Impact rollers have been effectively proven to prevent penetration, high energy, low frequency and load duration is relatively long, impact roller compaction equipment can effectively reduce the pore density of sandy soil, through stamping, kneading, deep underground soil large gaps closed, thereby effectively reducing the penetration caused by pores and cracks. If the cracks that develop on the concrete surface after stamping are mostly mesh small cracks, there is a more obvious crack development.
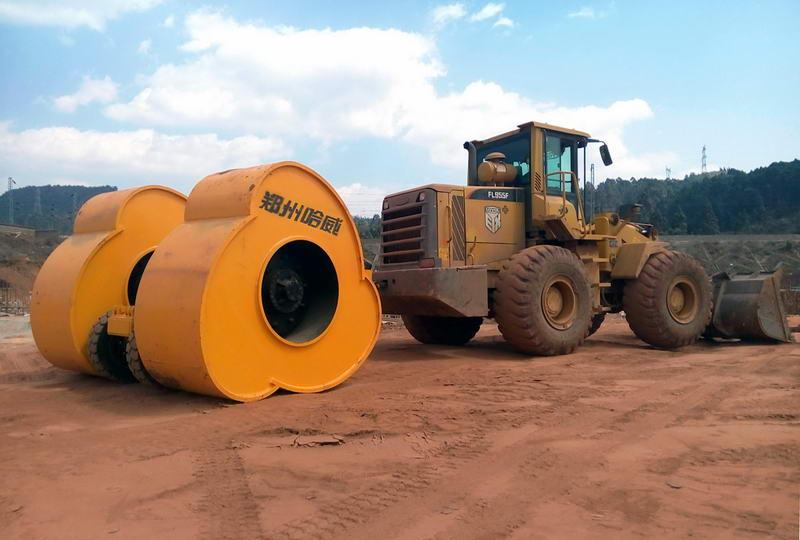
This crack generally runs through the entire plate thickness (about 25cm), and the cracks that produce forked cracks and diagonal crossings in the middle cause the concrete to form a certain degree of fracture, as shown in the figure, the core crushing block is about 10 pieces.
The huge impact force of the impact roller continues to act on the stone side, which can not only crush the super-particle size stone to a certain extent, make the filler gradation more reasonable, but also make the stone reorder into a dense, locked and stable overall structure, and improve the bearing capacity of the filler as a whole. At the same time, due to the increase in the thickness of the filling, the existence of stone with a large particle size is allowed, so it can save a certain material cost and accelerate the progress of engineering construction.
The working principle of impact compaction is that the impact roller is driven by the traction machine non-circular rolling to convert the high potential energy into kinetic energy to impact the substrate of the roadbed to produce a strong impact energy on the deep layer of the soil, and at the same time supplemented by the comprehensive effect of rolling and kneading, so that the displacement, deformation and shear between the soil and stone particles occur, with the increase of the compactness of the soil and stone, the depth of its impact is gradually increased, so that the deep layer of the soil is compacted with the propagation of the shock wave.
Years of construction experience and accumulation tell us that the old cement concrete pavement after impact compaction is positioned in the lower bearing layer of the newly added auxiliary layer, using the method of qualitative and quantitative combination, dynamic control and comprehensive evaluation, and the dual-control comprehensive treatment of combining the stability of settlement after impact compaction and the retention of the cracked plate to maintain the locking effect, in the case of stable settlement, there is no need to pursue excessive rupture blockness.
The larger sedimentation after the impact compaction of the loader-pulled impact roller will inevitably lead to a smaller rupture block. If the cracked block degree is large, the emptying of the base layer under the old concrete slab cannot be well eliminated, and the grass layer cannot be well compacted; if the crack block degree is very small, it is easy to cause excessive stamping of the base layer under the old concrete slab, resulting in the waste of the mechanical bench and the phenomenon of "spring soil".
After the impact of the compaction of the concrete surface development of the cracks are mostly mesh small cracks, and there are one or more obvious wide cracks development, observe its core, the concrete panel core is completely broken, it can be considered that when this crack occurs, the concrete pavement has been completely cracked into small pieces, completely losing the original bearing capacity.