to GB/T 19000-ISO 9000 series standards, how to compile a quality manual, how to evaluate the effectiveness of the quality system, and need expert guidance and help to avoid detours.
In order to ensure the effectiveness of consultations, the State Bureau of Technical Supervision exercises appropriate management of consultancy bodies engaged in certification. The consulting body should be an entity with legal personality, and its task is mainly to provide correct and effective consulting services for enterprises to establish a quality system, compile quality manuals, internal quality audits, etc.;
When enterprises need consultation, they should choose a consulting agency with strength and experience for consultation.
2. The main procedures for enterprises to apply for and obtain certification qualifications
The main procedures for applying for and obtaining product certification qualifications are as follows:
(1) Submit an application intention. Enterprises orally submit their intention to apply for certification to the relevant certification committees, ask for matters that need to be understood, and request relevant information.
(2) Consultation (non-essential procedure). If the enterprise has needs, it can submit a consultation request to the consulting agency, and the consulting agency can send experts to guide the enterprise to establish a quality system, compile a quality manual, and conduct a quality system audit (pre-inspection).
(3) Submit a formal application. The enterprise fills in the application form for certification (you can obtain a uniformly printed blank application form from the certification committee). Attach a quality manual and send it to (or send) to the relevant certification committee.
(4) The certification committee examines the application form, and after agreeing, issues a notice of acceptance of the application to the enterprise, informing it of the fees to be paid.
(5) The enterprise shall pay the fee in accordance with the requirements of the notice.
(6) The certification committee appoints an inspection team to be responsible for inspecting the quality system of the applicant enterprise and notifying the applicant enterprise of the list of inspection teams.
(7) The inspection team examines whether the quality manual submitted by the enterprise meets the requirements of GB/T 19001-ISO 9001; if it is not met, it is proposed to the applicant enterprise and asked to modify or provide supplementary materials until it is basically satisfied.
(8) The inspection team leader formulates an inspection plan and issues a copy to the applicant enterprise, including: the name and address of the inspected party, the members of the inspection team, the purpose, scope and basis of the inspection, the inspection date, the inspection activity arrangement and the confidentiality statement.
(9) Each inspector prepares a checklist for the inspection department he undertakes.
(10) The inspection team goes to the site to inspect, based on GB/T 19001-ISO 9001 and the quality manual of the enterprise, to inspect and evaluate the actual operation of the quality system of the applicant enterprise, the implementation of the quality manual; before the end of the inspection; the inspection team leader reports the preliminary results of the inspection and evaluation to the enterprise leader, and informs the conclusion of "recommendation", "postponement recommendation" or "recommendation".
Before the inspection team leaves the factory, the sample is taken and sealed, and the enterprise (or inspection team) submits it to the designated inspection agency and sends the inspection fee.
If it is a "postponement recommendation", the enterprise should formulate corrective measures, complete them within the time limit specified by the inspection team, achieve satisfactory results, and report the corrective measures and their implementation to the inspection team leader in writing.
The inspection team leader reviews the corrective action report submitted by the enterprise, and if necessary, goes to the scene to review, and can recommend it when the requirements are met.
The inspection team prepares and submits the quality system inspection report to the certification committee.
The inspection body inspects the product sample according to the requirements of the certification committee, submits a calibration report to the committee, and the committee sends a copy of the applicant enterprise.
When the certification committee reviews the quality system inspection report and the product inspection report, and meets the requirements of the certification regulations and relevant regulations, it issues a certification certificate to the enterprise and permits the use of the certification mark on the application products that leave the factory in the future; if the review does not meet the requirements, it should issue a written notice to the applicant enterprise to inform the reasons for not recommending.
Enterprises adhere to and continuously improve the quality system, improve product quality, accept the regular supervision and review of the certification committee, including the supervision and inspection of the maintenance of the quality system and the supervision and inspection of certified product quality.
3. What are the benefits of obtaining certification qualifications for enterprises?
Quality certification qualification is the proof that the quality system of the enterprise meets international standards, the certificate of trustworthy product quality, and the passport for products to enter the international market. Obtaining the qualification of quality certification has at least the following benefits for enterprises:
(1) Improve the quality management level of enterprises
A basic condition that must be met to obtain quality certification qualifications is that enterprises must establish a quality system in accordance with GB/T 19000-ISO 9000 quality management and quality assurance series standards. The ISO 9000 series of standards is based on the quality management experience of various industrial developed countries and is a valuable asset. The establishment of a quality system is the only way for enterprises to achieve the goal of good quality and low cost, which can enable enterprises to have a mechanism to reduce, eliminate, and especially prevent quality defects. In the process of applying for certification, the certification body will guide the enterprise to establish a quality system in various ways to meet the requirements of GB/T l9000-ISO 9000 series standards.
(2) Expand sales and obtain greater profits
The certification mark is a trustworthy proof of product quality, and the products with the certification mark have obvious competitiveness in the market, and are trusted by the majority of customers, selling more and selling fast. Experience at home and abroad shows that in the market economy environment, obtaining certification qualifications is a favorable means for enterprises to win in competition and improve profits.
(3) Expansion of exports
The implementation of quality certification system is a common practice in countries in the world today, especially in industrially developed countries, many buyers engaged in international trade are willing or designated to buy certified products, and some buyers require manufacturers to provide proof of quality system certification according to ISO 9000 (that is, GB/T 19000) when ordering. For example, Dandong canning factory production of red plum brand slippery mushroom canned mainly sold to Japan, before the certification of the annual production of up to 1200 tons, after obtaining the certification qualification (using a circle mark), in Japan "grain and oil news" published the factory slipper mushroom canned through the Chinese national certification news, Japan Chuan Iron Co., Ltd. immediately proposed to underwrite all the factory production with square circle certification mark products, the annual demand of 4000 tons, greatly exceeding the production capacity of the plant. Facts show that the qualification of enterprises to obtain quality certification is the need to make products enter the international market and expand exports.
(4) Protect the legitimate rights and interests of enterprises
China's product quality certification management regulations stipulate: "If a product is not certified or unqualified and is sold from the factory using the certification mark, the competent administrative department for standardization shall order it to stop selling, impose a fine of not more than three times the illegal income, and may impose a fine of less than 5,000 yuan on the person in charge of the illegal unit." "If your factory's products have obtained certification qualifications, when it is found that similar products produced by other manufacturers fraudulently use certification marks, the certification body will deal with them according to law, thereby protecting the legitimate rights and interests of certification manufacturers."
(5) Exempt from other supervision and random inspections
China's product quality certification management regulations stipulate: "Products that are approved for certification are exempt from other inspections except those provided for by national laws and administrative regulations." This article is for the current supervision and random inspection of enterprise products from all walks of life is particularly frequent and stipulated, after the enterprise products obtain certification qualifications, can reduce the excessive burden caused by various supervision and random inspection, which is of practical significance to enterprises.
4. The steps of quality system establishment
The establishment and improvement of the quality system generally goes through the planning and design of the quality system, the preparation of quality system documents, the trial operation of the quality system, and the review and review of the quality system, and each stage can be divided into several specific steps.
First, the planning and design of the quality system
This stage is mainly to do a good job in various preparatory work, including education and training, unified understanding, organization and implementation, formulation of plans; determination of quality policies, formulation of quality objectives; investigation and analysis of the current situation; adjustment of organizational structure, allocation of resources and other aspects.
(1) Education and training, unified understanding
The process of establishing and perfecting the quality system is the process of starting with education and ending with education, and it is also the process of raising awareness and unifying understanding, and education and training should be carried out at different levels and step by step.
The first level is the decision-making level, including party, political, and technical (technical) leadership. Main training:
1. By introducing the development of quality management and quality assurance and the lessons learned by the unit, explain the urgency and importance of establishing and improving the quality system;
2. Through the overall introduction of ISO9000 family standards, we will improve the understanding of establishing a quality system according to national (international) standards.
3. Through the explanation of the elements of the quality system (the focus should be on the overall elements such as "management responsibilities"), the key position and leading role of decision-making leaders in the construction of the quality system are clarified.
The second level is management, with a focus on the heads of management, technical and production departments, as well as staff related to the establishment of quality systems.
These two levels of personnel are the backbone of the construction and improvement of the quality system, playing a role in carrying forward the upper and lower levels, so that they can fully accept the training of the relevant content of the ISO9000 family standard, and the method can be combined with explanation and discussion.
The third level is the executive layer, that is, the operators related to the whole process of product quality formation. Personnel at this level mainly train content related to the quality activities of the post, including the tasks that should be undertaken in the quality activities, the authority to be given to complete the tasks, and the responsibilities that should be borne for causing quality negligence.
(2) Organize implementation and draw up plans
Although the construction of the quality system involves all departments and all employees of an organization, for most units, the establishment of a capable work team may be necessary, according to the practice of some units, this team can also be divided into three levels.
The first level: the establishment of the top management (factory director, general manager, etc.) as the group leader, the quality supervisor as the deputy leader of the quality of the department of construction leading group (or committee). Its main tasks include:
1. Overall planning of system construction;
2. Develop quality policies and objectives;
3. Decomposition of quality functions by functional department.
At the second level, a working group with the participation of leaders (or representatives) of various functional departments is established. This working group is generally led by the leaders of the quality department and the planning department, and its main task is to organize and implement it in accordance with the overall plan of the system construction.
The third level: the establishment of a working group on elements. According to the division of labor of each functional department, the responsible unit for the elements of the quality system is clarified, for example, "design control" should generally be responsible for the design department, and the "procurement" element should be responsible for the material procurement department.
After the implementation of the organization and responsibilities, the work plan should be formulated separately at different levels, and attention should be paid to when formulating the work plan:
1. The goal should be clear. What tasks to accomplish, what are the main problems to be solved, and what are the goals to be achieved?
2. You want to control the process. The main stage of establishing a quality system should stipulate the timetable for the completion of the task, the main responsible persons and participants, as well as their division of responsibilities and mutual cooperation.
3. Highlight the main points. The focus is mainly on weak links in the system and key minorities. This minority may be one or more features, or it may be some activity within a feature.
(3) Determine the quality policy and formulate quality objectives
The quality policy reflects the pursuit of quality and the commitment to customers of an organization, which is the guideline of quality behavior of employees and the direction of quality work.
The requirements for developing a quality policy are:
1. Coordination with the general policy;
2. Quality objectives should be included;
3. Combined with the characteristics of the organization;
4. Ensure that implementation is understood and adhered to by personnel at all levels.
(4) Investigation and analysis of the current situation
The purpose of the status survey and analysis is to reasonably select the elements of the system, including:
1. System situation analysis. That is, to analyze the quality system of the Organization in order to select the requirements of the elements of the quality system according to the quality system situation in which it is located.
2. Product characteristic analysis. That is, analyze the technical intensity of the product, the object of use, the product safety characteristics, etc., to determine the degree of adoption of the elements.
3. Organizational structure analysis. Whether the organization's management organization is set up to meet the needs of the quality system. An organizational structure appropriate to the quality system should be established and inter-agency affiliations and methods of communication should be established.
4. Whether the production equipment and testing equipment can adapt to the relevant requirements of the quality system.
5. Analysis of the composition, structure and level of technical, managerial and operator personnel.
6. Management of basic work situation analysis. That is, the analysis of standardization, measurement, quality responsibility system, quality education and quality information.
The above content can be compared with the quality system element requirements specified in the standard for comparative analysis.
(5) Adjust the organizational structure and allocate resources
Because in an organization, in addition to quality management, there are various other types of management. Since most of the organizational structure is not based on the objective law of quality to set up the corresponding functional departments, after the implementation of the quality system elements and the development of the corresponding quality activities, the corresponding work responsibilities and authorities in the activities must be assigned to each functional department. On the one hand, the quality activities carried out objectively, on the other hand, the existing functional departments are artificial, and the relationship between the two is handled, in general, a quality function department can be responsible for or participate in multiple quality activities, but do not let a quality activity be responsible for multiple functional departments.
At present, the responsibilities and roles of the existing functional departments of China's enterprises for quality management activities are generally not ideal, and should be strengthened in general.
In the course of the activity, the appropriate hardware, software and staffing must be involved, and appropriate allocation and enrichment should be carried out as needed.
Second, the preparation of quality system documents
The content and requirements of the preparation of quality system documents, from the perspective of the construction of quality system, should emphasize several issues:
1. System documents should generally be formalized after the completion of phase I and may be cross-cutting if necessary. If the preliminary work is not done, the direct preparation of system documents is prone to systematic, incomplete, and out of touch with reality and other drawbacks.
2. In addition to the quality manual needs to be uniformly organized and formulated, other system documents should be formulated separately by the focal functional department according to the division of labor, and the draft is first proposed, and then the review is organized, which is conducive to the implementation of future documents.
3. The preparation of quality system documents should be carried out in conjunction with the allocation of quality functions of the unit. According to the requirements of the selected quality system, the quality activities (including direct quality activities and indirect quality activities) are carried out one by one, and the quality functions are assigned to each functional department. Quality activity items and assignments may be presented in the form of a matrix diagram, which may also be attached as an annex to the Quality Manual.
4. In order to make the quality system documents prepared to be coordinated and unified, before the preparation, a "quality system document schedule" should be formulated, and the existing quality manual (if prepared), enterprise standards, rules and regulations, management methods and record forms should be collected together and compared with the quality system elements, so as to determine the new, addendum or revised quality system document items.
5. In order to improve the efficiency of the preparation of quality system documents and reduce rework, it is necessary to strengthen the coordination between the levels of documents and between documents and documents in the process of document preparation. Nevertheless, a set of good quality system documents also has to go through many iterations from the top down and from the bottom up.
6. The key to compiling quality system documents is to pay attention to practical results and not to take the form. It is necessary to meet the ISO9000 family standards in general and principle, and to conform to the actual situation of the unit in terms of methods and specific practices.
Third, the trial operation of the quality system
After the completion of the quality system documentation, the quality system will enter the trial operation stage. Its purpose is to test the effectiveness and coordination of the quality system documents through trial operation, and to take improvement measures and corrective measures for the exposed problems, so as to achieve the purpose of further improving the quality system documents.
In the process of trial operation of the quality system, it is necessary to focus on the following work:
1. Targeted promotion of quality system documents. To make all employees realize that the newly established or perfect quality system is a change in the quality system in the past, in order to be in line with international standards, to adapt to this change, it is necessary to seriously study and implement the quality system documents.
2. Practice is the only test of truth. Some problems will inevitably arise through the trial operation of system documents, and all employees will truthfully reflect the problems and improvement opinions that arise in practice to the relevant departments in order to take corrective measures.
3. Coordinate and improve the problems exposed in the trial operation of the system, such as poor system design and incomplete projects.
4. Strengthening information management is not only the need of the system trial operation itself, but also the key to ensuring the success of the trial operation. All personnel related to quality activities should do a good job in the collection, analysis, transmission, feedback, processing and archiving of quality information in accordance with the requirements of the system documents.
Fourth, the quality system audit and review
Quality system audits are often more important in the initial stages of system establishment. At this stage, the focus of the quality system audit is mainly to verify and confirm the applicability and validity of the system documents.
1. The main contents of the audit and appraisal generally include:
(1) Whether the specified quality policy and quality objectives are feasible;
(2) whether the system documents cover all the main quality activities and whether the interface between the documents is clear;
(3) Whether the organizational structure can meet the needs of the operation of the quality system, and whether the quality responsibilities of each department and position are clear;
(4) Whether the selection of quality system elements is reasonable;
(5) Whether the specified quality records can play a witness role
(6) Whether all employees have developed the habit of operating or working according to the system documents, and how the implementation is.
2. The characteristics of this phase of the system review are:
(1) The system audit during the normal operation of the system focuses on compliance, and in the trial operation stage, it is usually a combination of compliance and applicability;
(2) In order to make the problem as exposed as possible in the trial operation stage, in addition to organizing the audit team to conduct a formal audit, there should also be the participation of the majority of employees, and encourage them to find and raise problems through the practice of trial operation;
(3) After the end of each stage of the trial operation, an audit should generally be formally arranged in order to correct the problems found in a timely manner, and some major problems can also be organized as needed and timely;
(4) In the trial run, all elements should be reviewed and overwritten;
(5) fully consider the guarantee effect on the product;
(6) On the basis of internal audit, the top management will organize a system review.
It should be emphasized that the quality system is continuously improved by the Bank of China to improve, and after the quality system enters normal operation, it is still necessary to take various means such as internal audit and management review to enable the quality system to be maintained and continuously improved.
5. The function of the quality manual
Quality manuals generally have the following functions or purposes:
(1) Publicize and implement the quality policies, procedures and requirements of the organization;
(2) Describe and implement an effective quality system;
(3) Provide better control methods and promote quality assurance activities;
(4) Provide the document basis for the quality system audit;
(5) When the situation changes, ensure the continuity of the quality system and its requirements;
(6) Train personnel according to the requirements of the quality system and the corresponding methods;
(7) Introduce the quality system of the organization to the outside world;
(8) In the contractual environment, prove that the quality system meets the corresponding standards.
Analysis of the above eight functions shows that the first six belong to the needs of the Organization's quality management activities, the most important of which are the 1st and 2nd, that is, the implementation of an effective quality system through the promotion and implementation of the Organization's quality policies, procedures and requirements. Item 5, "Change of Circumstances", means that when the organization's main leader or head of the quality system changes, the organization's quality system will still operate according to the provisions of the quality manual. In particular, those organizations that are approved for quality system certification, their quality manuals are controlled by filing with the certification body, and important changes must be approved by the quality system certification body. Thus ensuring the continuity of the operation of the quality system. It has changed the "rule of man" situation in which the quality system often changes due to the change of management personnel in the past, and gradually moved towards the "rule of law".
6. Characteristics of the quality manual
A complete quality manual for both internal and external use should have the following features:
(1) prescriptive;
(2) systematic;
(3) Coordination; not only the parts of the manual itself are coordinated, but also the manual and the relevant quality system procedures, operating documents, and forms should be coordinated;
(4) Scientific: mainly manifested in following the principle of mass ring, in line with gb/T 19000-ISO9000 family standard elements;
(5) Feasibility: refers to the premise of meeting the requirements of the corresponding quality system standards, combined with the specific conditions of the organization, so that the provisions made in the manual are implemented article by article, implemented, some organizations emphasize that the organization has a poor foundation and conditions are not available, and it is inappropriate to delete or reduce the requirements stipulated in a certain system standard in the manual.
(6) Normative: That is, the quality manual (including procedural documents) is included in the standardized management of the Organization, rather than as a general line document management, which is conducive to the management and control of the manual's custody, query, change, and edition.
7. How to write the quality manual
The quality manual can be written according to the following procedure:
(1) Establishment of an organization
Once the decision makers of the Organization have taken the decision to prepare a quality manual, the following organizations shall generally be established:
(1) Leading Group for the Preparation of the Quality Manual shall be attended by representatives of the top managers of the Organization (general manager, plant director or director), the heads of the relevant business departments, and the heads of the manual preparation offices. Responsible for the guiding ideology of the preparation of the quality manual, the quality policy, the objectives, the progress plan for the preparation of the overall framework of the manual, and the determination and coordination of major issues in the preparation of the manual.
(2) The office for the preparation of quality manuals is generally based on the quality management department and is composed of appropriate personnel from various relevant functional departments. Responsible for the specific preparation of the manual.
(2) Clarify or formulate quality policies
One of the basic tasks of the Quality Manual is to elaborate on the quality policy and its implementation. Therefore, the premise of the preparation of the quality manual is to clarify the quality policy of the Organization (for organizations that have an existing quality policy and have been deliberated by the leading group for the preparation of the quality manual and deemed it suitable for explicit inclusion in the manual) or the development of the quality policy of the Organization (organizations that did not have a quality policy or needed to be reformulated after review).
(3) Learn GB/Tl9000-ISO9000 family standards
First of all, the managers of the organization, the leading group for the preparation of the quality manual, and the personnel of the quality manual preparation office should study in depth and grasp the above standards more systematically and comprehensively.
(4) Summarize the experience of the Organization in quality management in the previous period. Clarify what experiences and achievements are, and what lessons and gaps are available.
(5) Comparative analysis
The requirements of the GB/T19000-ISO9000 family standard are compared with the experience and lessons of quality management in the organization, and the practices that meet the standards or basically meet the standards and their regulations, systems, and necessary modifications and supplements are included in the quality manuals or procedural documents prepared.
(6) Implement quality functions
The functions specified in the quality system model standards adopted are specifically implemented to each functional department. Some elements involve multiple departments, and it should be determined which department is the organizer and which department is the cooperating unit. In the process of implementing the function, it must be clear that the establishment of a quality system that meets the requirements of international standards is the common responsibility of all departments and units of the whole company (factory), and should not be regarded as a matter of the quality department, so that many elements or sub-elements that should be undertaken by other functional departments are pushed to the quality department to be responsible. This is a noteworthy bias in the current development of the manual to implement quality functions.
(7) Prepare a draft quality manual
In practical work, the manual preparation office first proposes a framework for the preparation of a manual (including the issuance order, preface, order, body of the manual, the provisions for the management and use of the manual, the specific outline of the preparation of the supporting document catalog, the division of labor, the progress, etc.) after the approval of the leading group for the preparation of the manual, the division of labor is prepared, the office organizes collective discussion and coordination, and after several discussions and modifications, a draft is formed. In the process of preparing the draft, if difficult problems are encountered, if the competent leader can be solved quickly, it should be reported and solved in a timely manner; some major complex problems involving a wide range of aspects can also be gathered together and submitted to the manual leading group to be resolved when reviewing the draft manual.
(8) Verification, approval and issuance of quality manuals
(1) Verification of quality manual
After the preparation of all the contents of the quality manual, it shall be proofread and signed internally by the staff of the preparation office and submitted to the leading group for the preparation of the quality manual of the Organization for approval, and finally approved by the top management of the organization.
The following should be considered in the validation and approval of the quality manual:
a. The extent to which the quality manual is in compliance with the national standards adopted and the corresponding international standards;
b. The degree of compliance of the quality manual with the relevant policies and decrees;
c. The quality manual guarantees the level of assurance for the achievement of the established quality policy, quality objectives and quality requirements of customers;
d. The quality manual is systematic, coordinated, feasible and standardized.
(2) Publication of quality manuals
The publication of quality manuals is usually carried out by a release order signed by the top management of the organization.
The top management of the organization signed the issuance order of the quality manual, indicating that the manual is an important regulatory document of the whole organization and should be strictly complied with by all personnel; on the other hand, it also shows the commitment of the top management of the organization to quality responsibility.
8. Several issues that should be paid attention to when compiling quality manuals
In order to ensure the effective implementation of the quality manual and enable the enterprise to achieve good benefits, in the process of compiling the quality manual, the following issues should be paid attention to:
(1) It is necessary to pay attention to the compilation of the booklet based on the needs of the enterprise itself and prevent the adoption of the form
For an enterprise's products to enter the international market, it is necessary to provide evidence of product quality and credibility. In general, the evidence of providing reliable product quality includes two aspects, namely product inspection, test results and the quality assurance ability of the enterprise, with this evidence, the user can believe that you have the ability to provide products that meet the quality requirements, the user can sign a contract with you, many countries when signing the contract, not only put forward requirements for product quality, but also put forward requirements for the quality system of production enterprises, that is, requirements for quality assurance capabilities. Since the promulgation of the ISO 9000 family of standards, many countries have used it as a criterion for evaluating the quality system of manufacturers. If China's enterprises want to enter the international market and win in the competition, in addition to the product quality to meet the requirements of foreign users, the quality system of the enterprise must also meet the requirements of the internationally accepted set of standards, otherwise, can not obtain the trust of users. The quality manual comprehensively and systematically reflects the quality system of an organization and is the normative basis for the operation of the quality system, so how to compile the quality manual is directly related to whether the quality system of the enterprise can operate effectively. In fact, due to the differences in product types, equipment conditions, enterprise specifications, production characteristics, institutional settings, management methods, user requirements and corporate culture, the quality systems of each enterprise are relatively different from each other, so the quality manual describing the quality system should also have greater differences. The quality manual should indeed reflect the characteristics of the enterprise, and the various factors affecting the quality should be clearly stated and the focus of control should be clarified. Such a quality manual is a really useful manual. Internally, it can play a role in strengthening quality management; externally, it can make customers have a sense of trust in the management of the enterprise. In the past, Chinese enterprises also prepared quality documents when carrying out quality management activities, but because under the planned economy system, the market competition mechanism was not established, the pressure of the market on enterprises was not formed, and the quality documents prepared by enterprises were only to cope with the inspection of superiors, and did not really become the norms for enterprises to carry out quality management activities. At present, if enterprises still implement the GB/T 19000 family standards with the past concepts, the result can only be formalism, which is not conducive to the improvement of enterprise quality management. In order for the quality system to operate effectively, "it is important to determine the content and requirements of the quality system and the quality manual according to the quality standards to be achieved. "The main purpose of the quality manual is to implement effective quality management to ensure the proper functioning of the quality system. The preparation of the quality manual is not to cope with the inspection of superiors and externals, but to improve the quality management level of the enterprise, strengthen the competitiveness, and produce products that meet the needs of users on the basis of the most appropriate cost
(2) Pay attention to summarizing the experience of quality management of the enterprise
Since the purpose of compiling the manual is to improve the level of quality management, then, in the process of compiling the quality manual, the previous quality management work should be summarized, and the implementation of the GB/T 19000 family standard should be organically combined with the promotion of the previous advanced and successful experience.
Since 1979, the majority of enterprises in China have vigorously promoted total quality management: TQC knowledge has been disseminated and popularized among the majority of employees, and the quality awareness of employees has been continuously improved, and quality management institutions have been generally established in enterprises, initially forming a quality management team and accumulating certain quality management experience.
To conscientiously implement the GB/T 19000 family standard, it is necessary to properly handle the relationship between the standard and the implementation of TQC in the past. Now the TQC is compared with the GB/T 19000 family standard:
(1) The theoretical basis is consistent
Both believe that product quality has a process of generation, formation and realization, and that the quality in the process must be valued and controlled. The establishment and implementation of the quality system is an important management means to ensure that the quality of the product meets the requirements of the regulations, and the quality system runs through the whole process of product quality generation, formation and realization. The perfect quality system is to optimize the quality on the basis of considering the benefits, costs and risks, and effectively control all the links and factors that affect the quality of the product.
(2) The purpose is basically the same
According to ISO 8402, total quality management is what enables an organization to "achieve long-term success by satisfying its customers and benefiting all members of the organization and society." "The GB/T 19000 family of standards clearly states that an organization should continuously improve quality by implementing a quality system and continuously improve the satisfaction of customers and other beneficiaries (employees, owners, suppliers, society) in order to compete and maintain good economic efficiency. Thus, the two aims are basically the same, both are to satisfy customers and other beneficiaries and to make the organization successful.
(3) The comprehensive requirements are consistent
The basic requirements of TQC are "three complete and one diverse", that is, "total quality management requires the participation of all employees in quality management, the scope is the whole process of product quality generation, formation and realization, the quality management of the whole enterprise, and the management methods should be diverse (such as speaking with data, PDCA cycle, computer management, etc.)".
B/T 19000 family standards like TQC have comprehensive requirements, embodied in: the entire process of product quality formation, from marketing and market research to the disposal after the end of the product life cycle for quality control of the whole process; the quality of all the elements affecting quality, including technology, management and people, the implementation of a full range of quality control, both control of hardware and software, that is, control of material resources and control of human resources, both control of product quality and quality of work; require all personnel to undertake obligations and participate in quality management.
(4) The idea of prevention is consistent
TQC said: "The basic feature of total quality management is to change from the past post-inspection and control to the prevention and improvement of the main...". GB/T 19000 family standard stipulates that the quality system focuses on preventing the occurrence of problems, rather than relying on post-inspection.
(5) Emphasize that leadership is the key
TQC believes that the implementation of total quality management, leadership is the key, that is, the so-called "head QC", GB/T19000 family standards first stipulate the responsibilities of organizational managers, and clearly point out that managers are ultimately responsible for the formulation of quality policies and the planning, development, implementation and maintenance of quality systems.
(6) Pay attention to quality and economy
The determination, reporting, analysis and research of quality costs to promote the improvement of product quality and economic efficiency is an important part of TQC. China proposes to "take the road of quality and efficiency", "reduce the rate of defective products", "improve the first pass rate of key processes", etc. are all good ways to emphasize economy in the process of implementing TQC. The GB "49oo0 family standard" separately regards the "financial considerations of the quality giant system" as the 7 key points of the quality system, focusing on the financial income report as an important aspect of measuring the harmfulness of the quality system; and spends a lot of time describing the method of organizing the quality cost analysis.
(7) Pay attention to the application of statistical methods
TQC systematically and in-depth he talked about the application of statistical methods in quality management, such as hierarchical methods (questionnaire method, permutation chart B-day fruit chart method, histogram method, control chart method, scatter chart method, etc.). Gb/Tn0() 0 family standards as "application of statistical methods" as an element of the quality system, and pointed out that all stages of organization of production and operation can be applied, but also listed the commonly used methods of hypericilization, including: experimental design and analysis of factorial analysis, analysis of variance and regression analysis, significance test, quality control diagrams and accumulation techniques, statistical sampling, etc.
(8) Emphasize quality improvement
Both agree that organizations should make continuous quality improvements. = Improve the efficiency of the organization's various work and processes through quality improvement, so that the organization can obtain long-term quality benefits, so that customers can continuously obtain the value added due to the continuous quality improvement of the organization.
Although there are many similarities between the GB/T 19000 family and TQC, there are also differences. For example, TQC is a person-centered quality management that pays more attention to people's quality awareness. Through the education of operators and on-site personnel, they realize that the quality of nine products is not only very important to customers, but also extremely true to the company, including my own, so as to ensure the quality of diamond production. GB/T 19000 family is through the formulation of standards, emphasizing the institutionalization of quality management work, requiring employees to comply, in order to get the expected quality of a kind of management at night, so that employees are prone to the idea of doing work according to the standard, and its subjective initiative cannot be well played. For example: TQC is the generation, formation and realization of product quality and the law of operation and hook with its related factors" About the system of discussion, which provides a complete and effective method for quality management of enterprises, including quality management theory, quality design, quality control, assurance and inspection, quality economy, quality legal system, reliability and other contents. The standard is a unified provision for the management work and activities in quality activities, and only emphasizes the "what to do" and generally does not provide a "how to do" method. When implementing the GB/T 19000 family standard, enterprises can adopt the quality management method provided in TQC to make the management work more effective.
The above discussion shows that TQC and GB/T19000 family standards do not contradict each other and can complement each other. It can be said that the implementation of TQc in the past ten years has laid a foundation for the implementation of the grating/T19000 family standard today, both in terms of the management level of the enterprise and in terms of people's understanding. Passing the standard does not mean denying the "past", but to inherit and develop, and to further supplement and improve according to the requirements of the standard on the basis of the implementation of TQC achievements and economy in the past.
(3) Make full use of existing management standards and work standards
The quality manual should include or involve written quality system procedures for the commercial planning and management of quality-affecting activities within the organization. It also provides that, in accordance with the ISO 900O family of standards, these documented procedures shall contain all the applicable elements of the quality system standard, shall clarify (the level of detail shall meet the need for adequate control of the activities concerned) the responsibilities, powers and interrelationships of those managers, performers, validators or reviewers who affect the quality;
Management standards are standards with specific management functions formulated by management institutions to perform their management functions. It stipulates and measures the orderliness of management objects or procedures, and uniformly stipulates the content, procedures, methods, methods and requirements that should be met in management activities. In addition to quality management, management standards generally include business plan management, production management, technical management, material management, energy management, financial audit management, labor and personnel management, administrative management and other aspects of the standard. For example, technical research and development, technical documents and archives, intelligence data, etc. are technical management standards; production cycles and intervals, work quotas, production organizations, semi-finished products and inventory management are production management standards. Work standards are to achieve the coordination of the entire work process, improve the quality and efficiency of work, the standards formulated for the work of each post, the work standards generally include basic work standards, work quality standards, work procedure standards and work method standards. For example, the general and instructive outlines or norms related to the work of all types of personnel belong to the basic work standards; the standards related to the scope, content, requirements, responsibilities, authority, assessment, rewards and punishments of all kinds of personnel in various work positions belong to the work quality standards; the standards related to the arrangement, procedural requirements, and coordination requirements of the work process of all kinds of personnel belong to the work procedure standards; and the standards for the methods and means used by all kinds of personnel in completing various work are work method standards. The scope of management standards and work standards is relatively wide.
Quality manuals are prepared on the basis of procedural documentation, but manuals cannot be all-encompassing, and manuals often cover all aspects, with specific details set out in addition to documentation. For example, the responsibilities and authorities of leaders at all levels of the enterprise and personnel engaged in various quality activities, the interface and coordination measures between various activities, the requirements for the working ability of various types of personnel, and the procedures and methods of various work, etc., should be formulated according to the corresponding standards, through the implementation of these standards, in order to ensure the implementation of the quality manual, and make the quality system operate effectively. The standards that enterprises should develop in these areas are numerous, including management standards and working standards. Management standards and work standards directly affect whether the quality system can operate effectively.
In the past few years, many enterprises in Our country have made great efforts to build an enterprise standard system and formulated a considerable number of management standards and work standards. Now that enterprises implement gb/T 19000 family standards, they need to write quality system documents, so how to deal with the management standards and work standards of yizhu? The enterprise standard system should be closely integrated with the establishment of the quality system. In the process of using gb/T 19000 family standards to establish a quality system, if you can make full use of the set of standards that have been formed, you can make appropriate choices according to the requirements of GB/T 19000 family standards. The original management standards and work standards that can play a good role are directly quoted in the quality system program documents, which can not only avoid a lot of duplication of labor, save manpower, material resources and time, but also ensure the coordination and consistency between the two systems, and receive the effect of doing more with less.
(4) Pay attention to the active participation of employees
At present, when some enterprises implement the GB/T 19000 family standards and compile manuals, they often invite quality management experts at home and abroad, or a few quality management personnel within the enterprise to form a group to compile quality manuals, which is specifically responsible for the preparation of manuals, and does not pay attention to the active participation of employees within the enterprise, which is not conducive to the preparation of quality manuals and the implementation after compilation.
We know that the most important thing in the preparation of the manual is to be able to implement, and the implementation of the manual is the business of the internal employees of the enterprise, so in the preparation of the quality manual, we should listen to the opinions of all the employees within the enterprise, give full play to their enthusiasm and creativity. In fact, we have some good management methods in the past, which are worth continuing to carry forward. For example, "two references, one change, three combinations" is an example. The so-called "two participation, one reform, and three combinations" refers to the participation of cadres in labor, the participation of workers in management, and the reform of unreasonable rules and regulations; the abbreviation of the "three combinations" of technicians, workers, and cadres. When compiling quality manuals, enterprises should carry forward the good practices of employees participating in management and "three combinations", so that employees can participate in opinions; in order to fully absorb the valuable experience and practical knowledge formed by the majority of employees in long-term practical activities, so as to ensure that the quality manuals compiled have strong operability. Leaders, experts, and employees combine the preparation of quality manuals to ensure the scientificity, operability and effectiveness of the manuals. At the same time, the process of compiling the manual is also a process of communication between the upper and lower levels, forming a consensus, and establishing a common goal of struggle. This is of great benefit to the formation of internal cohesion and enhanced competitiveness of enterprises.
(5) Pay attention to the use of languages that are in line with the cultural traditions of the country
The quality manual should include the applicable elements of the quality system standard selected by the enterprise, because the GB/T 19000 family standard is equivalent to the use of ISO 9000 family standard, therefore, when compiling the quality manual, we must pay attention to avoid using some blunt translation language in the standard, so as not to make the enterprise employees can not understand, the implementation of the misunderstanding, so that the quality manual can not play its due role. The preparation of the manual should be based on a deep understanding of the standards and in a language that is in line with the cultural traditions of the country, which can facilitate the implementation of the quality manual.
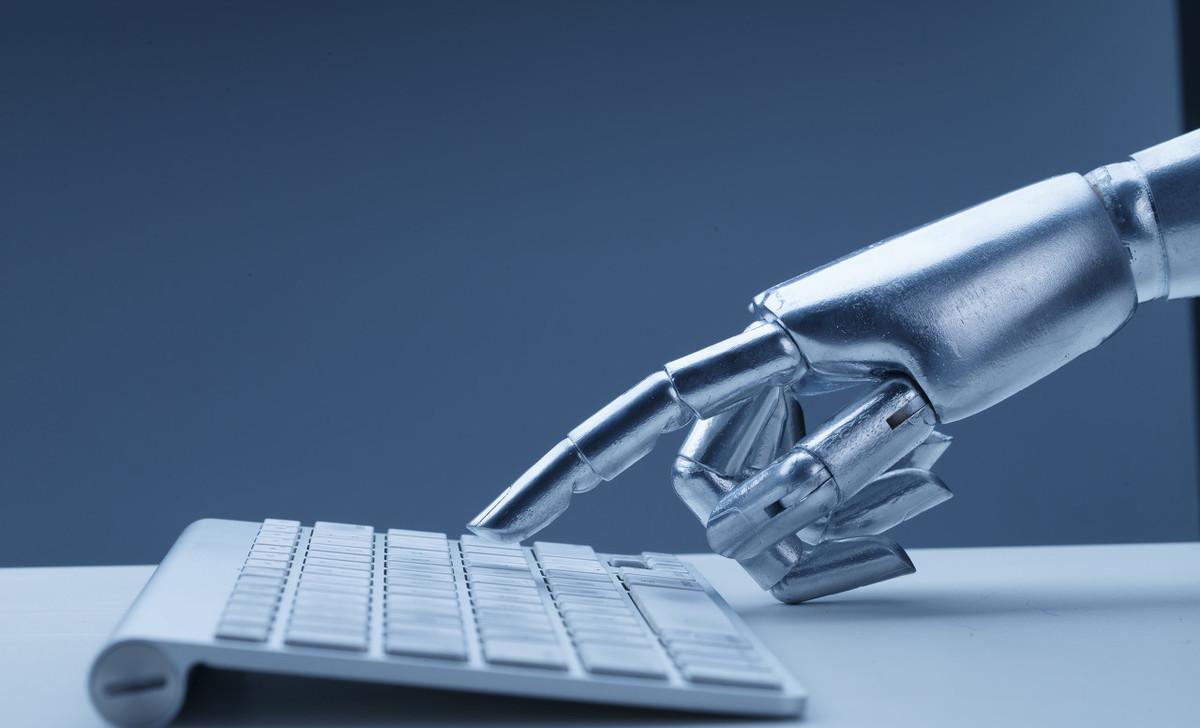