A French sneaker manufacturer is grappling with the question of how to take production home; Salomon has set up a new shoe factory in France. Now, it must also establish a footwear supply chain in a country that does not have a footwear supply chain.
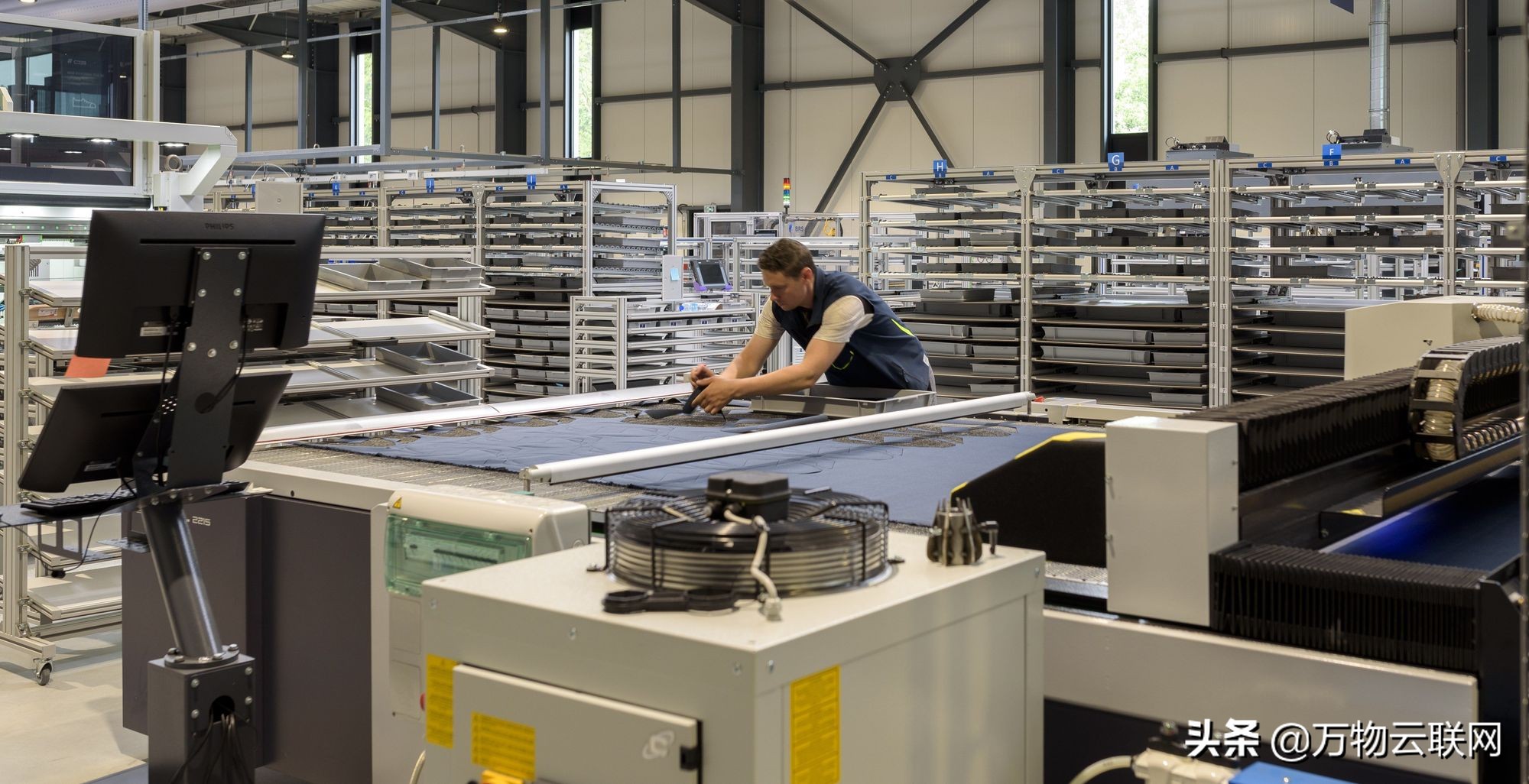
It is not easy for Western companies to bring production back to their home countries
ARDOIX, France – After 15 years of fully manufacturing footwear in Asia, French sportswear company Salomon SAS, eager to reduce emissions and bottlenecks, decided it was time to start producing its iconic sneakers in France. In a country where the footwear industry disappeared years ago, Salomon's challenge is how to build the necessary supply chains.
The first phase of Salomon's solution was the construction of an automated sneaker factory in this small town near the Alps. It also redesigned the shoe, drastically reducing the length of the supply chain by reducing the number of components used in each sneaker by nearly two-thirds. But it still makes sourcing the materials needed in a region where there are essentially no suppliers. So far, it has mainly sourced soles and other parts from China and Vietnam, which are the two main centers of modern shoemaking.
"For 30 years, all the innovations in sneakers, all the capacity in Asia," said Guillaume Meyzenq, vice president of footwear at the 75-year-old company, which also makes ski equipment and other sportswear. "We face a huge challenge to change the way this industry works."
For decades, Western companies have been looking for ways to leverage cheaper labor and highly developed supply chains to produce everything from clothing to toys in Asia, Eastern Europe or Latin America. But in recent years, the business logic of this approach has eroded as the global economy has been repeatedly impacted, prompting many companies to rethink this mode of production.
In 2018, then-President Donald Trump's trade war with China strained U.S. relations with China, rocking many companies that relied on smooth ties between the world's top two economies.
Then, starting in 2020, the COVID-19 pandemic brought a wave of factory closures, as well as port congestion and truck shortages, disrupting supply chains and pushing up freight costs.
Now, the conflict between Russia and Ukraine has once again disrupted the global supply system, further exposing the fragility of international trade.
A French factory in Salomon
These crises make "re-shoring" increasingly attractive. Re-shoring refers to the offshore operation of returning production to the country where the company is located. René Buck, chief executive of supply chain consultancy BCI Global, said: "Re-shoring used to be the subject of boring meetings; now it's the topic of the board. ”。“ What has changed is that these distractions have become the norm. ”
According to a BCI survey of 125 companies late last year, about two-thirds of U.S. and European manufacturers said they would bring some Of their Asian products to their home countries by 2025, and one-fifth said they would bring back most or all of them.
Some companies are already taking action. Toy maker Mattel Inc. said last month it would move some production from Asia to Mexico. Bedding maker Tempur Sealy International Inc. recently opened three new production facilities in the U.S., saying they would reduce the risk of future supply chain disruptions.
Advisers and executives say footwear production is particularly difficult to repatriate because Asian shoemakers use cheap, plentiful, low-skilled labor. This model cannot be rebuilt in the West, prompting companies to turn to automation.
Salomon's shoes
Salomon's Advanced Shoe Factory (in partnership with local fiber producer Chamatex SA), which opened last year, is initially producing two types of trail running and hiking boots, which will be available later this year after several delays. The local models are priced at €130 and €160, respectively, equivalent to $142 and $174, in line with Salomon's existing products. Meyzenq said the company's hope that the backstory of the shoe's sustainable production locally is a strong selling point.
Mr Meyzenq said French-made shoes would be as profitable as those made in Asia, thanks to savings from lower transport costs and the elimination of tariffs.
Salomon is a sought-after brand among serious trail runners, but it's a niche market relative to major sneaker producers like Adidas. With full tilt, the plant plans to produce 1 million cross-country running shoes per year; Solomon will account for half of that capacity, and two other French footwear brands, Babalat and Millet, are also partners in the plant and will take on the rest of the capacity. So far, the partners have invested 10 million euros, or about $11 million, in the project and plan to make more investments.
One shift of the factory; It takes 15 workers, and a typical shoe factory in Asia needs five times as many footwear workers to match its output. Some people operate sewing machines – this complex work is still best done by hand – while others need to monitor automated production lines.
A machine uses heat and pressure to glue the upper part of a sneaker together. Others spray glue on the soles of the shoes and then glue them to the rest of the shoe, or use lasers to cut parts of the sneakers from a colored plastic sheet. Another company stores hundreds of green molds, called shoe lasts, to give sneakers the shape they need.
Salomon, who makes shoes in several Asian countries, including China, began developing its plans in 2017 to reduce carbon emissions while strengthening and shortening its supply chain. The project continued even after the company's Finnish owner, Amer Sports Oyj, was acquired by China ANTA Sporting Goods Co., Ltd. in December 2018.
Other Western sneaker manufacturers have had mixed successes in local production.
Adidas AG opened an automated plant in Germany in 2016 and another in Atlanta, Georgia, the following year, but by 2020 it had closed both. A spokesperson said the company had resumed its previous model of producing shoes mainly in Asia and South America to get closer to suppliers and had no plans to try again to shift production to North America or Europe.
By comparison, New Balance Inc. opened a sixth U.S. plant in Mayhuin, Massachusetts, in March. Dave Wheeler, the company's chief operating officer, said that while most of the company's sneakers are still produced outside the U.S., it wants to meet growing demand for its U.S.-made range of sneakers while also strengthening its resilience to future supply chain disruptions.
"The closer we get to the consumer, the better it works," Wheeler said.
New Balance has never stopped producing shoes in the U.S. and has a local supply chain capable of providing more than 70% of the parts needed; The company says it is working to achieve a 100 percent U.S. domestic supply chain.
Robotic laser cutting system at Salomon's factory
The Boston-based company still imports some key parts, especially soles, from some Asian suppliers. "The (local) supply base is not at what it should be," Wheeler said, adding that building such a supply base "takes a lot of time and a lot of money." The company has been looking for local manufacturers with the skills and machinery to start manufacturing footwear parts, including working with a bulletproof vest manufacturer to produce materials for the upper parts of the sneakers.
In France, Salomon has fewer jobs. Salomon's redesigned shoe has 26 parts, down from more than 70 of other models. The sole is a sandwich made of five layers of independent rubber material. The upper consists of 14 parts, including colorful plastic trims and horseshoe-shaped mesh, which form the body of the sneaker. The tongue part of the shoe is a six-layer structure. Laces are the last component.
But only one part is currently sourced locally — the fibers for the main body of the sneakers, which Chamatex produces at a separate factory next door to its new factory.
Mr Meyzenq said getting the shoe factory up and running would be key to convincing suppliers to work with them.
An employee at work
"Now we are looking for European suppliers one by one," he said. Mr Meyzenq said that while there are few footwear suppliers in France, neighbouring Italy, like other European countries, retains some of its shoe-making capabilities and Salomon is already struggling to find future partners.
He said shoelaces and some other parts can be relatively easily sourced, but other parts are not readily available in Europe. These include the sole — a multi-layered cushion that seems tricky to make due to the fact that it has to be maintained through years of use — and a dedicated plastic part in the upper layer of the shoe. Vietnam is the best source of many of these parts today, Mr Meyzenq said.
Mr Meyzenq said it could take years to develop a local chain of supply stores for all of these components. Like New Balance, salomon will need to identify companies that may be its plastic producers with transferable skills that can be used to make shoes, he said.
The upper has been formed, waiting to be assembled
Even so, the plant will start using additional local parts around 2024 and should eventually rely entirely on European parts, he said.
If the French project is successful, Solomon hopes to build a similar automated factory in the United States to meet the demand there. Mr. Meyzenq said the goal is for the new plant to meet about a quarter of local demand in the U.S. and Europe.
An employee assembles the upper
This will allow the company to better withstand supply chain disruptions and meet environmental protection goals by reducing emissions, he said.
Still, Asia will remain the main force behind the company's largest global footwear production for the foreseeable future.
"It's one thing to drive innovation, but you still have to be pragmatic," Mr Meyzenq said. "Asian shoe factories will continue to exist".