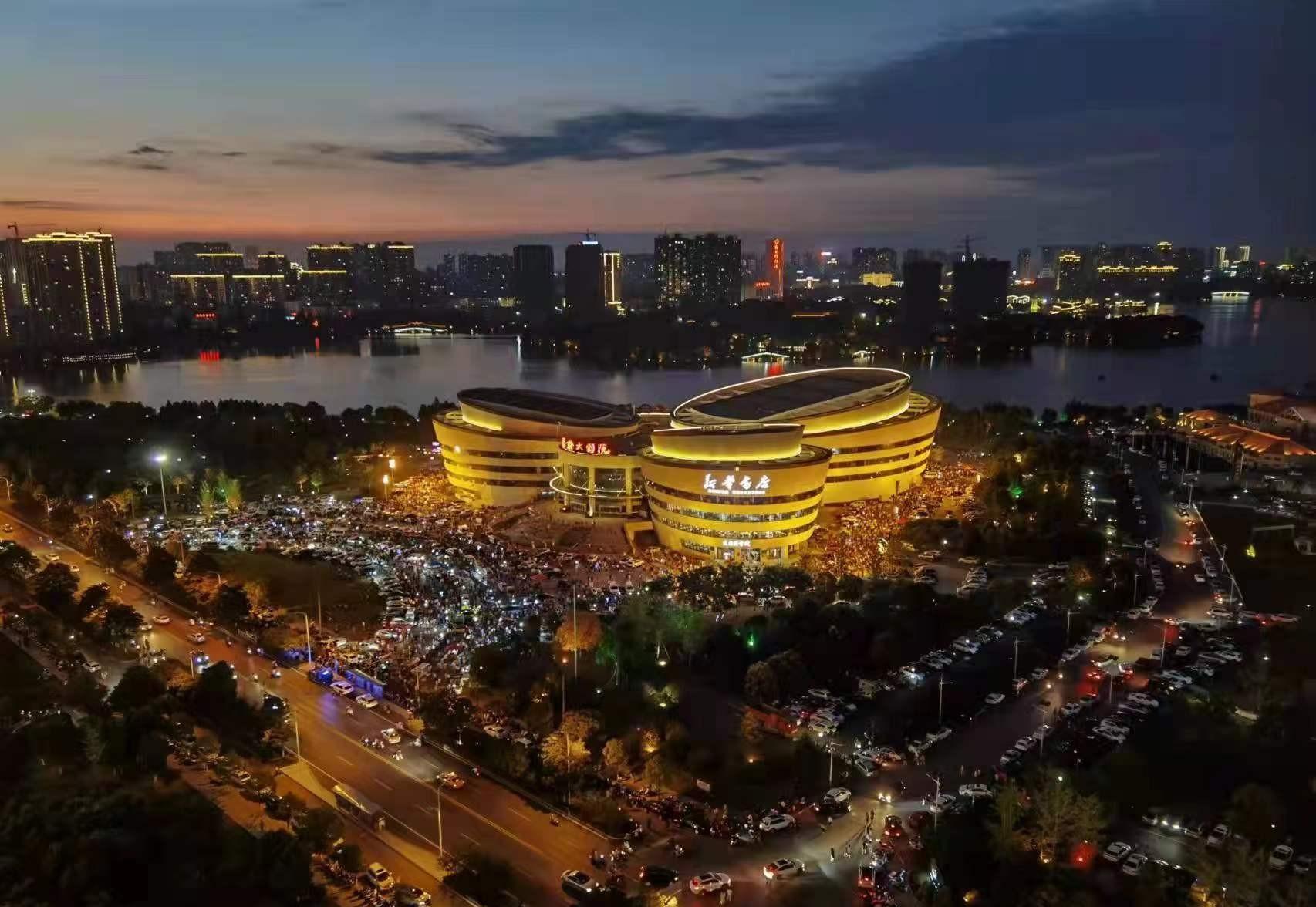
1. Purpose and Requirements
1.1 In order to establish the content, form and rectification procedures of safety inspection, timely discovery of problems, timely take measures, eliminate the unsafe state of things, correct unsafe behavior of people, promote safety management, and achieve safe production, these Regulations are specially formulated.
1.2 Safety inspection is an important means to do a good job in safe production, and its discretionary tasks are: to discover and identify various dangers and hidden dangers, supervise rectification, supervise the implementation of various safety rules and regulations, and stop illegal commands and illegal operations.
1.3 Safety inspections should implement the principle of combining leadership with the masses, and in addition to regular inspections, mass comprehensive inspections, professional inspections, seasonal inspections and daily inspections should also be carried out every year.
1.4 Safety inspection activities must have a clear purpose, requirements, content and specific plan, and the "Safety Checklist" shall be formulated.
1.5 Establish a safety inspection organization with the participation of the company's leaders and relevant functional personnel, so as to organize and rectify at the same time, and summarize and promote advanced experience in a timely manner.
2. Scope of application
This regulation is applicable to the safety technical inspection of each department of the company.
3. Duties
3.1 The Ministry of Safety and Environmental Protection is a functional department of safety inspection management, responsible for the drafting and management of safety production inspection regulations.
3.2 Each unit is responsible for the implementation of these Measures.
3.3 The safety production work of each workshop shall be supervised and inspected by the workshop safety officer.
4. Working procedures
4.1 The form of safety inspection can be divided into company-level safety inspection, division-level safety inspection, workshop-level safety self-inspection, team-level safety inspection, daily inspection, professional inspection, seasonal inspection, inspection before and after holidays and irregular special inspection. All kinds of inspections should be prepared with corresponding safety checklists, and checked item by item according to the inspection content.
4.1.1 Company-level security checks
Led by the company's leaders in charge of safety production, the relevant middle-level management personnel participate in the inspection, which is carried out once a month. The safety hazards detected shall be summarized by the Ministry of Safety and Environmental Protection, submitted to the relevant departments for rectification, and tracked the rectification.
4.1.2 Safety inspection at the division level
Led by the manager of the business department, the directors of each workshop participate in the inspection, which is carried out once a week. The safety hazards detected shall be summarized by the safety management personnel of the division, and shall be handed over to the relevant workshops for rectification, and the rectification shall be tracked, and the inspection shall be reported to the Ministry of Safety and Environment for the record. Rectification projects that cannot be implemented for the time being shall be reported to the company's safety and environmental protection department with rectification plans and measures, and the safety and environmental protection department shall report to the company's leaders to organize rectification according to the actual situation.
4.1.3 Workshop-level safety self-inspection
The workshop director and department leader are responsible for organizing the workshop safety officer and team leader to conduct inspections, at least three times a month, and each inspection should carefully fill in the workshop safety production inspection records, and the inspection situation should be reported to the Safety and Environmental Protection Department for the record.
4.1.4 Team level security inspection
The team leader shall organize the workers of the class to carry out the inspection on time and on time within the scope of their respective work, and strictly implement the handover system.
4.1.5 Routine examination.
4.1.5.1 Whether the understanding of safe production is correct and the sense of safety responsibility is; whether special operations are certified to work; whether they dare to struggle against the thoughts and behaviors of ignoring safety; and whether they seriously learn lessons from the ideology when an accident occurs.
4.1.5.2 Whether the safety activities are carried out conscientiously and whether the various records are complete.
4.1.5.3 Whether the leader puts safe production on the important agenda, whether he adheres to the leadership duty, whether he correctly handles the relationship between safety and production; whether he achieves the "five simultaneous" safety production, the implementation of safety education for employees, whether problems can be seriously dealt with, and whether safety technical measures and rectification measures for unsafe factors are seriously implemented.
4.1.5.4 The implementation of the various systems of safe production, the establishment, soundness and implementation of the safety technology operating procedures of each type of work; whether there is illegal command, non-implementation according to the operation procedures and standards, illegal operations, whether there is a workshop department safety management system and implementation. In the implementation of labor discipline, there are no violations of discipline such as leaving posts, colluding posts, and sleeping on posts.
4.1.5.5 Whether various raw materials are input in accordance with regulations, whether the operation of each unit is operated according to regulations, and whether the original records of operations are truthfully recorded.
4.1.5.6 Whether the safety conditions of machinery, instruments, plants, passages, safety devices, fire-fighting equipment, etc. are good, whether the work and appliances are stacked neatly, whether the labor protection supplies of employees are well worn and stored, and whether the fire passages are unobstructed. Whether the production site is managed according to the fixed requirements. Safe and civilized production, whether the signs are complete, whether the lighting is sufficient, the safety protection facilities are complete and reliable, the safety signs are eye-catching, and whether there are hidden dangers in safe production on the spot.
4.1.5.7 Whether the investigation, reporting and handling of employee work accidents adheres to the principle of "four do not let go" (that is, the cause of the accident is not clearly investigated, the person responsible for the accident is not dealt with, the rectification measures are not implemented, and the lessons are not learned).
4.1.5.8 Check whether the operating environment and working conditions, production equipment and corresponding safety protection facilities meet the requirements of safety standards, check whether the use of raw materials and toxic, harmful, flammable, explosive, material gases and other safety accident prevention measures, check whether the use of personal protective equipment meets safety protection standards, as well as ventilation, lighting, safe passages, safe exits and other operating environments, and whether labor conditions meet the relevant safety protection standards.
4.1.5.9 Safety inspections specified in the safety management assessment content;
4.1.6 Professional safety technical inspection.
The heads of each professional department shall lead the organization of the personnel of the system. Inspection at least four times a year, the content is mainly fireproof and explosion-proof, dustproof and anti-toxic, safety devices and pressure vessels, dangerous goods, electrical devices, mechanical equipment, plant buildings and safety facilities, personal safety, labor protection appliances, ventilation, dust removal, noise, shields, railings, manholes and other safety devices, etc.; inspection of civilized production, environmental health, etc. to carry out professional inspections, and the inspection items in accordance with the relevant provisions to establish safety technical files, copied to the Quality and Technology Department.
4.1.6.1 Spreader inspection: including lifting tongs, wire ropes, chains, rings, etc.
4.1.6.2 Lifting equipment inspection: hooks, accident switches, stroke limit switches, sky wheels, wire ropes, etc. of the crane.
4.1.6.3 Electrical inspection: The lighting in the workshop is not allowed to be connected to one place. Metal enclosures of electrical facilities protect grounding, temporary lines, power distribution and power outage devices, equipment, instruments, safety interlocks, alarm instruments, safety conditions;
4.1.6.4 Machine safety protection device: such as the shaft head should have a set, the wheel should have a cover, the table should have a fence, the pit should have a cover, etc.
4.1.6.5 Pressure vessel safety inspection: inspection of boilers, pressure vessels, various gas cylinders, special types of work and utensils, etc.;
4.1.:6.6 Safety inspection of flammable and explosive places: mainly for dangerous chemical warehouses, acetylene warehouses, storage tank areas for major hazard sources, coal silos, sulfur warehouses, etc. Check whether explosion-proof, anti-electric shock, lightning protection, anti-static grounding, lightning protection grounding, fire prevention, explosion protection, fire management and fire fighting facilities are in good condition;
4.1.6.7 Warehouse inspection: whether fire signs, fire fighting facilities, doors and windows, lamps, etc. are intact and effective;
4.1.6.8 Check process operation, running, running, dripping, leakage, plugging, string, etc.;
4.1.6.9 The professional safety inspection shall be organized by the Safety and Environmental Protection Department, led by the relevant deputy general manager in charge, and the electrical, technical, equipment and related technical personnel, safety personnel and the main leaders of each workshop shall conduct a joint inspection.
4.1.7 Seasonal security checks:
Led by the supervisors of each department, according to the company's geographical location and climatic characteristics, fire and explosion prevention, rain prevention, flood prevention, lightning protection, heat prevention and cooling, wind prevention and anti-freeze and warmth work, etc., to carry out preventive seasonal inspections, and the inspection and rectification content to establish safety technical files.
4.1.7.1 Spring safety inspection, with lightning protection, anti-static, anti-collapse, anti-running drip and fire prevention as the key inspection content;
4.1.7.2 Summer safety inspection, focusing on flood prevention, heat prevention, explosion prevention and personal injury prevention;
4.1.7.3 Autumn safety inspection, focusing on fireproof, explosion-proof, anti-freeze and thermal insulation;
4.1.7.4 Winter safety inspection, focusing on fireproof, explosion-proof, anti-freeze, anti-slip and anti-toxicity;
4.1.7.5 Seasonal safety inspection shall be organized by the Ministry of Safety and Environmental Protection, led by the leader in charge, and joint inspection shall be carried out by electrical, technical, equipment and related technical personnel, safety personnel and the main leaders of each workshop.
4.1.8 Holiday safety checks:
4.1.8.1 Before important holidays (such as: New Year's Day, Spring Festival, May Day, Eleventh, etc.), in order to ensure safe production during the holidays, safety inspections should be carried out;
4.1.8.2 The safety inspection on holidays shall be conducted by the Ministry of Safety and Environmental Protection to organize technical personnel and safety personnel to conduct self-examination and make records;
4.1.8.3 The following conditions shall be carefully checked before the festival:
4.1.8.3.1 Preparation of raw materials, fuels, auxiliary raw materials and spare parts for production;
4.1.8.3.2 Storage and storage of inflammable and explosive materials;
4.1.8.3.3 Fire prevention and safety of tank farms for the storage of flammable, combustible and explosive materials;
4.1.8.3.4 Implementation of holiday production safety measures;
4.1.8.3.5 Labor discipline, implementation of operating procedures and pre-holiday safety education;
4.1.8.3.6 The safe operation of various types of equipment and the rectification of hidden dangers;
4.1.8.3.7 Implementation of duty personnel on holidays.
4.1.9 Irregular safety checks
4.1.9.1 Is mainly divided into post worker inspection and management roving inspection at all levels. Production workers should conscientiously perform the post safety production responsibility system, carry out handover inspections and in-class inspections; leaders at all levels and management personnel of functional departments must conduct inspections within their respective business scopes, discover problems, and assist and supervise relevant departments to carry out rectification.
4.1.9.2 New, modified and expanded device operation, trial operation, commissioning acceptance inspection, equipment before and after maintenance inspection, temporary professional inspection and production problems must be carried out safety inspection. The inspection is carried out by the competent functional department, the workshop and the team.
4.1.10 Comprehensive safety inspection: including safety inspection of all aspects of the production site. According to the company, the general dispatching room, each division, and the workshop (team), the deputy general manager in charge, the director of the general dispatching room, the manager of the division department, and the director of the workshop organize the relevant departments, dispatchers, and team personnel to conduct inspections with the "five checks" (checking the leadership, checking the ideology, checking the system, checking the discipline, and checking the hidden dangers) as the central content. Inspection and rectification projects should be reported to the superior. The company level (including holiday inspection) is not less than four times a year, the business department checks once a month, and the general dispatch room and workshop are inspected once a week.
4.1.11 Other Security Checks.
4.1.11.1 Inspection of the layout and progress of each unit when carrying out safety activities;
4.1.11.2 Inspection of the implementation of newly formulated regulations and systems for safety management.
4.1.12 Safety production inspection content: five checks (check leadership, check ideology, check system, check discipline, check hidden dangers)
4.1.12.1 Check the leadership: whether the "chief responsibility system" has been implemented for safe production; whether the "safety first" has been achieved while leading the organization of production; whether the safety production has been included in the important agenda of the work of the unit; whether the "five simultaneous" production and safety have been achieved; whether the "four obediences" have been achieved when there is a contradiction between safety and production, progress, equipment, and energy conservation; and whether the personnel who have made meritorious contributions to safety work have achieved timely praise and rewards.
4.1.12.2 Check the idea: check the safety awareness of employees. In production, whether to adhere to the "safety first"; whether to strictly implement the safety technology operating procedures; whether there is risky recklessness, paralysis and luck thinking; check whether the violations of safety production are ignored, and whether they dare to take action and confront the hard.
4.1.12.3 Inspection system: the implementation of the safety production management system; whether there are any illegal commands, illegal operations and other behaviors.
4.1.12.4 Inspection discipline: Check the implementation of labor organization discipline, process discipline and safety discipline in production positions.
4.1.12.5 Check hidden dangers: whether there are unsafe factors in equipment, pipelines, containers, electrical instruments, etc. in production and operation; whether the platform railing is safe and reliable; whether the underground well and the dark ditch are kept unobstructed; whether the running, running, dripping, and leakage meet the specified standards; and the unsafe factors such as fire prevention, explosion prevention, poisoning prevention, electric shock prevention, object strike, and burning prevention.
4.2 Rectification of hidden dangers in safe production
4.2.1 Scope of accident hazards:
4.2.1.1 Unsafe factors that endanger production safety;
4.2.1.2 Hidden dangers of production facilities and safety facilities that cause accidents or expansion;
4.2.1.3 Working environments that may cause occupational diseases or occupational poisoning.
4.2.2 Management, implementation and acceptance of accident hazard management projects:
4.2.2.1 The hidden dangers found should be studied and formulated one by one to formulate a rectification plan, and rectification measures should be implemented item by item according to the management of the workshop and the team, and the rectification and reform should be rectified immediately without delay;
4.2.2.2 Register the hidden dangers detected, implement rectification measures, and achieve "three determinations" (that is, measures, responsible persons, and completion dates), and "two non-delivery" (that is, the team can rectify the non-delivery to the workshop, and the workshop can be rectified and not handed over to the company);
4.2.2.3 The hidden dangers detected must be rectified in time. If the limited material or technical conditions cannot be solved for the time being, risk reduction measures must be adopted and implemented, and then a plan is drawn up to solve the problem on schedule. If the business department and the workshop are unable to solve the problem, write a written report to the safety and environmental protection department of the company in time and apply for arrangement for solution;
4.2.2.4 Where major hidden dangers are found, before thorough rectification, all relevant departments and workshops shall take effective risk reduction measures and be supervised and implemented by the Ministry of Safety and Environmental Protection;
4.2.2.5 Projects that cannot be rectified temporarily, in addition to taking effective preventive measures, should be included in the technical measures, safety measures and maintenance plans within a time limit;
4.2.2.6 For hidden dangers that are not rectified on schedule, the "Hidden Danger Rectification Notice" method is implemented, which is filled in by the safety management personnel, issued by the Safety and Environmental Protection Department, signed by the person in charge of the workshop and handled within the specified time, and the "Hidden Danger Rectification Notice" should be archived for inspection;
4.2.2.7 All kinds of professional inspections, seasonal inspections and holiday inspections, the inspection results and rectification situation must be carefully preserved for the record;
4.2.2.8 Where all kinds of hidden dangers are found, and accidents are caused by failure to rectify in time, the person in charge of workshop safety should be held accountable.
4.3 Forms and precautions for security checks.
4.3.1 For the content of the inspection project, it is necessary to learn relevant regulations, policies, technologies and business knowledge in a targeted manner, and improve the level of regulations, standards and policies.
4.3.2 The self-inspection and mutual inspection are organically combined, the team is mainly self-examination, the workshop checks each other, learns from each other's strengths, and learns from each other.
4.3.3 Adhere to the combination of inspection and rectification, and the unsafe factors found in the inspection should be sorted out and analyzed according to the inspection records, and rectification measures should be taken. Where it is difficult to rectify and reform for a while, practical and effective preventive measures should be adopted.
4.3.4 Develop and establish security files. Collect basic data, grasp the basic safety situation, realize the dynamic management of hidden dangers of safety accidents and the source points of unsafe factors, provide data for the timely elimination of hidden dangers (potential risk factors), and lay the foundation for future safety inspections.
5 Supplementary Provisions
5.1 This system shall be implemented from the date of issuance. The matters not covered by this system shall be implemented in accordance with the relevant national standards, norms and regulations.
5.2 This system shall be interpreted by the Safety and Environmental Protection Department of the Company.