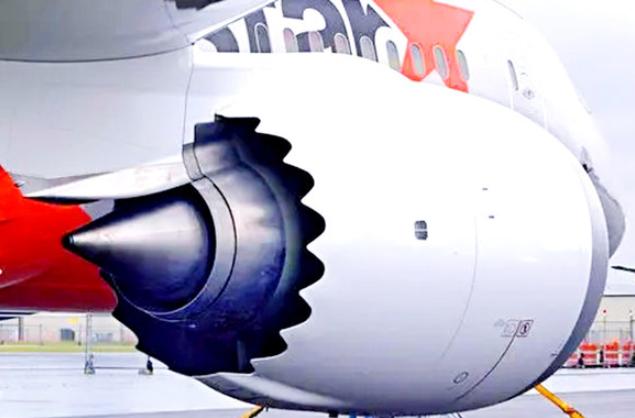
Recently, the GEnx engine used special vacuum equipment to complete more than 3,000 cycles of vacuum tests in a simulated harsh environment, and achieved excellent durability test results.
It is understood that the GEnx engine has been in service for 10 years, and more than 2700 GEnx engines are currently in service and on order. The GEnx engine uses lightweight, durable materials and advanced design processes to reduce weight, improve performance and reduce maintenance costs, resulting in sales records for high-thrust commercial turbofan engines. A number of key technologies support the engine's low fuel consumption, low pollution, low noise design goals.
Provides megawatt-class power
On traditional large passenger aircraft, most of the systems are driven by compressed air, such as the high-pressure air used in the cabin air conditioning system, which is provided by the engine high-pressure compressor. At the same time, the high-pressure hydraulic pump of the hydraulic system is driven by the drive shaft on the transmission receiver of the engine attachment. The Boeing 787 uses a non-induced architecture, using an alternating current motor to drive the air compressor and hydraulic pump, becoming a "quasi-all-electric" aircraft. For this, a high-powered alternator is required to be driven by an engine to provide sufficient electrical energy.
Conventional airliners drive 1 generator per engine and 1 generator per APU. The Boeing 787 has a total of 6 generators, 2 GEnx engines drive 4 generators, providing the main electrical energy, each generator has a power generation capacity of 250 kilowatts, and the APU drives 2 secondary generators, each with a power generation capacity of 225 kilowatts. If 6 generators are started at the same time, they can provide 1.45 megawatts of electrical energy, which is 4 times the power generated by the Boeing 777 and equivalent to the power generation capacity of solar panels the size of 10 football fields.
Reduced fuel consumption
Huge outer culverts and composite fans. GEnx engines have a 9:1 bypass ratio and fan blade diameters of up to 2.8 meters, reducing weight by using carbon fiber composite fans and receivers. The previous generation of fans was made of titanium alloy, which has a higher specific strength, but the specific strength of carbon fiber is higher and the rigidity is stronger. Carbon fiber composite fans have a larger diameter and thinner thickness, and compared with titanium alloy fans, the new material reduces the number of fan blades from 22 to 18, achieving a 15% weight reduction and a higher upper fan speed limit.
The compressor has a very high boost ratio. The GEnx has compressors with the highest pressure ratio in commercial engines in service. Increasing the pressure ratio maximizes the use of the energy released by the fuel, and the more energy the turbine and spouts convert. The pressure ratio of the GEnx engine can reach up to 58:1, and while the pressure ratio is increased, the compressor stage is reduced, which is 4 stages lower than that of the CF6 engine. The GEnx engine improves the performance of the blades by adopting three-dimensional pneumatic technology, and the aerodynamic efficiency is further improved by manufacturing the integral leaf disc through integrated processing.
Reduced NOx emissions
The core technology of the double-ring premixed cyclone combustion chamber is to introduce an innovative premix concept while maintaining the advantages of zoned combustion. To optimize the combustion chamber temperature distribution factor and reduce NOx emissions, GE has applied microscopic layering technology in fuel nozzles to achieve a smooth transition to combustion. As a result, air and fuel are well pre-mixed before they enter the combustion chamber. There are 3 air cyclones for the fuel nozzle, of which 1 is used for the swirl intake of the main mixer and 2 for the swirl intake of the secondary mixer, which is the key to achieving the micro-layering technology of the fuel nozzle. The center of the nozzle is an ignition flame, and the main nozzle is circular, creating a two-layer swirl flow. During the premixing phase, a large amount of air is required to ensure the combustion of lean oil. This nozzle looks simple, but requires countless simulations and iterative designs, and such a complex structure would be difficult to manufacture without the latest generation of metal 3D printing technology. According to statistics, after research and development, its nitrogen oxide emissions have been reduced by 60%.
Double-ring premix cyclone can realize the combustion of poor oil in the whole working condition of the engine, high combustion efficiency, low flame temperature, low pollution emissions, is a more advanced, more concise structure of the combustion chamber, representing the development direction of modern aviation turbine engine combustion chamber engineering technology. The double-ring premix cyclone has also been further developed and used on LEAP and GE9X engines, enabling stronger oil-poor combustion and lower NOx emissions.
Reduce noise
The reduction in noise in the GEnx engine is mainly due to its signature exterior design , the jagged spouts. Since the turbofan engine needs to quickly spew air and gas out of the inner and outer culverts, the speed is much higher than the flow rate of the outside air, and the action with the outside air will cause violent mixing, resulting in huge noise, like a waterfall hitting the water. The serrated nozzles are used to control the air flow that ejects, causing each serrated tooth to produce small vortices, making the high-temperature and high-speed jets mix more softly with the outside air, greatly reducing the noise generated by the engine. (Author: He Peng, Tian Tao, Cheng Wenwang)