During the Three Kingdoms period, Pu Yuan, a famous weapon maker of the Shu Han Dynasty, forged three thousand swords for Zhuge Liang at Xiegukou (in present-day southwest of Zhouzhi County, Shaanxi), "a gold-made vessel with special anomalies". After the knife was cast, in order to test the quality, Pu Yuan asked the soldiers to fill the iron beads with bamboo tubes, raise the knife and slash, such as cutting grass, the bamboo tube broke and the iron beads cracked, and people praised the steel knife cast by Pu Yuan as a "divine knife" that could "cut gold and jade, and cut iron like mud".
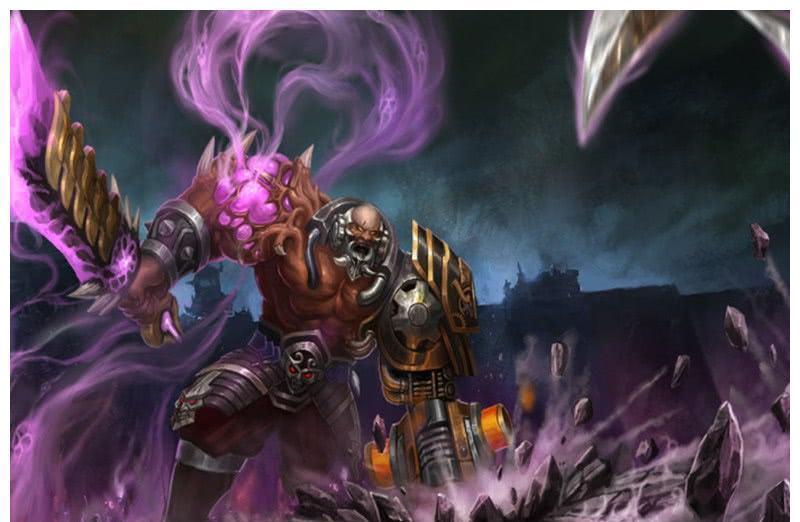
How is the "Divine Sword" refined? This should start from the advanced steelmaking process in ancient China.
China is one of the earliest steel producing countries in the world. Archaeologists once excavated a copper lattice "iron sword" in the tomb of Yangjiashan in the late Spring and Autumn period in Changsha, Hunan Province, which passed the metallographic examination and proved to be made of steel. This is the earliest steel object we have seen in China so far. It shows that since the late Spring and Autumn Period, there has been steelmaking production in China, and steelmaking production in China has a history of more than 2500 years.
During the Spring and Autumn Period and the Warring States Period, the weapons made by the Chu State were famous all over the world. Both the Book of History and the Book of Gowzi and the Book of Soldiers speak of the blades of weapons produced by wan (present-day Nanyang, Henan Province) in the Chu state of Chu, which were as powerful as bee stings, which must have been made of steel. Because the iron sword is too soft, it is impossible to reach the sharpness of a bee's thorn. At that time, the swords used by western ancient Roman soldiers were wrought iron, and when they clashed on the battlefield, they were bent with one stab, and before they stabbed, they had to be placed on the ground and stepped on with their feet. In the 1st century AD, the European Pliny once said: "Although there are many types of iron, none of them can compare with Chinese steel." "But during the Spring and Autumn Period and the Warring States Period, what method did Chinese take to carry out steelmaking production?" People have not found records in the literature, but archaeologists have revealed the oldest steelmaking method in China when scientifically testing some of the steel weapons excavated in Yanxiadu, Yixian County, Hebei Province.
We know that the main difference between pig iron, wrought iron and steel is in the carbon content, iron with a carbon content of more than 2%, called pig iron; the carbon content is less than 0. 05% iron, called wrought iron; carbon content in 0. 05%-2% of the iron, called steel. The earliest steelmaking process in ancient China was: charcoal was first used as fuel, and iron ore was smelted into a sponge-like solid block in the furnace, and then taken out after the furnace was cold, called block ironmaking. Block iron has low carbon content, soft texture and many impurities, and is the wrought iron refined by early humans. Then use a block of iron as a raw material, heat the carbon absorption in the carbon fire, increase the carbon content, and then after forging, remove the impurities and infiltrate the carbon, so as to obtain steel. This kind of steel is called block ironmaking carburized steel. The steel weapons unearthed in Yanxiadu, Yixian County, Hebei Province, are all made of block iron-made carburized steel.
Knives made of block iron-making carbon-permeable steel, although relatively sharp, still cannot reach the level of being able to "cut gold and jade, and cut iron like mud". Because the quality of this steel is not good enough, how much carbon infiltration of this steel is made, whether the distribution is uniform, and the degree of impurity removal are very difficult to grasp, and the production efficiency is extremely low. In order to improve the quality of steel, ancient Chinese craftsmen invented a new process of "hundred steelmaking" from the middle of the Western Han Dynasty.
The so-called "hundred steelmaking" is to repeatedly heat and fold the iron forging, so that the structure of the steel is dense, the composition is uniform, and the impurities are reduced, thereby improving the quality of the steel. Swords made of hundreds of steels are of high quality. In 1974, in the Cangshan Han Tomb in Linyi District, Shandong Province, a steel knife made in the sixth year of the Eastern Han Dynasty (112 AD) was excavated, with a total length of 111. 5 centimeters, the back of the knife has a wrong gold inscription: "Yongchu sixth year of May C noon made thirty-a-thousand-large knife Ji Yang Yi descendants." "湅" means refining. This is the earliest product of the Hundred Steelmaking type excavated so far. Scientific tests have shown that the carbon content of this steel knife is relatively uniform, the blade is quenched, and the impurities contained are similar to modern wrought iron. There are many varieties of hundred steelmaking, which can be found in the records: "five refining", "nine refining", "thirty refining", "fifty refining", "seventy-two refining" and "hundred refining". The specific meaning of these specific numbers in front of the alchemy word, researchers generally believe that it refers to the number of times heating, that is, how much fire is refined. Shen Kuo, a famous scientist of the Northern Song Dynasty, described in the "Mengxi Pen Talk" that the process of cizhou hundred steelmaking was to burn and forge more than a hundred times continuously until the pounds were not reduced. Cao Cao had ordered Yousi to make five "hundred sharp knives", which were called "hundred refining weapons" in the "Inner Commandments". Sun Quan had three swords, one of which was called "Bai Lian". Pu Yuan is a sword made by Liu Bei, with the inscription "Seventy-Two Refinements". It can be seen that during the Three Kingdoms period, hundred steelmaking was already quite common. The demand for hundred steelmaking is getting bigger and bigger, because the production efficiency of its raw material block ironmaking is very low, and it must be "cooled" after smelting to get it, so the development of hundred steelmaking is limited. In order to break through this limitation, ancient Chinese craftsmen invented a new pig iron steelmaking technology - fried steel.
Frying steel is to heat the pig iron to melt or basically melt, stir it in the furnace, and use the oxygen in the air to carbonize the pig iron, so as to obtain steel. This new steelmaking process can be found in the historical books of the late Eastern Han Dynasty. In book 72 of the Taiping Jing, it is recorded: "Let the engineer strike the smelting stone, and ask it to burn the iron to smelt it, so that it will become water, but then make the good workers forge it, and become the mo evil (ancient sword)." Although this passage does not explicitly put forward the word fried steel, it includes the steel frying process. Because the iron ore is refined into a liquid, of course, it can only be pig iron, and before the "Naihou Wan forging", it must be fried into steel or wrought iron (in fact, wrought iron is a fried steel with very low carbon content), otherwise pig iron cannot be forged, let alone "ten thousand forging". This is a whole process of smelting iron ore into pig iron, then frying steel, and finally forging into high-quality weapons. The invention of fried steel is a technological revolution in the history of steelmaking. In Europe, steel frying began in England in the 18th century, more than 1600 years later than in China.
During the Three Kingdoms period, steel frying was still a new technology, and most blacksmiths had not yet mastered it. From the "Biography of Zhuge Liang" about Pu Yuan casting a knife for Zhuge Liang at the mouth of the Xiegu Valley, "a gold made of ware, a special abnormal method", we can judge that Pu Yuan's casting knife this time must have used steel frying technology. In addition, in order to forge a "divine knife" that can "cut gold and jade, and cut iron like mud", the last process of quenching is also crucial. The so-called "quenching" is to first put the beaten steel knife on the stove and burn it red, and then immediately put it into cold water and dip it properly to let it cool suddenly. Repeat this a few times, and the steel knife will become tough and elastic. The quenching process seems to be easy, but it is extremely difficult to grasp the right thing, and the heat of the heat, the degree of cooling, and the quality of the water have a lot to do with it. Quenching is not enough, the blade is not hard, easy to curl the edge; quenching over the head, the blade will become brittle, easy to break; quenching is appropriate, must have extremely rich experience. According to the "Biography of Zhuge Liang", Pu Yuan has studied the water quality used for quenching. He believes that "Shujiang Is Refreshing" is suitable for quenching knives, while "Han shui is blunt and weak" and cannot be used for quenching, and Fushui is not available. He made a knife for Zhuge Liang at the mouth of the Xiegu Valley, and specially sent soldiers to Chengdu to fetch river water. Due to the rugged and difficult mountain road, the river water taken was overturned by more than half, and the soldiers mixed in some living water. After the water arrived, it was immediately recognized by Pu Yuan, "so Xian Qi was shocked and called Shen Miao." "In 1700 years ago, Pu Yuan discovered that the quality of water can affect the effect of quenching, which is a great achievement. In Europe, it was not until modern times that this problem began to be studied.
In summary, Pu Yuan's "sharp knife" was made by using the advanced steel smelting technology at that time and combining rich quenching experience.