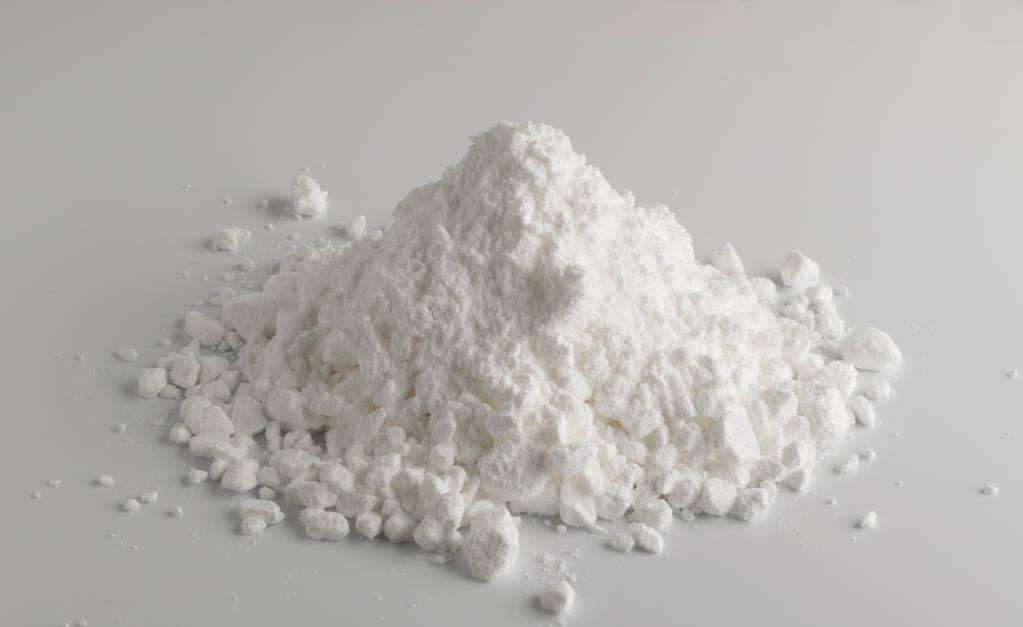
Calcium carbonate has been used as an inorganic filler for many years in plastic filling. In the past, calcium carbonate was generally used as a filler to reduce costs as the main purpose, and received better results. In recent years, with the widespread use of production and a large number of research findings, filling a large amount of calcium carbonate can also be done without significantly reducing the performance of the product, and even some aspects will be greatly improved, such as mechanical properties, thermal properties and so on.
01 Introduction to calcium carbonate
There are two main types of calcium carbonate: heavy calcium carbonate (commonly known as heavy calcium) and light calcium carbonate (commonly known as light calcium).
Heavy calcium is made by directly crushing natural calcite, limestone, chalk, shells, etc. by mechanical means (with Raymond mill or other high-pressure grinding).
Light calcium, also known as precipitated calcium carbonate, is the calcination of raw materials such as limestone to generate lime, and then add water to digest lime to generate lime milk, and then into the carbon dioxide precipitate, and finally dehydrated, dried and crushed. Or first use sodium carbonate and calcium chloride for a complex decomposition reaction to form a calcium carbonate precipitate, and then by dehydration, drying and crushing to prepare.
Due to the different preparation methods, the light calcium accumulation volume is large and appears light, and in fact, the difference in density between the two is very small. The density of light calcium was 2.4 to 2.7 g/cm3, and the density of heavy calcium was 2. 7~2. 9 g/cm3。
Heavy calcium particle size is generally larger, the distribution is wider, and the particle shape is irregular; while light calcium has a crystal shape and smaller particle size.
02 Technical indicators of calcium carbonate
The main technical indicators of calcium carbonate are: mesh number, whiteness, calcium carbonate content.
Mesh: mesh refers to the number of holes in a certain area of screen mesh, the larger the mesh, the smaller the particle size, the more complex the production process required. The larger the mesh number, the more active the filler particles are, the easier to bond with the plastic matrix, the compatibility is better, but the dispersion becomes worse. Common mesh numbers are 400, 600, 800, 1000, 1200, 2000. Usually, large mesh fillers need to be surfaced to improve their dispersibility.
Whiteness: Since pure calcium carbonate is white, the higher the purity of calcium carbonate products, the whiter the product and the less variegated. Ferrides, silicon, etc. will make the product appear yellow, dark and other variegated. Generally speaking, calcium carbonate can be used as a white dye for plastics when the whiteness is higher than 90%, but many manufacturers do not meet the 90% standard and even launch products with up to 97% whiteness. Products with higher whiteness, higher grade, less impurities, not easy to damage the processing equipment, in the plastic coloring, the color is more pure, more stable.
Calcium carbonate content: refers to the calcium carbonate content of limestone raw materials, which can also be said to be pure.
03 Application of calcium carbonate
Calcium carbonate is widely used, and most plastics can be used. The addition of calcium carbonate has a certain effect on improving some properties of plastic products to expand their application range, and in plastic processing they can reduce resin shrinkage, improve rheological behavior, and control viscosity. It can also play the following roles:
(1) Improve the dimensional stability of plastic products;
(2) Improve the hardness and rigidity of plastic products;
(3) Improve plastic processing performance;
(4) Improve the heat resistance of plastic products;
(5) Improve the astigmatism of plastics;
(6) Can make the product have certain special properties;
(7) Reduce the cost of plastic products.
Used in general plastics, the number of meshes is usually sufficient as long as 400 meshes. Calcium carbonate is filled into plastic, just like adding a skeleton to plastic, so that the dimensional stability and hardness of plastic can be improved, and the wear resistance and gloss of plastic can be improved to a certain extent. As commonly used in PP, PE, PVC plates, pipes.
Calcium carbonate is non-toxic, odorless, non-environmental pollution, is a common mineral in the natural environment, suitable for adding to biodegradable plastics, food packaging plastics, will not have adverse effects on people and the environment. There are also studies that show that biodegradable plastics with calcium carbonate added degrade faster in the soil.
Lightweight calcium carbonate has a characteristic, relatively absorbent oil, easy to absorb plasticizers in plastics, resulting in poor plasticizing effect, to improve this situation, calcium carbonate can be modified treatment.