The patented die technology aims to extend the layer count limit of blown film beyond the standards of 9 and 11 layers currently considered high-tech.
BBS is continuing to develop die technology for the production of nanolayer blown films, the second of two recently developed technologies designed to push film extruders to research new processing processes to surpass structures currently considered to be at the top of the industry at 9 and 11 layers. The Italian machine manufacturer GAP has developed a technology with 3 feeding blocks to produce blown film with 27 microlayers with only one ring die.
Nanolayer technology has gained a foothold in the field of cast membranes, especially in tensile applications, thanks to the efforts of Clöeren Incorporated, which has developed feed block technology that enables processors to produce dozens of layers of films.
BBS, based in Spartanburg, South Carolina, USA, is run by Hank Schirmer, who retired from his position as director of new technology at Cryovac (now Sealed Air). Schirmer holds more than 100 patents, the latest of which is an all-nanolayer die granted in December 2020, a continuation of The Layer-Sequence Repeater (LSR) die technology invented by Schimmer about 20 years ago, which was later sold by BBS to a global film manufacturer that makes medical kits.
According to Schirmerer's explanation, the BBS's all-nanolayer die consists of many modules, each of which in turn consists of many cells that remove the melt from the two symmetrical positions of 180, thus providing better symmetry for each layer. Schirmer insists that this would control the thickness of each nanolayer more evenly. Each cell consists of 9 or more extremely thin discs (dies) nailed together. "These dies are the cornerstone of each module unit, can change the shape of the module unit, they are more or less like a set of Lego toys." Schirmer says, "Accordingly, this is compatible with every plastic and can be adjusted to the rheology of each resin to achieve optimal flow. ”
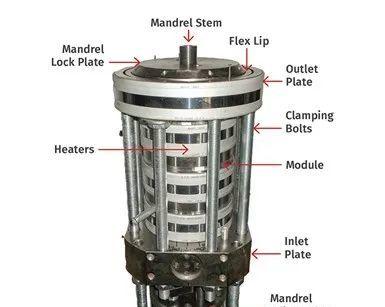
The new nanolayer die can be available in both 1X (as shown) and 2X (higher yield) designs, especially with external clamping bolts that prevent leakage
Schirmer further explains: "With the modular setup of cells and disks, this all-nanolayer die can meet any of your needs. We no longer need to describe this co-extrusion die in terms of the number of layers it produces. You just need to assemble the modules and you get what you want — one layer, two layers, or 50 layers to 100 layers— and you know that each layer is as evenly as thick as possible. The die is responsible for the orientation of all melts, so you only need to use one extruder to extrude every material used. Whether it's 3 or 50 layers, the die determines everything. ”
The latest patent is about this module. This is a often complex process of assembling precision laser-cut and hand-completed disks. This special modular assembly method determines the structure of the film. In a die combination, there can be multiple modules.
The new module consists of a module cell, each of which has two melt inlets with opposite structures, which can produce two layers of the same material or different materials, so that the thickness of all nanolayers of different materials produced by the die can be better controlled. Schirmer said: "Basically, the module is the core and soul of the die, which determines the quality of the film produced. By replacing the modules, the processor can change the structure of the film. He can have multiple modular configurations that can be used in the die at any time, which is similar to a shaver and a razor blade: the shaver remains the same, but the shaver blade can be replaced, and it is the shaver blade that decides to shave. ”
Modules can be pre-arranged and placed in the module inventory so that they can be placed in the die whenever needed, which reduces downtime every time the die is cleaned or the film structure is changed. "Heating the modules to about 900°F (about 482.2°C) or burning the polymers in other ways makes it easy to clean these modules, and we only need a wood stove to burn for 4h. After cooling, simply blowing off the ashes, the module can be put back into service without disassembling it. Schirmer said.
This figure shows the thin film structure of nylon 6/EVOH material containing 75 nanolayers made in a BBS die, and these layers around the circumference of the film bubble are concentric and continuous
These dies are designed with external clamping bolts. "This is done to obtain the highest clamping pressure so that the die does not leak." Schirmer says, "The module gets hot, but the clamping bolts stay cool. Heat causes the module to expand, but the cold bolts are pulled tighter than you would with a torque wrench. ”
Since Schimmerer unveiled his LSR technology, he has established contacts with two blown film system suppliers: China's Jinming Company and Canada's Alpha Marathon, which tested high-output LSR dies. In addition, BBS sold the die to a French processor. Alpha Marathon, on the other hand, sold a line to a processor in Asia with Schimmerer's die. BBS also sold several dies to a European processor, as well as two U.S. processors. Now BBS operates independently.
The new nanolayer dies are available in 1X and 2X designs. The 1X die has a ring of up to 8 in (approx. 20.32 cm) and a maximum output of 300 lb/h (approx. 136 kg/h). The 2X die has a ring of up to 18 in (about 45.72 cm) and can be used on production lines with an output of more than 1000 lb/h (453.6 kg/h).
BBS has a film laboratory in Spartanburg that can be tested by customers. "We can show them how to assemble modules with cells and cells with disks." Schirmer said, "This can be simplified by using a simple CAD calculation program. ”
BBS has a production line of 6 extruders in its laboratory that can manufacture films containing 52 nanolayers
Schirmer is filing a new patent for further improvements to the die, including manufacturing more symmetrical nanolayers and reducing the number of extruders used to fabricate complex structures. "We are patenting a new blown film line consisting of fewer extruders designed to manufacture a wide range of high-quality films to demonstrate the full range of functional features that these new dies have." Schirmer said. The new line is currently installed in BBS's laboratory in Spartanburg.