Due to the variety of types of holes on the parts, the processing methods of the holes are more than those of the outer circular surface, such as drilling, cutting, turning, boring, broaching, grinding, etc.
Compared with outer circular surface machining, although hole machining has many common points in cutting mechanism, there are large differences in specific processing conditions. The size of the hole processing tool, limited by the processed hole, is generally slender and has poor rigidity; when the hole is processed, the tool is surrounded by the workpiece material, the heat dissipation conditions are poor, the chips are not easy to exclude, and the cutting fluid is difficult to enter the cutting area; and the processing situation is not easy to observe directly. Therefore, if the same precision and surface roughness are processed, holemaking is more difficult and costly than the outer circular surface.
The choice of holemaking methods and the selection of machine tools is much more complex than the outer circular surface. When formulating the processing plan of the hole, in addition to considering the technical requirements of the hole processing, the size of the hole diameter and the depth of the hole, the material, shape, size, weight and batch of the workpiece, and the specific production conditions of the workshop (such as existing processing equipment, etc.) should also be considered.
If the hole is machined on the solid material (mostly small and medium-sized holes), the hole must be drilled first. If the holes that have been cast or forged (mostly medium and large holes) are machined, reaming or boring can be used directly.
As for the finishing of holes, reaming and drawing holes are suitable for processing undefined holes of medium and small diameter; holes of medium diameter or above can be fine boring or fine grinding; hardened holes can only be finished with grinding.
In the finishing method of holes, honing is mostly used for holes with slightly larger diameters, while grinding is suitable for both large holes and small holes.
Table 1-3-3 shows the hole machining scheme and the scope of application, which can be used as the basis and reference for formulating the machining scheme.
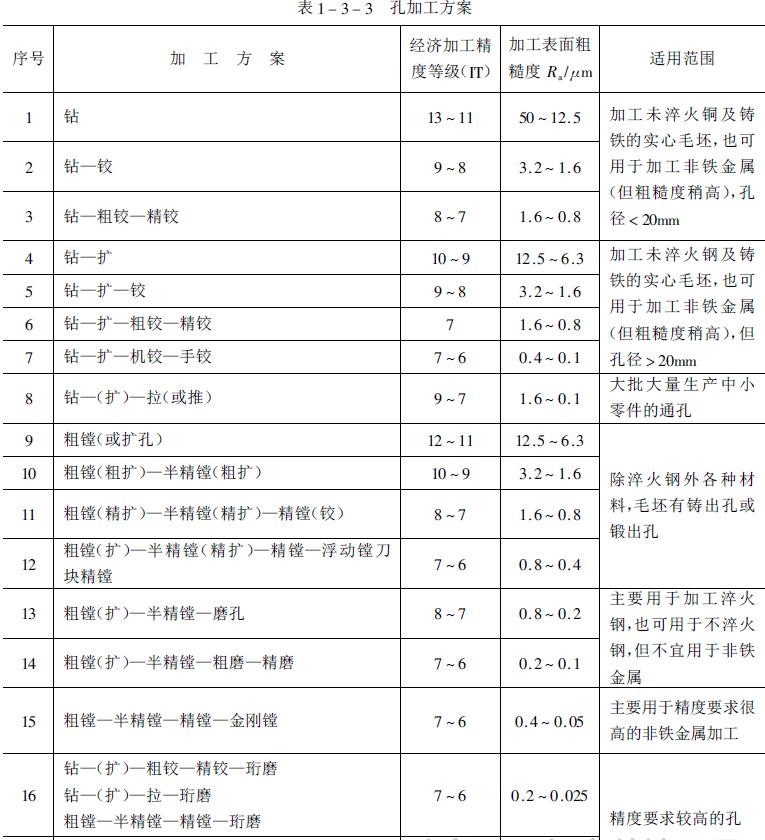
Table 1-3-3 refers to the economic accuracy and surface roughness achieved by various processing methods under normal conditions. When the processing conditions change, the resulting accuracy and surface roughness also change.
Typical scenarios for machining holes on solid materials are as follows:
(1) Holes with accuracy below IT10 can be achieved by the general drilling method (hole diameter <20mm).
(2) Holes with an accuracy of IT9 If the hole diameter is less than 20mm, drilling dies can be used to drill holes, or reaming holes after drilling; holes with a hole diameter greater than 30mm are generally boring after drilling.
(3) Holes with an accuracy of IT8 When the hole diameter is less than 20, mm, the reaming hole after drilling should be used; if the hole diameter is greater than 20mm, different processing schemes can be selected according to specific conditions, such as drilling - expanding - hinging, drilling - rough boring - semi-fine boring or drilling - (expanding) - pulling (or pushing) and so on.
(4) Holes with an accuracy of IT7 When the hole diameter is less than 20mm, the scheme of reaming twice after drilling is generally adopted; when the hole diameter is greater than 20mm, different processing schemes can be selected, such as drilling - expanding - rough hinge - fine hinge, drilling - expanding - machine hinge - hand hinge or drilling - rough boring (expansion) - semi-fine boring - rough grinding - fine grinding, etc.
The processing accuracy of the IT6 hole is roughly the same as the order of processing it7 precision hole, but its final work, the sequence should be based on the specific situation, respectively, using fine boring, hand hinge, fine drawing, fine grinding, grinding or honing and other methods for fine processing.
The holes that have been cast (or forged) on the cast (or forged) parts can be directly reamed or boring, and the holes with a diameter of more than 100mm are more convenient to use boring holes. As for semi-finishing, finishing and finishing, it can be carried out with reference to the above scheme.