With the development of building industrialization, the application of stacked panels has been particularly extensive. How is this new process constructed? What are the key points in the field that need to be controlled? This paper takes the example of Jining Jiujulong Construction Company project to share and exchange the construction process and node quality control of stacked panels.
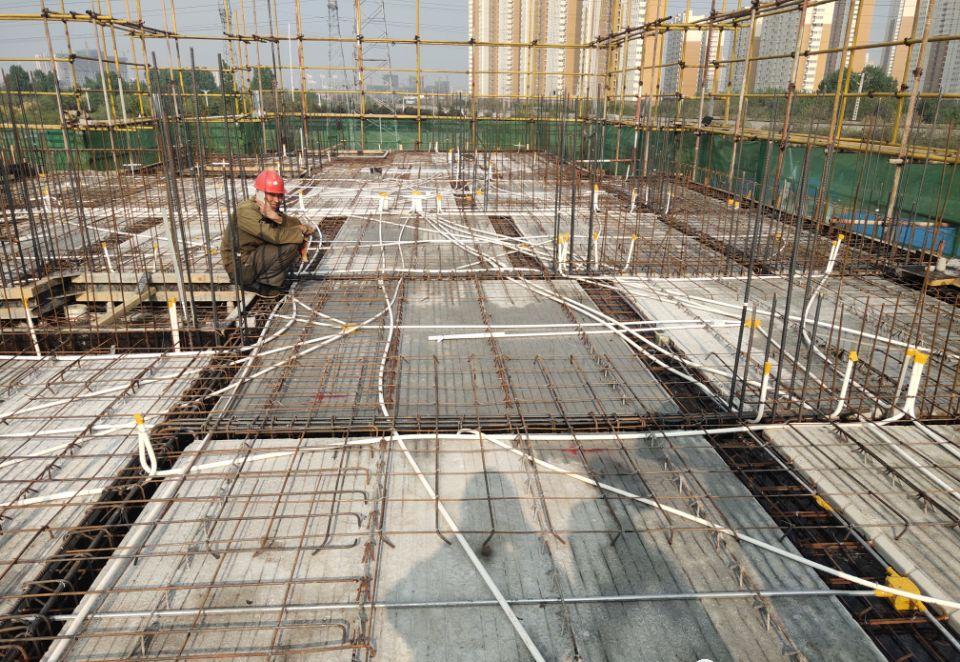
Construction process
Quality control of major nodes
1 Stacked board entry and acceptance
Acceptance Criteria:
The thickness of the stacked board is 60mm, the concrete strength grade is C30, the self-weight is about 150kg/㎡, the bottom surface is smooth and smooth, the color is uniform, and there are reserved openings and embedded parts.
The stack has a penetrating crack, does not receive goods, and is abandoned:
Stacked plate reserved rebar length measurement:
The size of the stacked plate is compared with the nameplate to check whether it is consistent:
The lock female is added in four directions of the embedded wire box and blocked, and the height of the lock female from the board surface is checked to see whether the construction requirements are met:
Each stack has a logo nameplate that compares to the drawings:
Four hoisting points of the stacked board are painted, and the installation direction is marked with paint:
Drawing laminated board mounting direction identification:
2 stacked plywood on-site stacking
I-beam is laid under the stacked plate to ensure the level:
Place the gasket, the upper and lower positions of the cushion are consistent, to ensure that the vertical force point is the same, to prevent the uneven force from causing cracks:
The stacked board is placed at a height, communicating with the component factory, and unifying into six layers to prevent cracks caused by high storage on site:
3 Template installation
The roof formwork is fully paved and the edge mold is laid without any impact on the finished construction product, mainly the flatness of the formwork and the reinforcement support in place.
Spread out the template
The edge mold is not laid under the support
The circumference of the stacked plate is adhered to the sponge rubber strip to prevent slurry leakage; the edge mold distance is about 500 on both sides:
4 stacked plate hoisting
When the stacking board is lifted, it is necessary to reduce the bending moment caused by self-weight in the non-prestressed direction as much as possible, and the steel flat lifting frame is used for lifting, and the 4 lifting points are evenly stressed to ensure the smooth lifting of the components, as shown in the following figure. When lifting, it is necessary to try to lift first, first lift 50 cm from the ground to stop, check the force of the wire rope and hook, keep the stacking board level, and then lift it to the sky above the working layer.
When in place, the stacked plate should be installed vertically from the top down, pause slightly at 20cm above the working layer, the construction personnel adjust the direction of the floor slab, align the edge of the board with the placement position line on the wall, pay attention to avoid the reserved steel bar on the stacked plate and the wall reinforcement fight, stop and slow down when lowering, and strictly prohibit rapid release, so as to avoid the impact force being too large to cause the plate surface to collapse and crack. Hoisting should be stopped when the wind is above level 5.
Stacked plate hoisting special spreader
5 formwork supports
6 beam tendon lashing
The reinforcement lashing is different from the original, after the stacked plate installation is completed, there are stacked plate reserve reinforcement on both sides of the beam.
7 plate steel bar lashing, line box embedded
The line pipe goes under the stacked panel truss to avoid the stampede of the line pipe, protect the line pipe and ensure that the line pipe is not exposed after the ground pouring is completed.
8 plates at the junction of the negative rib corners
At the junction of negative reinforcement, the distribution ribs are tied under the truss ribs to avoid the reduction of the protective layer caused by the intersection of multiple layers of reinforcement, which affects the flatness of the cast-in-place surface.
The distribution ribs are from underneath the stack truss ribs
9 concrete pouring
Before concrete pouring, water in advance to moisten to avoid affecting concrete and translibility due to water absorption on the stack.
10 concrete roof maintenance
Because the cast-in-place surface layer is only 7cm, it is necessary to strengthen the maintenance of watering, and each building is required to send daily maintenance photos to the working group.
11 Inspection of finished products after mold removal
Check the quality of concrete pouring molding without slurry leakage.
Frequently Asked Questions and Handling
Frequently asked question: Leaking slurry on both sides of the cast-in-place plate.
The main causes of slurry leakage are:
1. The sponge adhesive strip in the position of the plate and belt is not in place.
2. The support and reinforcement of the plate and belt position template are not in place, and the deformation and leakage of the formwork after pouring concrete.
Other reasons:
1. After the stacking board is hoisted, it is fine-tuned, and the artificial pry causes the destruction of the sponge rubber strip.
2. The gap between the stacked board and the template is large, and the rubber strip cannot guarantee that it will be completely blocked.
3. The stacked plate itself has warpage, and the bottom of the plate is uneven.
Sponge strip position deviation
There is a gap between the stacked board and the template
To avoid this problem, strengthen the inspection of the stacking plate hoisting installation stage:
1. Paste of sponge strips.
2. Strengthen the support and reinforcement of the plate and belt position template.
3. After the stacking board is hoisted, the formwork supports the secondary topping.
In view of the phenomenon of slurry leakage, timely correction is carried out and construction methods are corrected.