About drilling fluids
Drilling fluid is a fluid used for drilling, and its functions in drilling are: 1. Cleaning the bottom of the well, suspending and carrying debris, and keeping the wellbore clean. 2. Balance the formation pressure, stabilize the well wall, prevent well collapse, blowout and well leakage. 3, transmit water power to help the drill bit to break the rock. 4. Transmit power for downhole power drilling tools, 5, cool drill bits, drilling tools. 6. Use drilling fluid for geological and gas logging. The conventional performance of drilling fluids has a great impact on drilling work.
First, the density of drilling fluid
1. Drilling fluid density concept:
The mass of a unit volume of drilling fluid is called the density of the drilling fluid, which is expressed in grams per cubic centimeter (g/cm3) commonly used symbols. The density of drilling fluid is generally determined on site using a drilling fluid density meter.
2. Calculation formula of drilling fluid density
P=(P地×102)÷H+Pe
P---- drilling fluid density g/cm3
where:
P ground ---- formation pressure MPa
H----- Ibukam
Pe----- additional density, oil layer additional 0.05-0.1 gas layer additional 0.07-0.15
Since the drilling may produce suction or liquid level drop, in addition, gas into the well, will also cause the pressure of the liquid column to decrease, so the drilling fluid density should have added value.
3. The relationship between drilling fluid density and drilling work:
In the drilling operation, the role of drilling fluid density is to generate pressure on the bottom and well wall through the drilling fluid column to balance the oil, gas pressure and rock side pressure in the formation, prevent blowout, protect the well wall, and prevent high-pressure oil and gas water from invading the drilling fluid, so as not to destroy the performance of the drilling fluid and cause downhole complications, in actual work, should be based on the specific situation, choose the appropriate drilling fluid density, if the drilling fluid density is too small, it is impossible to balance the formation fluid pressure, and stabilize the well wall, which may cause accidents such as blowout, well collapse, card drilling, etc. If the density of drilling fluid is too large, the formation will leak and easily damage the oil and gas layer. Drilling fluid has a great influence on drilling speed, the density of large liquid column pressure is also large, drilling speed becomes slower, due to the positive pressure difference between the drilling fluid column pressure and formation pressure, the removal of rock chips is hindered. Cause repeated crushing, reduce the efficiency of the drill bit to crush the rock, so that the drilling speed decreases, usually under the premise of ensuring normal downhole conditions, in order to increase the drilling speed, low-density drilling fluid should be used as much as possible.
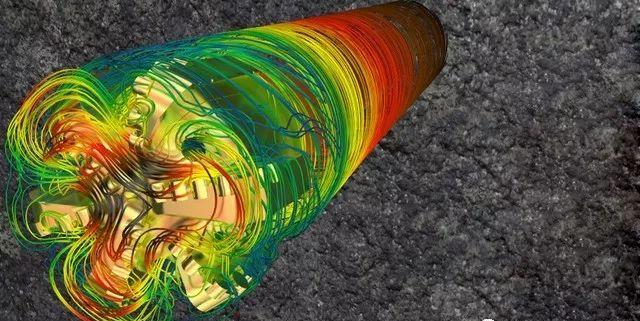
Second, the viscosity of drilling fluid
1, the viscosity concept of drilling fluid: drilling fluid viscosity refers to the flow of drilling fluid, between solid particles, between solid particles and liquid molecules, and between liquid molecules in the total reflection of friction, drilling fluid viscosity can be measured by funnel viscometer and rotary viscometer, due to the different measurement methods, there are different viscosity values, the site often uses funnel viscometer to measure the viscosity of drilling fluid, the unit is seconds.
2, the relationship between drilling fluid and drilling work, the size of the viscosity of the drilling fluid, the drilling fluid carries the ability to carry chips has a great impact, in general, the drilling fluid viscosity is large, carrying chips ability is strong, but in the process of drilling, the viscosity of the drilling fluid should be appropriate, otherwise it will cause adverse consequences. If the drilling fluid viscosity is too low, it is not conducive to carrying rock chips, the sand in the well is fast, the well wall is washed out, and it is easy to cause the well wall to peel, collapse, well leakage, etc., and the drilling fluid viscosity is too high, which may cause the following hazards: (1) Large flow resistance, high pump pressure, poor bottom cleaning effect, seriously affecting the drilling speed. (2) The drill bit is easy to mud pack, and the drilling is easy to produce suction effect or pressure agitation. So that it causes complex situations such as well leakage, blowout, and well collapse. (3) Sand grit difficulties, poor purification, wear drilling tools and accessories. (4) It is difficult to degass out, and the density of drilling fluid decreases, which is easy to cause complications of drilling. (5) Rock chips form fake mud cakes in the well wall, which is easy to cause obstruction. (6) Cement slurry is easy to groove during cementing, which affects the quality of cementing.
Therefore, the level of viscosity of drilling fluid should be determined according to the specific situation, usually under the premise of ensuring the carrying of rock chips, the viscosity should be low, the pump pressure is high when the well is deep, the pump displacement is limited, the wellbore situation is generally more complex than the shallow well, in order to effectively carry the cuttings and suspended rock chips, the viscosity is easy to be larger, when the wellbore collapses, more sand or mild leakage occurs, in order to eliminate the complex situation of the downhole, the viscosity is also appropriately increased. From the perspective of increasing the drilling speed, new requirements are put forward for the viscosity of the drilling fluid, that is, the viscosity of the drilling fluid should decrease with the rise of the flow rate gradient, which is the characteristic of shear and viscosity reduction. When drilling fluid is ejected from the drill eye, it has a lower viscosity, which is conducive to the drill bit crushing the rock chips. Cleaning the bottom of the well, and when returning to the annular space, it has a high viscosity, which is conducive to carrying rock chips, which is beneficial to increasing the drilling speed, except for clean water, most of the drilling fluids have the characteristics of shear and viscosity reduction.
Third, the shear force of drilling fluid
1, drilling fluid shear concept: because the shape of the clay particles in the drilling crossing is very irregular, the surface properties are also extremely uneven, the particles are easy to partially bond, forming a flocculation mesh structure, when the particle concentration is large enough, it can form a continuous space mesh structure with a relatively large volume, if the drilling fluid flows, it is necessary to destroy the continuous mesh structure to a certain extent, in order to make the particles produce relative movement, the shear force is the reflection of this mesh frame structure, and the greater the structural strength, the greater the shear force, and vice versa. The parameters that reflect the structural force of the drilling fluid are static tangential, thixotropic, dynamic shear force, etc.
The strength of the gel structure formed by the drilling fluid under stationary conditions, called the static shear force, the physical significance of which is the force required to destroy the grid structure on the internal unit area of the drilling fluid when the drilling fluid is stationary, usually measured by a pontoon shearometer, the unit is mg/cm3. The thixotropy of the drilling fluid refers to the thinning after stirring, and the thickening after standing (reduced shear force). The characteristics of (increased shear force), or the characteristics of the shear force of the drilling fluid increase with the long standing time after stirring, such as the low viscosity of the drilling fluid continuous circulation when drilling, and the large viscosity of the static circulation of the drilling fluid when drilling down, which is the truth. Because the drilling fluid has thixotropy, the rest time is different, the shear force is different, usually the shear value of the two stationary time is measured, the shear force measured for one minute at rest (or 10 seconds) is the initial cut, the shear force measured after 10 minutes of rest is the final cut, the difference between the initial shear force and the final shear force indicates the size of the thixotropy, and the greater the difference, the greater the thixotropy. The dynamic shear force, also known as the yield value, is measured by a rotational viscometer in the unit of dyne centimeter 2
2, the relationship between drilling fluid shear and drilling work: the size of the drilling fluid shear represents the drilling process of the suspended solid particles of the drilling fluid requires the drilling fluid to have appropriate shear force and good thixotropy, when the drilling fluid stops circulating, the shear force can increase rapidly, to a certain appropriate value, which is conducive to the suspension of drilling chips and not to be left standing after the pump pressure is too high, if the shear force is too low, the suspension carries the rock chip effect is not good, once the pump is stopped, it is easy to cause complex situations, if the shear force is too high, It may also cause the following hazards: (1) The flow resistance is large, and it is difficult to open the pump after drilling down and it is easy to leak the formation. (2) Sand grit is difficult, affecting purification, and the density rises rapidly. (3) When it is difficult to remove gas and the gas intrusion is serious, it will reduce the density of drilling fluid and lead to blowout. (4) The sand content increases, wears drilling tools and accessories, and the quality of the filter cake is poor, which is easy to cause adhesion card drilling. (5) The rotation resistance of the drill tool is large, the power consumption is large, and the drilling speed is reduced.
Fourth, the water loss of drilling fluid and filter cake
1. The concept of water loss and mud cake of drilling fluid:
Under the pressure difference between the pressure of the drilling fluid column pressure and the formation pressure, the water in the drilling fluid seeps into the formation from the pore crack of the well wall, this phenomenon is called water loss (or filtration loss), the amount of water lost is called the water loss of the drilling fluid, usually the water loss measured on the spot refers to the volume of water lost by the filtration area through the filtration area of 75mm in diameter within 30 minutes under the action of 0.686 MPa pressure, and the unit is milliliters. At the same time as the water is lost, the clay particles in the drilling fluid are blocked and deposited on the well wall to form a layer of solid particles of cement called filter cake. The unit of the filter cake is millimeters. The loss of water of the drilling fluid and the production of filter cakes occur at the same time, but also affect each other, the beginning is due to the loss of water and the formation of filter cakes, the loss of water is large to form the filter cake thick, the loss of water is small, the formation of the filter cake book, and the formation of the filter cake in turn to block further water loss, water loss mainly depends on the permeability of the filter cake itself, and the water loss is not the only factor that determines the thickness of the filter cake, the water loss of the drilling fluid and the filter cake can be measured by the air pressure water loss meter.
2. The size of the water loss of the drilling fluid, the relationship between the quality of the filter cake and the drilling work:
In the process of drilling, there is water loss to form a filter cake, the formation of a filter cake can consolidate the well wall and prevent further water loss, generally speaking, drilling requires drilling fluid to have low water loss and book and tough and dense mud cake. Too thick and loose filter cakes that lose too much water are not good for drilling. Hazards of excessive water loss:
(1) The formation is soaked, which can easily cause the diameter of the borehole to shrink or cause the mud shale to peel and collapse. (2) Moisture penetrates into the production layer, expanding the bentonite in the oil layer, reducing the permeability of the oil layer gas layer, and reducing the production capacity.
The hazards of too thick filter cakes are:
The filter cake is thick and loose, and the friction system is large, which is easy to cause the mud cake to adhere to the card drill.
Easy mud drilling bag head or blocking water holes, so that the downward drilling fluctuation pressure is large.
When drilling down, the friction resistance increases, and even hits a card.
Hinders casing smooth entry and affects cementing quality.
Electrical measurement encounters resistance meets card, and the data taken by electrical measurement and well wall is inaccurate.
But the water loss is not as small as possible, the requirements for too small water loss is the cost of drilling fluid increases, the drilling speed decreases, the mud cake book is required, and the water loss control is not necessarily very small, in the drilling process, it should be based on the characteristics of the formation rock, the well depth, the well structure, the drilling fluid and other types to decide, such as limestone, dolomite, cemented sandstone, do not require water loss, easy to absorb water expansion, collapse of shale and other formations that are easy to collapse, the water loss should be strictly controlled, in addition, the well can be relaxed when shallow, and the eye time should be strict, The use of brine drilling fluid should be relaxed, the use of freshwater drilling fluid should be strict, in short, when the well wall allows, the requirements for water loss should be appropriately relaxed to maximize the drilling speed.
Fifth, the solid phase content of drilling fluid
1. The concept of solid phase content and sand content of drilling fluid
The sand content of the drilling fluid refers to all the solid substances in the drilling fluid, including clay drilling chips, chemical treatment agents, barite powder, etc., these solid substances account for the percentage of the drilling fluid volume called the drilling fluid solid content, usually expressed in percentages, the solid substances in the drilling fluid are not without difference, according to the different effects of the solid on the performance of the drilling fluid and the effect on the drilling fluid is different, the solid phase in the drilling fluid can be divided into two kinds (1) useful solid phase, refers to the solids necessary to maintain the drilling fluid, such as bentonite powder, chemical treatment agent, Aggravating agents, etc. (2) Harmful solid phase, in addition to the solid phase of the useful solid phase, such as drill chips, inferior bentonite, sand grains, etc. In the non-dispersed low solid phase drilling fluid, bentonite accounts for 2-4% of the drilling fluid volume, which can meet the requirements of the performance of the drilling fluid, therefore, the harmful solid phase in the general drilling fluid is a lot, in order to effectively control the performance of the drilling fluid, improve the downhole situation, improve the drilling speed, remove all the harmful solid phases, and control the useful solid phase.
2. The influence of solid phase content of drilling fluid on drilling speed
Practice has proved that when drilling clear water, the drilling speed is the highest, and once the water enters the bentonite particles drilling speed decreases, the solid phase content in the drilling fluid increases is an important reason for the decline in drilling speed, and the high solid phase content of the drilling fluid will also seriously affect the performance of the drilling fluid, and bring many hazards to the drilling, the drill bit is reduced, and the drilling equipment wear is serious. The density and viscosity of the drilling fluid increase, the filter cake is thickened, and it is prone to accidents such as well leakage and jam drilling, and damage to the oil and gas layer. And and and the drilling fluid flow resistance increases, pump pressure rises, is not conducive to jet drilling, so that the performance of the drilling fluid fluctuations process frequently, consume a lot of drilling fluid treatment agent, therefore, to effectively improve the drilling speed, safe drilling, must strictly control the solid phase content, the use of non-dispersed low solid phase drilling fluid.
Sixth, the PH value of the drilling fluid
1. The concept of PH of drilling fluid
The PH value of the drilling fluid is the acid-base value of the drilling fluid, which indicates the strength of the acidity and alkalinity of the drilling fluid, which is equal to the negative logarithmic value of the hydrogen ion concentration in the drilling fluid, also known as PH, when the PH value is less than 7, the drilling fluid is acidic, when the PH value is equal to 7, the drilling fluid is neutral, when the PH value is greater than 7, the drilling fluid is alkaline, and the PH value of the drilling fluid is usually determined by colorimetric method
2. The influence of PH on drilling fluid
The PH value has a great influence on the performance of the drilling fluid, and the clay particles in the drilling fluid are more stable in the alkaline medium due to the large negative charge and large cation exchange capacity. Secondly, there are many organic treatment agents, which must be under the alkaline action to play a role, such as denim, humic acid, etc., in addition, the PH value is low, and the organic treatment agent is easy to ferment and deteriorate at high temperatures, so the PH value of the general drilling fluid is maintained at more than 8. However, if the ADSOR of high hydroxygen ions on the surface of the clay will promote the hydration and expansion of bentonite, which is not conducive to collapse prevention. Experience has shown that all types of drilling fluids have their own suitable pH range. For example, the PH of high alkaline drilling fluid is 12-14, the PH value of non-dispersible low solid phase drilling fluid is 8-9, the PH value of weak acid drilling fluid and saturated brine drilling fluid is 6-7, the PH value is controlled within the appropriate range, the drilling fluid is low in viscosity, the water loss is small, the performance is relatively stable, and the PH value is the basis for determining the alkali ratio of the treatment agent.
Seven, drilling fluid treatment agent
In order to meet the requirements of the drilling process, it is not enough to adjust and control the performance of the drilling fluid by using clean water and mechanical equipment alone, and a variety of chemical treatment agents must be used in the drilling fluid. There are the following types of inorganic treatment agents, organic treatment agents and surfactants commonly used in the production of drilling fluids:
(1) Inorganic treatment agent
1, sodium hydroxide (NaOH),
Sodium hydroxide commonly known as caustic soda, caustic soda, density at room temperature is 2.0-2.2g / cm3, easy to tolerate water, dissolve when released a lot of heat, solubility with increasing temperature and increase, water dissolution is strong alkaline PH value of 14. Use should pay attention to safety, to prevent corrosion of skin and clothing, NaOH is easy to damp, with the CO2 action of the air to generate NaOH, storage should pay attention to moisture-proof, NaOH is a strong alkali, mainly used to mediate the PH value of drilling fluid, with some organic matter, such as tannin into tannin lye, with polypropylene eye hydrolysis to get hydrolysis polypropylene eye, etc., in addition, NaOH also removes harmful Ca2 + Mg2 +.
2. Sodium chloride (NaCI)
Commonly known as table salt, for white crystals, density of 2.17g / cm3 is easily soluble in water, aqueous solution is neutral, solubility increases slightly with the increase of temperature, pure NaCI does not deliquescence, Containing MaCI2CaCI2 and other impurities NaCI easy to absorb moisture NaCI is mainly used to prepare brine drilling fluid and saturated brine drilling fluid to prevent the dissolution of rock salt well section, maintain the well diameter rules, NaCI can also be used to improve the mineralization of drilling fluid, inhibit the hydration expansion of shale formations, and prevent collapse.
3、 Potassium hydroxide (KOH)
Commonly known as caustic potassium, is a translucent crystal, the density of 2.04g/cm3 at room temperature is easily soluble in water, strong exothermic when dissolved, the aqueous solution is strongly alkaline, the PH value is 14, there is a strong corrosive effect, KOH is very easy to absorb moisture in the air and CO2 to generate K2CO3
KOH can be used to adjust the PH value of the drilling fluid and provide K+. K+, has a good anti-collapse effect, so potassium salt drilling fluid is widely used, in addition to KOH can be used with some organic treatment agents for hydrolysis, the formation of potassium salts, such as potassium polypropionate, polypropylene potassium and so on.
4. Sodium carbonate (Na2CO3)
Commonly known as soda ash, soda, no foam, Na2CO3 is a white powder, the density is 2.5g/cm3. It is easily soluble in water, the aqueous solution is alkaline, and the PH value is 11.5. Na2CO3 easily absorbs moisture in the air to form a hard block, and the CO2 in the absorbed air becomes Na2CO3. Na2CO3 in the drilling fluid through ion exchange and precipitation, so that the calcium bentonite into sodium bentonite, the current preparation of drilling fluid mostly use calcium bentonite, so in the preparation of drilling fluid need to add a certain amount of Na2CO3, the purpose is to improve the bentonite hydration and dispersion performance, improve the bentonite slurry rate, in addition, Na2CO3 can be used to remove gypsum or cement immersed in the drilling fluid Ca2+, improve the performance of the drilling fluid.
5. Calcium sulfate (CaSO4 2H2O)
Commonly known as gypsum, divided into raw gypsum (CaSO4 2H2O) and slakton (CaSO41/2H2O) as a drilling fluid treatment agent commonly used slit gypsum, hydrated gypsum can be hardened into raw gypsum when exposed to water, hydrated gypsum is a white powder, density of 2.5g / cm3 can be soluble in water, 40 degrees Celsius before, solubility increases with temperature increase, 40. After C, the solubility decreases with the increase of temperature, gypsum is mainly used to prepare gypsum drilling fluid, inhibit the dissolution of gypsum in the gypsum mudstone layer in the formation, make the well diameter regular, reduce pollution, in the gypsum drilling fluid, there is also low resistance to gypsum immersion, salt leaching and collapse prevention, in addition to calcium treatment of raw materials.
6. Sodium silicate (Na2SiO3)
Commonly known as water glass, bubble soda ash, is a viscous translucent liquid, depending on the impurities contained can be colorless, brown or turquoise, etc., density of 1.5-1.6g/cm3, PH value of 11.5-12. Soluble in water and alkaline solutions, miscible with brine. Therefore, the viscosity of Na2SiO3 can be adjusted by saturated brine, Na2SiO3 is added to the drilling fluid, which can be partially hydrolyzed to generate colloidal precipitation, but part of the bentonite particles (or silty sand, etc.) are deposited, thereby maintaining a low solid phase content and density, in addition, Na2SiO3 drilling fluid has a certain production use for shale hydration and expansion, so it has good anti-collapse performance, if the PH of Na2SiO3 is reduced to below 9, the entire solution will form a non-flowing gel, using this feature, Na2SiO3 and lime are commonly used to formulate leak plugging agents.
7、 Barium sulfate (BaSO4)
Barium sulfate, commonly known as barite, pure products are white powder, impurity-containing products are green or gray-green, and the density is 4.30-4.60g/cm3. BaSO4 is not in water, soluble in dilute hydrochloric acid, BaSO4 in the drilling fluid role is to increase the density of drilling fluid, as a heavy agent of drilling fluid, the density of BaSO4 is required to be no less than 2.70g/cm3 powder particle size required 99% through the 200 mesh sieve.
(2) Organic treatment agents
Organic treatment agents are generally organic polymer compounds, from a certain source and development point of view, can be divided into natural products, modified products, synthetic products three categories, according to its role can be divided into diluents, water loss agents, flocculants three categories
1. Diluents:
(1) Iron chromium lignosulfonate (code name FCLS)
Referred to as iron chromium salt, the finished product is brown-black powder, soluble in water, the aqueous solution is weakly acidic, has a strong anti-pollution ability, strong thermal stability, temperature resistance up to 170--180 degrees Celsius, iron chromium salt is a salt resistance to calcium and temperature resistance to drilling diluent, can be used to talk about water, seawater and saturated brine drilling fluid, a variety of calcium treatment drilling fluid and deep well drilling fluid, iron chromium salt in dilution at the same time, there is a certain water loss and anti-collapse effect. Iron chromium salt is generally used as a lye, if the PH value of the drilling fluid is high, the powder can be directly added to the drilling fluid, the PH value is generally between 9-12, the dilution effect is the best, the PH value is too high The amount of use is too large to produce foam, the PH value is too low, the dilution effect is poor, in addition, the use of iron chromium salt treatment of the drilling fluid filter cake friction system is large, and the use of anti-collapse ( collapse) card agent is used.
(2) Sulfamethyl tannins (code name SMT)
Commonly known as sulfonated tannin, is also a modified new diluent, mainly used as a diluent for deep well drilling fluid, temperature resistance up to 180--200 degrees Celsius, sulfonated tannin in high temperature conditions can effectively control the viscosity shear of freshwater drilling fluid, but salt resistance, calcium resistance is poor, sulfonated tannin can be directly added to the drilling fluid when used, the dilution effect is better when the PH value is greater than 9, suitable for freshwater drilling fluid and general drilling fluid.
(3) Sulfamethyl quercetin (codename SMK)
Commonly known as sulfonated quercetin, is also a modified new diluent, the finished product is brown exhaustion powder or fine particles, easily soluble in water, aqueous solution is alkaline, sulfonated quercetin is a diluent of deep well drilling fluid, generally temperature resistance up to 180. C, there is a good dilution effect in freshwater drilling fluid, but the salt resistance and calcium resistance are poor, and sulfonated quercetin can be directly added to the drilling fluid when used, and the PH value between 8-11 is appropriate. (4) Ethylenediamine tetramethyl fork sodium phosphate (code EOTMPS) belongs to the organic phosphate, the solid is white powder, easily soluble in water, the liquid is brown viscous, slightly alkaline, it is a new non-dispersible drilling fluid diluent, can effectively reduce the viscosity and shear force of the drilling fluid, and it can form a stable bond with Ca2 + Mg2+, so it can eliminate the influence of Ca2 + Mg2+ on the drilling fluid, and has strong salt resistance and temperature resistance.
2. Water loss reducing agent
(1) Sodium carboxymethyl cellulose, (codenamed Na-CMC or CMC)
The finished product is a white or light yellow powder, non-toxic and easily soluble in water, with a certain degree of anti-calcium and salt resistance, but in the face of high-priced AI3 + Fe3+ will occur flocculation, temperature resistance is poor, generally up to 140. C。 Industry is often divided into three types of high viscosity, medium viscosity and low viscosity according to the viscosity of its aqueous solution, and pay attention to the difference when using it. Carboxymethyl cellulose is the most commonly used water loss agent, which reduces the water loss of drilling fluid while inhibiting the expansion of mud shale hydration and consolidating the well wall, and can be used to improve the ability of drilling fluid to suspend and carry rock chips, high viscosity carboxymethyl cellulose can also be used as a thickener without solid phase drilling fluid. When used, it can be directly added to the drilling fluid, and can also be used with different concentrations of glue.
(2) Sulfamethyl lignite (code name SMC)
Commonly known as sulfonated lignite, the finished product is black brown powder or granules easily soluble in water, is a new type of modified treatment agent, it reduces the water loss of drilling fluid at the same time, has a certain dilution effect, temperature resistance up to 200--220. C。 When used, it can be directly added to the drilling fluid, because the sulfameth lignite has poor salt resistance and calcium resistance, and is suitable for reducing water loss in freshwater drilling fluid.
(3) Sulfamethylphenolic resin (code name SMP)
Commonly known as sulfonated phenolic resin, is a new type of anti-high temperature water loss agent, according to its salt resistance can be divided into SMP-2 two models, both have good thermal stability, temperature resistance of 180--200. C。 The sulfonated phenolic resin of the liquid is a brown viscous liquid, the solid is a tan powder, both of which are easily soluble in water, which can be directly added to the drilling fluid when used, if used together with the sulfonated humic acid treatment agent and iron chromium salt, the effect of reducing high temperature and high pressure water loss is particularly obvious.
(4) Sodium polyacrylate (code 8A44, 80A46)
Calcium polyacrylate (code CPA). 8A44, 80A46) is different molecular weight, sodium polyacrylate is a white powder, or fine sand particles, easily soluble in water, aqueous solution is neutral, easy to deliquescence, commonly used as a stabilizer of low solid phase drilling fluid, due to poor salt resistance to calcium, commonly used as a water loss reducing agent for freshwater drilling fluid. The finished calcium polyacrylate is a white powder, easily soluble in water, the aqueous solution is alkaline, has a strong salt resistance and calcium resistance, and can be used as a water loss reducing agent and tackifier for brine and seawater drilling fluid.
(5) Chromium humic acid (code C1—NaC)
The finished product is tan powder, easily soluble in water, water soluble is alkaline, is a high temperature resistant drilling fluid water loss agent and diluent, in the drilling fluid can reduce the shear force of the drilling fluid, but also can reduce the water loss of the drilling fluid. Temperature resistance up to 200 degrees Celsius, external, chromium humic acid has a strong salt resistance and calcium resistance, suitable for brine drilling fluid with a salt content of less than 50,000 PPm and calcium treatment drilling fluid with a calcium content of less than 600 PPm. When used, it can be directly added to the drilling fluid, and the PH value is 10-11.
(6) Hydrolyzed polypropylene sodium salt (code HPAN)
The finished product has two kinds of solid and liquid, both of which are easily soluble in water, its thermal stability is good, and the temperature resistance is up to 240--250. C, has strong salt resistance, but poor calcium resistance. Hydrolyzed polypropylene clear sodium salt is a deep well and ultra-deep well drilling fluid water loss agent, in the reduction of water loss at the same time can improve viscosity, increase suspension capacity, often used in freshwater drilling fluid, has a good water loss effect, water seawater drilling fluid needs to be equipped with sulfonated phenolic resin to be effective, when used can be directly added to the drilling fluid.
(7) Hydrolyzed polypropylene potassium salt (codename KPAN)
Hydrolyzed polypropylene clear calcium salt (code pan), high temperature hydrolysis polypropylene clear (code name NPAN), these three products are drilling fluid water loss agent, hydrolyzed polypropylene clear potassium salt has the characteristics of water loss, friction resistance, temperature resistance, anti-pollution and anti-collapse, hydrolyzed polypropylene calcium salt and polypropylamide, hydrolyzed polyacrylate calcium can be used in combination to achieve low viscosity, low density, low shear force of the drilling liquid, high temperature hydrolysis polypropylene clear due to high temperature hydrolysis, the molecule contains NH4, Therefore, it can effectively control high-pressure water loss in drilling fluids and has a good anti-collapse effect.
(8) Polymeric humic acid (code sh23 SH24)
It is a water loss reducing agent for drilling fluids of deep wells and ultra-deep wells, and its thermal stability performance is good. Temperature resistance up to 200. C, SH23 and SMP-1 compound use, salt resistance up to 60,000-130,000 PPm, SH23 and SMP-2 compound use, salt resistance up to 13-300,000 PPm, SH24 and SMP-1 compound use salt resistance of 60,000 PPm.
3. Flocculant
(1) Polyacrylamide (codename PAM)
Drilling fluid used in colloidal and solid two products, polypropylamide is often used as a non-dispersible low solid phase drilling fluid full flocculant, in the drilling fluid both flocculation drilling chips, inferior bentonite, but also can improve the flow of drilling fluid, reduce friction resistance, increase drilling speed, when used solid can be directly added to the drilling fluid, colloidal need to be formulated into a solution to use.
(2) Hydrolyzed polyacrylamide (code name PHP)
Hydrolyzed polyacrylamide is also a flocculant of drilling fluid, the flocculation effect in the drilling fluid is affected by molecular weight and hydrolysis, the general molecular weight is 300-5 million, the hydrolysis degree of 30% of the polypropylamide flocculation effect is the best, the appropriate hydrolysis degree and molecular weight of polyacrylamide is a selective flocculant, both flocculation drilling fluid in the drilling chip, inferior bentonite, strong hydration of bentonite, no flocculation effect, high hydrolysis of polypropylamide can be used to improve viscosity, leak prevention, plugging and reduce the water loss of drilling fluid.
(3) Polyacrylamide and sodium acrylate copolymer (code 80A51)
The finished product is white powder or fine particles. It is a new type of selective flocculant, which has the characteristics of flocculent rock chips, temperature resistance and pollution resistance, and can also be used as a flow type improver for freshwater drilling fluids, as well as certain anti-collapse and tack increase effects.
(4) Acrylate and sodium acrylate copolymer (code PAC141)
The finished product is white powder, easily soluble in water, it is a new type of drilling fluid flocculant, with a certain degree of salt resistance and calcium resistance and improve the structural strength of the drilling fluid, salt resistance to saturation, its thermal stability is strong, temperature resistance up to 190. C, can be used for freshwater, seawater and brine drilling fluids, for low solid phase drilling fluids, has strong shear stability.
Third, surfactants
There are many types of surfactant doses, the role in drilling fluid is also multifaceted, in addition to being used as an emulsifier defoamer, the selection of appropriate surfactants, the treatment of drilling fluids, to improve the stability of drilling fluids, protect the oil layer to reduce the friction coefficient of the filter cake, anti-collapse, anti-corrosion to improve drilling speed, prevention and lifting of complex accidents in drilling and other aspects have outstanding effects. Surfactants commonly used in drilling fluids are:
1. Emulsifier,
(1) Sodium alkylsulfonate (code name AS)
It can be used as an emulsifier for oil mixing of drilling fluid and brine drilling fluid, and can be used for deep wells and ultra-deep wells to improve the thermal stability of drilling fluids, in addition, there is a better wetting and corrosion inhibition effect.
(2) Sodium alkylbenzenesulfonate (code abs) has similar properties to AS, but has stronger thermal stability and can be used as an emulsifier for oil-in-water drilling fluids.
(3) Alkyl alcohol amide (code number 6501) is an amber or light yellow viscous liquid, mainly used as an emulsifier for drilling fluids, 6501 is sensitive to salts and can increase the viscosity of water. (4) Polyoxyethyl octylphenol ether (code name OP) is often called op series, commonly used op-4op-7op-10op-15, etc., easily soluble in water, high temperature resistance, is a drilling fluid emulsifier. (5) Sorbitan monooleic acid grease (code name sp-80) is a viscous oily liquid, insoluble in water, strong lipophilicity, is a good water-in-oil emulsifier, with a variety of roles of chemical lubrication, defoaming and rust prevention, used in ultra-deep well drilling fluids to improve the thermal stability of drilling fluids.
2. Wetting anti-card anti-card release agent
(1) Polypropylene, polyoxypropane alkyl ether, common models are 2Y-150 2Y-200 2Y-300 is a pale yellow or yellow viscous liquid, which can reduce the surface tension of water, wetting and permeability are strong, and have a certain emulsification effect.
(2) Polyethylene glycol (code name PEG-400) is a yellow liquid, mainly used as a wetting agent for drilling fluids.
(3) CP233 anti-card agent, yellow-red colloid, soluble in water, with dispersed lubrication to reduce friction resistance and other effects, can improve the fluidity of drilling fluid, to prevent filter cake sticking card drill.
(4) Sulfonated toner oil, a viscous liquid, is mainly used to reduce the friction coefficient of the filter cake, is a good anti-jamming agent, and has a certain defoaming effect.
(5) SR301 card unlocking agent is a good card disassembly immersion solution, which is very effective for lifting the filter cake adhesion card drill, and also has a good effect on lifting the shrinkage diameter and small wellbore card drill.