Panorama of the hollow glass bead industry chain
Hollow glass microspheres (HGM) is a micron-level spherical hollow lightweight ultra-fine powder, which is widely used because of its low density, insulation, fluidity and excellent dispersion, and is known as "space age material".
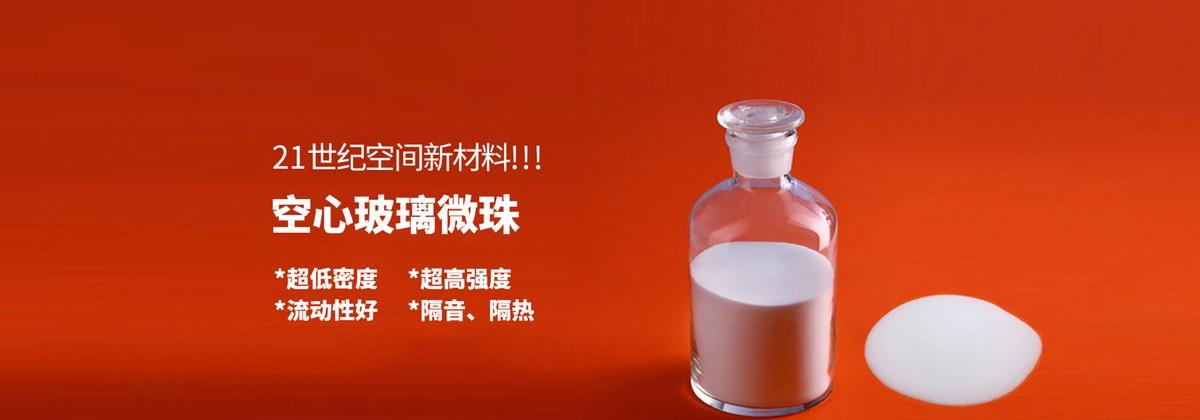
Source: Zhengzhou Shenglite Hollow Microbead New Material Co., Ltd
Introduction and raw materials for hollow glass beads
Glass beads
Glass beads are a new type of micron-level material, according to the structure can be divided into solid glass beads, porous glass beads, hollow glass beads.
Solid glass beads have a diameter of less than 0.8mm, and can be divided into high refractive index beads, water-repellent glass beads, colored glass beads, etc. according to different characteristics.
Porous glass beads are mostly prepared from minerals such as fly ash or coal gangue, which have the characteristics of good chemical stability, high strength, corrosion resistance and strong adsorption type, and can be used as catalysts and carriers for fixed enzymes in the brewing industry.
Compared with other materials, hollow glass beads have become a new type of silicate material due to their good physical and chemical properties.
Performance of hollow glass beads
It is a non-metallic inorganic material, which has the advantages of light weight, large volume, low thermal conductivity, high compressive strength, dispersibility, fluidity and good stability, and also has the advantages of low oil absorption, insulation, self-lubrication, sound insulation, non-absorbent water, fire resistance, corrosion resistance, radiation protection, non-toxic and other ordinary materials do not have excellent properties.
Parameters of the physical properties of hollow glass beads
Classification of hollow glass beads
According to the density, it can be divided into drift beads and sink beads.
Drift beads refer to HGM powders with a density of less than 1.0g/cm3; sinking beads refer to their density greater than 1.0g/cm3;
According to the source method, it can be divided into natural hollow glass beads and artificial hollow glass beads.
Natural hollow microbeads generally refer to fly ash hollow microbeads sorted and extracted from fly ash in thermal power plants.
Although the cost of extracting HGM from fly ash is low, but the fly ash beads are dark in color, there are many impurities, and there are often many open holes on the surface of the sphere, not only the shape is irregular, because the sintering temperature is different and the chemical composition and particle size of the pulverized coal make the glass composition and properties of HGM very different, and the true density of fly ash beads is generally relatively large, and its true density is often greater than 0.6g/cm3 after multiple sorting, so the application field is mostly limited to low-end products.
If you want to obtain high-performance, low-density, uniform particle size distribution of hollow microbeads, or continue to study the synthetic hollow microbeads.
Raw material for hollow glass beads
At present, the production method of hollow glass beads often uses organic alcohol salts, sodium silicate, boric acid, broken glass, etc. as the main raw materials.
sodium silicate
The production method of sodium silicate is divided into dry method (solid phase method) and wet method (liquid phase method).
Dry production is to mix quartz sand and soda ash in a certain proportion and heat it to about 1400 °C in a reverberation furnace to form a molten sodium silicate.
Wet production uses quartzite powder and caustic soda as raw materials, and reacts under 0.6~1.0MPa steam in a high pressure steamer to directly generate liquid water glass. Microsilica powder can replace quartz ore to produce sodium silicate with a modulus of 4.
boric acid
Boric acid has a wide range of applications in the glass industry, ceramics, machinery, agriculture, electronics and modern science and technology, and at the same time, boric acid is also an important raw material for the manufacture of various borides (boron carbide, boron nitride, boron fiber, etc.).
Special glass/waste glass
The preparation of glass beads using special glass or waste glass is an important research direction. For example, the HGM products developed by the glass powder method developed by Bengbu Glass Industrial Design and Research Institute have been successfully applied to the preparation of solid buoyancy materials used by China's first 4500-meter-class deep-sea remotely controlled unmanned submersible - "Haima" underwater robot.
Deep-sea submersible based on HGM composite foam material
Preparation and modification of hollow glass beads
The production process of hollow glass beads
Glass powder method
The glass matrix material is first crushed, a blowing agent is added to it, and then the particles containing the foaming agent are softened or melted by high temperature heat treatment, and gas is generated inside the particles and expanded to form a hollow ball, and finally collected by a cyclone separator or bag collector.
Preparation of hollow glass beads by glass powder method
This method can design a variety of glass systems, a variety of products, the quality is relatively high, can be used to produce high-performance hollow glass beads, is currently internationally recognized method of preparing high-performance hollow glass beads. However, the yield is low and the cost is relatively high.
At present, Kaisheng Substrate, which belongs to Bengbu Yuan, has built the first high-performance hollow glass bead production line with an annual output of 5,000 tons of glass powder, and has dozens of core products that have reached the international first-class level.
Droplet method
The solution containing the low melting point substance is spray dried at a certain temperature or heated by a high-temperature vertical furnace to form a hollow ball, which can be used to produce highly alkaline microbeads. The most obvious disadvantage of the beads prepared by this method is the difference in strength.
Preparation of hollow glass beads by droplet method
Jet granulation
First prepare an aqueous sodium silicate solution containing auxiliary special reagents such as boric acid, urea, ammonium pentaborate, etc., and then spray the solution into the spray dryer through the nozzle to generate particles with a certain particle size, and then heat the particles to foam, and finally form hollow glass beads.
Preparation of hollow glass beads by jet granulation
The hollowness rate of this method is high, the cost is relatively low, but its physical and mechanical properties are poor, especially in the compressive strength performance is much lower than that of the products produced by the glass powder method, and its chemical stability is relatively poor.
Subsequent studies have improved this method (after the improvement is called soft chemical synthesis method), and some metal oxides with low melting point, high viscosity and high surface tension tendency have been added to the production process, which greatly improves the performance of the product.
Sol-gel method
Using organic alcohol salts as raw materials, dry gels are prepared by a sol-gel process, then crushed, and the powder is heat treated at high temperature to prepare hollow glass beads. Due to the high raw material price, the cost of this method is very high and it is not suitable for industrial production.
Preparation of hollow glass beads by metal alkoxide method
Degradation of the shaft core method
American Stehan A. Letter et al. first proposed and conducted a large number of studies of a new method of preparing HGM. It is a low discharge polymer (GDP) layer doped with Si by plasma chemical vapor deposition with poly α-methylstyrene (PAMS) microspheres as the shaft core. The experimental parameters of the production of HGM mainly include: the degradation process, mechanism, temperature and so on of the mandrel.
Advantages: The prepared HGM ball wall does not form bubble defects, so the compressive strength is relatively high
Disadvantages: When the PAMS shaft core is degraded, the Surface Si-GDP shell is prone to collapse or fragmentation, and the Si-GDP shell is easy to blacken during oxidation treatment and it is difficult to obtain transparent HGM, so the preparation conditions need to be strictly controlled.
Surface modification of hollow glass beads
Hollow glass beads that have not been modified by the surface have shortcomings such as poor thermal insulation effect, no electromagnetic properties, and unsatisfactory surface hydrophobic performance, which seriously affect their application. Therefore, to broaden its field of application, it needs to be surface modified.
Combined agent treatment
Through the coupling agent molecule, the inorganic phase and the organic phase can be tightly combined, enhancing the interface adhesion, thereby improving the performance of the material. Common coupling agents can be roughly divided into three categories: silane coupling agents, titanate coupling agents, and organochromic compounds. Wherein the silane coupling agent contains a three-functional inorganic functional group, that is, [Si-(OR2)3], when treating the surface of the hollow glass beads, the silane coupling agent first hydrolyzed the alkoxy group to generate silanol, and then codension reaction with the Si-OH on the surface of the glass bead to form a chemical bond. It is a type of coupling agent with the largest amount, the largest variety and obvious modification effect.
Acid-base etching
Acid-base etching modification is mainly the use of acid-base corrosion, corrosion on the surface of the hollow glass beads out of the gully, the surface shape of the beads will be rough and uneven. When the corroded hollow glass beads are filled with resin, on the one hand, the polymer chain segments of the resin matrix can enter the gullies on the surface of the beads, producing an "anchoring" effect and increasing the force between the two interfaces; on the other hand, after etching, a large amount of silicon hydroxyl groups are generated on the surface of the beads, which is conducive to increasing the interfacial binding force between the two phases.
Plasma surface treatment
The surface of hollow glass beads contains a large amount of silicon hydroxyl groups, but the activity is low, and it is difficult to participate in chemical reactions. The plasma surface treatment can make the silicon hydroxyl group on the surface of the bead become the active center, which in turn triggers the polymerization of the monomer on the surface of the bead. Plasma modification achieves results by increasing the roughness of the bead surface, activating the bead surface, and plasma polymerization.
Surface coating treatment
It is the use of inorganic or organic matter to coat the surface of the beads to achieve the effect of modification. Some scholars use the alkali method to coat the surface of the hollow glass beads with a layer of TiO2 film, which can improve the brightness of the hollow glass beads, improve the reflectance of sunlight, and use the insulation coating prepared by it to have a better reflectivity of sunlight.
Surface graft polymerization modification
This type of modification is mainly based on the method of in situ polymerization using raw materials such as monomers and initiators to coat the surface of the filler with a layer of polymer. Reactive points are introduced on the surface of hollow glass beads, and then react with functional groups to achieve a modified effect. Its biggest advantage is that it is possible to design interface layers with different performances by selecting specific monomers and polymerization conditions, which has good theoretical significance.
Other surface modification methods
Hollow glass beads are an inorganic non-metallic material whose main components are SiO2 and Al2O3, so they do not have properties such as conductivity and electromagnetism. If the surface of the hollow glass beads is chemically nickel-plated, drilled, copper, silver, iron and other metals, it can have the function of absorbing electromagnetic waves and reflecting near-infrared, so it can replace the transition group metal powder with large density and magnetic properties as a conductive material, electromagnetic wave absorption or electromagnetic shielding material. In addition, with the continuous development and improvement of biotechnology, hollow microspheres have been continuously promoted and applied in this field with their unique structure and excellent properties. Caruso F. et al. report that by encapsulating biological enzymes in hollow balls, novel biofunctional materials can be obtained, and the hollow balls they prepared containing proteins and polymers can be injected into the organism as drug carriers.
2021 Hollow Glass Beads Related Dynamics
In April 2021, the results of "Ultra-light and High-Strength Hollow Glass Bead Preparation Technology and Industrialization" jointly completed by CNBM Bengbu Glass Industrial Design and Research Institute, Anhui Kaisheng Basic Materials Technology Co., Ltd. and China National Building Materials International Engineering Group Co., Ltd. were awarded the first prize of Anhui Provincial Science and Technology Progress Award.
In August 2021, the advanced powder material project of China Steel Mining Institute held a groundbreaking ceremony in Qingpu Industrial Park, Ma'anshan Economic Development Zone, and will build production lines such as carbon aerogel, high-performance hollow glass beads, and spherical weighted materials.
In August 2021, Gaoping Qihang Industrial Revitalization Fund completed all decision-making procedures and signed an investment agreement to invest 100 million yuan in the hollow glass bead project of Shanxi Hainuo Technology Co., Ltd.
In August 2021, 3M launched a new product of insulating glass beads for the 5G field. As the latest addition to 3M's high-strength insulating glass beads product line, the new product is a high-frequency high-speed (HSHF) resin additive with excellent performance and low signal loss that can be used in composite materials for 5G equipment and components.
3M hollow glass beads
Source: Official website
Application and market of hollow glass beads
In the early stage of the development of hollow glass beads, due to the high cost, it was mainly applied in cutting-edge fields such as aerospace and national defense. With the development of science and technology, hollow glass beads can be industrially produced, becoming a low-priced, resource-rich new inorganic materials, insulation and fireproof materials, high-grade insulation materials, composite materials, petrochemicals, coatings and other military and civilian fields have been widely used.
Application in emulsified explosives
Hollow glass beads have the characteristics of low oil absorption rate and low density, which can be used as a density adjuster and sensitization effect after the introduction of emulsified explosives, thus effectively improving and improving the detonation performance and storage stability of explosives.
Applications in solid buoyancy materials
Hollow glass beads have the characteristics of high strength, low density, etc., which can improve the buoyancy by reducing the density of the composite foam material and improve the strength of the composite material by dispersing the stress and bearing the load.
Applications in aviation and aerospace materials
The microsphere adhesive with non-combustible, chemically inert and electrically insulating hollow glass beads modified with epoxy-phenolic resin to make honeycomb structure can be used to replace the aluminum alloy riveting structure of the aircraft cabin floor or the insulation anti-ablation sealing protective cover of the spacecraft spacecraft.
Application in coatings
Hollow glass beads due to the unique hollow structure and has light weight, small density, good thermal insulation and other properties, mixed into the ordinary paint after drying tightly arranged to form a layer of microbead hollow layer, the hollow layer can reflect part of the light back to the atmosphere and block the external heat transfer to the interior of the paint, so the prepared paint has thermal insulation performance.
Applications in modified plastics
Compared to conventional plastics where mineral powder is added, hollow glass beads are used in resins to impart a range of excellent properties to plastics.
Applications in oil well cement
The drilling fluid prepared after the addition of hollow glass beads performed well, the beads were well dispersed in the system, and their density could be adjusted between 0.8 and 1.0g/cm3 and had good rheology.
Applications in catalyst carrier materials
The catalyst is loaded on the surface of the hollow beads, which not only reduces the amount of catalyst used, but also recovers it through filtration and other means.
Applications in functional materials
It can be used to prepare materials with excellent properties such as electricity, magnetism, acoustics and biochemistry. For example, Wang Yu et al. activated the 3~10μm hollow microbeads in formaldehyde-silver ammonia solution for chemical silver plating, and the dense continuous silver cladding thickness of 50nm absorbing material can absorb energy in different frequency bands.
With the advancement of product technology and industrial application technology, the application field of high-performance hollow glass beads will further increase. For example, in the field of 5G infrastructure construction, the characteristics of high-performance hollow glass beads with low dielectric constant and light weight are suitable for their functional requirements, and can be applied to 5G base station components such as FRP radomes, insulating laminates, and copper clad laminates. For the field of new energy vehicles, high-performance hollow glass beads can improve the physical and mechanical properties of body plastics and reduce the weight of products, which is in line with the requirements of lightweight new energy vehicles.
High-performance hollow glass beads
Source: China Steel Group Ma'anshan Mining Institute New Material Technology Co., Ltd
In the past few years, the glass bead industry has developed rapidly. In 2019, the global sales scale of plastics and rubber was $1.081 billion, the sales scale of paints and coatings was $831 million, the sales scale of building materials was $839 million, and the sales scale of other fields was $427 million.
In 2019, the global hollow microbead industry sales scale
Source: Collation of publicly available information
In 2019, the main sales areas of hollow microbeads were Europe, North America and Asia Pacific, with sales scales of US$1.56 billion, US$1.066 billion and US$368 million, accounting for 49.1%, 33.55% and 11.58% of the market size, respectively.
Global hollow microbead sales scale by region in 2019 (unit: %)
With the continuous progress of technology and technology, the application depth of hollow glass beads, especially high-performance hollow glass beads, in various industries has gradually deepened, and the market demand has continued to grow. The global and Chinese hollow microbead market size is expected to be $2.756 billion and $145 million in 2020, and the global and Chinese market size is expected to grow to $4,131 million and $251 million by 2026.
Analysis of the development trend of the global hollow microbead market size from 2019 to 2026
Statistics: CICC Qixin International Consulting
International giants such as 3M and Potters can offer high-end products for the aerospace and automotive industries. The United States is a major supplier and major consumer market for glass beads. In particular, the United States 3M company, as a leading enterprise, the market share of up to 17.3%. However, in the next few years, China's glass bead industry is expected to develop more rapidly and will continue to maintain a growth trend.
Domestic hollow glass beads key production enterprises
Zhengzhou Shenglite Hollow Micro beads New Material Co., Ltd
China Steel Group Ma'anshan Mine Research Institute Co., Ltd
Anhui Kaisheng Basic Materials Technology Co., Ltd
Shanxi Hainuo Technology Co., Ltd
Zhongke Huaxing New Materials Co., Ltd
Resources:
Cai Yaowu et al. Preparation method and application research progress of hollow glass beads
GUI Shupeng. Preparation and performance study of hollow glass beads
DUAN Ting. Preparation and performance study of hollow glass beads
Peng Shou et al. Preparation method and application research progress of hollow glass beads
Kaishengren. How much do you know about the material| high-performance hollow glass beads, small beads have big dreams!
CICC Qixin International Consulting.Global and China High Performance Hollow Glass Bead Industry Segment Market Size Analysis and Forecast in 2021
Analysis of the current situation of the global hollow microbead industry in 2020, the application field of high-performance products has further grown
China National Building Materials, Ma'anshan Economic Development Zone, Gaoping Big Data Center, 3M Press Release, etc