"Our first phase of the 70,000 tons of brominated butyl rubber production line is expected to be put into operation in July, and the new device has greatly improved its process, design and stability compared with the existing 50,000 tons of plant, fully meeting the needs of downstream customers, and it is expected that the output of butyl rubber will reach 110,000 tons by the end of the year." Recently, China Rubber Magazine visited Shandong Bozhongju New Materials Co., Ltd., and Chen Fuqiang, general manager of the company's market technology team, introduced the annual output of 150,000 tons of brominated butyl rubber project to reporters. He said that after the new project reaches production, it will become the largest brominated butyl rubber production base in China, and they are full of expectations for the future market.
The largest brominated butyl rubber project in China
It is understood that the Construction of Jingbo Zhongju's annual output of 150,000 tons of brominated butyl rubber project began in September 2019, including two brominated butyl rubber production lines with an annual output of 70,000 tons and 80,000 tons, and it is expected that the first phase of the project will be completed and put into operation in July this year.
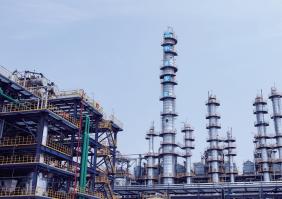
"Jingbo Zhongju has an annual output of 50,000 tons of butyl rubber production line, the device was put into production in 2015, the current annual output has reached 60,000 tons, the production capacity increased by 120%; the new phase of the annual output of 70,000 tons of brominated butyl rubber production line next year can reach 90,000 tons, when the company's brominated butyl rubber output can reach 150,000 tons." In the later stage, the second phase of the annual output of 80,000 tons of brominated butyl rubber production line will be carried out. Liu Tengfei, general manager of product marketing of the company's butyl rubber product marketing team, told reporters.
According to Zhang Min, engineer of the technical general manager team of the butyl rubber market, the annual output of 150,000 tons of brominated butyl rubber project is the first production line in China to adopt polymer direct dissolution (PDD) technology, positioning itself to produce high-performance brominated butyl rubber. Compared with the double glue liquid (DSS) technology commonly used in China, PDD technology reduces the water addition process after the polymerization reaction, and reduces wastewater discharge directly from the source, and its technology is internationally advanced.
The technical source of the project is the same as the existing 50,000 tons of butyl rubber project per year, which is the introduction of italian process packages. "Although all of them are imported from Italy' process packages, the process has undergone major changes, and we have integrated the experience of technical exploration and technological transformation of 50,000 tons of devices into the new project, and have innovated and optimized the original process package again, reducing energy consumption and material consumption, and the new project has reached the international advanced level in some aspects of technology." Zhang Min said that the reactor, equipment, process and design of the new production line can reach the international level, and its equipment and process parameters are the most advanced in the world, and the domestic brominated butyl rubber will be raised to a higher grade in quality.
The technical advantages of the new project products are obvious
According to Wang Xiaohai, general manager of the company's technology, the new production line products have four advantages:
First, the stability of the product has been greatly improved. First of all, the PDD process dissolves in one step, which realizes the stable and reliable product quality from the process. Secondly, the longer cycle of production and operation has greatly improved the polymerization reaction cycle and the condensate kettle operation cycle, reduced switching and improved stability; finally, reliable and strict self-produced isobutene supply, stable raw material supply to ensure product stability.
The second is the wide molecular weight distribution of the product. Improved processing performance, better dispersion of filler, improved mechanical properties, improved the performance of the rubber compound, more conducive to processing.
Third, the product is more pure. Reducing the polymerization flocculation and alkali process, the product ash content is less, the cleanliness is improved, and the salt content is reduced by more than 30%; the aging resistance of its products is better, which prolongs the product life cycle and life.
Fourth, the production process is more green and environmentally friendly. A new more efficient brominated brine treatment process has been added, and the VOCs treatment uses a regenerative incinerator (RTO) process; the process is designed to achieve environmental protection at the source and reduce emissions.
Wang Xiaohai said that the new device PDD production process does not have a post-polymerization and agglomeration process, the material will not be in contact with water, and there is no process such as chloromethane drying and triethylene glycol regeneration, which greatly reduces exhaust gas emissions. Based on the advanced nature of the process, the new production line reduces material consumption and energy consumption from the source, that is, reduces the generation of "three wastes", and also reduces the VOCs content in the waste gas and the COD content in the wastewater, reducing the difficulty and treatment volume. In the case of the whole society attaching great importance to environmental protection, the new device has a greater environmental protection advantage, which not only reflects the social responsibility of the enterprise, but also conforms to the national "double carbon" strategy.
Strengthen innovation and research and development to enrich product lines
Liu Tengfei introduced, "Among the 3 butyl rubber manufacturers in China, we started the latest, but we have made rapid progress in market development and product promotion, and have established communication relations with international tire companies. ”
Chen Fuqiang also said that the butyl rubber process technology of Jingbo Zhongju is relatively advanced, and the level and level of personnel are relatively high, which has overall advantages. In addition, in 2015 the company established an application technology department to continuously improve the product based on user feedback. "Customer needs are fed back to the technical department, we will give the customer the first feedback within 24 hours, and the relevant technicians will come to the site to solve the problem within 48 hours."
At present, the global demand for butyl rubber is 1.3 million tons, China is the world's largest market, the annual demand is about 400,000 tons, especially most of the brominated butyl rubber rely on imports. "At present, we only have ordinary butyl and brominated butyl rubber products, the next step is to increase the number of chlorobutyl rubber products, at the end of the year can achieve the production of ordinary star-type branched butyl rubber, brominated butyl rubber, chlorobutyl rubber, the new project specializes in the production of high-performance brominated butyl rubber, so that our product line is rich, can provide customers with more diversified choices." Liu Tengfei said.
"In addition to butyl rubber, we and Beijing University of Chemical Technology jointly successfully developed the world's first batch of bio-based coat-based ester rubber; for domestic card neck synthetic rubber products, during the '14th Five-Year Plan' period, we are ready to build another polystyrene-butadiene rubber project." Liu Tengfei said.
It is understood that at present, Jingbo Zhongju's products have been applied in Bridgestone, Goodyear, Youke Haoma, Zhongce, Linglong, Zhengxin, Sailun, Hengfeng and other tire enterprises, and have been well received by users, and the next step will be to step up the certification of new project products in customers and continuously open up domestic and foreign markets.
China Rubber Magazine
Editor's Tel: (010) 8491-5661/6637/6815
Advertising issue: (010) 8492-4066/0005, 84916907
Website phone: (010) 84915391
Email: [email protected]
Scan code to pay attention